Silicones are an exciting group of polymeric materials available in a number of different forms. Their properties give them a nearly limitless potential for tailoring to the exacting requirements of the medical and aerospace industries. They can seal, lubricate, and satisfy a wide range of other applications.
This article will discuss the physical and mechanical properties that make silicone so useful. It will also introduce the four main groups of silicone materials, touch on manufacturing methods, and explain why silicone could be the perfect material for your application. The table below summarizes the properties of silicone and offers a brief description of each:
Properties of Silicone | Description |
---|---|
Properties of Silicone Chemical Reactivity | Description Generally non-reactive |
Properties of Silicone Thermal Conductivity | Description Naturally low thermal conductivity; can be increased as needed by adjusting formulation |
Properties of Silicone Toxicity | Description Non-toxic when used appropriately, with FDA-approved medical and food grades |
Properties of Silicone Water Repellency | Description Highly water repellent |
Properties of Silicone Sealing Ability | Description Excellent adhesion to smooth surfaces; forms watertight seals |
Properties of Silicone Resistance to Oxygen, Ozone, and Ultraviolet Light | Description Extremely resistant to degradation by both radiation and oxidation |
Properties of Silicone Electrical Conductivity | Description Natural insulator, but the addition of filler materials can make silicone conductive |
Properties of Silicone Gas Permeability | Description Highly permeable to gas molecules |
Properties of Silicone Thermal Stability | Description Physical and mechanical properties remain stable across a wide temperature range |
Properties of Silicone Organic Solvent Resistance | Description Resistant to attack by most chemicals. |
Table 1. Properties of Silicone
1. Silicones Are Non-Chemically Reactive and Have Low Thermal Conductivity
It takes a lot of energy to break the bonds of the silicon-oxygen chains that form the polymeric skeleton of silicone molecules. Because most chemicals that silicones come into contact with do not have enough energy to overcome the silicone molecule’s resistance to change, there is little driving force for chemical reactions. Thus, silicone is considered generally non-chemically reactive. These stable silicone bonds are the basis for many of the desirable properties of silicone.
Silicones generally have low thermal conductivity. This is because the molecular structure of silicone tends to impede the transfer of heat vibrations from one molecule to the next. This can be desirable for some uses of silicone, like oven mitts. But in other situations, the inability to efficiently transfer heat is a problem. In that case, thermally conductive fillers can be added to the silicone formulation to improve the heat transfer required for the intended application.
2. Silicone Toxicity Is Also Low
Silicone is considered a very safe material for human health. Food-grade and medical-grade silicone compounds are FDA-approved for use in contact with the food we eat every day, and even for long-term implantation in the human body. As with all chemicals, however, it is important to use silicone products according to the manufacturer’s instructions to maintain the highest levels of safety.
3. Silicone Has the Ability To Repel Water and Form Watertight Seals
Silicone is what is known as a “hydrophobic” material. It repels water. This is because the methyl groups attached to the silicon-oxygen polymer chain are non-polar in nature. It is not attracted to water molecules. Its low surface energy gives water molecules no way to spread over and penetrate the silicone surface. Instead, water beads up and runs off. This great water repellency, combined with silicone’s ability to form a tight adhesive bond with many surfaces, means that silicone sealing products can form seals that last for decades.
4. Silicone Has a High Resistance to Oxygen, Ozone, and UV Light
The silicon-oxygen bonds in silicones are more stable than those between the carbon atoms in organic polymer chains. The amount of energy that can be provided by UV light is higher than that needed to break down C-C bonds, but not enough to damage Si-O bonds. This is why silicones are more resistant to UV light and oxidation than carbon-based plastics. Silicones can be used for components exposed to harsh outdoor weather.
5. Silicone Is Electrically Insulative As Well as Conductive
Standard silicone rubber is naturally an insulator. It has no free electrons available to carry a positive or negative charge. That is perfect for many applications, especially in the medical industry, where the insulative property is critical. But silicone can be coaxed into being conductive enough for applications like gaskets and static shields. This is accomplished by adding fillers to the silicone such as carbon, silver, or other conductive materials.
6. Silicone Has Excellent Gas Permeability and Thermal Stability
Silicone’s molecular chains contain openings that are large enough to allow gas molecules to pass through, but not water molecules. This combination of water repellency and gas permeability yields coatings that give us the luxury of water-resistant, breathable fabrics.
A key property of silicone rubbers is their thermal stability. Silicone maintains its critical mechanical and physical properties within defined design limits over a large range of temperatures. Depending on the exact nature of the silicone product, the minimum service temperature in the air may be as low as -136 °C, and the maximum as high as 316 °C.
7. Silicone Has Superior Resistance to Organic Compound Solvents
Silicone is resistant to attack by most chemicals due to its non-reactive structure and low surface energy. However, a few inorganic chemicals, notably sulfuric and hydrofluoric acids at high concentrations, will damage silicones. Among organic compounds which might act as solvents, toluene, mineral spirits, gasoline, and carbon tetrachloride cause deterioration in silicones only after prolonged exposure.
