Galvanized steel is a steel that has a protective zinc coating on its outer surface. The zinc is used to increase the steel's corrosion resistance and is applied most commonly by hot dipping the steel into molten zinc. The zinc can also be annealed after the hot dipping process or electroplated to the steel. Galvanized steel can be used in a variety of applications, the only common factor being the applications needed for corrosion resistance. Galvanized steel is used in construction, aerospace, automotive, oil & gas, and many other industries.
This article will discuss what galvanized steel is, how it is made, its properties, and its uses.
What Is Galvanized Steel?
Galvanized steel is a form of standard steel in which the steel is coated in zinc to ensure enhanced corrosion resistance. This galvanized coating protects the steel substrate from damage typically caused by moisture or temperature changes. The steel is dipped into molten zinc, which then bonds itself to the steel and becomes part of its chemical composition.
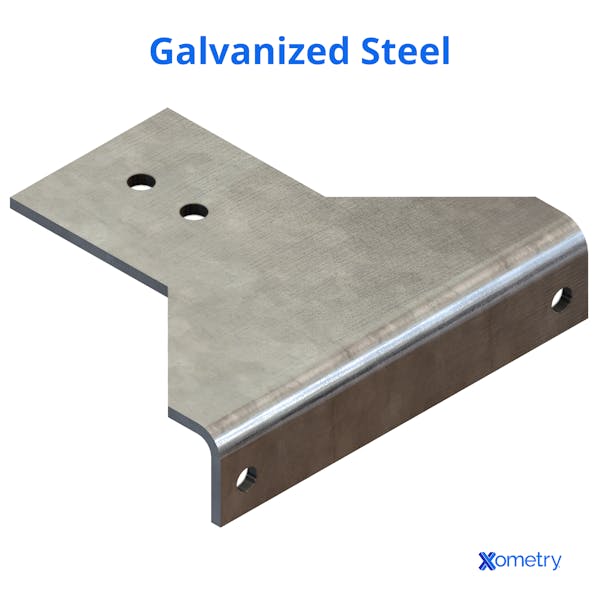
How Does the Galvanizing Steel Process Work?
The manufacturing process of how to galvanize steel is relatively straightforward to understand. Normally, the manufacturer will dip steel into a bath of molten zinc at a temperature of approximately 450 ºC, which in turn binds itself to the steel, as is the case with any alloy. The zinc becomes part of the steel’s chemical composition, therefore, affording it the properties of both as a gradient mixture of the two metals. The most common form of galvanization is hot-dipped galvanization. It is possible to spray zinc onto the steel, however, a weaker layer of zinc is created by this method. The galvanized steel coating then acts as a barrier to protect the metal underneath from environmental conditions and enables it to be more resistant to corrosion.
Methods of Galvanizing Steel
There are four ways in which steel can be galvanized, each affecting the type of layer formed and the final application. The four methods are described below:
1. Galvannealing
Galvannealing is the combination of hot-dip galvanizing and annealing processes to produce a specialized coating on steel sheets. The finished product is a zinc-iron alloy product, with a dull matte surface finish that is ideally suited for paint adhesion. This process works by hot-dipping the base metal, and then heating it in an annealing oven at a temperature of roughly 565 ºC to induce alloying between the steel and molten zinc coating. Examples of galvannealing include: welding operations, marine applications, and any high-tensile stress applications.
2. Hot-Dip Galvanizing
Hot-dip galvanizing is a form of zinc coating applied to steel sheets (or manufactured steel items). This occurs by passing the steel objects through a bath of molten zinc and then cooling them. The zinc bonds to the iron within the steel. Hot-dip galvanizing works by forming a protective layer on either side of the metal to protect the finished product from corrosion. Galvanized steel does not require any secondary or additional coating or painting. Examples of hot-dip galvanizing include: industrial flooring, motorway guardrails, brackets, and fixings.
3. Electrogalvanizing
Electrogalvanization is a process in which steel is galvanized with a zinc coating using electroplating. Steel is submerged in a zinc salt solution and an electrical current is applied to create electrogalvanized steel. The current creates a reaction between the zinc salt and the surface of the steel, leaving behind a thin layer of zinc. This zinc laver is much thinner than the hot dipping method. Electrogalvanized steel is used in: acoustic ceiling tiles, door frames, and switchboards.
4. Pre-Galvanizing
The pre-galvanizing process, also referred to as mill galvanization, is performed at the very initial stages of production on metals which are likely to have a limited number of processes after pre-galvanization. This is because carrying out any process on galvanized steel will result in the exposure of bare metal to the atmosphere increasing the risk of oxidation. Components that are pre-galvanized are usually steel plates and bars. This method enables galvanizing to be done quickly and efficiently on a larger scale than is possible with traditional hot-dipping. This process works by rolling the sheet metal (or other shaped steel stock) in a cleaning agent to prepare the material to be passed through the molten zinc, which is then rapidly recoiled. Pre-galvanizing is primarily used for materials that already have a specific shape before being cut.
