Steel is one of the most extensively used metallic materials worldwide. It is an alloy primarily composed of iron and a controlled amount of carbon, typically less than 2% by weight. Additional alloying elements—such as manganese, chromium, nickel, and molybdenum—can be incorporated to tailor the steel’s mechanical properties, corrosion resistance, and thermal performance. Steel exists in a broad range of grades and classifications, which are typically based on composition (e.g., carbon content and alloying elements), microstructure, and manufacturing processes. Its versatility makes it suitable for applications ranging from structural frameworks in bridges and buildings to consumer goods, such as washing machines and refrigerators.
This article provides a comprehensive overview of steel, including its various types and grades, classification methods, and the major systems used to standardize and grade steel materials.
What Are the Different Types of Steel?
Steel comes in different types, distinguished by their composition and properties. The different steel types are mentioned and discussed below:
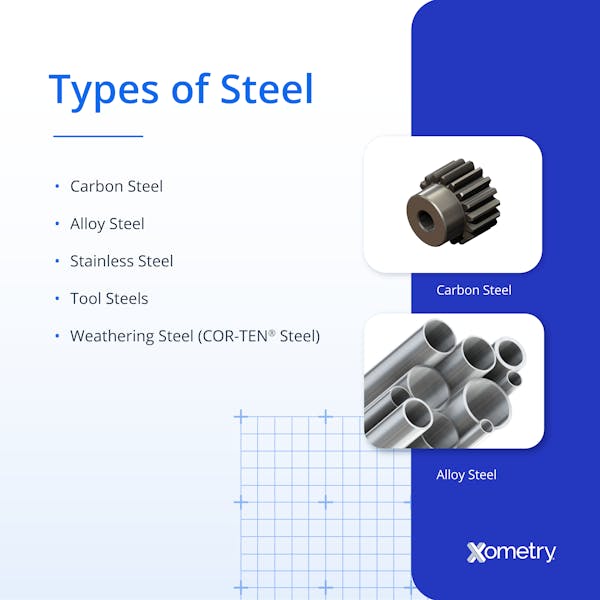
1. Carbon Steel
Carbon steel is the most fundamental and widely produced category of steel, accounting for approximately 90% of global steel production. It is primarily composed of iron and carbon, with a limited number of alloying elements. According to the American Iron and Steel Institute (AISI), carbon steel typically contains no more than 2% carbon by weight and does not include significant amounts of other alloying elements. It may contain residual quantities of elements such as manganese (up to 1.65%), copper (up to 0.6%), silicon (up to 0.6%), sulfur (up to 0.05%), and phosphorus (up to 0.04%). Still, no elements are deliberately added beyond these thresholds.
Carbon steel is generally divided into the following subcategories based on carbon content:
- Low-Carbon Steel (Mild Steel): This type of steel contains up to 0.3% carbon, making it highly ductile, malleable, and easily weldable. Its softness and workability make it ideal for construction materials, automotive body panels, and wire products.
- Medium-Carbon Steel: Contains approximately 0.3% to 0.6% carbon, offering a balance between strength and ductility. This type is often used for gears, railway tracks, and structural components where improved mechanical performance is required.
- High-Carbon Steel: Contains more than 0.6% carbon and up to about 1.0%, offering increased hardness and wear resistance. Typical applications include cutting tools, springs, and high-strength wires.
- Ultra-High Carbon Steel: Contains over 1.0% carbon, up to approximately 2.1%, and is used in specialized applications such as knives, axles, and hard tooling. This steel is very hard but less ductile, requiring careful processing and handling to prevent damage.
To learn more, see our full guide on the Definition of Carbon Steel.
2. Alloy Steel
Alloy steel contains additional elements, besides iron and carbon, that are introduced to enhance strength, hardness, corrosion resistance, and other mechanical properties. Common alloying elements include manganese, silicon, nickel, chromium, molybdenum, and vanadium. The total percentage of alloying elements can range from a few percent to over 50%, depending on the steel's intended application.
Alloy steels are generally grouped into the following categories:
- Low-Alloy Steel: Contains less than 5% total alloying elements. Typical limits include <1.8% nickel, <6% chromium, and <0.65% molybdenum. These steels offer a tensile strength range of approximately 450–1000 N/mm² and are commonly used in structural components, pipelines, and pressure vessels.
- Medium-Alloy Steel: Contains approximately 5–12% alloying elements. This group includes nickel steels used for axles and shafts, nickel-molybdenum steels suitable for cams and bearing races, and nickel-chromium-molybdenum steels, which are known for their high fatigue resistance and are used in automotive and aerospace components.
