Polycarbonate (PC) is a thermoplastic that transmits visible light even better than glass but blocks much of the UV spectrum. It is commonly employed as a more durable substitute for glass. PC is widely used in optical and protective applications because of its high refractive index and its impact and heat resistance. It is used for lighting components in the automotive sector, optical and protective eyewear, agricultural glazing, and medical devices.
PVC (polyvinyl chloride) is a synthetic polymer that comes in two basic forms: flexible and rigid. It is the third-most manufactured polymer, after polyethylene and polypropylene, due to its durability, low cost, and easy processability. PVC finds uses in electric cables, pipes, signs, clothing, and construction.
This article will compare polycarbonate vs PVC in terms of properties, applications, costs, and sustainability.
What Is Polycarbonate?
Polycarbonate is the first choice in many optical- and durability-focused applications. Though its scratch resistance is not good, this can be countered with hard coatings that are increasingly effective and now come quite cheaply. It is ideal for spectacles and lenses due to its high refractive index, at 1.58, enabling slimmer lenses for equal focal effect.
Polycarbonate is often considered interchangeable with acrylic (polymethylmethacrylate or PMMA), though it loses out in terms of refractive index (1.48 for PMMA). Extruded PC sheet offers better light transmission than glass, making it a popular alternative. High-molecular-weight grades of PC offer better properties than lower-weight materials, but the lower-weight grades are easier to process. On this basis, the higher weight grades are widely used in aerospace construction, such as in aircraft windows.
Automotive manufacturers value the clarity and toughness of PCs, using them extensively in lighting applications where clarity and chip resilience is beneficial. Though it has relatively poor UV stability, the use of hard UV reflective coatings and antioxidants increase the material’s effective life to acceptable levels. Vehicle headlight covers don’t fail through yellowing and embrittlement the way they used to. Similarly, PC is useful for skylight and greenhouse roofing applications, as it is tough, quite cheap, very transparent to useful wavelengths, and almost opaque to UV.
PC is very significant as a copolymer additive, lending strength, and resilience to other polymers. PC is extremely vulnerable to attacks by oils, however, which rapidly break the polymer down. For more information, see our guide on What is Polycarbonate Material.
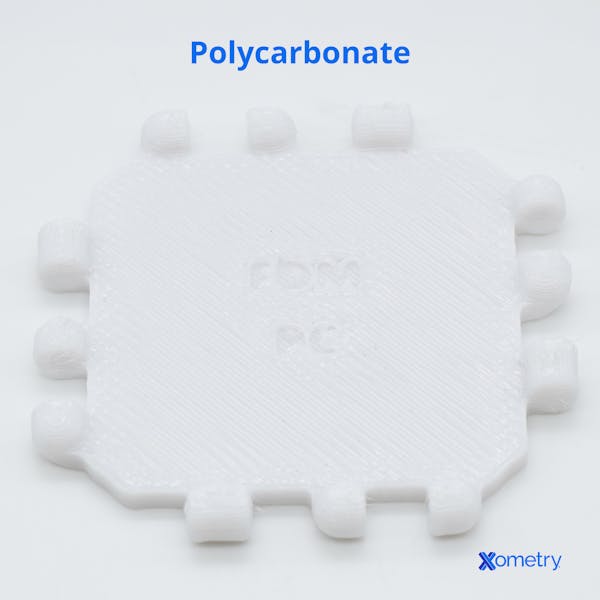
What Is PVC?
PVC is a simple chain polymer made up of vinyl chloride monomers. It is manufactured by three methods: suspension, emulsion, and bulk polymerization. This results in slight variations in properties, but additional polymerized material added after the fact makes it brittle and has no useful applications.
Each has some advantages, so no single process is universal. All three deliver polymers of the formula (C2H3Cl)n, varying only in particle size in the raw, newly polymerized state. C2H3Cl is vinyl chloride and the n indicates that this monomer is repeated in chains. To be converted into the materials seen widely today, a range of additives and property modifiers like those below are often necessary:
- Thermal stabilizers that raise the maximum service temperature.
- Plasticizers that turn the more brittle pure material into a malleable and tough polymer.
- Impact modifiers to reduce brittleness and shock fracture.
