Polyamide has had its place in the manufacturing world for almost a century, which all comes down to a handful of characteristics that make it hard to replace in all kinds of engineering and product design scenarios. You can feed these synthetic plastics through plastic extrusion machines or cut them with lasers to get exactly the product you need. If polyamides show up often in your industry, we’ve broken down how they’re made, what types exist, and the applications in which you can expect to use them.
Defining Polyamide and How it’s Made
This type of plastic was made more than 90 years ago by a DuPont researcher, and it’s still a major category of material used in today’s factories. To create it, you start with crude oil and mix the monomer diamine (hexamethylenediamine, to be exact) with adipic acid, which appears in the form of a salt. It’s then melted down, cooled, and then extruded into fibers that can be turned into everything from clothing fabrics to spark plug tubes. In the image below, you’ll see an illustration of the molecular structure of polyamide 6.
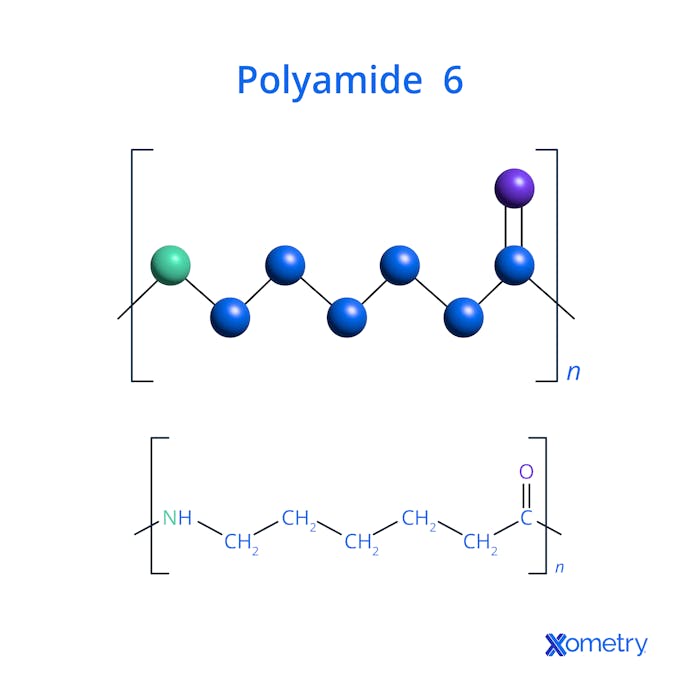
The types of polyamides you might be most familiar with are nylon and aramid, but there are plenty more types and forms out there, including all of nylon’s subcategories. Lookswise, polyamide tends to naturally take on a yellow, light brown, or whitish hue, but it’s easy to dye it any color.
Characteristics
This category of plastic is beloved by manufacturers because of its durability and wear resistance. These are a few other characteristics that have led it to become such a common material, as well as reasons why it may not be used for specific applications:
- Great chemical resistance
- High tensile strength
- Good flexibility
- Low creep
- High impact resistance
- Hygroscopic
You’ll see Xometry’s “X” printed in a white polyamide material in the image below.
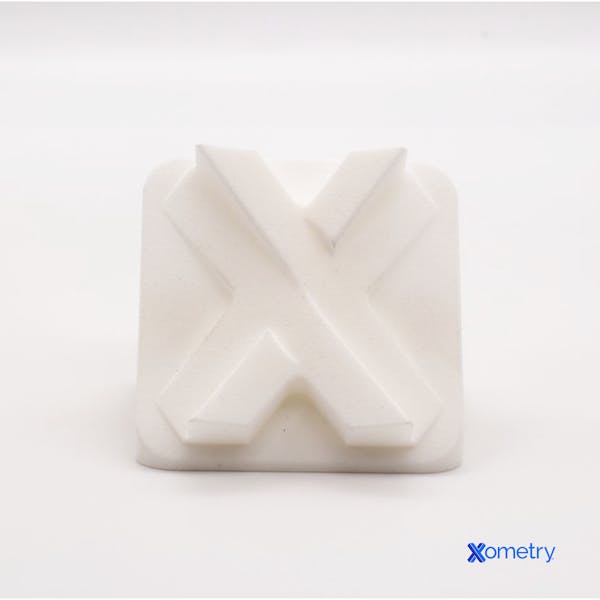
As far as benefits go, polyamides are renowned for being low-cost, especially with all of the traits they provide, whether it’s chemical resistance or stability. That being said, they’re limited by their ability to absorb a lot of water and how quickly many types degrade when exposed to UV radiation or light.
Properties
There are many types of polyamides, and we’ve created a table, below, that lists several of the most well-known versions, along with some of their properties and uses.
