Silicone rubbers are created by the cross-linking of siloxane (silicone-oxygen short chains). Being essentially mineral in nature makes them quite different from the largely organically sourced natural and synthetic rubbers. They are extremely resistant to chemical reactions and high temperatures (in some cases handling more than 300°C). Silicone rubbers can also be moderately strong, though oftentimes they tear easily. Silicone is available in hydrolysis-catalyzed or mutually reactive two-part chemistries. They are resilient and highly elastic materials, offering a wide range of hardnesses from Shore A 30 near-gels to Shore A 90+ firm rubbers.
Neoprene is a highly resilient and stable synthetic rubber first developed in response to rubber shortages during the First World War. It is manufactured in sheets, as partially vulcanized bulk material for molding, and in the form of closed-cell and open-cell foams. Another common form is latex. Neoprene latex comes from colloidal suspensions of partially vulcanized 𝛂-chloroprene that finds use in coatings (paints, dips, etc.). This form is transformed into fully vulcanized µ-chloroprene by heating.
This article will differentiate silicone vs neoprene in terms of applications, properties, recyclability, and costs.
What is Silicone?
Silicone rubbers are synthetic elastomers that are based on siloxanes. Siloxanes are organosilicon compounds (“–Si–O–Si–O–” backbones) with side “R” chains attached to the silicon atoms. The chemical formula is R2SiO, where R is either a hydrogen atom or an organic radical functional group. Polymerized siloxanes are called silicones or silicone rubbers. The most common form of silicone rubber is polydimethylsiloxane (PDMS). Manufacturers can synthesize a wide variety of siloxanes and polysiloxanes, making silicone rubbers an extensive family with a wide spectrum of property variations.
One differentiator among silicone rubbers is the method by which the cross-linking occurs:
- A platinum-catalyzed cure (or the addition-catalyzed system) catalyzes the reaction between a hydride-siloxane and a vinyl-functional siloxane with the help of a platinum complex trigger. This cross-links the two polymers using an ethyl group attached between them.
- The condensation cure systems can have single- or dual-component chemistries. In the single-component type, hydrolysis leaves a hydroxyl or silanol group which condenses with a hydrolyzable complex built into the R-component polymer, curing the elastomer. Two-component systems use a range of organic catalysts to create the cross-links, releasing some byproducts as they do so. Many such silicones release acetic acid as they cure. Others release an alkaline residue and some are neutral. Learn more in our guide on Silicone Rubber.
What is Neoprene?
Neoprene was originally a DuPont™ product name, but today it is used generically. These are synthetic rubbers manufactured through the polymerization of chloroprene. They are chemically known as polychloroprene or, alternatively, as 𝛂- and µ-chloroprene to denote partial and complete vulcanization status. The IUPAC (International Union of Pure and Applied Chemistry) name is 2-chlorobuta-1,3-diene. Figure 1 is an example of neoprene fabric:
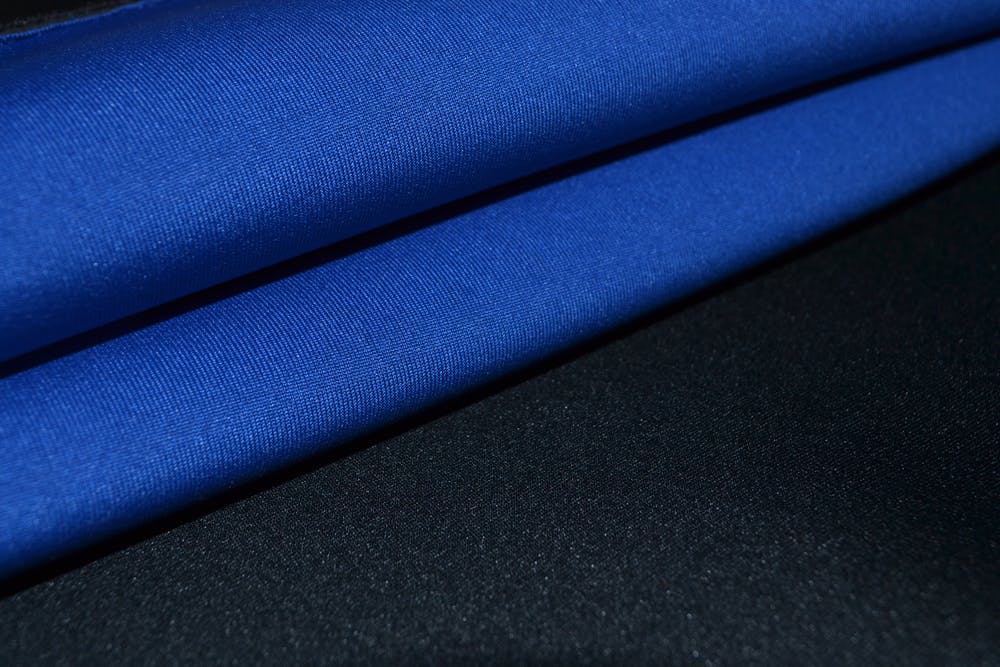
Neoprene fabric in black and blue.