- High-Alloy Steel: Contains more than 12% total alloying elements. This includes stainless steels with 13–18% chromium for corrosion resistance, Hadfield steels with more than 11% manganese for wear resistance, and other alloys that offer heat resistance and high strength for use in power generation, chemical processing, and high-temperature environments.
To learn more, see our full guide on the Definition of Alloy Steel.
3. Stainless Steel
Stainless steel is well-known for its corrosion resistance, strength, and clean appearance. Its defining feature is a minimum chromium content of 10.5%, which enables the formation of a passive chromium oxide layer on the surface. This layer is self-healing and protects the steel from oxidation, staining, and rust in many environments.
Stainless steel is commonly categorized into the following types based on microstructure and alloy composition:
- Austenitic: Non-magnetic, highly formable, and corrosion-resistant. Common in kitchenware, chemical equipment, and medical devices.
- Ferritic: Magnetic with good corrosion resistance. Often used in automotive parts and home appliances.
- Martensitic: Hard and strong. Suitable for cutlery, tools, and surgical instruments.
- Duplex: Combines strength and corrosion resistance. Used in marine and chemical processing applications.
To learn more, see our full guide on Stainless Steel Metals.
4. Tool Steels
Tool steels are engineered for use in cutting, shaping, and forming tools, where wear resistance, hardness, and heat resistance are essential. Typical applications include drill bits, cutting tools, dies, molds, punches, chisels, blades, and knives. They are alloyed with elements such as tungsten, molybdenum, chromium, cobalt, and vanadium, which enhance their ability to resist deformation, abrasion, and thermal stress.
Tool steels are categorized based on their hardening method, heat resistance, and impact strength. The main types include water-hardening (W-series), air-hardening (A-series), oil-hardening (O-series), high-speed (M and T-series), hot-working (H-series), and shock-resisting (S-series) tool steels. Each type is optimized for specific tooling applications, such as cutting, shaping, forming, or impact-intensive operations.
To learn more, see our full guide on the Definition of Tool Steel.
5. Weathering Steel (COR-TEN® Steel)
Weathering steel, known commercially as COR-TEN® steel, is engineered to resist corrosion in outdoor applications, forming a protective rust-like appearance over time without corroding. Alloyed with small amounts of chromium, nickel, and copper, it offers increased resistance to atmospheric conditions. This steel is used in bridges, sculptures, and other outdoor installations.
What Are the Different Types of Steel Grades?
Steel grades are classifications used to define the specific chemical composition, mechanical properties, and processing methods of steel. These grades are standardized by recognized organizations such as the American Society for Testing and Materials (ASTM) and the Society of Automotive Engineers (SAE). Each grading system provides a framework for selecting the appropriate steel for a given application, whether based on strength, corrosion resistance, formability, or thermal performance.
The following sections outline key steel grading systems and explain how steel grades are designated and applied across industries.
1. ASTM Grading System
The ASTM grading system is a widely recognized classification framework that designates steel and other materials based on their chemical composition, mechanical properties, and intended applications. It applies to various categories of steel, including carbon steel, alloy steel, stainless steel, and tool steel.
ASTM standards typically use a letter prefix followed by a numerical code to identify material types. For steel-related standards, the prefix “A” is commonly used (e.g., ASTM A36 for structural carbon steel). The numeric portion is sequentially assigned and used solely for identification—it does not directly indicate a material’s properties, such as strength, hardness, or composition.
Each ASTM grade standard defines specific testing requirements, permissible chemical ranges, and performance criteria to ensure consistency across various applications, including structural engineering, pressure vessels, pipelines, and tooling.
2. SAE Grading System
The SAE grading system, often used in conjunction with the American Iron and Steel Institute (AISI) designation, classifies steels based primarily on their chemical composition. It is widely used in automotive and mechanical engineering applications.
This system uses a four-digit numerical code:
- The first two digits identify the steel type and major alloying elements.
- The last two digits indicate the approximate carbon content, expressed in hundredths of a percent.
For example, SAE 1040 designates a plain carbon steel (10-series) with approximately 0.40% carbon. In contrast, a grade like 4340 denotes alloy steel (43-series) with nickel, chromium, and molybdenum and about 0.40% carbon.
While the SAE system originated in the U.S., it remains a widely referenced classification in global materials engineering, particularly for specifying steel used in machinery, structural components, and automotive parts.
What Is Steel?