Polyamide Type | Description | Properties | Applications |
---|---|---|---|
Polyamide Type Nylon 6,6 or PA 66 | Description Most common polyamide | Properties High melting point, good abrasion resistance, poor chemical resistance, and high water absorption | Applications Good for machine parts, bearings, gears, and even conveyor belts |
Polyamide Type Nylon 6 or PA 6 | Description A popular choice for non-woven fabrics | Properties It has decent ductility and abrasion resistance | Applications Used for strings of violins and as fibers to make nets and ropes |
Polyamide Type Nylon 6,10 or PA 610 | Description A type that’s popular for monofilaments | Properties This nylon has good chemical resistance, high strength, and low moisture absorption | Applications Great for brush filaments, hosiery like tights, and zip fasteners |
Polyamide Type Nylon 11 or PA 11 | Description Comes from vegetable oil | Properties High UV and thermal resistance,impact resistance, and dimensional stability | Applications Made into fuel lines for vehicles, tool handles, gears, and coatings |
Polyamide Type Nylon 6,12 or PA 612 | Description More expensive than others and less common | Properties Has low moisture absorption and high abrasion resistance but poor chemical resistance. | Applications Good for gears, cams, spark plug tubes, and electrical components |
Polyamide Type Nylon 12 or PA 12 | Description Also more expensive, similar to nylon 6,12 | Properties Has wear resistance and is flexible | Applications Works for creating cable fasteners, sheet gaskets, sealing rings, diaphragms, and protective covers |
Polyamide Type Nylon 6,9 or PA 69 | Description Like nylon 6, it’s great for non-woven fabrics and has a semi-crystalline structure | Properties It has a low melting point and moisture absorption | Applications Can be made into luggage, furniture, electrical connectors, and banners |
Polyamide Type Nylon 4,6 or PA 46 | Description Made through a process called polycondensation, which happens with 1, 4-diaminobutane and adipic acid | Properties Has dimensional stability and is resistant to extreme temperatures, chemicals, and fatigue | Applications Great for electrical parts |
Polyamide Type Aramid | Description An aromatic polyamide that usually takes on a fabric format | Properties Resistant to abrasion and chemicals but not to UV rays and light | Applications Can be made into air filters, helmets, fiber-optic cables, engine nacelles, and reinforced pipes |
Polyamide Type Polyphthalamide | Description A semi-aromatic polyamide that comes from reacting aromatic acids and aliphatic diamines | Properties This is a stiff polyamide with excellent creep resistance. It has great heat, chemical, and abrasion resistance too | Applications Good for air coolers, motor insulators, electrical connectors, and jet engine bearing pads |
Table 1: Properties and Application of Polyamides
Applications
The uses for polyamides are about as wide and varied as the material itself. Here are just a few examples:
- Textiles and fibers for clothing, bedding, carpets, curtains, and other products
- Engineering plastics that can make helmets, pipes, and protective equipment
- Car and vehicle parts like lights trim, fuel lines, and engine covers
- Electronics such as phones and computer motherboards
- Filaments for 3D printing — a use that’s becoming more and more popular
Types of Polyamide
Whether you’re working with nylon or another polyamide, you can usually separate each type into one of these three categories:
1. Aliphatic Polyamide
These are very common polyamides, and they stand out from others when you examine them from a chemical level, as they don’t have double or triple carbon bonds like other types. You’d use them in situations where high strength, flexibility, and chemical resistance are necessary. They also have less friction and low creep. An example of an aliphatic polyamide is nylon 6, which is a popular choice for everything from seat belts to carpets to nylon tights.
2. Aromatic Polyamide
This is another name for aramid polyamides, and when you compare them to aliphatic options, you’ll find that they’re much stronger and better resistant to chemicals and high heat. One type of aromatic polyamide — and probably the most familiar — is Kevlar and it’s used for items such as bulletproof vests and jet engine inlets.
3. Semi-Aromatic Polyamide
These plastics have a semi-crystalline structure, and they’re made by combining aliphatic and aromatic polyamides. When you mix them together, you get a plastic that’s super stable, very resistant to chemicals, and has low creep, making it popular for aircraft engines and headlights for cars.
How Xometry Can Help
Xometry has several services that incorporate polyamides, so it’s just a matter of finding exactly what’s fit for your business. You can get a free quote on our website, and explore options such as plastic 3D printing and custom plastic fabrication.
Copyright and Trademark Notices
- KEVLAR® is a trademark of E. I. DuPont de Nemours and Company
Disclaimer
The content appearing on this webpage is for informational purposes only. Xometry makes no representation or warranty of any kind, be it expressed or implied, as to the accuracy, completeness, or validity of the information. Any performance parameters, geometric tolerances, specific design features, quality and types of materials, or processes should not be inferred to represent what will be delivered by third-party suppliers or manufacturers through Xometry’s network. Buyers seeking quotes for parts are responsible for defining the specific requirements for those parts. Please refer to our terms and conditions for more information.
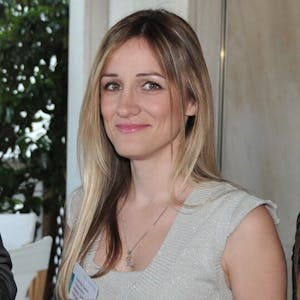