There’s no doubt that PC (polycarbonate) and ABS (acrylonitrile butadiene styrene) are among the most widely used industrial materials, made into everything from pipes and tubes to medical equipment and luggage. They’re both versatile and reliable and can sometimes be used interchangeably—but not always. Let’s have a look at the properties of each and how they differ.
What is Polycarbonate?
PC is a type of thermoplastic polyester known for its impressive mechanical properties. You’ll likely have come across it under brand names like Lexan, Makrolon, or Palgard. It’s usually made through a chemical reaction between phosgene gas and bisphenol A, known as BPA. Another way it can be made is through the reaction of BPA with diphenyl carbonate in a process called transesterification, which involves one type of ester being converted into another. You don’t, however, have to use BPA to make PC. You could use an alternative.
PC is a very tough and strong material. It’s perfect for situations that require good resistance to impact and high-temperature environments while being transparent. It can absorb more energy than some other materials because it has non-crystalline, loosely packed polymer chains. That’s also why it’s transparent: light can travel through the gaps in the chains.
You can shape this plastic using many different methods, including press brake bending, injection molding, extrusion, FDM (fused deposition modeling) 3D printing, and machining. For 3D printing, you’ll need special high-temperature equipment because of PC’s high glass transition temperature. It’s also great for prototypes because you can process it at room temperature using the techniques used for sheet metal machining. You can see what the material looks like when used in 3D printing:
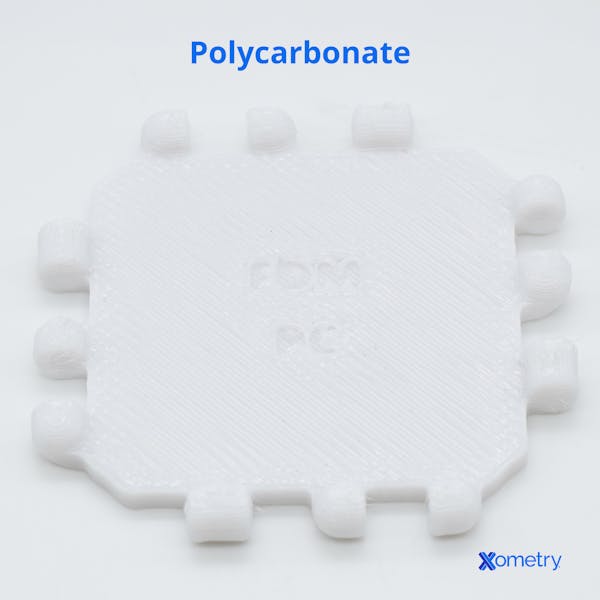
This material doesn’t have to be used in its simplest form. You can add additives to adjust its toughness, chemical or heat resistance, and ductility, and you can generally find different grades of PC that vary in toughness, strength, and flexibility. Another thing you could try is using certain coatings that can make it more resistant to scratches.
What is ABS?
ABS is a very durable and rigid thermoplastic polymer that’s dimensionally stable. It’s impressively resistant to warping and scratches and looks great, too. To make it, acrylonitrile and styrene are polymerized with polybutadiene, and the ratio of these monomers can be adjusted as needed to get different ABS grades. The general rule is this: more acrylonitrile will make it stronger due to extra polar bonds between the nitrile chains, more styrene will increase its rigidity and make it shinier, and more polybutadiene will make it tougher and resistant to harder impact.
ABS can be mixed with other materials, too. Actually, adding PC to the mix will create PC-ABS, another rather prominent substance that exhibits the best of both, namely ductility, processability, scratch resistance (from ABS), and heat resistance and toughness (from PC). ABS alone can be tampered with in terms of its properties. For example, if you add glass fibers to it, you could make it stiffer. You can also switch its surface finish between glossy and matte and dye it using a variety of pigments.