- UV stabilizers that slow the degradation in sunlight.
- Smoke suppressors to reduce toxic gas release during combustion.
- Blowing agents which increase the toughness of the softened plastic during extension.
- Processing agents that reduce the melt viscosity and melt flow index in molding and extrusion.
- Biocides to reduce environmental staining.
The application specifies which additives are necessary. They have given rise to many specialist materials based around this simple and chemically uniform polymer. Figure 1 is an example of PVC pipe:
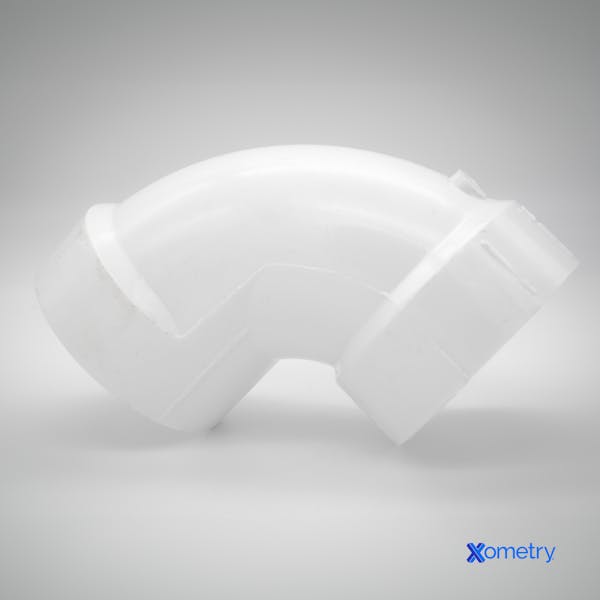
The PVC that is so widely used today comes in two basic forms:
- Plasticized: An elastic, soft, and highly extendible material with many desirable properties as a barrier, coating, film, and textile.
- Unplasticized: Designed for extruded and molded components, this material is rigid, tough, chemically resilient, and inexpensive.
Polycarbonate vs. PVC: Applications and Uses
The main applications for polycarbonate (extruded sheet and molded parts) are listed below:
- Medical equipment: Cameras, lenses, medical tools.
- Eye protection: Safety glasses and face shields.
- Optical lenses: Spectacle lenses, instrument lenses, fiber optic cables, and light guides.
- Auto: Headlight covers and lenses.
- Media discs: Blu-ray discs, DVDs, etc.
- Display stands and advertising weatherproofing: Advertising panels, protective billboard overlays, weather shields, and vandal-proof panels/windows in public spaces, bus stops, etc.
- Armored, vandal-resistant, and bulletproof windows: For vehicles and personnel protection.
- Agriculture: Greenhouse paneling.
- Luggage: Bags and suitcases.
Polycarbonate vs. PVC: Physical Properties
Table 1 lists the properties of polycarbonate and PVC:
Property | PC Value (metric) | UPVC Value (metric) | PVC Value (metric) |
---|---|---|---|
Property Optical transmission | PC
Value (metric) Very high — better than glass in the optical range | UPVC
Value (metric) Opaque | PVC
Value (metric) Good, but depends heavily on compounding agents |
Property Density | PC
Value (metric) 1.2 g/cm3 | UPVC
Value (metric) 1.3-1.45 g/cm3 | PVC
Value (metric) 0.92-1.89 g/cm3 |
Property Hardness, Shore D | PC
Value (metric) 90-95 | UPVC
Value (metric) 37-88 | PVC
Value (metric) 34 -83 |
Property Tensile strength, ultimate | PC
Value (metric) 28-75 MPa | UPVC
Value (metric) 14.3-53.7 MPa | PVC
Value (metric) 0.76-156 MPa |
Property Tensile strength, yield | PC
Value (metric) 39-70 MPa | UPVC
Value (metric) 3.45-73.1 MPa | PVC
Value (metric) 0.121-50 MPa |
Property Elongation at break | PC
Value (metric) 10-138% | UPVC
Value (metric) -330% | PVC
Value (metric) 16-700% |
Property Modulus of elasticity | PC
Value (metric) 1.79-3.24 GPa | UPVC
Value (metric) 1.82-7.03 GPa | PVC
Value (metric) 0.0055-3.23 GPa |
Property Flexural yield strength | PC
Value (metric) 36-103 MPa | UPVC
Value (metric) 50.7-104 GPa | PVC
Value (metric) — |
Property Flexural modulus | PC
Value (metric) 0.971-3.1 GPa | UPVC
Value (metric) 0.22-6.43 GPa | PVC
Value (metric) 0.075-3 GPa |
Property Dielectric constant | PC
Value (metric) 2.85-3.17 | UPVC
Value (metric) 3-3.3 | PVC
Value (metric) 2.87-7.04 |
Property Melting point | PC
Value (metric) 288-316 °C | UPVC
Value (metric) 100-260 °C | PVC
Value (metric) 140-210 °C |
Property Max service temperature | PC
Value (metric) 115-135 °C | UPVC
Value (metric) 60-190 °C | PVC
Value (metric) 40-194 °C |
Polycarbonate vs. PVC: Cost
