Engineers need to know how to calculate thermal conductivity because it can give them valuable insights into materials to help them make the right selection. Mainly, it lets them know if a material is insulating or conductive. In this article, we’ll go over thermal conductivity in more detail, factors that can influence it, and the exact formula for you to calculate it.
What is Thermal Conductivity?
Thermal conductivity refers to how easily heat can move through a material, down a gradient from high temperature to low temperature. If a material is an insulator, you’ll usually find the term “thermal resistivity” used instead. This thermal conductivity/resistivity is often found experimentally. The calculation is a handy way of determining whether a material is an insulator or a conductor. Copper is a highly heat-conductive material, which makes it ideal for something like a heat sink. Ceramic, though, has low thermal conductivity, so it’s perfect for thermal insulation. For heat exchangers, a good thermal conductor will be needed, but something like a furnace lining calls for an insulator.
Thermal conductivity is especially important when it comes to 3D printing. For starters, the bed of the printer needs to be kept hot in order for the first layer to stick to it. 3D printer bed plates are usually made of aluminum plate with a heating element attached to the underside. Aluminum is an excellent heat conductor, so it can evenly distribute the heat wherever it’s needed. Good thermal conductivity is also needed to transfer heat from the thermistor to the plastic in order to melt it. But, on the other hand, if there’s any thermal conductivity inside the extruder assembly, this can cause heat creep, and ultimately, the print can fail.
For heat to move from the hot area to the cold area of a material, a few things happen. First of all, what we perceive as heat when we touch something hot is actually atomic-scale vibrations that happen within the material. When a material absorbs heat energy, that energy is transformed into kinetic energy, causing the atoms to move. But, as atoms in solids don’t have much room to move, they start vibrating, and the ones directly exposed to the heat start crashing into their neighbors. This collision excites the neighbors, and they also begin to vibrate. As this happens and continues to move along from the hot to the cold part of a material, the heat begins to move further down too. It’s kind of like a ripple that spreads from a pebble hitting the surface of a pond.
As conductors, materials with high thermal conductivity can transfer heat from a heat source to a heat sink, keeping equipment cool. They can also move heat from a heat source to cooler fluid in order to heat it up and distribute the heat evenly, which can prevent warping. Materials with low thermal conductivity are good insulators, preventing heat from escaping the source or entering a temperature-sensitive area like inside a spacecraft during atmospheric reentry. However, the calculation is not entirely precise. A material’s thermal conductivity can change with temperature. That’s why some calculations may not be right for you if they were done under different conditions. In addition, thermal conductivity usually only covers heat transfer via conduction and doesn’t really address convection or radiative heat transfer.
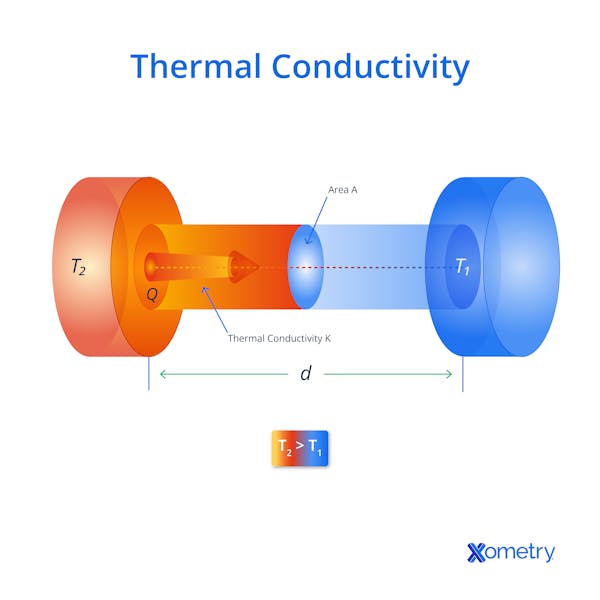
Thermal Conductivity Formula
Without further ado, let’s get straight to the formula for calculating thermal conductivity. First, you’ll need to know what all the symbols mean:
- k = Thermal conductivity
- Q = Heat flux
- A = Cross-sectional area
- ΔT = The difference in temperature of the material’s two sides
- T1 = The material’s hot side
- T2 = The material’s cold side
- d = The length of the material
We’ll use a simplified form of Fourier’s law for heat transfer, but there are a few things to keep in mind with this law. If the temperature on the hot side doesn’t change, heat transfer can be classified as a “steady state,” and heat is only transferred in one direction. Also, the thermal conductivity value of a material will change depending on the temperature. As a general rule, the higher the temperature, the higher the thermal conductivity. So here it is:
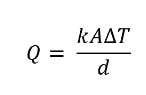
Heat transfer equation.