In its simplest form, steel can be defined as an alloy primarily composed of iron and carbon, typically ranging from 0.2% to 2.1% by weight. However, all steels (carbon steel, alloy steel, tool steel, stainless steel, and weathering steel) can also contain small amounts of other elements in their composition. The added elements impart different properties and characteristics to the steel, resulting in various commercial steel types and grades. Some of the most common elements added to steel to alter its properties include manganese, chromium, molybdenum, and nickel.
How Does Steel Differ From Other Metals?
Metal refers to any pure metallic element or alloy, including materials like aluminum, copper, titanium, and zinc. Steel is distinct in that it is an alloy based explicitly on iron and carbon. This unique combination gives steel its characteristic balance of strength, ductility, and versatility. Its mechanical and chemical properties differ significantly from those of pure metals and other alloys due to its carbon-based microstructure.
What Are the Properties of Steel?
Steel exhibits a wide range of physical and mechanical properties, which can be tailored through composition and heat treatment. Below are some of the key characteristics associated with different types of steel:
- Strength: Steel is known for its high tensile and yield strength, making it suitable for construction, transportation, and heavy machinery. The strength can be adjusted through the addition of alloying elements (e.g., manganese, vanadium) and heat treatment processes (e.g., quenching and tempering).
- Toughness: Certain steels can absorb impact energy without fracturing. However, not all steel grades are equally tough. Ferritic steels, for instance, exhibit a ductile-to-brittle transition temperature; below this critical point, they become more susceptible to brittle fracture under stress.
- Hardness: Hardness refers to steel’s resistance to indentation, abrasion, and wear. It varies significantly based on alloying and heat treatment. Tool steels and hardened martensitic steels are among the hardest.
- Fatigue Strength: Steel performs well under cyclic loading, provided the stress remains below a material-specific fatigue limit. Under such conditions, certain steels can exhibit an infinite fatigue life, making them useful in applications such as bridges, crankshafts, and springs.
- Corrosion Resistance: While plain carbon steel is susceptible to rust, stainless steels with chromium content ≥10.5% offer significantly improved corrosion resistance. Grades like 304 and 316 are commonly used in marine and chemical environments.
- Heat Resistance: Specialized steels, such as stainless steel grades 309, 310, and 330, as well as Cr-Mo (chromium-molybdenum) steels, retain their strength at elevated temperatures. These are used in boilers, turbines, and exhaust systems.
- Weldability: Most steels are readily weldable, though high-carbon and alloy steels may require specific procedures or preheating to prevent cracking. Austenitic stainless steels typically exhibit excellent weldability.
- Electrical and Thermal Conductivity: Steel conducts heat and electricity at lower rates than pure metals like copper or aluminum. Conductivity varies with composition and microstructure.
- Magnetic Properties: Ferritic steels are ferromagnetic, while martensitic steels show variable magnetic behavior. Austenitic stainless steels, due to their face-centered cubic structure, are non-magnetic or only weakly magnetic.
- Machinability: Most steels are machinable, though free-machining grades (with added sulfur or lead) enhance this property. Machinability is influenced by hardness, microstructure, and alloy content.
- Recyclability: Steel is highly recyclable, with over 60% of global steel production derived from recycled material. It retains its properties indefinitely through multiple recycling cycles.
How Are Steel Grades Classified and Categorized?
Steel grades are classified and categorized based on their chemical composition and specific properties. The primary methods include:
- Carbon Content: Steel is divided into categories based on its carbon content: low (up to 0.3%), medium (between 0.3 and 0.6%), high (0.6-1.0%), and very high (1.0-2.1%) carbon content).
- Alloying Elements: Beyond carbon, the addition of elements such as manganese, silicon, nickel, chromium, and molybdenum distinguishes alloy steels from carbon steels and contributes to specific properties, including strength, ductility, and corrosion resistance.
- AISI/SAE Numbering System: This naming system uses a four-digit code to designate steels, in which the first two digits indicate the type of steel and its primary alloying components, and the last two digits represent the carbon content in hundredths of a percent.
- ASTM Specifications: These cover a wide range of steel types and forms, focusing on test requirements, manufacturing processes, and properties specific to applications.
- Additional Classifications: Other ways to categorize steels include groupings such as high-strength low-alloy (HSLA) steels, stainless steels, and tool steels, based on their unique characteristics and intended uses.
How Is Steel Typically Manufactured?
Steel is produced using one of two primary methods: the blast furnace–basic oxygen furnace (BF–BOF) process or the electric arc furnace (EAF) process. Each method differs in its raw materials, energy sources, and emissions profile.