Polycarbonate is a low-volume, specialist, and high-cost material, coming in at around $2.80 per kg. Recycled material of near-top grade PC can sell for $1.60 per kg if it comes from a consistent supply chain. PVC, on the other hand, is widely available from many manufacturers. It is a commodity material, with sources being interchangeable (with established specifications). The virgin material price for UPVC granules is $0.80-2.00 per kg.
Alternative Materials to Polycarbonate and PVC
Alternative materials for the usual polycarbonate applications are highly dependent on the intended use. Examples are:
- Acrylic offers better scratch resistance and can be formed at lower temperatures, but it lacks impact and tensile resilience. While it has good clarity, the lower refractive index makes it unsuitable for lenses.
- The urethane material Trivex® offers a refractive index that is almost as good as PC while suffering less residual stresses. Combined, that makes for better optical properties.
- Where poorer transparency is acceptable, polystyrene (PS) is an alternative to PC, though much weaker and more brittle. For zero-stress applications such as light pipes/guides, PS can save costs without significantly affecting light transmission.
- In many applications, ABS and ABS/PC copolymers are alternatives to pure PC, achieving high strength with easier processing and lower cost.
PVC is used in two primary forms (rigid and flexible), with very different applications. Some examples are:
- For piping application, rigid PVC can be replaced with either low-density or high-density polyethylene (LDPE or HDPE), depending on applied loads.
- For packaging applications, clear rigid PVC can be substituted with polypropylene (PP), polyethylene terephthalate (PET), and polystyrene (PS).
- For architectural fixtures such as window and door frames, polymer alternatives to PVC are not used, but more traditional materials such as wood or more rigid solutions such as Aluminum extrusions are common.
- For flexible applications such as clothing and toys, various thermoplastic and thermoset rubbers can be applied as coatings to make fabrics waterproof and airtight.
- For cable sheaths, various silicone rubber, and thermoplastic rubbers are used as alternatives to flexible PVC.
Summary
This article presented polycarbonate and PVC materials, explained what they are, and discussed the comparisons of each material. To learn more about polycarbonate and PVC, contact a Xometry representative.
Xometry provides a wide range of manufacturing capabilities and other value-added services for all of your prototyping and production needs. Visit our website to learn more or to request a free, no-obligation quote.
Copyright and Trademark Notices
- Dupont™ is a registered trademark of the E.I. DuPont de Nemours Company
- Trivex® is a registered trademark of PPG Industries, Inc.
Disclaimer
The content appearing on this webpage is for informational purposes only. Xometry makes no representation or warranty of any kind, be it expressed or implied, as to the accuracy, completeness, or validity of the information. Any performance parameters, geometric tolerances, specific design features, quality and types of materials, or processes should not be inferred to represent what will be delivered by third-party suppliers or manufacturers through Xometry’s network. Buyers seeking quotes for parts are responsible for defining the specific requirements for those parts. Please refer to our terms and conditions for more information.
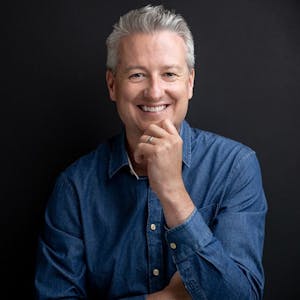