Normalizing and annealing are dual methods used to improve the workability and toughness of certain metals, relieving internal stresses, hardness, and loss of ductility. Although similar processes, normalizing and annealing serve quite different purposes in the manufacturing sector. The differences between them, although relatively small, are profound in the selection between the processes. Normalization is a coarse and basic adjustment of a material's atomic/crystalline structure to bring properties back to workability after cold work has imposed some degree of micro dislocation and work hardening on a component or material.
Annealing, on the other hand, is a precise process that allows a reset of material properties back to a natural state. It maximizes softness, ductility, and malleability by using higher temperatures and longer process times to allow extreme adjustment of the crystalline microstructure of a material.
This article will differentiate between normalizing vs. annealing, how they work, their applications, and their key differences.
What Is Normalizing in Heat Treatment?
Normalizing is a process applied to a variety of metals. It is conducted to relieve the crystalline structural changes and internal stresses that result from malleable work (often called work hardening) or heat treatment that has resulted in hardening.
The process uses a relatively low level of control whereby the part or material is heated to just above its upper critical temperature. The material is held at that heat level for a period that varies according to material, condition, and target effect; and then allowed to cool in still, ambient air.
How Does Normalizing Work?
Normalizing works with the part or material being furnace or flame heated to a temperature slightly above the upper critical temperature point. The level is highly dependent on the metal classification and composition. An example is steel, the relevant temperature for which is in the range of 815–925 °C.
With the material at the target temperature, it is held in that condition for a duration that depends on several variables. This soaking time allows for uniform heating throughout the material and for the grain structure modifications to be completed to the required degree. After the soak period has been completed, the material is removed from the heat and cooled in still, ambient air.
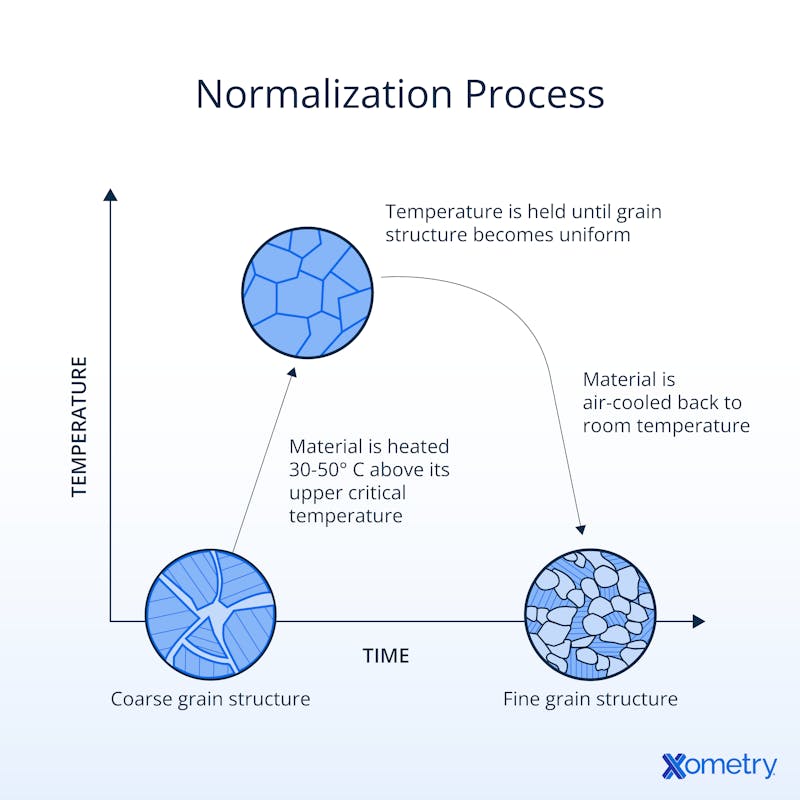
What Is the Purpose of Normalizing?
The main purpose of normalizing is to alter the mechanical properties of the material. When the metal is heated sufficiently, there is a strong tendency towards the dissolution of grain boundaries, allowing smooth crystalline and disjoint-free recrystallization to occur. Atomic migration also occurs, reducing anisotropy that results from interstitial condensation of alloy components into non-uniform regions.
The application of heat literally reforms the crystalline structure to a less disjointed and regionalized form. It returns the worked or previously heat-treated material to its relaxed state. The consequence of this is the recovery of ductility and toughness, as grains are more pliable (reducing in hardness) and the majority of crack initiation sites are expunged. This has various benefits in both component functions and in reducing the effort of follow-on processes.
What Are the Benefits of Normalizing?
The benefits of normalizing are:
- Reduced hardness improves machinability in subsequent manufacture. The hardness induced by work or heat/quenching can be reduced selectively.
