If you want to work with amorphous materials, like polymers and glasses, you’ll need to know about glass transition temperature. This information tells you which material keeps or loses its properties in higher temperatures, so is a must when choosing materials. This article will explain exactly what it is and how it works, as well as why it’s an important part of the 3D printing process.
What Is Glass Transition Temperature?
The point at which an amorphous material transitions from a hard and brittle state to a softer, more flexible one—i.e., when its polymer chains have been made more flexible with higher temperatures—is its glass transition temperature (Tg). This is sometimes also called the critical temperature and can predict material behavior in all temperatures and during processing, like extrusion or molding. If the material is kept at temperatures less than its Tg, it will stay hard and glass-like, but if subjected to temperatures higher than that, it will get viscous or rubbery.
To get a little more technical, at its Tg, a material’s thermal energy overpowers its intermolecular forces, and this allows the polymer chains to move more freely. The change is gradual and happens over a temperature range (unlike melting). It can be measured in Celsius (°C), Fahrenheit, or Kelvin. This transition will change aspects of the material, like its stiffness, ductility, conductivity, stability, durability, longevity, creep deformation resistance, and thermal, electrical, and mechanical properties.

Material selection is where this information comes in handy so you can make sure it can do what you want it to do. For instance, choosing polystyrene, which has a Tg of approximately 100°C, to make ovenware is a disaster waiting to happen. That’s a very generic example, but you get the idea. The Tg will also let you know how mechanically stable and thermally resistant a material is, as well as its expected shelf life (lower Tg options typically have a shorter life because they’re more prone to structural changes) and the best manufacturing methods to process.
The measurement only works with amorphous materials (not metals and ceramics) and provides only one aspect of the material’s overall properties (important nonetheless). Also, it might not be a reliable predictor of a material’s behavior because measurement sensitivities can lead to report variations/inconsistencies, and the value can change depending on several factors—this will then affect how the material reacts in cooling and hardening (i.e., if its properties change), and ultimately how it can be processed. These include:
- Molecular weight: If this is higher in a material, then its Tg will be higher, too, due to the stronger intermolecular forces
- Plasticizers: These will reduce a Tg in a material by increasing the free volume between the polymer chains, which increases mobility
- Crystallinity: Highly crystalline polymers tend to have higher Tgs because their more ordered structure reduces the chain mobility
- Moisture: This acts as a plasticizer, so will lower the Tg as it disrupts the molecular bonds and increases chain flexibility
- Chemical structure: Flexible polymer backbones have lower Tg, while rigid structures have a higher one, and cross-linking can restrict molecular motion to make it even more rigid
- Composition and additives: The Tg of a material made from two different copolymers will be a mix of both the materials’ Tg values, and additives—like fillers and stabilizers—will also likely affect the Tg
- Pressure: High pressure compresses the polymer chains and increases the rigidity
- Polar groups: Adding these strengthens the intermolecular forces and will raise the value
- Thermal history: Rapid cooling can trap the polymer in a less stable, higher-energy state (lowering Tg), while annealing could make it more stable (increasing Tg)
- Environmental factors: Extremes temperatures, UV radiation, or exposure to solvents or acids can degrade molecular bonds or alter polymer structure over time
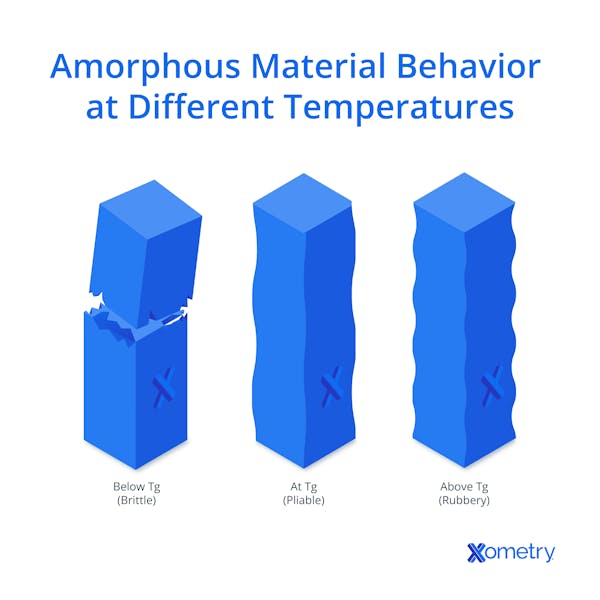
Method | What It Measures | How It Measures | Best For |
---|---|---|---|
Method Differential Scanning Calorimetry (DSC) | What It Measures Heat flow associated with the material’s transition | How It Measures Provides data on the energy absorbed or released during the transition | Best For Materials with thermal transitions, i.e., polymers used in thermal applications |
Method Dynamic Mechanical Analysis (DMA) | What It Measures Changes in mechanical properties (i.e., stiffness) | How It Measures Deforms the polymer sinusoidally | Best For Materials that need mechanical properties, like composites or structural polymers |
Method Thermomechanical Analysis (TMA) | What It Measures Dimensional changes during heating | How It Measures Calculates from the material’s plot of thermal expansion/ compression vs. the temperature | Best For Measuring thermal expansion and contraction in things like coatings or adhesives |
Method Dielectric Analysis (DEA) | What It Measures Changes in electrical properties during transition | How It Measures Monitors changes in dielectric constant or loss factor | Best For Polymers used for electronics or insulation |
Method Fourier Transform Infrared Spectroscopy (FTIR) | What It Measures Changes in molecular vibrations near Tg | How It Measures Detects changes in infrared absorbance corresponding to molecular bond vibrations | Best For Chemically analyzing changes to molecular structure in blends and copolymers |
