High-density polyethylene (HDPE) is an early thermoplastic polymer, derived from hydrocarbon sources. HDPE has a lesser number of side branches compared to other grades of polyethylene (PE) —which leads to higher density. HDPE is heavily used in packaging for household chemicals such as bleaches and detergents. It is very commonly used for making caps for LDPE and PET bottles for household chemicals, carbonated drinks, foods, and water.
Polycarbonate (PC) is a tough and resilient thermoplastic with the excellent transmission of visible light. Its transmission is better than glass because of its amorphous structure, high refractive index, and absorption frequencies being in the UV range. These properties make it an ideal substitute for glass in many applications, particularly because it is very hard to break. PC’s use in spectacles, general lighting/lenses, and protective applications is widespread. It is commonly used for lighting lenses and covers in car manufacture, for face and eye protection, vandal-proof applications, and for advertising glazing. This article will compare HDPE vs. polycarbonate in terms of applications, properties, sustainability, and costs.
What Is HDPE?
High-Density Polyethylene (HDPE) is the family of a range of moderate to high-density polyethylene tacticities. They are all chemically identical and differ only in the degree, regularity, and size of side-branched monomers. They are made of repeating CH2 chains, resulting from catalyzed byproducts of diazomethane, in a high-pressure reaction chamber.
HDPE variants have very low levels of side groups as branches on the polymer spine, and they have zero complex or long branches off the chain. This enables the polymer threads to align closely in pseudo-crystalline lattices that result in higher density and increase the material’s hardness and strength. Side branching is a result of differences in catalytic materials and polymerization conditions. This is a precisely controlled characteristic, so the molecular weight end-result of materials can be selected exactly, controlling properties with finesse. This control of the polymerization process makes HDPE stronger, stiffer, and harder. Among its common applications are: filament for 3D printers, vehicle fuel tanks, packaging materials, and boat parts. For more information, see our guide on What is High-Density Polyethylene.
What Is Polycarbonate?
Polycarbonate (PC) is the ideal choice of material for various optical and impact-susceptible applications. Although its scratch resistance is poor, the use of a variety of hard coats compensates for this, potentially making the surface among the most scratch resistant of all polymers. It is a great option for optics and corrective lenses, due to its 1.58 refractive index. This property allows for thinner lenses than other materials. In many applications, polycarbonate is interchangeable with acrylic (PMMA), though less so for lenses, as PMMA also has a 1.48 refractive index. Extrusion-made PC sheet provides superior light transmission to glass.
Higher-molecular-weight PC grades are generally stronger and tougher than lower-weight materials but cost more as raw materials and require more complex processing. The highest-molecular-weight grades are used in military and aerospace, for example in aircraft windows, for which cost is less critical than performance.
Car manufacturers exploit the clarity and robustness of PCs by making lenses and covers for lighting applications. The combination of good light-transmission quality and stone-chip resistance in the PC is unmatched. Although the material has quite poor UV stability, blending the material with antioxidants in the molding process and the use of hard coatings compensate for this. Before, vehicle light lenses used to be very susceptible to yellowing and embrittlement, but this is not the case now. PC is used extensively for commercial greenhouse roofing, as it is tough, quite low cost, highly transparent, and the hard coatings exclude UV, reducing plant stress. For more information, see our guide on All About Polycarbonate.
Figure 1 is an example of polycarbonate sheets:
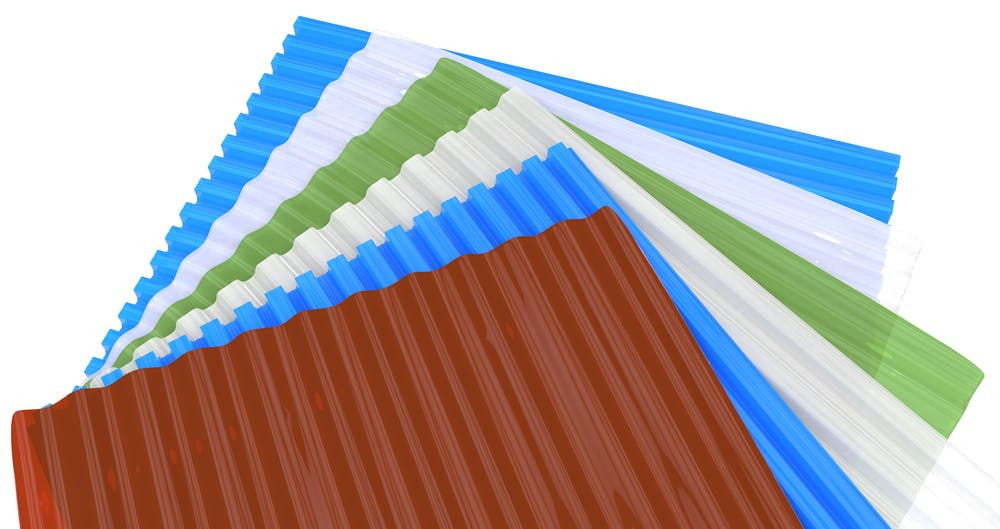
Polycarbonate sheets.
Image Credit: Shutterstock.com/Peter Sobolev
HDPE vs. Polycarbonate: Applications and Uses
The main sectors that make use of polycarbonate, in both extruded sheet and molded parts, are:
- Cameras, optics, and medical tools.
- Safety goggles, and face shields.
- Spectacles, some laser guides, instrument lenses, light guides, and fiber optics.
- Advertising panel covers, weather shields, and vandal-proof panels/windows in public spaces, bus stops, etc.
- For vehicles and personnel protection.
- Headlight components.
- Blu-ray, DVDs, etc.
- Greenhouse windows.
- Bags and hard suitcases.
HDPE applications include:
- Fuel tanks, wiring & cables, cable ties and retainers, and body-mounted clips.