Image Credit: Shutterstock.com/neux creative
Chloroprene was originally manufactured through an expensive process, using acetylene as the starting point. A lower-cost process was developed that used 1,3-butadiene (or isoprene) as the raw material; it was then modified through a chlorination process.
Neoprene has impressive chemical and thermal stability and is a strong general-purpose rubber. Users typically value its high tensile strength, oil and flame resistance, and oxygen and ozone insensitivity. It is easily foamed in either open- or closed-cell configurations using nitrogen gas. It is also sold in the form of resilient sheets or blocks, as partially vulcanized 𝛂-chloroprene for compounding and molding, and as colloidal suspensions (latex) for coating purposes.
Silicone vs. Neoprene: Applications and Uses
Silicones are widely used in gel forms and as a thickening and binding agent. Their roles as elastomers are less common but very critical in some fields. Some examples are:
- Construction/wet area sealants — generally one part silicone and an acetic acid curing agent, though various options are available.
- Seals on food-grade containers and equipment such as the combined nipple/seal section of baby bottles.
- Glass retainer materials and door/window seals.
- Phone and tablet shock boots and highly decorated skins.
- Medical/cosmetic breast implants and specialty wound dressings.
- Skin-contact comfort pads for consumer products/wearables (e.g. earbuds).
- Shock mount components that demand extreme softness.
- Screen/stage makeup and prosthetics.
- Manufacturing molds for vacuum casting of urethanes
Neoprene is a widely used material found in a variety of markets. Examples are:
- Gaskets, O-rings, seals, and hoses in automotive and other sectors.
- Wetsuits (open-cell foam) and drysuits (closed-cell foam).
- Cable insulation.
- Machine and engine drive belts, timing belts, and conveyor belts (often compounded with a fiber layer).
- Springs, shock absorbers, and flexible couplings for machines and architecture (earthquake protection, bridge expansion joints).
- Textiles, machine filters, and breathing filters
- Adhesives such as 𝛂-chloroprene colloids (latex) whose vulcanization to µ-chloroprene creates strong bonds.
Silicone vs. Neoprene: Physical Properties
Table 1 shows a comparison of silicone vs neoprene’s physical properties:
Property | Silicone value (metric) | Neoprene value (metric) |
---|---|---|
Property Density | Silicone value (metric) 1.0-1.5 g/cm3 | Neoprene value (metric) 1.23-1.25g/cm3 |
Property Hardness, Shore A | Silicone value (metric) 1-95 | Neoprene value (metric) 95-95 |
Property Tensile strength, ultimate | Silicone value (metric) 0.138-165 MPa | Neoprene value (metric) 3.45-20.7 MPa |
Property Tensile strength, yield | Silicone value (metric) 7.6-14 MPa | Neoprene value (metric) Typically 9 MPa |
Property Elongation at break | Silicone value (metric) 0-900 % | Neoprene value (metric) 100-800 % |
Property Modulus of elasticity | Silicone value (metric) 5x10-6-1.99 GPa | Neoprene value (metric) Typically 1.36 GPa |
Property Tear resistance | Silicone value (metric) Poor to moderate | Neoprene value (metric) Moderate to good |
Property Dielectric constant | Silicone value (metric) 2.0-35 | Neoprene value (metric) 2.0-2.6 |
Property Coefficient of thermal expansion | Silicone value (metric) 11.0-335 µm/m°C | Neoprene value (metric) 14.0-25 µm/m°C |
Property Max service temperature | Silicone value (metric) 93-316°C | Neoprene value (metric) 250°C |
Silicone vs. Neoprene: Recyclability and Sustainability
Neither neoprene nor silicone rubber can be recycled. Both are formed into elastomers by irreversible and complex chemical changes that fundamentally alter the material structure and render it chemically and thermally stable.
