Precipitation hardening of stainless steel is a process that is used for making an excellent class of alloys that have the advantages of both martensitic and austenitic grades of steel. The specialized heat treatment process that they go through gives the alloys increased tensile strength (from 850 MPa to 1,700 MPa) while keeping their effectiveness and ductility.
The precipitation hardening (PH) process has been adopted by many Xometry users in all different industries, from oil & gas to aerospace. There are several steps involved in precipitation hardening, including dissolving, rapid cooling, and aging, and we’ll look at each of these below in detail. We’ll also cover just what precipitation-hardened stainless steel is, how it works, and its advantages and disadvantages.
What is Precipitation Hardening of Stainless Steel?
Precipitation hardening of stainless steels creates a family of alloys made up of iron, chromium, and nickel. PH steel is created when we add aluminum, copper, molybdenum, titanium, or niobium and then heat treat it. One or more of these materials can be added, and the final result offers the perfect blend of martensitic and austenitic grade characteristics.
The process gives the material all the good martensitic and austenitic benefits, namely enhanced strength and corrosion resistance respectively. PH stainless steels have tensile strengths ranging from 850 MPa to 1,700 MPa, and yield strengths from 520 MPa to over 1,500 MPa.
The treated steel can have elongation levels from 1 to 25%, and cold working the steel before aging can make it even stronger. PH stainless steel alloys are available in annealed (Condition A) and tempered (Condition C) states. Annealed state alloys are relatively soft and malleable, with Rockwell hardness ranging from B75 to C20. For a higher Rockwell hardness of C35 to C49, the parts can then go through the age-hardening process.
The main purpose of PH stainless steel is to create a material with the strengths of both austenitic and martensitic stainless steels, namely exceptional strength and corrosion resistance. PH is often used in aerospace, marine, medical, and automotive industries as the controlled heat treatment allows engineers to bespoke the material's properties according to their exact needs.
History of Precipitation Hardening Stainless Steel
The process of precipitation hardening stainless steel dates back to the early 20th century. In 1929, an inventor from Luxembourg, William J. Kroll discovered that adding titanium to stainless steel, then heat treating it, made the steel much stronger. After that, he created the Kroll process—the method of making metallic titanium from titanium tetrachloride. In the 1940s, precipitation hardening metals gained momentum, and the first martensitic PH stainless steel was designed.
In 1948, the American Rolling Mill Company’s work led to the birth of 17-4 PH steel which has been widely used since in aircraft landing frames, fasteners, and engine components, and is a popular choice among Xometry customers. 15-5 PH stainless steel entered the scene when chromium use was reduced and replaced by nickel within the 17-4 PH group. The advancements in technology and science in recent years has led to a mass rise in PH stainless steel. One of these newer PH steels, Ferrium S53, is used in aerospace thanks to its corrosion resistance and high strength, and is an example of just how far PH has come.
How Precipitation Hardening Stainless Steel Works
Precipitation hardening stainless steel works through a controlled heat treatment process that gives PH stainless steel improved strength by forming fine precipitates within its microstructure. The process starts by heating the alloy with a solution treatment which then turns into a solid solution. This step is followed by rapid cooling (or quenching) which traps the alloying elements in the crystal structure. The last step is aging. This is where the metal is reheated and turned into fine particles. This phase stops any potential dislocation or movement, and increases the material’s strength. For extra strength and hardness, some choose to cold work the material during the aging process.
Process Phases of Precipitation Hardening Stainless Steel
The PH process involves three main phases—solutionizing (heating to dissolve alloying elements), quenching (rapid cooling to trap these elements in solution), and aging (controlled reheating to allow the precipitates to form)—where the metal goes through a series of metallurgical changes during heat treatment.
Here's a general overview of how the PH process works.
1. Solutionizing
The first PH step is known as solutionizing. Also known as the "solution treatment," this step involves dissolving precipitates and minimizing the potential for the alloy to separate. The material is heated to its solvus temperature and kept there until a uniform solid solution is made. It is then taken away from the heat source.
2. Quenching
The next stage involves the rapid cooling or “quenching” of the alloy. By cooling the material so quickly, a supersaturated solid solution with lots of extra copper components is created. The quickness also prevents nucleation sites and precipitates from forming on the alloy.