- Increased malleability reduces the forces required in subsequent forming operations. The trade-off between malleability/ductility allows relatively fine adjustments to properties to be reliably performed by a moderate degree of control of normalization parameters.
- Reduction in crystal boundary dislocations is a beneficial consequence of the dissolution of grain boundaries and reformation of the matrix. This results in a lower risk of fracture in subsequent forming operations or in use.
- Increased ductility is intrinsic to the large, uniform crystalline structure that results from normalization. This makes materials and components tougher and more resilient in real-world uses.
- Thermal processes that involve uneven cooling and the potential for regional differences in alloy constituent distribution are reduced in impact, allowing greater uniformity in component distribution. The atomic redistribution that occurs during normalization increases the mutual dissolution of alloy elements into a more homogenous and isotropic structure. This reduces the risk of disjointed properties resulting in property variations in the part.
What Are the Drawbacks of Normalizing?
The drawbacks of normalizing are listed below:
- Effective for ferrous metals like steel and cast iron. It may not be suitable or as effective for non-ferrous metals and alloys.
- Does not provide the same level of hardness control as other ductility-restoring heat treatment methodologies.
- Achieving and maintaining the high normalizing temperatures for the required soak period is energy and time-demanding.
- Normalizing involves slow cooling in still, ambient air. This limits throughput, as cooling cannot be accelerated.
- Any heating process can result in slight dimensional changes in the material, which may need to be considered in precision applications. This is a particularly significant feature in thin and non-uniform sections.
- Some applications require specific material properties that may not be achievable through normalizing.
What Is Annealing in Heat Treatment?
Annealing is used to alter the properties of materials, primarily metals and alloys. It is done by heating them to a specific temperature and then cooling them slowly to achieve desired microstructural changes.
Annealing can be differentiated between distinct classes of treatment. It is selected according to the desired crystal lattice, hardness/ductility spectrum, and residual stress effects. The types of annealing are: full, partial, isothermal, and process annealing. These four types differ in the temperature applied to the part.
How Does Annealing Work?
Annealing works by heating the material to a temperature above its upper critical or recrystallization temperature. The temperature varies with the type and composition of the material and with the desired effect on the microstructure. Next, the material is held at that temperature for a specified duration that facilitates uniform heating throughout the material. It allows the transformation of the microstructure to the required degree, controlled by the duration of soaking. Lastly, the material is either cooled within the furnace or removed from the furnace and allowed to cool in an insulating medium, such as vermiculite or sand. The cooling rate is deliberately controlled to achieve specific microstructural changes that are slow to complete.
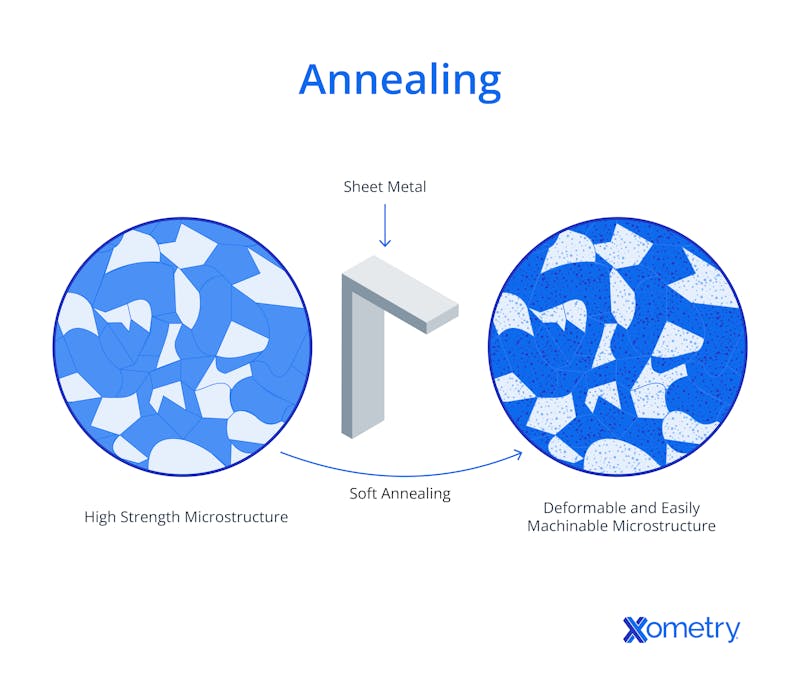
What Is the Purpose of Annealing?
The purpose of annealing is to achieve specific and repeatable microstructural changes and material property adjustments. The key mechanisms at work during annealing apply adjustments to the crystalline matrix, the isotropy of the properties, and the overall mechanical properties of the material or part. The mechanisms at play in annealing are recrystallization, stress relief, and grain refinement.
