Hardness is a material’s ability to resist deformation at its surface. A measurement is taken of the resulting indentation and converted to a hardness value relative to the hardness scale of the particular test. Many different standardized hardness tests exist, with each having an area of applicability to different types of materials, such as metals, ceramics, or rubbers. Measuring hardness has a number of benefits in comparing materials and providing quality control in manufacturing and hardening processes. This article will discuss hardness testing, its definition, how it works, its types, and benefits.
An Overview of Hardness Testing and How it Works
Hardness testing measures a material’s resistance to permanent deformation at its surface, by pressing a harder material into it. It is used in a number of industries for material comparison and selection, as well as quality control of a manufacturing or hardening process. A specifically manufactured indenter, with chosen dimensions, is used to press into the material being tested, with a prescribed force. The pressing time is also important in the hardness test.
Hardness is not a fundamental physical property of a material, but rather a measured characteristic. It can however provide some valuable information about the strength and durability of a material, depending on the application it is intended for.
Hardness testing works by pressing a standardized, hard instrument into the material that is being tested. The instrument, called an indenter, is pressed into the sample for a standardized length of time (a number of seconds), and with a specific load (force) behind it. When the indenter is pressed into the material, it deforms the surface of the material by a measurable amount. This deformation is then measured, and the measurement is used to assign a hardness value to the material according to the test’s specific scale.
Hardness Testing Materials
Hardness testing can be applied to various types of materials, some of which are listed below:
- Metals and alloys.
- Ceramics.
- Elastomers.
- Polymers and plastics.
- Films.
- Rocks and minerals.
Importance of Hardness Testing
Hardness testing is important for a number of different reasons. The hardness of a material can be a critical parameter in its application. This can be the case for metal components used in cutting and grinding or on the opposite extreme, for rubbers used for shock absorption. It is important to be able to measure and compare the hardness of materials objectively.
Having an objective, standardized hardness value for a material is important to allow quality control during manufacturing. Each unit would need to be within an acceptable range of the specified hardness. Furthermore, these objective hardness values allow for the comparison of different materials and are therefore important for material selection to match the needs of an application.
Benefits of Hardness Testing
Hardness testing provides a valuable measure of a material characteristic with a number of benefits, including:
- An automated hardness testing machine allows hardness to be measured relatively simply.
- To provide meaningful hardness readings for a wide variety of materials, from soft to hard.
- For some applications, the hardness of a material is the key characteristic that is valuable to know. This can be measured directly, rather than inferred by a physical property.
Challenges of Hardness Testing
Hardness testing does have some limitations and challenges that can affect the accuracy and repeatability of hardness results, some of which are listed below:
- It is necessary to have properly prepared the surface of the sample to be measured, usually by grinding and polishing. The surface condition has a significant influence on the hardness reading, so improper surface preparation can give inaccurate or spurious readings.
- Most hardness tests are designed for flat surfaces, so curved surfaces do present a challenge. There are some correction factors that need to be applied to compensate for an indentation on a curved surface.
- The size of the indentation can be difficult to ascertain objectively, particularly when manually reading the size of micro impressions through an eyepiece. This is mainly an issue with older machines. The latest models have cameras and software packages to automatically focus correctly, and display the edge of the impression clearly on a connected computer screen.
- If the prescribed minimum distances between indentations are not followed according to the testing standards, the results of the hardness test will be affected. This is also true of an indentation too close to the edge of a sample.
Types of Hardness Test Methods
There are a number of different hardness test methods, each suited to a certain scale of measurement, or type of material. Therefore, different methods should be selected according to the substance being tested. The most common hardness tests are explained below:
- Rockwell: Developed to give a quick reading, mainly for metallic samples. The depth of the deformation made by the indenter is measured, and a deeper indentation is assigned a lower number, indicating a softer material. Two broad types of tests are used: the Rockwell superficial hardness and the Rockwell regular hardness tests.
- Brinell: A spherical indenter is used, and the diameter of the resulting indentation is measured to give the hardness value. It is generally used for testing larger samples, or samples that are not perfectly homogenous since it causes a larger indentation that is less sensitive to local variations in material hardness.
- Vickers: Uses a diamond pyramid to make a square indentation on the surface of the material being tested. The diagonal of the indentation is measured optically and is converted to the hardness value. The Vickers hardness test can be applied for micro-testing.
- Knoop: Specifically used to test thin or brittle materials, as it gives a meaningful reading with a shallow indentation. It uses an elongated pyramid to make the impression, with the measurement of the long diagonal used to calculate the Knoop hardness. It is used for micro-hardness testing.
- Mohs: A scale from 1 to 10 that provides an indication of the relative hardness of minerals based on how easily they can be scratched. A mineral’s hardness is measured by attempting to scratch it with materials of known Mohs hardness and ranking it accordingly.
- Shore: Is used for softer materials such as elastomers and plastics. A spring-loaded indenter (called a durometer) is pressed into the material sample, and the depth of penetration is converted to a hardness value.
