Silicone and EPDM (Ethylene Propylene Diene Monomer) are two types of rubber that are common in the industrial sector. While silicone has a more generalized usage, the purpose of EPDM is specific. Both Silicone and EPDM have properties that make them unique and which, in turn, determine their areas of application. Silicone is manufactured from inorganic compounds consisting of silicon, carbon, hydrogen, and oxygen. It is valuable in: automotive parts, food/beverage accessories, aerosols, construction items, electronics, and more.
On the other hand, EPDM is manufactured by the polymerization of ethylene and propylene and is applied mainly in the automotive and construction industries. This article explains in detail the properties of both and compares silicone vs EPDM in terms of applications, properties, and cost.
What is Silicone?
Silicone, also known as polysiloxane, is an inorganic polymer with a characteristic chain consisting of oxygen and silicon as its backbone elements and side chains made up of hydrogen and carbon. When compared to organic polymers with carbon-based backbones, silicone is more stable. It can withstand temperatures of up to 230°C thanks to the silicon-oxygen bonds in its backbone structure. The hydrocarbons in the side chains make it insoluble in water and sometimes even hydrophobic; it resists and even repels water.
In addition to the water- and heat-resisting properties of silicone, it is also a good insulator and can be considered chemically inert, gas permeable, and resistant to ultraviolet light, oxygen, and ozone. Generally, products made with silicone are not resistant to steam, acid, alkali, aromatic hydrocarbons, or trichloroethylene.
Silicone is manufactured by first extracting silicon from silica. The silicon is passed through hydrocarbons and then combined with other chemicals to give rise to silicone rubber. Silicone has a wide range of applications, seeing use in: adhesives, sealants, cooking utensils, lubricants, thermal and electrical insulations, etc. Learn more from our guide on What is Silicone Material.
Figure 1 is an example of a silicone adhesive:
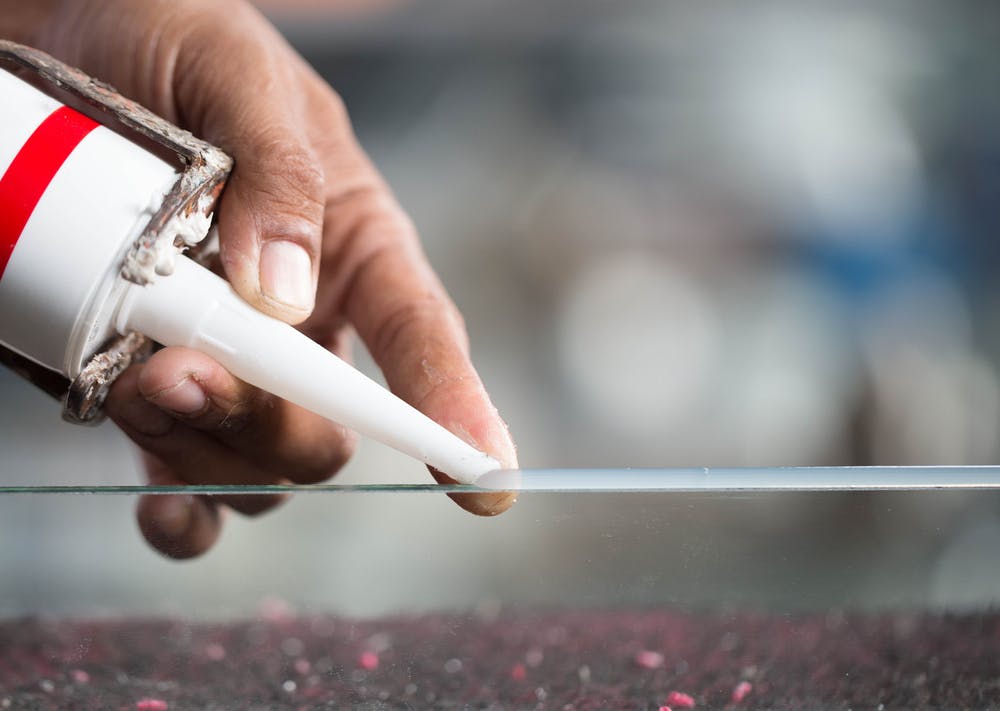
An example of applying silicone adhesive.
Image Credit: Shutterstock.com/noprati somchit
What is EPDM?
EPDM stands for ethylene propylene diene monomer. Just as the name implies, EPDM is a synthetic rubber that consists of diene monomers that serve as cross-linking hubs for vulcanization. EPDM has a single bond and a saturated backbone structure that makes it resistant to abrasion, ozone, ultraviolet rays, harsh weather conditions, and steam up to 130°C.
In addition to this, EPDM resists many polarized fluids like water, acids, bases, and esters. Generally, EPDM is known as the most water-resistant rubber on the market. Also, the electrical conductivity of EPDM is low and it can adhere easily to metals, making it good as an electrical insulator. The same properties make it an effective thermal insulator and noise dampener suitable for use in the automotive sector.
