M2 tool steel is one of the high-speed tool steels. In addition to its relatively high carbon content, M2 contains tungsten and molybdenum as its key alloying elements. M2 tool steel has excellent abrasion resistance, hardness, and toughness, making it ideal for metal-cutting tools.
This article will describe what this material is, how it's made, it's chemical composition, and key properties.
What Is M2 Tool Steel?
M2 tool steel is a high-carbon, high-molybdenum steel alloy—one of a family of steels known as high-speed steel (HSS). There are different grades of tool steel which are differentiated by the number after the “M.” The “M'' signifies that the alloy contains molybdenum. It is often used for cutting tooling due to its high hardness, high toughness, heat treatable, and good abrasion resistance. M2 is typically used in tooling applications where high-speed and light cuts are required, such as drills, milling cutters, and reamers.
How Is M2 Tool Steel Made?
M2 high-speed tool steel can be made using a number of processing techniques. The most common technique is by melting metal in an electric arc furnace along with the required alloying elements. Impurities are removed, after which the molten metal is cast into ingots. These ingots are then forged into the required shapes for further processing. After forming, the material is annealed and then either hot-rolled into the desired standard stock shape.
How Does M2 Tool Steel Differ From Stainless Steel?
In general, steels are classified as “stainless” when their chromium content exceeds a certain amount, typically 10.5%. M2 tool steel’s chromium content is lower, thus it is not a stainless steel. Stainless steels are widely used for their exceptional corrosion resistance. However, M2 tool steel has relatively poor corrosion resistance and is not suited for similar applications. M2 tool steel has much better abrasion resistance due in part to its higher hardness. This hardness is also maintained at higher temperatures than is the case for stainless steels.
To learn more, see our guide on Stainless Steel Uses.
How Much Does M2 Tool Steel Cost?
Tool steel is sold in standard stock shapes like solid square bars or rods, specifically for the purpose of creating cutting tools. For example, a 1” x 1” x 7” long square shank can cost as much as $154.70, and a 5/32” x 3 ⅛” long round shank can cost as little as $3.02.
Is M2 Tool Steel a High-Alloy Steel?
Yes. High-alloy steel is defined as steel whose alloying elements make up at least 5% of the meta by weight. M2 tool steel contains high levels of molybdenum (4.5%), tungsten (5.5%), and vanadium (2.2%), making it a high-alloy steel.
To learn more, see our guide on What is Alloy Steel.
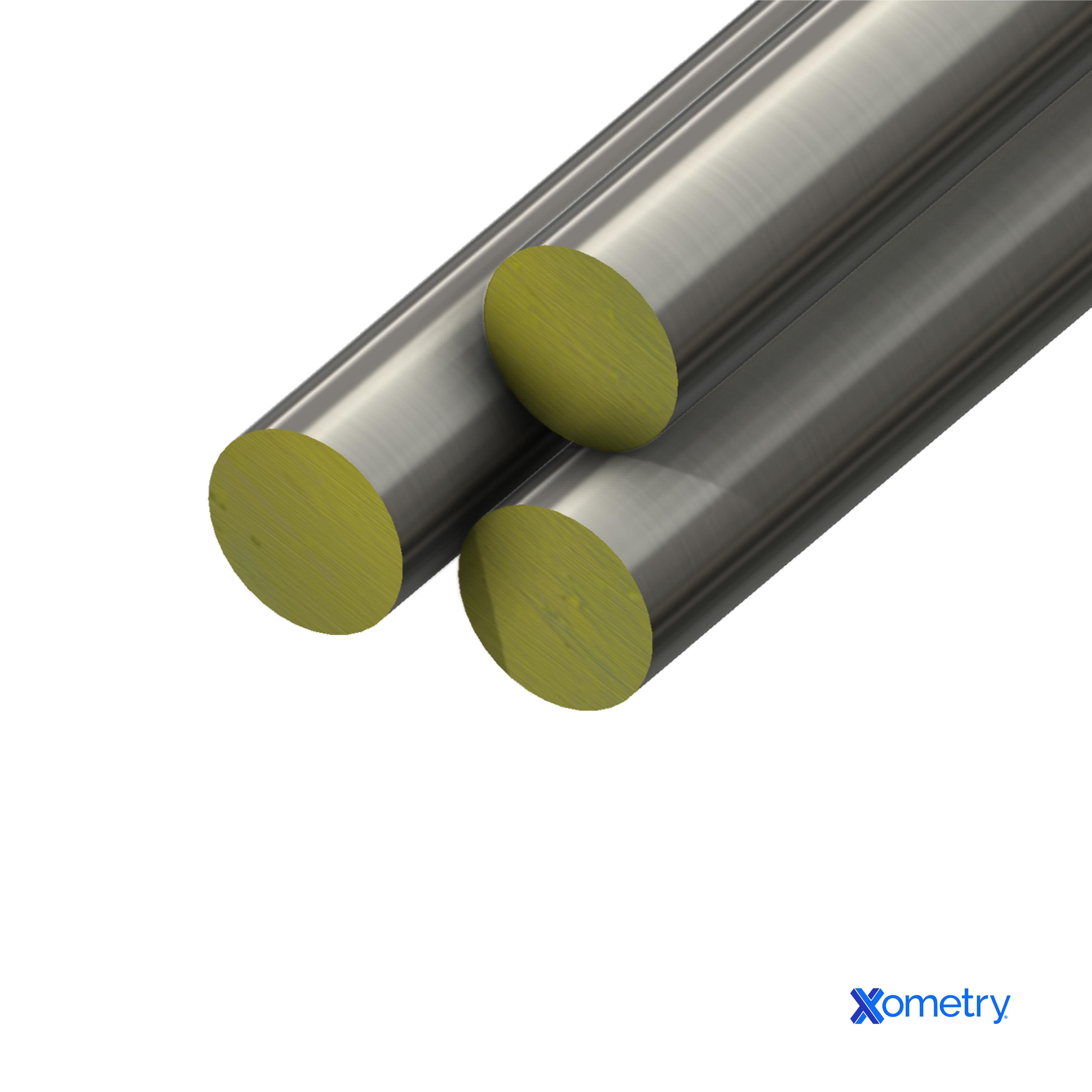
What Are the Uses of M2 Tool Steel?