This substance is used a lot in processes like injection molding and FDM 3D printing. The reason many of our customers love using it for additive manufacturing is because it can be extruded at relatively low temperatures, so it doesn’t need any special high-temperature-rated equipment. This image shows an example of 3D-printed ABS components we made in-house:
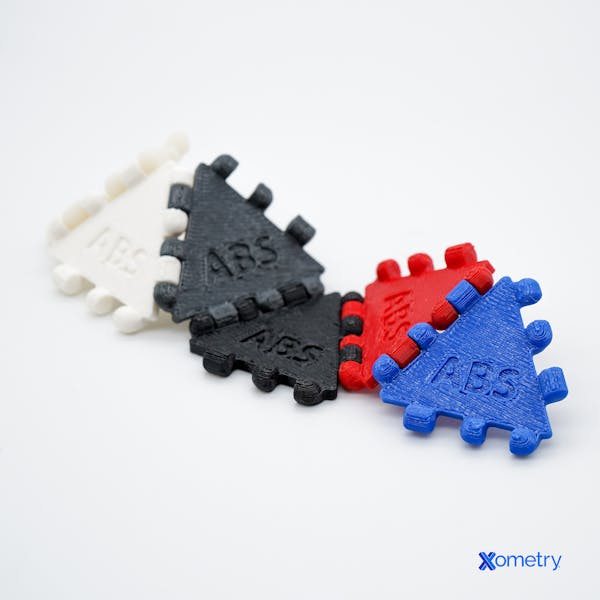
Property | Polycarbonate | ABS |
---|---|---|
Property Tensile strength (MPa) | Polycarbonate 58.6–154 | ABS 31–50 |
Property Heat deflection temperature (°C) | Polycarbonate 132 | ABS 97 |
Property Water absorption (%) | Polycarbonate $0 | ABS $2 |
Property Hardness (Rockwell R) | Polycarbonate 72–126 | ABS 68–118 |
Property UV resistance | Polycarbonate Yes, after adding a UV stabilizer before molding/extrusion or a coating on its surface | ABS Yes |
Property Elongation (%) | Polycarbonate 60 | ABS 48 |
Property Young’s modulus - rigidity (GPa) | Polycarbonate 1.79–6 (average 2.37) | ABS 0.778–6.1 (average 2.15) |
Property Weldability | Polycarbonate High | ABS Low |
Property Cost | Polycarbonate More expensive than ABS (by up to 50%), approx. $31/kg for standard PC sheeting and $1.52/kg for pellets | ABS Less expensive, approx $20/kg, and $0.90/kg for pellets |
Property Applications | Polycarbonate Insulation layers and glass alternative in construction, food containers, bullet-proof windows, safety equipment (visors, screens, etc.), electronics | ABS Light switches, office equipment, toys, vehicle interiors, housings for electronic devices |
Polycarbonate vs. ABS Properties
Frequently Asked Questions on PC and ABS
Are these plastics recyclable and sustainable?
They are! If heated above their respective melting points, they’ll turn into liquid and can immediately be injection molded into new shapes or made into pellets for later use. They can both be recycled several times and it won’t degrade their material properties. PC can also be recycled chemically using a zinc-based catalyst. This involves isolating pure BPA, which is purified using water and then dried. The BPA can later be reused and mixed with sodium hydroxide and phosgene to create new PC, and that can be shaped into final parts or pellets. Another good thing about this method is that it produces eco-friendly byproducts like dimethyl carbonate. This sounds great, doesn’t it? Unfortunately, there’s a caveat. Both of these materials have a resin identification code of 7, meaning it can be tricky to find a recycling facility in the U.S. that accepts them (most do not).
PC vs. PMMA—what’s the difference?
PMMA stands for polymethyl methacrylate and is also known as acrylic or Perspex. It’s similar to PC in that it’s optically clear, especially in sheet form. The downside is that PMMA is more brittle and could possibly crack if it’s in a situation where it’ll be exposed to high impact.
ABS vs. ASA—what’s the difference?
ASA (acrylonitrile styrene acrylate) has some similar properties to ABS. It has high impact strength and performs really well throughout a range of temperatures. It also has very impressive resistance to ultraviolet light, low water absorption (varies between grades), and can tackle adverse weather conditions with ease. So, if you’re looking for a great automotive exterior material, ASA is probably the way to go.
How Xometry Can Help
If you need any help or have more questions on this topic or anything else manufacturing-related, feel free to reach out to one of our representatives. If you like what you’ve read in this article about PC and ABS, and want to use them in your next 3D printing project, you can request a free, no-obligation quote to get started ASAP.
Copyright and Trademark Notices
- PERSPEX® is a registered trademark of PERSPEX INTERNATIONAL LIMITED.
- Lexan™ is a trademark of GE Plastics.
- Makrolon® is a registered trademark of COVESTRO INTELLECTUAL PROPERTY GMBH & CO. KG.
- Palgard™ is a trademark of PALRAM INDUSTRIES LTD.
Disclaimer
The content appearing on this webpage is for informational purposes only. Xometry makes no representation or warranty of any kind, be it expressed or implied, as to the accuracy, completeness, or validity of the information. Any performance parameters, geometric tolerances, specific design features, quality and types of materials, or processes should not be inferred to represent what will be delivered by third-party suppliers or manufacturers through Xometry’s network. Buyers seeking quotes for parts are responsible for defining the specific requirements for those parts. Please refer to our terms and conditions for more information.
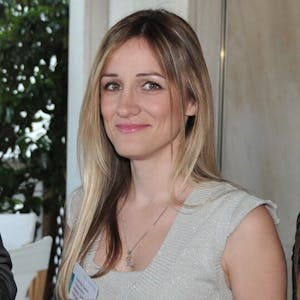