The lifespan of EPDM depends on how it is managed. If EPDM is consistently exposed to extremely high temperatures, it can degrade quickly. However, if EPDM is properly managed, it can last for a long time. For example, roofing sheets made of EPDM can survive as long as 50 years. EPDM can be used to produce: seals, garden hoses, belts, roofing membranes, electrical insulators, gaskets, and hydraulic brake components.
EPDM is manufactured via the process of polymerization. The monomers are combined and mixed continuously and then transferred to a stirred-jacketed reactor with a solution that contains the catalyst. When the polymer is formed, it gets purified by mixing it with water and toluene. This step extracts the catalyst. The monomers and the solvent are then removed from the polymer slurry and moved to the polymerization reactor to be recycled.
The resulting crumbs of wet rubber polymer then undergo a finishing stage, going into a drum that contains an anti-agglomerate agent to prevent agglomeration. The wet crumbs are then transferred to a screw extruder that separates the water from the polymer. The dried crumbs are allowed to cool before being packaged.
Silicone vs EPDM: Application and Uses
Silicone and EPDM have a wide variety of uses. Both rubbers are good options for some purposes but they can’t fill all roles. Here are examples where either silicone or EPDM are equally viable.
- Automotive Industry: Both silicone and EPDM are commonly used in the automotive industry because they are stable and can handle high heat. Silicone and EPDM are also resistant to intense weather conditions, ultraviolet rays, and ozone — all potential hazards in the automotive industry.
- Building and Construction Industry: EPDM and silicone are both utilized as: door and window seals, gaskets, O-rings, and hoses due to their elastic properties, flexibility, and durability.
- Electronics: Both silicone and EPDM are good insulators. Examples of applications include: gaskets and electrical insulators for power delivery cables.
Here are some exclusive areas where silicone is used:
- Aerospace: Silicone is a very important rubber in the aerospace industry. Its high tensile strength and temperature resistance have made it an excellent choice for many critical components. The application of silicone in aerospace includes: protective coatings for circuit terminals, sealants, encapsulants, components of engines, thermal protection, sensors, adhesives, and fuel tank coating.
- Food/Beverage: Silicone is widely used in the food/beverage industry because of its stability at high temperatures and ability to withstand damage caused by most chemicals. The production of food requires strict safety measures to avoid food contamination. Silicone is an ideal material for storing and manipulating food and beverage products.
Some specific areas where EPDM can be applied are:
- HVAC: EPDM is applied in the heating, ventilation, and air conditioning (HVAC) industry because it has a low electrical conductivity, reduces vibration, and allows for thermal expansion. It is found in: grommets, drain tubes, and gaskets.
- Consumer Appliances: EPDM helps decrease noise and vibration in consumer appliances that produce a large amount of noise.
Silicone vs. EPDM: Physical Properties
Table 1 highlights the physical properties of silicone vs. EPDM:
Physical Properties | Silicone | EPDM |
---|---|---|
Physical Properties Chemical resistance | Silicone Poor resistance to acid and alkali | EPDM High resistance to acid and alkali |
Physical Properties Flexibility | Silicone More flexible | EPDM Less flexible |
Physical Properties Melting Point | Silicone 1414 °C (2577.2 °F) | EPDM 130°C (266°F) |
Physical Properties Abrasion Resistance | Silicone Low resistance to abrasion | EPDM High resistance to abrasion |
Physical Properties Heat Resistance | Silicone High resistance to heat | EPDM Lower resistance to heat compared to silicone |
Physical Properties Weather Resistance | Silicone High weather resistance | EPDM High weather resistance |
Physical Properties Tear Resistance | Silicone Lower resistance to tearing compared to EPDM | EPDM Good tear resistance |
Physical Properties Tensile strength and Elongation | Silicone Low tensile strength and high elongation | EPDM High tensile strength and low elongation |
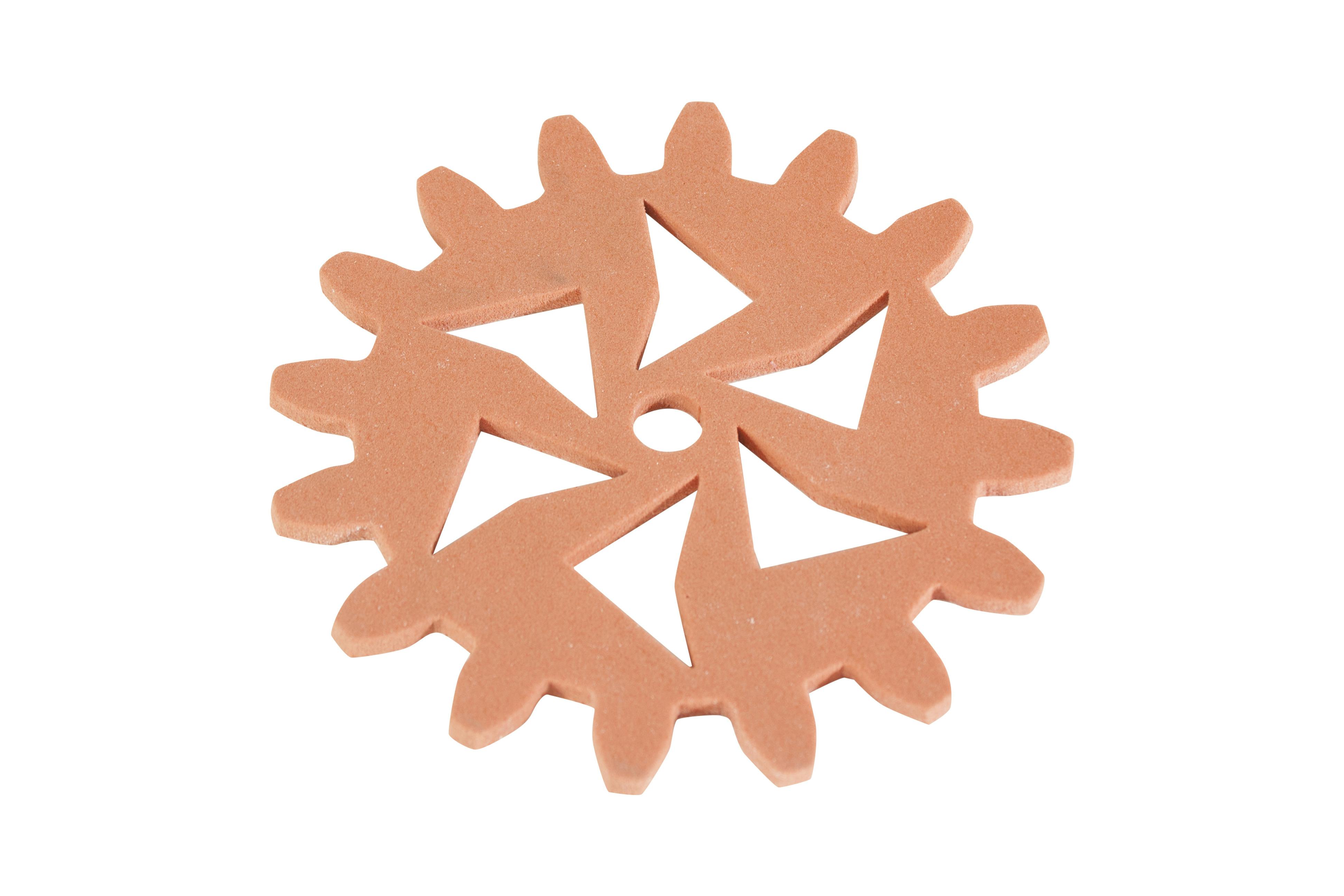
Silicone vs EPDM: Recycling and Sustainability
Although silicone can be recycled, it requires a specialized type of recycling plant. Conventional methods are ineffective. By comparison, EPDM is much easier to recycle. The reuse of EPDM materials reduces waste and the need to manufacture new raw materials. Also, EPDM can be recycled by degrading the material into smaller compounds for use in rubber mats, running tracks, and so on.
Silicone vs. EPDM: Cost
Silicone costs more than EPDM. Therefore, EPDM might be a better choice when looking for a budget-friendly synthetic rubber. Silicone costs roughly $6.25 per kilogram while EPDM goes for $2 to $4 per kilogram.
Alternative Materials to Silicone and EPDM
Substitute materials for silicone and EPDM are:
- Neoprene: Neoprene is durable, flexible, and highly resistant to oil. However, it can cause environmental pollution and should be disposed of with care.
- Vinyl: Vinyl is also known as polyvinyl chloride and is a combination of ethylene and chlorine. Vinyl costs less than silicone or EPDM and is less toxic to the environment.
- Thermoplastic Elastomers: Thermoplastic elastomers (TPEs) are primarily silicone alternatives but may fit some EPDM roles as well. They are cheap, lightweight, and flexible.
Summary
This article presented silicone and EPDM, explained what they are, and discussed the properties and applications of each. To learn more about silicone and EPDM, contact a Xometry representative.
Xometry provides a wide range of manufacturing capabilities and other value-added services for all of your prototyping and production needs. Visit our website to learn more or to request a free, no-obligation quote.
Disclaimer
The content appearing on this webpage is for informational purposes only. Xometry makes no representation or warranty of any kind, be it expressed or implied, as to the accuracy, completeness, or validity of the information. Any performance parameters, geometric tolerances, specific design features, quality and types of materials, or processes should not be inferred to represent what will be delivered by third-party suppliers or manufacturers through Xometry’s network. Buyers seeking quotes for parts are responsible for defining the specific requirements for those parts. Please refer to our terms and conditions for more information.
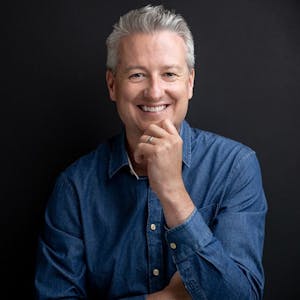