As the material is heated and soaked, new grains with a more uniform and refined microstructure form. This replaces/subsumes the previous deformed, fractured, or strained grains. Annealing also relieves internal stresses created during prior deforming or cutting processes exerted on the part. This stress relief reduces the risk of post-machining deformation or fracture in subsequent processes or use. Finally, the refined grain structure enhances the mechanical properties of the material. Its ductility, toughness, and formability are all improved to a controlled degree, at the expense of hardness.
What Are the Benefits of Annealing?
Annealing offers a variety of benefits such as:
- Softens the material, making it more ductile and less prone to brittleness.
- Relieves internal stresses within the material, reducing the risk of deformation or cracking.
- Annealed materials are easier to machine and fabricate, improving their manufacturability.
- The treatment promotes a more uniform and fine-grained microstructure, resulting in better material consistency, plus better and more uniform mechanical properties.
- Annealing helps homogenize the material, making it more uniform in composition and properties throughout.
- Eliminates or refines grains and structures that were deformed during previous processing steps, such as cold working or heat/quenching.
- Allows for the tailored adjustment of material properties to specific requirements, within limited ranges.
- The process is commonly used to relieve stresses in welded components, reducing the risk of post-weld cracking due to highly localized heating and matrix changes.
What Are the Drawbacks of Annealing?
The drawbacks of annealing are listed below:
- Slow cooling increases production schedules.
- Is not suitable for various metals and alloys.
- Can cause dimensional changes in the material, particularly if section thicknesses vary or very uniform heating is impractical.
- Achieving and maintaining the annealing temperature is energy-intensive, defining much of the operational cost.
- Achieving the desired properties in annealed materials often requires prolonged cooling and deviations from this rate can significantly affect outcomes.
- During annealing, materials are exposed to high temperatures, which can lead to surface oxidation, requiring post-processing.
What Is the Role of Normalizing and Annealing in Steel Microstructure?
Normalizing and annealing are used to modify the microstructure of steel and other alloys, to selectively alter mechanical properties. Some of their roles are:
- Microstructure Transformation: Promotes the formation of a fine and uniform grain structure in steel. This replaces the prior deformed or strained grains with new, more regular grains. Annealing can have a more profound effect than normalizing in this regard. The changes wrought by annealing are driven by higher temperatures and longer cooling periods, creating a more profound influence.
- Refined Microstructure: The refined microstructure achieved through normalizing results in improved mechanical properties, including increased strength, toughness, and ductility. This is additionally significant in fully annealed steel, resulting from the hotter and slower processing.
- Stress Relief: Normalizing relieves internal stresses within the steel, reducing the risk of deformation or cracking. Annealing is similarly effective in this. This is particularly important in components that have undergone prior manufacturing processes.
- Uniformity: Both ensure a consistent and uniform microstructure throughout the material, contributing to quality control and reliability.
- Enhanced Ductility and Reduced Hardness: Annealing softens the steel and enhances its ductility, making it more suitable for forming, bending, and shaping operations. Normalization is generally somewhat less effective in this regard, but still influential.
- Homogenization: Annealing helps homogenize the composition and properties of the steel, resulting in a more consistent material. Normalization is less helpful in this regard, as it is more limited in the degree of atomic migration that it facilitates.
To learn more, see our guide on Steel Microstructure.
Which Is More Preferable, Normalizing or Annealing?
It depends. There is no simple preference for one process or the other. Annealing is generally employed for more precise control and/or more extreme adjustment of properties. Normalization, on the other hand, is often sufficient for basic processing and carries a lower cost burden than annealing.
How Do Normalizing and Annealing Differ in Applications?
Normalization is utilized as an approximate relief stage between processing stages that have imposed work hardening onto the material. When forging a crankshaft for an IC engine, for example, normalization will generally be used after forging. It is done to partially relieve the internal stresses and recover the easy machinability of the part. Annealing would destroy the anisotropic structures that have developed through forging, whereas these are desirable and beneficial in the strength of the part.
Annealing is a method that is widely used prior to high-strain cold-working processes, in which high ductility is required in the processing stage. Deep-drawn sheet steel for car bodies is a good example, in which the annealed sheet is used to make the press form relatively low resistance. The pressed shape then carries a degree of work hardening that is highly desirable, though not excessive.
How Do the Processes of Normalizing and Annealing Differ?