3. Aging
The final stage in the PH process is aging. This is where the material goes through more heat treating, but this time below the solvus temperature. This allows the atoms to diffuse slightly over short distances, resulting in the creation of finely dispersed precipitate layers within the material. It makes the alloy stronger by limiting dislocation movement. To achieve maximum strength it is crucial that the material is aged for the optimal amount of time, otherwise precipitates may be too small (underaged) or too large (overaged) to effectively prevent dislocation movement. The aging-to-strength curve is outlined in the graphic below:
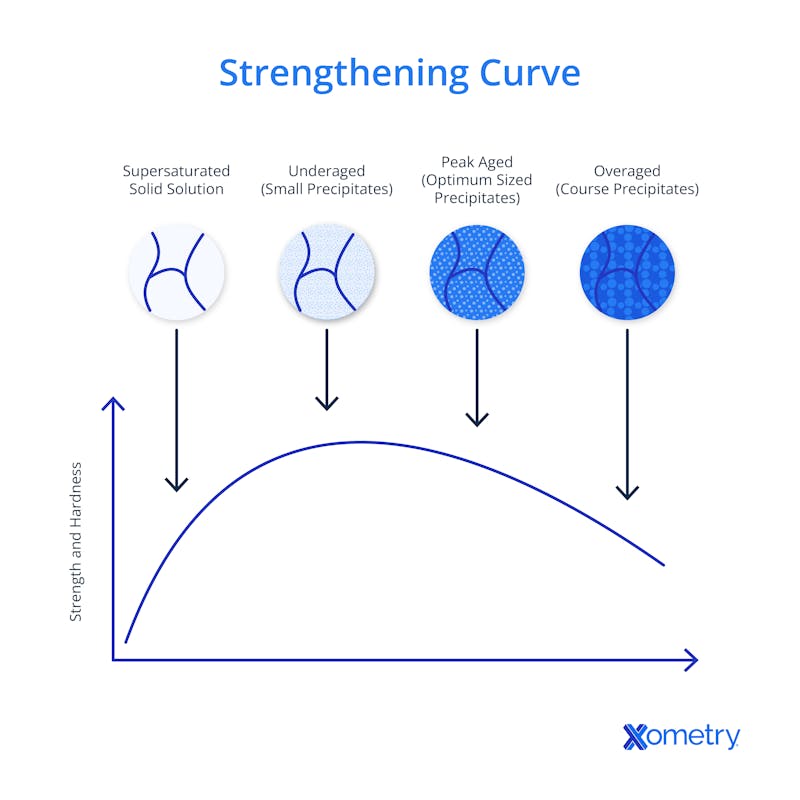
Requirements of Precipitation Hardening Stainless Steel
PH stainless steels have specific requirements to make them suitable for different uses. First, their alloy composition includes elements like iron, chromium, nickel, and additional additives such as copper, aluminum, and titanium. These materials are important in the PH process as they give the final material its amount of strength and corrosion resistance.
Another important requirement for creating the proper microstructure for a strong, durable, and resistant steel is sticking to the above process phases (solution treatment, quenching, and aging). Ultimately, you want the best balance between strength and impact resistance. Weldability is another requirement to prevent cracking, and loss of mechanical properties, and corrosion resistance during welding.
How Long Precipitation Hardening Stainless Steel Takes
Precipitation hardening can be a sluggish process lasting anywhere from one to 24 hours. The dissolving stage can last up to four hours. The quickest phase is quenching which usually takes just a few minutes. The length of the aging step can vary, but it can last up to a day. If you go for the natural aging method, this can last a few weeks. Depending on the result you’re after, there are different times for each step, so precise calculations of both time and temperature are important.
For your ease of reference, we’ve put the optimal hardening temperatures and duration for some alloys in the table below.
Type | Hardening Temperature | Hardening Time |
---|---|---|
Type H900 | Hardening Temperature 482 °C | Hardening Time 1 hour |
Type H925 | Hardening Temperature 496 °C | Hardening Time 4 hours |
Type H1025 | Hardening Temperature 552 °C | Hardening Time 4 hours |
Type H1075 | Hardening Temperature 580 °C | Hardening Time 4 hours |
Type H1100 | Hardening Temperature 593 °C | Hardening Time 4 hours |
Type H1150 | Hardening Temperature 621 °C | Hardening Time 4 hours |
Table Credit: https://www.azom.com/article.aspx?ArticleID=2819
Temperature At Which Precipitation Hardening of Stainless Steel Occurs
The temperature that PH of stainless steel occurs depends on the different stainless steel types and your desired outcome. Martensitic PH steels, for example 17-4 PH, goes through the martensite transformation at the relatively low temperature of around 250 °C. Kicking it up a few notches to anywhere between 480 °C and 620 °C will make the material even stronger.
Austenitic-martensitic PH steels are already fully austenitic after just the solution treatment. To start the martensite process, another heat treatment at 750 °C for two hours, followed by cooling to room temperature, is necessary. Some alloys need to be refrigerated at temperatures as low as -50 °C to -60 °C for eight hours to get that stable austenitic/martensitic structure.
Different Types of Precipitation-Hardened Stainless Steel
The different types of PH stainless steel are characterized into four groups, based on their final microstructures after the heat treatment. These are:
1. Semi-Austenitic PH Stainless Steels
Once cooled from the annealing temperature to room temperature, the semi-austenitic PH steels will keep its austenitic make-up which is tough and ductile, and better suited for cold-forming processes than martensitic PH steels that tend to be rather on the hard side. To harden and strengthen this type of steel, it must first be converted from austenite to martensite which will then prep the material for the aging process. To reduce the presence of austenite-stabilizing elements, semi-austenitic PH steels need to be heated to 650–870 °C.