In the blast furnace process, iron ore, coke (a carbon-rich material derived from coal), and fluxes such as limestone or lime are charged into a blast furnace. Air is blown in at high temperatures to enable chemical reactions that reduce the iron ore into molten pig iron. This pig iron, high in carbon and impurities, is then transferred to a basic oxygen furnace (BOF), where pure oxygen is injected to oxidize and remove excess carbon and impurities, resulting in molten steel.
The electric arc furnace method, typically used in mini-mills and for producing recycled steel, begins with scrap steel or direct-reduced iron (DRI). DRI is made by reducing iron ore using natural gas or hydrogen without melting it. This metallic iron is then melted in an electric arc furnace, where high-voltage electric arcs from graphite electrodes generate the heat required for melting. Alloying elements can be added during this stage to achieve the desired steel composition.
After smelting, the molten steel is cast—usually through a continuous casting process—into semi-finished forms such as slabs, billets, or blooms. These are further processed in hot strip mills or rolling mills to produce final products. Depending on the application, the steel may undergo hot rolling, cold rolling, annealing, tempering, or other heat treatments to adjust its microstructure and properties.
What Are Some Common Applications of Steel in Daily Life?
Steel plays a crucial role in modern infrastructure and everyday products due to its strength, durability, and versatility. Its applications span multiple industries and household uses, including:
- Construction: Steel is used in the structural framework of buildings, bridges, tunnels, and high-rises. It also appears in roofing materials, reinforcing bars (rebar), and steel beams due to its load-bearing capacity and resilience.
- Transportation: The frames, bodies, and engines of cars, trucks, trains, ships, and aircraft commonly incorporate steel. It offers the strength needed for crash safety and structural integrity.
- Appliances and Tools: Many household and industrial products, such as refrigerators, washing machines, stoves, cutlery, and hand tools, are made from steel, particularly stainless and carbon steels, due to their corrosion resistance and toughness.
- Medical Equipment: Stainless and tool steels are utilized in the production of surgical instruments, hospital beds, diagnostic equipment (e.g., MRI machines), and support structures due to their hygiene, strength, and non-reactivity.
- Storage Solutions: Steel is widely used in cabinets, shelving units, safes, and warehouse systems due to its strength and durability.
- Hardware Components: Screws, bolts, hinges, and fasteners are frequently made from various grades of steel to ensure mechanical reliability and longevity.
How Does Xometry Select Steel Grades for Manufacturing?
Xometry selects steel grades for manufacturing based on the specific requirements of the project, including mechanical properties, application environment, manufacturability, and cost. Factors considered include:
- Strength and Durability Needs: Depending on the structural demands of the part.
- Corrosion Resistance: Necessary for parts exposed to harsh environments.
- Machinability and Weldability: Based on the manufacturing processes to be used.
- Client Specifications: Adhering to client-provided requirements or industry standards.
- Cost-Effectiveness: Balancing Material Properties with Budget Constraints.
This approach ensures that the selected steel grade optimally balances performance, cost, and manufacturability for the intended application.
What Is the Difference Between Iron and Steel?
The primary difference between iron and steel is that iron is a chemical element, while steel is an alloy mainly composed of iron and carbon. Iron, in its pure form, is soft and prone to rusting, whereas steel, with a small amount of carbon added, is harder, stronger, and less likely to rust. The addition of carbon and other alloying elements to iron during the steel-making process significantly enhances its mechanical properties, making steel more durable and versatile for a wide range of applications.
Summary
This article presented steel types and grades, explained each of them, and discussed their various applications. To learn more about steel, contact a Xometry representative.
Xometry provides a wide range of manufacturing capabilities and other value-added services for all of your prototyping and production needs. Visit our website to learn more or to request a free, no-obligation quote.
Copyright and Trademark Notice
- COR-TEN® is a trademark of the United States Steel Corporation (USS).
Disclaimer
The content appearing on this webpage is for informational purposes only. Xometry makes no representation or warranty of any kind, be it expressed or implied, as to the accuracy, completeness, or validity of the information. Any performance parameters, geometric tolerances, specific design features, quality and types of materials, or processes should not be inferred to represent what will be delivered by third-party suppliers or manufacturers through Xometry’s network. Buyers seeking quotes for parts are responsible for defining the specific requirements for those parts. Please refer to our terms and conditions for more information.
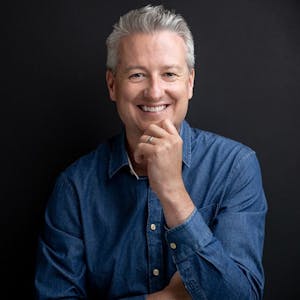