Polycarbonate is pretty much everywhere nowadays, used to make everything from eyeglasses and medical devices to protective gear and auto parts. It’s naturally transparent and can transmit light internally almost as well as glass can. It also has a higher impact resistance than other types of plastic… but its perks don’t end there! Let’s have a look at what this material is good for, how it’s made, and the forms it comes in.
What is Polycarbonate?
Polycarbonates are a group of strong and versatile thermoplastics that are almost twice as impact-resistant as ABS or PVC. Despite this, PCs are quite sensitive to scratches. They’re most times see-through, something that makes them a common go-to for making lenses, and windows, and used to replace glass parts on items like blenders and water bottles to make them more lightweight and less fragile. This material is usually easy to work with, mold, and thermoform, and often comes in the form of sheets that can replace metal in prototypes to allow viewers to see inside. It even comes in the form of filament for 3D printers, which we happen to offer here at Xometry. The below image shows a 3D print we made using PC.
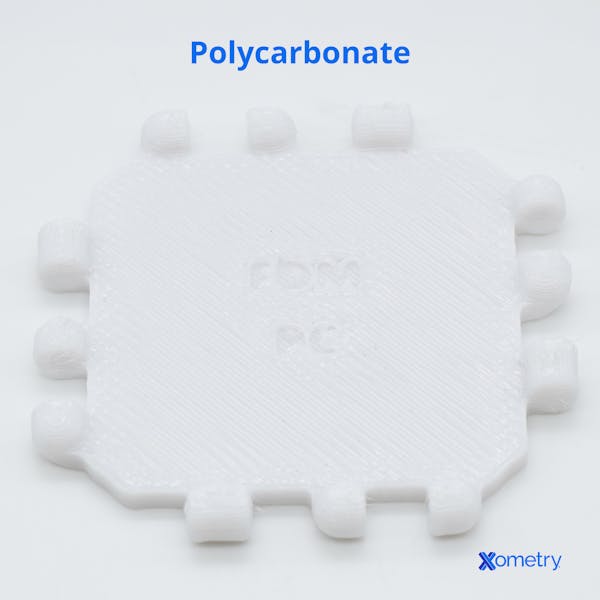
PC is a good material for injection molding because it turns to liquid at its melting point (between 260–320°C), which is also good for recycling. Unlike crystalline polymers, PC is amorphous, softening gradually over time (as opposed to suddenly). PC sheets, which typically have a tensile strength of 8500psi and a shrink rate of 0.006 to 0.009 in/in, can be joined together with solvents, adhesives, or mechanical fasteners. PC has a higher coefficient of expansion (0.065mm p/meter, p/°C) than metals, like steel or aluminum, so if you’re using glue or sealant, make sure it’s flexible. For PC forming, you’ll need to remove any trapped moisture. One way to do this is to heat it in an oven at 120°C for 2–4 hours.
How it’s Made
PC is made by combining bisphenol A (BPA) and phosgene. Treating the BPA with sodium hydroxide is the first step. This removes hydrogen atoms from the BPA molecules’ hydroxyl groups and creates diphenoxide. This molecule forms a chloroformate when reacted with phosgene, which then reacts with another phenoxide (similar to diphenoxide) to link together and make polycarbonate chains. Around one billion kilograms of PC is made each year using this process. It can be made at room temperature without cracking or breaking, and it can be re-formed without the use of any heat, too. Additives are sometimes included to make the material more resistant to UV rays, fire, and discoloration. These include the following tongue twisters: tetrabromobisphenol A, dihydroxybenzophenone, and bis(4-hydroxyphenyl) cyclohexane.
Types of Polycarbonate Plastic
Though PC sheeting has been around since the mid-20th century when it was developed by GE and Bayer, many manufacturers and developers now have their own formulas and production processes. Some of the most widely used variations are the following:
Clear GP Sheet
This is great for glazing and industrial purposes as it’s the best type of PC to protect against vandalism and intentional breakage. It has a whopping 250 times higher impact strength than glass and 30 times higher than acrylic sheeting.
Clear SL Sheet
This is the type of PC to go for if you’re setting it up outside. It has excellent resistance to UV light and can maintain its color in the face of severe environments. It also usually offers the same UV protection on both sides, so you’re covered.