Method Dynamic vapor sorption (DVS) | What It Measures Changes in the material’s ability to absorb water vapor | How It Measures Monitors weight changes due to vapor absorption | Best For Hydrophilic materials, finding environmental effects on polymers, like packaging films |
Glass Transition Temperature Measuring Methods
Polymer Type | Example | Approximate Tg in °C | Measuring Method |
---|---|---|---|
Polymer Type Crystalline* | Example Polypropylene (PP) | Approximate Tg in °C 165°C (melting temp) | Measuring Method DSC, TMA, DMA |
Polymer Type Crystalline* | Example Polyethylene terephthalate (PET) | Approximate Tg in °C 250°C (melting temp) | Measuring Method DSC, DMA |
Polymer Type Crystalline* | Example Nylon (polyamide, PA) | Approximate Tg in °C 220°C (melting temp) | Measuring Method DSC, DMA |
Polymer Type Semi-crystalline** | Example Polyethylene (PE) | Approximate Tg in °C -100°C | Measuring Method DSC, DMA |
Polymer Type Semi-crystalline** | Example Polyvinylidene fluoride (PVDF) | Approximate Tg in °C -35°C | Measuring Method DSC, DMA |
Polymer Type Semi-crystalline** | Example Polyethylene terephthalate (PET) | Approximate Tg in °C 70°C | Measuring Method DSC, DMA |
Polymer Type Amorphous*** | Example Polystyrene (PS) | Approximate Tg in °C 100°C | Measuring Method DMA, TMA, DSC |
Polymer Type Amorphous*** | Example Polycarbonate (PC) | Approximate Tg in °C 150°C | Measuring Method DSC, DMA |
Polymer Type Amorphous*** | Example Polymethyl methacrylate (PMMA) | Approximate Tg in °C 105°C | Measuring Method DSC, DMA |
Glass Transition Materials and Their Properties
* these have no clear Tg because they don’t have amorphous regions; melting temp is used to measure transition
** have both amorphous and crystalline regions; the Tg usually refers to the amorphous part
*** no crystalline regions, so have very distinct Tg
Glass Transition Temperature in 3D Printing
In 3D printing, Tg directly impacts material performance, print quality, and how stiff, tough, and dimensionally stable the final product will be. It will dictate the best temperature for extrusion, melting, and fusion of layers. If the material isn’t kept within a stable temperature range, the layers could crack or bond incorrectly (if too cool) or warp, deform, or collapse under their own weight (if too hot). Take PLA as an example; its relatively low Tg (approx. 55–60°C) makes it easy to print with but prone to softening and deformation even at moderate temperatures. ABS, though, has better resistance to warping and deformation during printing since its Tg is around 105°C.
It’s not the only value you need to know to work out the stability and durability of a 3D printed part—this depends on other things like material properties, printing parameters, and design considerations. To predict how it will behave, various techniques and tools can be used, like finite element analysis (FEA). This simulates the mechanical behavior of a 3D printed part under different conditions, including static and dynamic loads, temperature and humidity changes, and various environments. In this way, you can gain insights into stress and strain distribution within the part, find potential failure modes, and optimize your design and material selection accordingly.
FAQs on Glass Transition Temperature
Can Tg be changed as the material is being synthesized?
Yes, changing the chemical makeup or processing conditions during the synthesis process will change a material's Tg. For example, if you add a plasticizer, this can lower the value, but if you increase the cross-linking, it’ll get higher.
What’s the difference between Tg and melting temperature?
A material’s melting temperature (Tm) is the point at which it changes from a solid to a liquid state (the way a material behaves when flexible isn’t the same as when it’s liquid). The Tg, as we’ve seen, is when the material’s state reverses from hard and brittle to rubbery and flexible.
Does Tg tell you how stiff a material is?
Although a material’s Tg is linked to stiffness, it’s not a direct indicator of it because stiffness depends on other factors as well, such as degree of crystallinity, cross-linking density, and any fillers/additives that have been included. Also, unlike Tg, stiffness is a measure of a material's resistance to deformation under stress at a specific temperature.
How Xometry Can Help
To learn more about glass transition temperature, or any other related concept, you can reach out to one of our representatives. Xometry provides lots of services for all your manufacturing, prototyping and production needs. Visit our website to learn more, or upload your designs to the Xometry Instant Quoting Engine® and get started straight away.
Disclaimer
The content appearing on this webpage is for informational purposes only. Xometry makes no representation or warranty of any kind, be it expressed or implied, as to the accuracy, completeness, or validity of the information. Any performance parameters, geometric tolerances, specific design features, quality and types of materials, or processes should not be inferred to represent what will be delivered by third-party suppliers or manufacturers through Xometry’s network. Buyers seeking quotes for parts are responsible for defining the specific requirements for those parts. Please refer to our terms and conditions for more information.
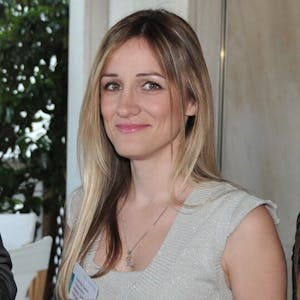