In this instance, the heat transfer is one-dimensional and in a steady state. We can also rearrange the equation, switching the value for thermal conductivity on the left-hand side. Here’s what the thermal conductivity formula would look like:
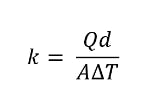
Thermal conductivity equation.
We wouldn’t recommend solely relying on this formula to determine a material’s thermal conductivity, though. The best way to do so is experimentally under controlled conditions, according to strict international standards. Most material data sheets will show thermal conductivity at specific temperatures, or even in a range of temperatures.
To illustrate the effect of a material’s thermal conductivity on the heat flux magnitude, below are three examples of thermal conductivities of common materials that have been experimentally determined. For these examples, the plate is assumed to be 1m thick with a length and breadth of 1m, T1 is equal to 250°C, and T2 is equal to 25°C.
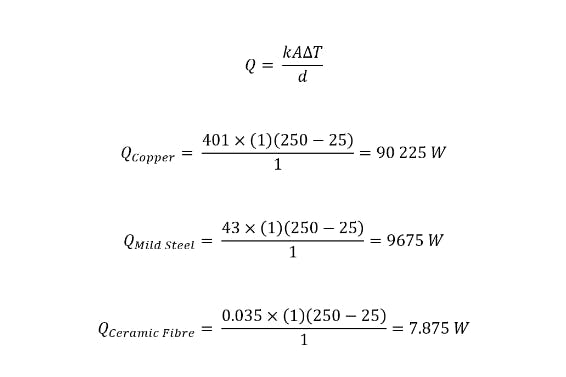
Examples of thermal conductivity calculations for common materials.
Material | Thermal Conductivity (Cal/cm·s·oC) | Thermal Conductivity (W/m·K) |
---|---|---|
Material Mild Steel | Thermal Conductivity (Cal/cm·s·oC) 0.102 | Thermal Conductivity (W/m·K) 43 |
Material Type 316 Stainless Steel | Thermal Conductivity (Cal/cm·s·oC) 0.039 | Thermal Conductivity (W/m·K) 16.3 |
Material Copper | Thermal Conductivity (Cal/cm·s·oC) 0.958 | Thermal Conductivity (W/m·K) 401 |
Material Silver | Thermal Conductivity (Cal/cm·s·oC) 1.025 | Thermal Conductivity (W/m·K) 429 |
Material Ceramic Fiber | Thermal Conductivity (Cal/cm·s·oC) 0.00008 | Thermal Conductivity (W/m·K) 0.035 |
Material PLA (FDM 3D Printing Material) | Thermal Conductivity (Cal/cm·s·oC) 0 | Thermal Conductivity (W/m·K) 0.13 |
Material ABS (FDM 3D Printing Material) | Thermal Conductivity (Cal/cm·s·oC) 0.00059 | Thermal Conductivity (W/m·K) 0.25 |
Material SS 316 (SLM 3D Printing Material) | Thermal Conductivity (Cal/cm·s·oC) 0.0389 | Thermal Conductivity (W/m·K) 16.3 |
Material Nylon PA12 (SLS 3D Printing Material) | Thermal Conductivity (Cal/cm·s·oC) 0.00072 | Thermal Conductivity (W/m·K) 0.3 |
Thermal Conductivity Examples in Different Materials
Factors Affecting Thermal Conductivity
Your calculation with this equation won’t be the same every time, even if you have the same piece of material, and there are several reasons for this:
- Temperature: Many conductive materials, like metal, tend to decrease in thermal conductivity when they get hot. As they heat up, the atoms and phonons begin to vibrate more intensely, and this reduces the mean free path for free electrons (known as electron phonon-scattering). For nonmetals, the relationship between thermal conductivity and temperature can be more complicated, and the material’s conductivity can either increase or decrease.
