If you’ve studied engineering and/or materials science, or work in any related sectors, you’ll likely know all about longitudinal stress — but this isn’t a tidbit that’s typically in the average person’s general knowledge arsenal. It is, however, something you should know about if you’re in the process of finding the right material for your manufacturing needs. This article will explain what it is, how it works, and how to calculate it in any material.
What is Longitudinal Stress?
Also known as axial stress, longitudinal stress is the internal stress that materials suffer when force is applied along their length (the longitudinal axis) causing an increase or decrease in the length and sometimes changing the diameter depending on how elastic the material is. So why is knowing a material's longitudinal stress important? Well, it helps predict its behavior, such as whether and when it will deform or change in its intended application — particularly necessary for buildings, bridges, and machinery that are safe and durable. It’s also a good way for manufacturers to meet strict safety and performance standards. There are two types of stress, tensile and compressive, shown in the below image.
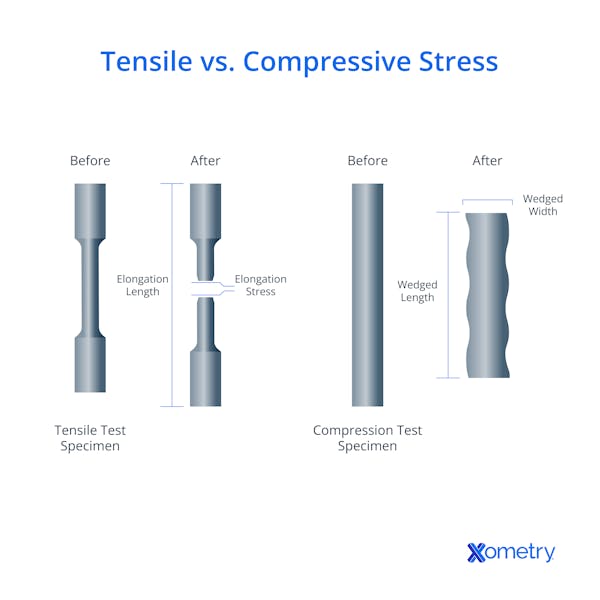
As you can see, these act in opposite directions. Tensile stress (pulling) stretches or pulls along the material’s length, increasing both its length and internal tension. Compressive stress (pushing) happens when a material’s length is squashed, reducing its length and internal compression.
How to Calculate it
There’s a simple formula to calculate longitudinal stress, as follows:
σ = F / A
Where:
σ = longitudinal stress (Pa or N/m²)
F = force applied along the length of the material (N)
A = cross-sectional area of the material perpendicular to the applied force (m²)
You begin by measuring the cross-sectional area of the material perpendicular to its length before any load is applied to it—if this is circular, you’d measure its radius and use that to find the area in square meters, but you could also measure it directly. Next, you have to work out the force that’s being applied along the material’s length, which will typically be in newtons. Once you have both the area and the force, divide the applied force by the cross-sectional area. The last step is interpreting the stress based on the direction of the force — as a reminder, it’s tensile if the force pulls and stretches the material, and compressive if it pushes and compresses.
Type of Stress | What It Is | What’s Affected | Applications |
---|---|---|---|
Type of Stress Longitudinal | What It Is Force per unit area acting along the length of an object | What’s Affected Length of an object (e.g., cables) | Applications Bridges, tension in ropes or beams |
Type of Stress Normal | What It Is Stress perpendicular to a surface | What’s Affected Surface area of a material | Applications Foundations, pressure vessels, buildings |
Type of Stress Circumferential | What It Is Stress acting tangentially around a curved surface (hoop stress) | What’s Affected Curved structures (e.g., cylinders) | Applications Pressure vessels, pipelines |
Type of Stress Shear | What It Is Stress parallel to a surface, causing layers to slide against each other | What’s Affected Internal planes within materials | Applications Rivets, bolts, cutting tools |
Type of Stress Tensile | What It Is Stress from a pulling force that elongates an object | What’s Affected Length and structural integrity | Applications Testing material strength, load-bearing |
Type of Stress Volumetric (bulk) | What It Is Stress applied uniformly in all directions, causing a change in volume | What’s Affected Volume of an object | Applications Hydraulic systems, pressure vessels, deep-sea structures |
Type of Stress Bending | What It Is Stress due to forces causing an object to bend | What’s Affected Cross-section of beams or rods | Applications Beams in construction, cantilevers |
Type of Stress Torsional | What It Is Stress caused by twisting forces (torques) around an axis | What’s Affected Axial rotation of shafts or rods | Applications Drive shafts, turbines, screw propellers |
Type of Stress Fatigue | What It Is Stress due to repeated loading and unloading cycles over time | What’s Affected Material endurance over cycles | Applications Aircraft wings, bridges, rotating machinery |
Longitudinal Stress vs. Other Stresses
How does longitudinal stress affect material quality?
If the stress that a material is put under is more than what it can handle (more than its yield strength), it’s likely that you’ll get permanent deformation, i.e., cracks or fractures that greatly reduce the quality, reliability, and service life. At the very least, it will increase the need for more frequent maintenance or replacement. So, in answer, it directly impacts the material’s structural integrity and dimensional stability.
Does it occur in steel?
Yes, steel frequently experiences longitudinal stress. It’s a material used widely in engineering and structural applications, mechanical components, and machinery, so many steel parts are subjected to stretching and compressive forces. In construction, designing steel-framed structures, including buildings and bridges, requires careful analysis of longitudinal stress to know how the material will react under various loading conditions.
Does it occur in titanium?
Titanium is also affected by this type of stress, and the severity will depend on the specific application and the type of forces involved. For instance, titanium components in space and aircraft will get it from gravity and aerodynamic loads, which only increase during high-speed maneuvers, turbulence, and hard landings. In medicine, titanium implants used in bone and joint replacement regularly experience longitudinal stresses as they bear weight and accommodate movement. Understanding these stresses is crucial to optimizing the design and performance of titanium components in such demanding applications.
How Xometry Can Help
For additional information about longitudinal stress and its applications, contact an Xometry representative. We also provide a wide range of manufacturing capabilities and other value-added services for all of your prototyping and production needs. Visit our website to learn more or to request a free, no-obligation quote.
Disclaimer
The content appearing on this webpage is for informational purposes only. Xometry makes no representation or warranty of any kind, be it expressed or implied, as to the accuracy, completeness, or validity of the information. Any performance parameters, geometric tolerances, specific design features, quality and types of materials, or processes should not be inferred to represent what will be delivered by third-party suppliers or manufacturers through Xometry’s network. Buyers seeking quotes for parts are responsible for defining the specific requirements for those parts. Please refer to our terms and conditions for more information.
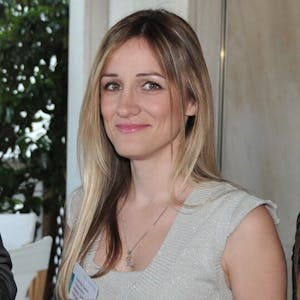