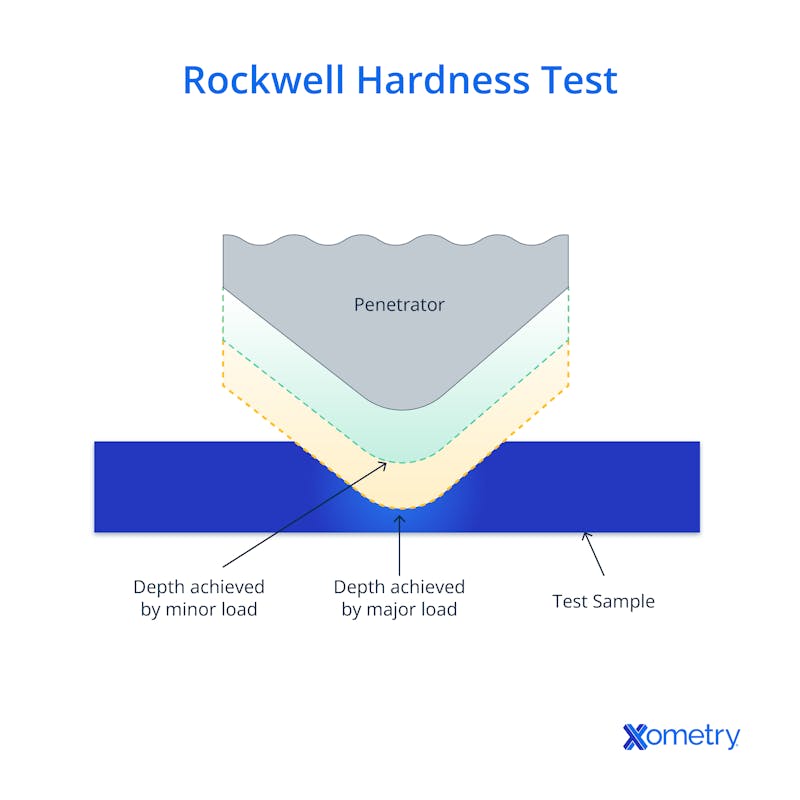
Hardness Testing Loads
The hardness testing load is the load (“force”) that is applied to the indenter when pressing into the material being tested. The depth or size of the deformation made by the indenter will depend directly on the load that was used to press it in. This load is applied by a machine, a hardness testing device. The automatic machine will apply a load according to the parameters given by the operator.
The load that is applied will depend on the size of the sample and the type of material being tested. Harder materials like metals will need higher loads in order to make an easily measurable depression. Softer materials like thermoplastics will need lower loads to produce an appropriately-sized indentation.
Loads of Different Hardness Test Methods
Each hardness testing method has a range of loads that are applicable to the use of the test. Some tests, like the Vickers hardness test, can be used on a macro scale as well as a micro scale. The loads required are listed in Table 1 below:
Method | Load Range | Standard |
---|---|---|
Method Brinell | Load Range 1 kgf–3,000 kgf | Standard ASTM E10, ISO 6506 |
Method Rockwell | Load Range 15 kgf–150 kgf | Standard ASTM E18, ISO 6508 |
Method Knoop | Load Range 1 gf–1 kgf | Standard ASTM E384, ISO 4545 |
Method Vickers | Load Range 1 gf–1 kgf
1 gf–120 kgf
10 gf–100 kgf | Standard ASTM E384
ASTM E384
ISO 6507 |
Hardness Tests vs Ductility Tests
A hardness test uses a limited compressive force to apply a small deformation to the surface of a material, in order to assign a relative value for the material’s hardness. However, a ductility test uses a destructive tensile force to measure the amount of plastic deformation that a material can withstand before breaking.
Both types of tests apply a load to cause plastic deformation in a material. However, the direction of the load is different (compressive vs. tensile) and the extent of the load is different (limited to surface indentation vs. complete yield).
Hardness Testing Standards
There are various standards available for the different hardness testing methods. Generally, the internationally accepted standards for hardness testing are those issued by ASTM (American Society for Testing Materials) and ISO (International Organization for Standardization). The two standards are very similar for each corresponding type of hardness test but have small differences between them for details such as the minimum thickness of the sample. The common ASTM and ISO standards for the four most popular hardness tests in metallic materials are listed below:
- ASTM E10: This standard covers Brinell hardness testing in metallic samples.
- ASTM E18: This standard includes the various ways that Rockwell hardness can be measured by standard methods, specifically for metallic materials.
- ASTM E384: This standard is for hardness testing on a micro-scale, and therefore includes the Vickers and Knoop hardness tests.
- ISO 6506: This standard mirrors ASTM E10, as it contains the standard method for measuring the Brinell hardness of metals.
- ISO 6507: This standard contains the details for the Vickers hardness test in metallic materials.
- ISO 6508: This standard is very similar to ASTM E18, as it deals with the Rockwell hardness tests, both superficial and regular, for metallic samples.
- ISO 4545: This standard covers Knoop hardness testing for metals.
Xometry provides a wide range of manufacturing capabilities including CNC machining, 3D printing, injection molding, laser cutting, and sheet metal fabrication. Get your instant quote today.
Disclaimer
The content appearing on this webpage is for informational purposes only. Xometry makes no representation or warranty of any kind, be it expressed or implied, as to the accuracy, completeness, or validity of the information. Any performance parameters, geometric tolerances, specific design features, quality and types of materials, or processes should not be inferred to represent what will be delivered by third-party suppliers or manufacturers through Xometry’s network. Buyers seeking quotes for parts are responsible for defining the specific requirements for those parts. Please refer to our terms and conditions for more information.
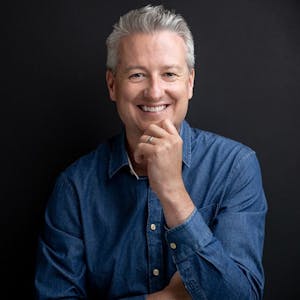