Why You Should Use Silicone as a Material
The properties of silicone offer numerous benefits. Here are a few ways that both manufacturers and end-users can benefit from its unique characteristics:
- Silicones are safe. They are one of the go-to materials for making implantable medical devices.
- Silicones have good dimensional stability. They maintain their strength and shape over a wide range of temperatures.
- Silicones are chemically non-reactive in most environments. They do not degrade under exposure to moisture, fuels and oils, heat, cold, salt spray, or ultraviolet light.
- Silicones can take any shape. Silicones come as liquids, viscous pastes, rubbery sheets, and hard, plastic-like consistencies. They can be used as coatings, made into injection- or compression-molded parts, stamped, formed into tubing, and used as lubricants.
Where Silicone Is Prepared
Chemical factories produce raw silicone materials. These facilities can process the required chemical precursors and catalysts in bulk, repeatedly, and precisely.
In the factory, silica (usually from sand) is turned into silicon in a high-temperature reaction with carbon. Through a sequence of complex chemical reactions, the silicon is then combined with water and methanol to form basic silicone products packaged as liquids, gels, or sheets. Component fabricators then apply the appropriate molding or other industrial processes to create final products for customers.
Silicone's Chemical Composition
Silicone, technically referred to as “polysiloxane,” consists of a chain of alternating silicon and oxygen atoms. Silicon atoms, like carbon atoms, have space for four covalent bonds with other atoms. Two of those spots are occupied by oxygen atoms, one on each side. The other two spots will bond with other molecular groups that are available. The general chemical formula for silicone is [R2SiO]n. “R” indicates whatever groups are attached to the silicon atoms. The most common, basic silicone has methyl groups (CH3) attached in the available slots, yielding an inorganic (since it is not carbon-based) polymeric structure. Technically, this is called polydimethylsiloxane.
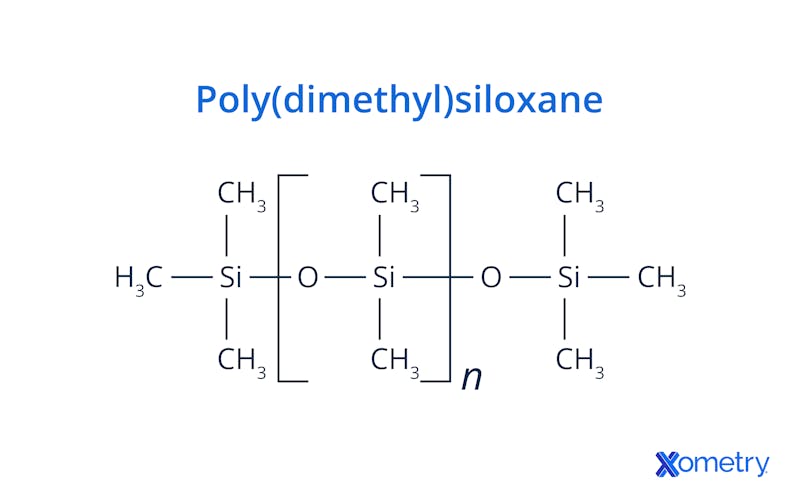
Mechanical Property | Range of Results |
---|---|
Mechanical Property Shore A Hardness (Resistance to indentation) | Range of Results 1.00–95.0 |
Mechanical Property Yield Strength (MPa) (Stress at onset of plastic deformation) | Range of Results 0.0448–145 |
Mechanical Property Tensile Strength (MPa) (Stress at failure) | Range of Results 0.138–165 |
Mechanical Property Elongation at Yield (%) (Sample deformation at yield point) | Range of Results 0.000–900 |
Mechanical Property Elongation at Break (%) (Sample deformation at tensile failure) | Range of Results 5.00–1490 |
Mechanical Property Modulus of Elasticity (GPa) (Measure of material stiffness in tension) | Range of Results 0.00000500–1.90 |
Mechanical Property Compressive Modulus (GPa) (Measure of material stiffness in compression) | Range of Results 25.0 – 65.0 |
Mechanical Property Poisson’s Ratio (Ratio of transverse to axial strain during tensile elongation) | Range of Results 0.500 |
Mechanical Property Compression Set (%) (Permanent deformation after compressive force is removed) | Range of Results 3.00–200 |
Mechanical Property Tensile Set (%) (Permanent deformation after tensile force is removed) | Range of Results 2.00–10.0 |
Mechanical Property Tear Strength (kN/m) (Force applied for crack propagation) | Range of Results 0.877–125 |
The Various Types of Silicone
The four main physical types or forms of silicone products are listed below:
- Room-temperature Vulcanizing (RTV): These silicones will cure, or set, at room temperature. They are typically used for sealing and bonding. RTV-1 formulations start curing immediately upon contact with moisture in the air. RTV-2 silicones come as two separate compounds that the end-user must combine to initiate curing. This makes RTV-2 more flexible for applications like molding and coating.