Neoprenes are manufactured from hydrocarbon source materials and no meaningful organic-source alternatives have been developed. Silicones have a notionally mineral structure and are made from purified silicon extracted from geological sources. Silicone rubber precursor materials are produced with the help of complex organic chemicals, metallic and organic catalysts, toxic processes, and complex chemistry. Many aspects of this are energy intensive and create pollution.
Since neither material can be broken down by non-destructive means, the only practical method of disposal (other than as environmental waste) is incineration. This can produce a range of toxic fumes unless performed in a high-temperature furnace at nearly 5000°C with an oxygen-rich atmosphere for complete combustion.
Silicone vs. Neoprene: Cost
Silicone rubber is a high-cost material and is generally reserved for high-value soft products, baby products, or medical applications. Typical (bulk) prices range from $5,000 to $10,000 per metric ton. High-grade silicones for casting or cosmetic purposes can be purchased for $25 per kilogram or more.
Neoprenes, on the other hand, are sold in three forms:
- Cast/rolled and vulcanized sheets — typical price: $1,000 for a 50’ x 36’ x ½’ sheet.
- Closed-cell foam sheets — typical price: $403 for 39’ x 78’ x 1’.
- 𝛂-chloroprene as a raw material for blending and molding — typical price range: $2,500 to $9,000 per metric ton, depending on grade.
Alternative Materials to Silicone and Neoprene
Silicone rubbers have some outstanding characteristics such as chemical and temperature resilience. Many applications, however, don’t approach these limits and merely demand a highly attractive matte finish and vibrant colors. Likewise, neoprenes are very strong, and fairly temperature and chemical-resilient, so in many non-food-related contexts, silicone rubber and neoprenes are somewhat interchangeable. Differences in certain design considerations such as minimum thickness will have to be accounted for, though.
Where high-temperature performance and chemical stability are not required, TPE (thermoplastic elastomer) offers cost-effective options. In resilient rubber applications, EPDM, butadiene, and acrylonitrile rubbers are all good substitutes. While not fully interchangeable, these materials exhibit roughly parallel properties. For high-temperature applications, however, expensive PTFE elastomers such as Viton™ offer very high resilience in all properties. For some applications, such as medical implants, no practical alternative to silicone exists.
Summary
This article presented silicone and neoprene, explained what they are, and discussed the applications and properties of each. To learn more about silicone and neoprene, contact a Xometry representative.
Xometry provides a wide range of manufacturing capabilities and other value-added services for all of your prototyping and production needs. Visit our website to learn more or to request a free, no-obligation quote.
Copyright and Trademark Notices
- DuPont™ is a trademark of Dupont de Nemours, Inc.
- Viton™ is a trademark of The Chemours Company FC, LLC.
Disclaimer
The content appearing on this webpage is for informational purposes only. Xometry makes no representation or warranty of any kind, be it expressed or implied, as to the accuracy, completeness, or validity of the information. Any performance parameters, geometric tolerances, specific design features, quality and types of materials, or processes should not be inferred to represent what will be delivered by third-party suppliers or manufacturers through Xometry’s network. Buyers seeking quotes for parts are responsible for defining the specific requirements for those parts. Please refer to our terms and conditions for more information.
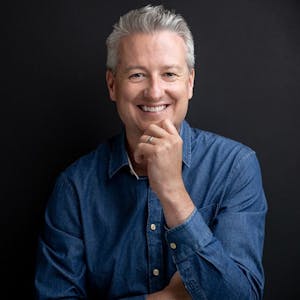