M2 tool steel is primarily used to make machining tools that are used in subtractive manufacturing processes such as turning and milling. M2 tool steel is also used to produce cutting tools such as metal cutting saws. Its excellent abrasion resistance is especially useful for injection molding tooling. Such molds are exposed to high-pressure plastics which can require materials with high wear resistance to withstand repeated high-pressure plastic injection.
Is M2 Tool Steel Good for Knives?
Yes, M2 tool steel is a good option for fabricating knives. It can maintain a sharp edge due to its excellent hardness and abrasion resistance. M2 tool steel has good machinability making it relatively easy to form via machining or grinding. However, when machining, specialized tooling like CBN (Cubic Boron Nitride) is required as M2 tool steel can be hard on tooling. Tool steels are not as corrosion-resistant as stainless steels and are not suited for applications where the knife needs to be cleaned in a dishwasher for example, which can be very corrosive environments.
What Is the Chemical Composition of M2 Tool Steel?
The key elements in M2 tool steel are molybdenum at 5.5 % and tungsten at 6.75%. The molybdenum, vanadium, chrome, and tungsten give tool steels their excellent hardness and wear resistance due to the formation of carbides while also improving their high-temperature wear resistance. The relatively high carbon content aids in the formation of carbides and increases the overall hardness of the matrix. Table 1 below indicates the typical chemical composition of M2 tool steel:
Element | Percentage by Weight |
---|---|
Element Tungsten (W) | Percentage by Weight 5.50 - 6.75% |
Element Molybdenum (Mo) | Percentage by Weight 4.50 - 5.50% |
Element Vanadium (V) | Percentage by Weight 1.75 - 2.20% |
Element Carbon (C) | Percentage by Weight 0.78 - 0.88% |
Element Nickel (Ni) | Percentage by Weight 0.30% |
Element Copper (Cu) | Percentage by Weight 0.25% |
Element Silicon (Si) | Percentage by Weight 0.20 - 0.45% |
Element Chromium (Cr) | Percentage by Weight 3.75 - 4.5%` |
Element Phosphorus (P) | Percentage by Weight 0.03% |
Element Sulphur (S) | Percentage by Weight 0.03% |
Table Credit: https://www.azom.com/article.aspx?ArticleID=6174#:~:text=M2%20tool%20steels%20are%20pre-heated%20prior%20to%20hardening,and%20quenched%20in%20air%2C%20salt%20bath%2C%20or%20oil.
What Is the Carbon Content of M2 Tool Steel?
M2 tool steel has a carbon content of between 0.78 and 0.88 % by weight. This is in comparison to a carbon content of between 0.17 and 0.23 for AISI 1020 mild steel. High carbon steels tend to be harder and more brittle than lower carbon steels which are more tough and ductile.
What Are the Properties of M2 Tool Steel?
Table 2 below lists some key properties of M2 tool steel:
Property | Value |
---|---|
Property Density (kg/m3) | Value 8138 |
Property Compressive Yield Strength (MPa), Tempered at 149 ºC | Value 3250 |
Property Hardness, Rockwell C, Tempered at 621 ºC, quenched at 1204 ºC | Value 65 |
Property Abrasion loss (mm3). Hardened ASTM G65 | Value 78 |
Table Credit: https://blog.thepipingmart.com/grades/m2-high-speed-steeluns-t11302-properties-uses-and-composition/
What Is the Machinability Rating of M2 Tool Steel?
M2 tool steel has a machinability rating of 39% compared to C360 copper alloy with a machinability of 170%, SAE 1112 with a machinability of 100%, and Inconel® 625 at 17%. Machining M2 tool steel is relatively simple provided the correct tooling is used. It is recommended that CBN (Cubic Boron Nitride) tooling be used due to its high hardness.
What Are the Characteristics of M2 Tool Steel?
Listed below are some key characteristics of M2 tool steel:
- Resistant to wear and erosion.