- Liquid Silicone Rubber (LSR): LSR consists of a two-component system, with the two compounds combined at the time of use. It is generally cured at a high temperature, using a platinum catalyst. Both the molding process used and the final product characteristics of LSR are adaptable to a wider range of applications.
- Fluorosilicone Rubber (FSR): FSR molecules consist of repeating units of a silicon-oxygen backbone with other bonding sites occupied by other groups of molecules (methyl and fluoroalkyl groups). This gives the material better resistance to oils and fuels. FSR is popular for sealing applications in aviation settings.
- High-Consistency Rubber (HCR): HCR, also known as “heat-curing rubber,” consists of very high molecular weight silicone polymer chains. The raw material can accommodate fillers and additives to obtain desired characteristics. It is usually furnished in a partially cured, somewhat “gummy” form that has been rolled into a thick sheet. It is ideal for use in certain medical devices, including tubing, balloons, and sheets.
Silicones can take a variety of forms, from liquid to solid. There are many variations of each type, with the properties of the silicones tailored to the needs of specific end products.
For more information, see our guide on the types of silicone.
Why Silicon Is Classified as a Metalloid
Silicon belongs to a group of elements that cannot be cleanly characterized as either metals or non-metals – so they are referred to as “metalloids.” A lump of pure silicon has that lustrous, shiny surface that we associate with metals, as can be seen in the photo below:
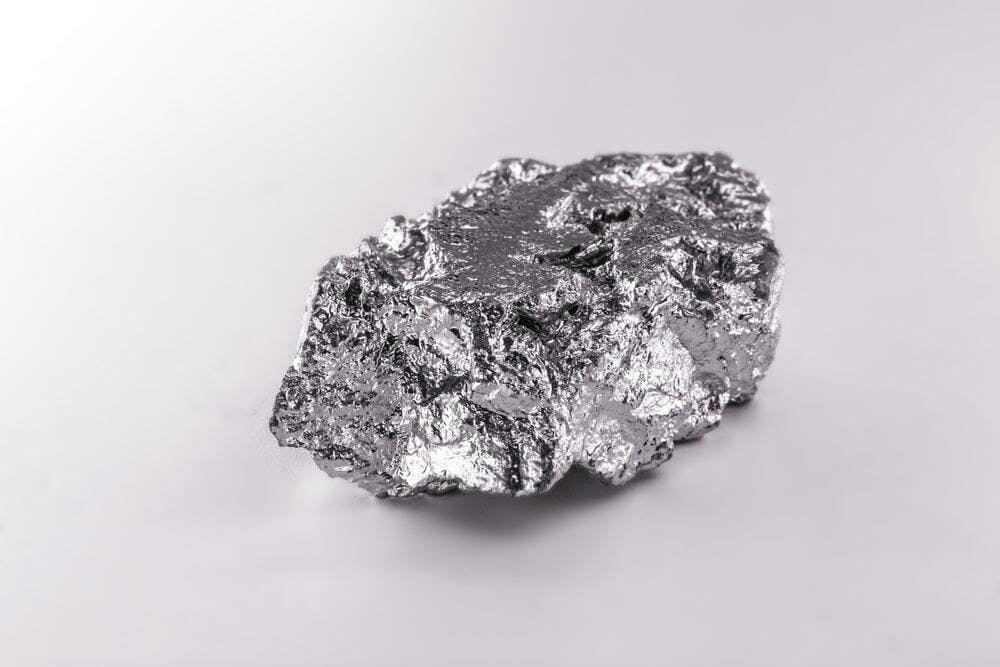
High purity polycrystalline silicone.
Image Credit: Shutterstock.com/RHJPhtotos
However, silicon’s other characteristics are somewhere in the middle between those of true metals, like iron, and true non-metals, like phosphorus. In spite of its metallic appearance, silicon is quite brittle, has poor room-temperature electrical conductivity, and behaves more like a non-metal in chemical reactions.
How Xometry Can Help
This article discussed 7 key properties of silicone, presented the chemical and physical characteristics of the material, and showed the different common forms or types that are used in industry.
Xometry provides a wide range of manufacturing capabilities and value-added services for all of your prototyping and production needs. Visit our website to learn more or to request a free, no-obligation quote.
Disclaimer
The content appearing on this webpage is for informational purposes only. Xometry makes no representation or warranty of any kind, be it expressed or implied, as to the accuracy, completeness, or validity of the information. Any performance parameters, geometric tolerances, specific design features, quality and types of materials, or processes should not be inferred to represent what will be delivered by third-party suppliers or manufacturers through Xometry’s network. Buyers seeking quotes for parts are responsible for defining the specific requirements for those parts. Please refer to our terms and conditions for more information.
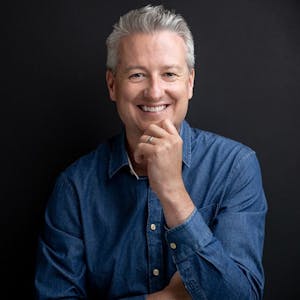