Inconel® variants are superalloys made primarily from nickel, with chromium, iron, and a selection of other metals like cobalt, manganese, copper, niobium, and tantalum, according to alloy specifications. Inconel serves in extreme environments because of its high strengths, high service temperatures, and extreme corrosion resistance. Alloys coded 600, 617, 625, 690, 718, and 750 include type variants and treatment variants such as solution annealed and precipitation-hardened conditions. This article will discuss Inconel, how it is made, its uses, and its types.
Inconel alloys are high-performance nickel/chromium superalloys developed for high temperatures, corrosive environments, and oxidation resistance. They are used in the harshest environments such as in chemical processing reaction chambers/valves, polymer granule manufacture, military applications, gas turbine components, oil fields, and high-grade marine applications.
Inconels are generally alloys of nickel, chromium, iron/steel, plus other constituents like molybdenum, titanium, and copper. They deliver very high strength, abrasion resistance, toughness, and good weldability. Figure 1 below is an example of an Inconel part made by Xometry using the DMLS 3D printing process:
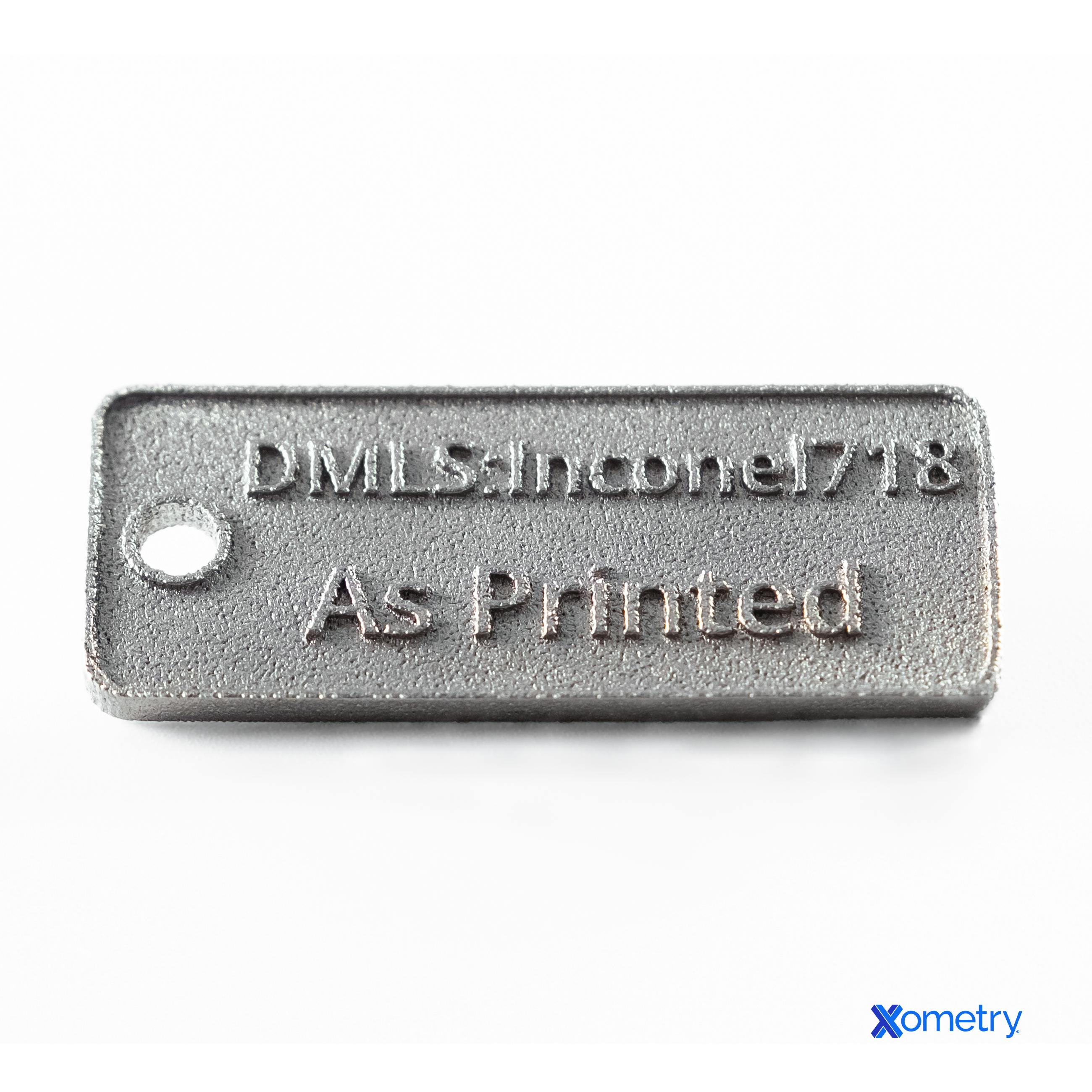
The Composition of Inconel
The original Inconel alloy was coded 600 and consists of >72% nickel, 14–17% chromium, 6–10% iron, and ~1% manganese, plus traces of copper, silicon, carbon, and sulfur. Constituents vary in proportions, and other alloys contain molybdenum, niobium, tantalum, cobalt, aluminum, titanium, lead, and boron at various levels.
All of the Inconel alloys are of high strength. Inconel 718, one of the higher-strength superalloys, delivers around 1,375 MPa of tensile strength and yield strength of around 1,100 MPa. Precipitation-hardened stainless steels can achieve tensile strengths of 850 MPa to 1,700 MPa and yield strengths of 520 MPa to over 1,500 MPa. However, precipitation-hardened stainless steels degrade fairly rapidly in strength above 650 °C, whereas Inconel 718 generally maintains its strength to over 1,000 °C.