- Resistant to cracking and chipping.
- Can maintain its mechanical properties at higher temperatures.
Does M2 Tool Steel Rust?
Yes. Despite its chromium and nickel content, tool steel is not specifically formulated for corrosion resistance and will rust over time.
Can M2 Tool Steel Be Welded?
Yes, M2 tool steel can be welded using normal welding methods. However, it must be preheated to between 204 ºC and 538 ºC — the specific preheat temperature depends on the original draw temperatures. Both torch and furnace preheating are acceptable. Post-weld heat treatment is also required.
Is M2 Tool Steel Corrosion Resistant?
No. While it does have improved corrosion resistance when compared to other low-carbon steels, it is not as corrosion-resistant as stainless steels, for example.
Can M2 Tool Steel Be Tempered?
Yes, M2 tool steel can be tempered. It is typically tempered between 540 ºC and 595 ºC which results in a final hardness of between 60 and 65 Rockwell C.
What Are the Thermal Properties of M2 Tool Steel?
Tables 3 & 4 below lists some common thermal properties of M2 tool steel:
Property | Value |
---|---|
Property Melting Point (ºC) | Value 1420-1430 |
Property Specific Heat capacity (J/g·ºC) | Value 0.46 |
Property Thermal Conductivity (W/m·K) | Value 19 |
Property | Value |
---|---|
Property 20 to 100 ºC | Value 11.5 |
Property 20 to 200 ºC | Value 11.7 |
Property 20 to 300 ºC | Value 12.2 |
Property 20 to 400 ºC | Value 12 |
Property 20 to 500 ºC | Value 12.7 |
What Are the Common Forms of M2 Tool Steel Material?
There are many different forms of M2 steel material, with the most common being solid square bars, rods, and flats.
What Are the Equivalents of M2 Tool Steel?
M2 tool steel has many different designations. Table 5 lists below some common equivalents:
Country | Equivalent |
---|---|
Country USA | Equivalent ASTM A600, UNS T11302 |
Country Britain | Equivalent BS BM 2 |
Country Japan | Equivalent JIS SKH9 |
Country Germany | Equivalent DIN 1.3343 |
What Are the Advantages of Using M2 Tool Steel?
Listed below are some key advantages of M2 tool steel:
- It has a Rockwell C hardness of between 60 and 65. It also has good hot (red) hardness which refers to its ability to maintain high hardness even when heated. This hardness is what makes it ideal for use as a cutting tool material, as it can maintain an edge under high-stress, high-temperature service conditions.
- It has excellent wear resistance. This translates to longer tool life when used for manufacturing tooling.
- It has excellent toughness. This means it is less prone to chipping or cracking when exposed to shock loads. It will tend to bend rather than crack under typical loads present when using this material for cutting.
What Are the Disadvantages of Using M2 Tool Steel?
Listed below are some key disadvantages of M2 tool steel:
- It has a low machinability rating, making it difficult to machine when compared to low- and medium-carbon steel. For this reason, it is processed via grinding and by using specialized cutting tools with CBN cutting tips.
- While M2 tool steel contains chromium and molybdenum, it is in relatively small amounts when compared to stainless steel. For that reason, it has comparatively poor corrosion resistance.
- M2 tool steel must be annealed, tempered, and hardened to achieve its optimal properties. This can make it difficult to process while also adding additional cost to the material
Is M2 Tool Steel Better Than D2 Tool Steel?
D2 tool steel has comparable hardness to M2 tool steel and has an increased chromium content. This makes D2 tool steel slightly more corrosion-resistant. However, M2 tool steel is tougher and more wear-resistant.
What Is the Difference Between M2 Tool Steel and T1 Tool Steel?
Both M2 and T1 are classified as high-speed tool steels. The main difference between M2 and T1 steels is that M2 contains substantial molybdenum and a modest amount of tungsten, while T1 tools steels have no molybdenum, but a high level of tungsten. T1 tool steel is often used for slotting and drilling tools due to its high strength afforded by the tungsten content.
Summary
This article presented M2 tool steel, explained it, and discussed its composition and various applications. To learn more about M2 tool steel, contact a Xometry representative.
Xometry provides a wide range of manufacturing capabilities and other value-added services for all of your prototyping and production needs. Visit our website to learn more or to request a free, no-obligation quote.
Disclaimer
The content appearing on this webpage is for informational purposes only. Xometry makes no representation or warranty of any kind, be it expressed or implied, as to the accuracy, completeness, or validity of the information. Any performance parameters, geometric tolerances, specific design features, quality and types of materials, or processes should not be inferred to represent what will be delivered by third-party suppliers or manufacturers through Xometry’s network. Buyers seeking quotes for parts are responsible for defining the specific requirements for those parts. Please refer to our terms and conditions for more information.
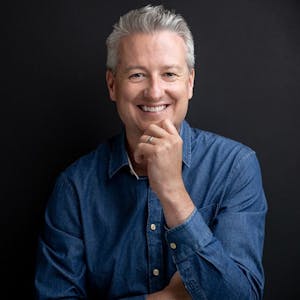