This partially transforms the material to martensite upon it’s cooled to room temperature, but it can also be achieved by refrigeration below the beginning of martensite transformation (Ms temperature) or through cold working. The reinforcement of semi-austenitic PH stainless steels has a two-step approach. After the initial martensite treatment, the second phase involves exposure to the aging temperature of 455–593 °C, which leads to precipitation, resulting in hardness and overall strengthening.
2. Austenitic PH Stainless Steels
Austenitic alloys keep their structures through annealing and aging. At the annealing temperature of 1,095–1,120 °C, the precipitation hardening phase dissolves and stays in the solution during rapid cooling. Precipitation happens when the alloys are reheated at 650 to 760 °C. This results in increased hardness and strength (although it won’t be as hard as its martensitic or semi-austenitic counterparts) and they’ll also keep their non-magnetic properties.
3. Welding PH Stainless Steels
Welding will bring out areas of solution-treated or annealed base metal. For optimal harness in these zones, you may have to do some double or single post-weld heat treatments. The steel manufacturer will be your best point of call for welding and treatment guidance on the particular steel that you’re working with, but if you have any good books on the subject, you can always refer to them. Thinner PH stainless steel sections generally don’t need any preheating before welding. The martensitic PH grades, which have low-carbon content, don’t go through a full hardening like, for instance, the type 410.
With single-pass welds, both the weld metal and the heat-affected zones tend to respond together to post-weld precipitation hardening treatments. Multiple-pass welds aren’t as uniform and this tends to cause differences in the base and weld metals, and the heat-affected zones. Annealing after welding will ensure a more consistent and uniform outcome.
For example, when welding a 17-4 PH plate that’s under four inches thick, you might find that the instructions will recommend interpass temperatures up to 150 °C, but preheating isn't mandatory. When it comes to 17-4 PH with plate thicknesses of over four inches, preheating at 95 °C and keeping an interpass temperature of 95–260 °C will likely be necessary. When welding 17-4 PH using bare ER630 wire, you can use argon for GMAW welding, or helium/argon gas for GTAW welding.
4. Martensitic PH Stainless Steels
At annealing temperatures ranging from approximately 1,040 to 1,065 °C, martensitic alloys, in particular, will have mainly austenitic structures. When cooled to room temperature, these alloys go through a transformative process that turns the austenite structure into martensite. Quickly cooling the material in air or oil after that will keep the additives, like copper and columbium, within the solid solution at room temperature. The austenite to martensite transformation happens at roughly 150 °C to room temperature. After that, reheating this supersaturated solid solution in the martensite matrix at the aging temperature of 482 °C to 593 °C will produce minute particles precipitate for an even harder and stronger result.
Need Custom PH Stainless Steel Parts?
Precipitation-Hardened Stainless Steel—Applications
Precipitation-hardened steel is used in many industries and sectors. In the oil & gas industry, the PH of steel is used for gates, valves, machinery components, retaining rings, springs, and spring holders. In automotive, it’s used for engine parts, gears, shafts, balls, plungers, bushings, chains, valves, and gears. PH steel is also used on aircraft components, airplane engine parts, and turbine blades. Other uses include valve stems, molding dies, processing equipment, fasteners, nuclear waste containers including pressure vessels, and seals in general industrial use.
Advantages of Precipitation Hardening Stainless Steel
There are many advantages to PH stainless steel, and these far outweigh the disadvantages. Thanks to the development of a sturdier microstructure within the metal, PH can make metal up to four times stronger. The process can also improve the material’s ductility which will help against cracking and breakage. It makes the metal more corrosion resistant, and gives it a sort of shield against wear and tear.
Disadvantages of Precipitation Hardening Stainless Steel
Despite its advantages, PH does come with a few cons that need consideration. Using too high a heat during the PH process can make the metal brittle, or cause it to crack or warp during the quenching phase. It’s also a time-consuming and intricate process that needs very specialized equipment which is sometimes hard to get. It also requires expertise, and precise time and temperature calculations (which is why it’s typically reserved for high-end applications where increased strength justifies the higher investment). Its high cost, lengthy process, and demand for precision means that it’s not always feasible for some applications and can lead to higher material costs.
If you are interested in utilizing PH stainless steel for your next project, be sure to use the Xometry Instant Quoting Engine® to get an instant quote on a variety of materials, including 17-4 PH and 15-5 PH stainless steels.
Copyright and Trademark Notices
- Ferrium® S53® is a registered trademark of QuesTek Innovations LLC.
Disclaimer
The content appearing on this webpage is for informational purposes only. Xometry makes no representation or warranty of any kind, be it expressed or implied, as to the accuracy, completeness, or validity of the information. Any performance parameters, geometric tolerances, specific design features, quality and types of materials, or processes should not be inferred to represent what will be delivered by third-party suppliers or manufacturers through Xometry’s network. Buyers seeking quotes for parts are responsible for defining the specific requirements for those parts. Please refer to our terms and conditions for more information.
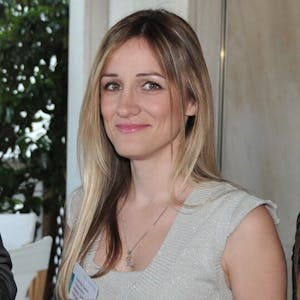