- Trash bins, garden equipment, furniture, storage bins, children's toys, and playground equipment.
- Crates, trays, milk bottles, caps for PET bottles, fuel cans, drums, and industrial fluid containers.
- Ropes, fishing and sports nets, as well as industrial and decorative fabrics.
- BOHDPE packaging for high-value products and foodstuffs.
HDPE vs. Polycarbonate: Physical Properties
Table 1 compares the physical properties of HDPE and polycarbonate:
Property | HDPE value (metric) | PC value (metric) |
---|---|---|
Property Optical transmission | HDPE value
(metric) Poor to zero unless biaxially oriented | PC value
(metric) Very high; better than glass in the optical range |
Property Density | HDPE value
(metric) 0.933–1.27 g/cm3 | PC value
(metric) 1.2 g/cm3 |
Property Hardness, Shore D | HDPE value
(metric) 55–69 | PC value
(metric) 90–95 |
Property Tensile strength, ultimate | HDPE value
(metric) 15.2–45 MPa | PC value
(metric) 28–75 MPa |
Property Tensile strength, yield | HDPE value
(metric) 2.69–200 MPa | PC value
(metric) 39–70 MPa |
Property Elongation at break | HDPE value
(metric) 3–1900% | PC value
(metric) 10–138% |
Property Modulus of elasticity | HDPE value
(metric) 0.483–1.45 GPa | PC value
(metric) 1.79–3.24 GPa |
Property Flexural yield strength | HDPE value
(metric) 16.5–91 MPa | PC value
(metric) 36–103 MPa |
Property Flexural modulus | HDPE value
(metric) 0.5–4.83 GPa | PC value
(metric) 0.971–3.1 GPa |
Property Dielectric constant | HDPE value
(metric) 2.0–2.6 | PC value
(metric) 2.85–3.17 |
Property Melting point | HDPE value
(metric) 120–130 °C | PC value
(metric) 288–316 °C |
Property Max service temperature | HDPE value
(metric) 80–120 °C | PC value
(metric) 115–135 °C |
HDPE vs. Polycarbonate: Recyclability and Sustainability
Polycarbonate (PC) is made from hydrocarbon-derived raw materials. It is very easy to recycle by the common shredding, cleaning, and pellet extrusion method.
In the recycling PC, much of the PC is in copolymers which cannot be recycled, other than as low-grade mixed material. The total volume of PCs for recycling is low; there is little established collection and reuse. Much of it passes to landfill or incineration.
Despite HDPE (high-density polyethylene) being very recyclable and able to yield good quality results for 10 (or many more) cycles, very little is recycled. Real recycling levels are minimal, for the simple reason that the collection streams are sparse and most HDPE materials are not ♳ marked. Most HDPE ends up in the environment, in landfills, or incinerated. HDPE film materials are often used in thicker sections, and they are often colored. Relatively easy to sort for high purity, the process does not need separation of colors. For most recycled applications, a general brown color is accepted.
Waste polymer, once collected, is washed/dried/shredded to find shards. Shredded material is then extruded as pellets. This results in a second-grade polymer that is usually dark in color and used for routine, dark-color applications. This is used in place of virgin material, or as an addition to new material.
HDPE vs. Polycarbonate: Cost
HDPE (high-density polyethylene) is a commodity material widely available and subject to great competition. Virgin material costs $0.80–1.20 per kg, falling to $0.20 for recycled material. PC, on the other hand, is a relatively low-volume and high-cost material, costing ~$2.80 per kg. Recycled material of near-top grade sells for $1.60 per kg, where a supply chain exists.
Alternative Materials to HDPE and Polycarbonate
Polycarbonate (PC) has a variety of alternative materials, depending on the application. Some alternative materials are:
- PMMA (acrylic) has much better scratch resistance and is easier to manufacture with, but it has poorer impact strength and lower tensile strength. Its clarity is slightly poorer than PC, and the lower refractive index makes it a poor option for lenses.
- Trivex® (urethane) offers a good refractive index while showing less residual stress in molded parts, which can make for better optical clarity.
- Polystyrene (PS) is an alternative to PC with good clarity, though it is much weaker and quite brittle. For zero-stress applications such as light pipes/guides, PS is much lower cost.
- ABS and ABS/PC copolymer are alternatives to PC, offering great strength with easier manufacturing and lower cost.
HDPE (high-density polyethylene) is widely used, but applications are narrow in scope and alternatives are straightforward. For most applications, HDPE alternatives are: LDPE, PEX, ABS, PP, and rubber-modified PP.
Summary
This article presented HDPE and polycarbonate, explained what they are, and discussed the different applications of each material. To learn more about HDPE and polycarbonate, contact a Xometry representative.
Xometry provides a wide range of manufacturing capabilities and other value-added services for all of your prototyping and production needs. Visit our website to learn more or to request a free, no-obligation quote.
Copyright and Trademark Notices
- Trivex® is a trademark of PPG INDUSTRIES OHIO, INC.
Disclaimer
The content appearing on this webpage is for informational purposes only. Xometry makes no representation or warranty of any kind, be it expressed or implied, as to the accuracy, completeness, or validity of the information. Any performance parameters, geometric tolerances, specific design features, quality and types of materials, or processes should not be inferred to represent what will be delivered by third-party suppliers or manufacturers through Xometry’s network. Buyers seeking quotes for parts are responsible for defining the specific requirements for those parts. Please refer to our terms and conditions for more information.
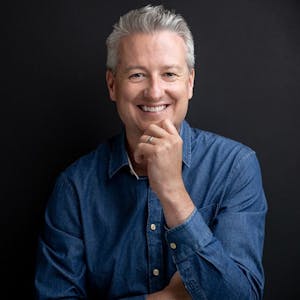