- Density: Materials that are more dense tend to be more thermally conductive. That’s generally because they have a higher packing density of atoms, which helps heat to be transferred via phonons or free electrons.
- Pressure: It’s possible to increase a material’s density when it’s exposed to high pressure, and this, in turn, can make the material more thermally conductive. Another possibility, however, is that pressure could change the phase of a material—i.e. from a solid to a liquid.
- Composition: The types of atoms, molecules, or ions in a material can also affect its heat conductivity. Nonmetallic materials, i.e., polymers or ceramics, are less thermally conductive because their molecular structures are more rigid.
- Structure: The lattice structure of a material could affect the result as some are better at transferring heat than others. Materials with larger crystals are usually better at transferring heat because they have fewer grain boundaries (basically obstacles). The form of the crystal structure can also have an effect. FCC (face-centered cubic) structures like those in copper are more thermally conductive than BCC (body-centered cubic) structures like those found in iron.
- Porosity: Referring to voids or gas pockets within a material’s structure, porosity can be naturally occurring, added on purpose, or present because of bad processing. The thermal conductivity through these little pockets is much less than the base material. But, ultimately, this will decrease the overall thermal conductivity of that material.
- Impurities: Any impurities in a material can affect its thermal conductivity, and that’s due to something called electric impurity scattering. These impurities can create local anomalies in the electric potential within the crystal lattice. This can cause the free electronics to move less and ultimately reduce the material’s thermal conductivity.
Thermal Conductivity in Laser Cutting and Plastic Injection Molding
Laser cutting and plastic injection molding—both services we offer here at Xometry—are processes in which thermal conductivity plays an important role. For laser cutting, highly thermally conductive materials require more energy in order to cut through them. On the contrary, though, if materials are on the less conductive side, they’ll localize the heat near the cut edge and cause an uneven distribution of heat, which can eventually cause warping or cracking.
Similar things can happen during plastic injection molding. During this process, if the mold is not kept at the best temperature and then cooled down quickly, you can have huge cycle times and run the risk of making a bad-quality part. That’s why molds with high thermal conductivity are great: they allow for quick heating and cooling.
How Xometry Can Help
Xometry provides many manufacturers with services related to metal and thermal conductivity. We offer a wide range of manufacturing capabilities, including 3D printing, laser cutting, CNC machining, and more. If you’d like to learn more about thermal conductivity or request a free, no-obligation quote, reach out to a Xometry representative today.
Check out our Technical Datasheet Glossary to learn more about different material properties.
Disclaimer
The content appearing on this webpage is for informational purposes only. Xometry makes no representation or warranty of any kind, be it expressed or implied, as to the accuracy, completeness, or validity of the information. Any performance parameters, geometric tolerances, specific design features, quality and types of materials, or processes should not be inferred to represent what will be delivered by third-party suppliers or manufacturers through Xometry’s network. Buyers seeking quotes for parts are responsible for defining the specific requirements for those parts. Please refer to our terms and conditions for more information.
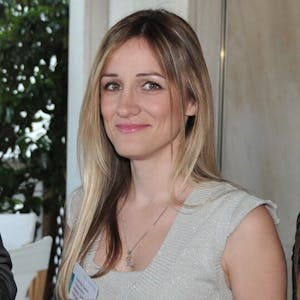