Chemical Properties of Galvanized Steel
Table 1 below shows the chemical properties of galvanized steel:

Property | Characteristic |
---|---|
Property Tensile strength | Characteristic 510–600 MPa |
Property Density | Characteristic 7.8 g/cc |
Property Hardness (Rockwell B) | Characteristic 74 |
Property Young’s modulus | Characteristic 210 GPa |
Galvanized Steel Use Across Industries
Galvanized steel is used across a wide range of industries and is ideally suited to any item that is designed for outdoor use, such as nuts or fasteners that are required to withstand exposure to water.
Aerospace is one of the most common industries in which galvanized steel is used because durability is one of the most important factors in a design. The construction industry also utilizes galvanized steel, for example, in bridges and other structures such as train lines and sculptures. Galvanizing these products typically found outdoors ensures they have a sturdy foundation against elements such as temperature variation and moisture.
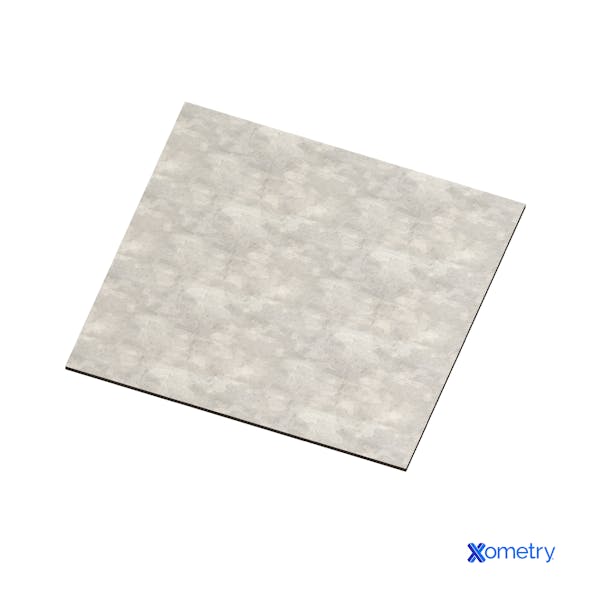
Advantages of Galvanized Steels
Due to the additional zinc layer of protection against many different environmental conditions, galvanized steel has a range of advantages, such as:
- Rust Resilience: Zinc provides a protective barrier to the steel, creating a defense against oxygen, moisture, and other environmental conditions.
- Extended Life Span: Once galvanized, a sheet of industrial steel is estimated to last over 50 years in moderate environments, and more than 20 years in environments with severe water exposure.
- No Maintenance Required: Once dipped in zinc, galvanized steel does not require any further conversion.
- Easy Inspection: It is possible to determine the strength of the galvanized steel just by looking at it. However, stress tests are quick and easy to perform and indicate how thick the layer of zinc is and therefore how much protection the steel has.
Disadvantages of Galvanized Steels
Despite the many advantages of galvanized steel, there are still some disadvantages to this type of steel, which means galvanizing is sometimes not an option to protect steel due to:
- Impracticality: Certain pieces of steel are impossible to hot-dip and impractical to galvanize by other methods due to their size (either too big, such that no container is large enough to accommodate them for dipping or too small to be economically viable to dip) or their shape.
- Requires Precision When Galvanizing: When not enough time has been allowed to let the galvanized steel cool down and set, the zinc does not bind to the steel properly and the galvanization won’t be nearly as effective. Additionally, the correct coating thickness must be applied to achieve maximum effectiveness.
- Finished Effect is Not Necessarily Aesthetically Pleasing: Once coated with zinc, the galvanized metal coating is not always smooth and can have a rough surface.
Galvanized Steel vs. Regular Steel
The main difference between galvanized steel and regular steel is the protective barrier formed by the addition of zinc to the surface of galvanized steel. This zinc makes galvanized steel much more durable, robust, and rust-resistant. Whereas galvanized steel has been coated in zinc, regular steel is predominantly made of iron which will corrode when exposed to moisture.
To learn more, see our article on Galvanized Steel vs Aluminum.
Xometry provides a wide range of manufacturing capabilities including CNC machining, 3D printing, injection molding, laser cutting, and sheet metal fabrication. Get your instant quote today.
Disclaimer
The content appearing on this webpage is for informational purposes only. Xometry makes no representation or warranty of any kind, be it expressed or implied, as to the accuracy, completeness, or validity of the information. Any performance parameters, geometric tolerances, specific design features, quality and types of materials, or processes should not be inferred to represent what will be delivered by third-party suppliers or manufacturers through Xometry’s network. Buyers seeking quotes for parts are responsible for defining the specific requirements for those parts. Please refer to our terms and conditions for more information.
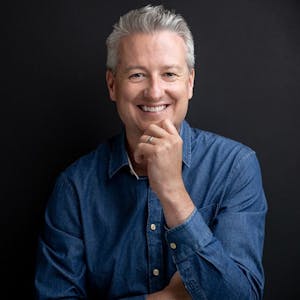