The Use Case Examples of Inconel
Some uses of Inconel among Xometry customers are:
- Gas turbine blades.
- Combustion chambers.
- Chemical rocket combustion chambers.
- High-pressure chemical reaction chambers.
- Pollutant separation in harsh environments.
- Oil field extraction processing systems.
The Different Types of Inconel
There is a huge array of Inconel-type alloys (not including Incoloy® and Hastelloy®). The different types are listed below:
1. Inconel 600
This is the original alloy. It is heat- and corrosion-resistant, noted for elevated temperature corrosion/oxidation resistance, good hot and cold processing characteristics, good low-temperature strength, and both hot/cold fatigue properties. It offers high strength under 650 °C, and it’s suitable for chemical-plant components.
2. Inconel 601
This alloy has excellent oxidation resistance at elevated temperatures and high resistance to carburization. It is good for high-temperature organic-chemical plants. It resists oxidation from sulfur atmospheres and has good mechanical properties at room temperature and high temperature. It also has great stress corrosion crack resistance because of the low carbon content and fine grain structure. It has particularly good creep strength at elevated temperatures (above 500 °C, at which other alloys can fail). 601GC is the grain-controlled version of the alloy, offering some enhancement of properties over 601.
3. Inconel 625
This alloy offers better corrosion resistance than 600 and 601. It has better performance in retaining strength and resisting creep from low temperatures up to a maximum service temperature of 980 °C
4. Inconel 718
This alloy is suited to precipitation hardening. It offers good strength and toughness up to 650 °C and good general corrosion/oxidation resistance at all service temperatures. It is formulated for solution treatment or precipitation hardening.
5. Inconel X-750
This alloy offers elevated corrosion resistance and oxidation resistance, as well as good strength below 980 °C. In addition, Inconel X-750 has good low-temperature performance and molding performance. It is mainly used for aerospace and industrial gas turbine components.
6. Inconel 690
This alloy offers greater resistance to chloride corrosion (e.g., salt water), high temperature/pressure water stress corrosion, strong oxidation environments, and fluorinated atmosphere attack. It is mainly applied in nitric acid environments, steam generators, and nuclear waste treatment plants.
7. Inconel 792
This alloy has an elevated aluminum content which improves the high-temperature corrosion resistance. It is best suited to gas turbine blades and combustion chamber parts for chemical rockets.
Machining with Inconel
While Inconel is not an easy group of materials to machine, with good tooling and cooling, great results and moderate cut depths and feeds can be maintained. Listed below are some helpful tips to follow:
- Regularly check for signs of tool wear, as the material is hard on cutting tips.
- Machine in the solutionized state for best results.
- Always use cermet tips for continuous cutting.
- Don’t stop/start when drilling, but continue the feed for smooth chip flow.
- Use four- and five-flute variable helix, high-performance milling cutters.
For more information, see our guide on Types of Machining Processes.
Inconel is hard to weld, as there is a strong tendency to crack at the welds. The use of TIG and Inconel 625 filler rods gives the best results when executed by automated welding equipment. Inconel pricing is very dependent on the alloy type and the form in which it is delivered. As a rule, a tube is more expensive than a plate or bar. Solutionized is the normal delivery state, and prices start at around $40 per kg of stock product. Inconel’s hardness varies, depending on how it is processed. Cold-rolled Inconel has a hardness of 175–240 Brinell. Annealed varieties, on the other hand, have a hardness of 145–220 Brinell. Solutionized, the hardness falls further to 116–194 Brinell. For more information, see our guide on Hardness (Durometer). Most Inconel alloys melt at around 1,400 °C, similar to generic stainless steels.
The Heat Treatment for Inconel
Two basic forms of heat treatment are used on Inconel alloys. These are:
- Solution Annealing: At 925–980 °C followed by quenching in water.
- Precipitation Hardening: At 720 °C for 8 hours, then slowly cool to 620 °C. Hold there for 18 hours of aging, then open to the atmosphere at room temperature for natural cooling.
Inconel vs. Titanium
Inconel is stronger than titanium. Inconel 718 has a tensile strength of 1,375 MPa while Ti-6Al-4V titanium alloy (highest-strength type), has a tensile strength of around 1,170 MPa. While this is lower strength than the strongest Inconel alloys, a wider range of properties may need to be considered in material selection. For more information, see our guide on Everything You Need to Know About Titanium Anodizing.
Xometry provides a wide range of manufacturing services including CNC machining, 3D printing, and more for Inconel and dozens of other materials. Get your instant quote today.
Copyright and Trademark Notices
- Inconel® and Incoloy® are registered trademarks of Special Metals Corporation of New Hartford, New York.
- Hastelloy® is a registered trademark name of Haynes International, Inc.
Disclaimer
The content appearing on this webpage is for informational purposes only. Xometry makes no representation or warranty of any kind, be it expressed or implied, as to the accuracy, completeness, or validity of the information. Any performance parameters, geometric tolerances, specific design features, quality and types of materials, or processes should not be inferred to represent what will be delivered by third-party suppliers or manufacturers through Xometry’s network. Buyers seeking quotes for parts are responsible for defining the specific requirements for those parts. Please refer to our terms and conditions for more information.
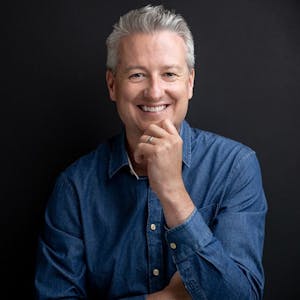