The two processes are essentially similar in most regards. Annealing generally involves heating to a temperature above the upper critical temperature of the material, enabling greater atomic motility and a deeper recrystallization effect. The controlled and slower cooling of annealing allows more time for the crystalline and atomic adjustments to complete and for the formation of matrix changes that can be differentiated in the cooling process—for example in the formation of austenitic structures and the control of pearlite-ferrite proportions. The precision control of the cooling process used in annealing, and particularly selective plateaus in the cooling ramp rate, can have a profound influence on the crystallization and resulting structures.
In comparison, normalizing is a little simpler, a little less controlled, and uses lower temperatures. It can't deliver the complete precision of end properties or ultimate reversion of hardness that annealing achieves—but in many cases, simplicity suffices. Normalizing is faster, less skilled, uses less equipment, and is energy-intensive, but it often can deliver exactly what the next manufacturing step requires, in easing hardness and internal stresses.
Does Temperature Factor Into Normalizing and Annealing?
Yes, temperature is the first critical driving property in both processes. Normalization generally involves heating and soaking at a temperature around the upper critical temperature and then a moderate but uncontrolled cooling in ambient air. Annealing, on the other hand, requires more aggressive heating to above the upper critical temperature and then a moderated and even paused cooling rate in an insulated environment. It allows deeper crystallization processes to be completed.
What Results Can Be Achieved Through Normalizing and Annealing?
Normalizing and annealing are used to achieve similar effects, which differ in detail and precision. The specific results achieved through normalizing and annealing depend on factors such as the initial condition of the steel, the desired properties, and the intended application. These heat-treatment processes are valuable tools for tailoring the properties of steel to meet specific requirements in various industries, and their selection depends on the material, its prior condition, and the effect being sought. The results from normalizing are listed below:
- Promotes the formation of a finer and more uniform grain structure. It replaces the preexisting deformed, displaced, or strained grains.
- Seeks to improve ductility, tensile strength, and yield strength.
- The refined microstructure enhances material toughness.
- Somewhat improves the consistency and uniformity of the microstructure throughout the material.
- It relieves internal stresses, reducing the risk of deformation or cracking in subsequent processes or use.
The results from annealing are also listed below:
- Delivers full recrystallization and a highly uniform microstructure.
- Restores the softness/malleability of metals and completely removes all effects from prior heat/quench hardening.
- Delivers optimum ductility, easing further processes and improving toughness.
- Similar to normalizing but to a greater degree, annealing relieves internal stresses within the steel.
- Helps homogenize the composition and properties of the steel, resulting in a more consistent material.
How Do the Fields of Use for Normalizing and Annealing Differ?
Annealing and normalizing have distinct applications due to their specific effects on materials. Annealing is used to soften materials, making them more ductile and suitable for forming and shaping. It relieves stresses in welded components, enhances formability, and improves machinability while homogenizing material properties and promoting a fine-grained microstructure. Normalizing aims to enhance mechanical properties like strength and toughness. It prepares materials for subsequent heat treatments, relieves internal stresses, and ensures uniformity in structural components.
How Do Normalizing and Annealing Differ in Cost?
The two processes differ in cost in a number of regards. For example, annealing takes longer than normalizing, particularly in the cooling phase. Annealing generally requires higher temperatures and longer soak times, increasing energy usage. It is also a more controlled and skilled process, so the labor costs are generally higher compared to normalizing. Annealing, being hotter and more controlled, requires better and more expensive equipment. The controlled cooling stage also requires dedicated equipment, adding a cost burden. On that basis, annealing is more costly than normalizing, but the processes are somewhat overlapping in utility, rather than closely related in application.
Are Normalizing and Annealing Applied to the Same Materials?
Yes, the materials that can be normalized can also be annealed, in general.
Summary
This article presented normalizing vs. annealing, explained each of them, and discussed their key differences. To learn more about normalizing and annealing, contact a Xometry representative.
Xometry provides a wide range of manufacturing capabilities and other value-added services for all of your prototyping and production needs. Visit our website to learn more or to request a free, no-obligation quote.
Disclaimer
The content appearing on this webpage is for informational purposes only. Xometry makes no representation or warranty of any kind, be it expressed or implied, as to the accuracy, completeness, or validity of the information. Any performance parameters, geometric tolerances, specific design features, quality and types of materials, or processes should not be inferred to represent what will be delivered by third-party suppliers or manufacturers through Xometry’s network. Buyers seeking quotes for parts are responsible for defining the specific requirements for those parts. Please refer to our terms and conditions for more information.
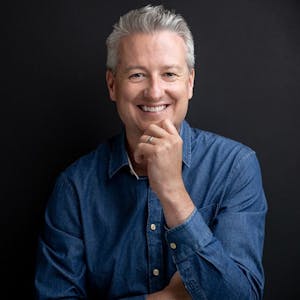