Polycarbonate Mirror Sheet
This type of sheeting has lots going for it and can be used to make objects of different shapes, sizes, colors, and transparencies. Its “two-way” mirror features, along with the extra strength and impact resistance, make it ideal for car mirrors, store displays, and public bathrooms. It’s also surprisingly affordable and works well as an electrical insulator—it’s used in electronic devices and dielectric in high-stability capacitors. Here’s an example of how this PC form can be used:
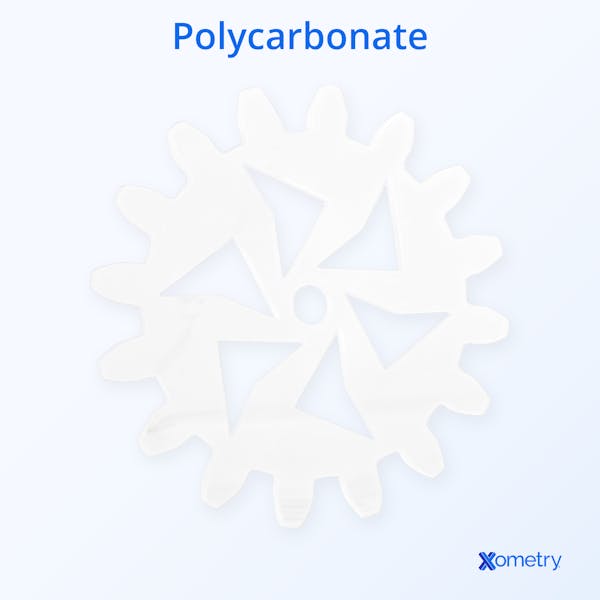
Frequently Asked Questions about Polycarbonate
Is polycarbonate toxic?
Not always. Many types of PC used today are fine, but the ones to be wary of are the non-food grade PCs because the BPA can be released when in contact with water, and if that comes into contact with food, you’re in trouble. That’s why many PC types made today don’t contain BPA.
How do polycarbonate and acrylic differ?
PC is much stronger than acrylic—17 times more impact-resistant to be precise—so it’s little wonder it’s used for making bullet-resistant windows. Acrylic tends to be more glossy with higher transparency and is better suited for making display cases, though it’s easier to fracture. It’s more cost-effective than PC, can be heated and molded into any shape, and reheated without losing its form.
Is polycarbonate a sustainable material?
PC can be considered sustainable because it has a long lifespan and is fully recyclable. But… it relies heavily on petrochemicals… not the best for our planet and not exactly sustainable. One way industries could potentially make this material more sustainable is to increase their rate of recycling and find ways to reduce reliance on BPA and fossil fuels.
What materials is polycarbonate compatible with?
PC gets along with quite a few materials but not all of them. It can handle mineral and mild acids, alcohol, gentle soaps, and silicone-based oils and greases. It’s fine with low levels of alkalis and even petroleum oils that don’t have any extra chemicals. Any super strong stuff—like benzene, toluene, gasoline, acetone, and other aromatic and halogenated solvents—can make PC turn white and weaken. Methyl ethyl ketone and strong acids like hydrochloric acid could make it crack.
Some manufacturers have made special coatings that can be more resistant to cleaning agents for things like signs and architectural panels. Like many other materials, whether PC will be able to resist chemicals depends largely on how long it’s exposed, its temperature, the chemical and its concentration, and the level of stress on the PC. It can also be combined with polyester to make it more chemical- and heat-resistant and ABS to make it more ductile.
How Xometry Can Help
Thanks to all of its benefits and wide use in almost every industry, PC is a material we’re very familiar with here at Xometry. We offer many related services, like 3D printing, laser cutting, CNC machining, and many more. You can get a free, no-obligation quote quickly by uploading your design to our Instant Quoting page, or contact one of our representatives if you have any PC-related queries.
Disclaimer
The content appearing on this webpage is for informational purposes only. Xometry makes no representation or warranty of any kind, be it expressed or implied, as to the accuracy, completeness, or validity of the information. Any performance parameters, geometric tolerances, specific design features, quality and types of materials, or processes should not be inferred to represent what will be delivered by third-party suppliers or manufacturers through Xometry’s network. Buyers seeking quotes for parts are responsible for defining the specific requirements for those parts. Please refer to our terms and conditions for more information.
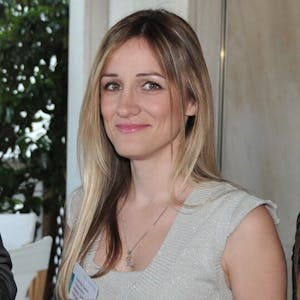