Thermal resistance is an essential parameter in engineering, physics, thermodynamics, and even manufacturing. It plays an important role in the design and optimization of thermal systems, like electronic devices, insulation materials, and building envelopes. Here’s everything you need to know, including how to calculate it in every material.
What is Thermal Resistance?
A material or system’s ability to resist the transfer of heat, more precisely, the ratio of temperature difference to heat transfer rate, is referred to as its thermal resistance. This can also be described as the relationship between the temperature difference across a material and the rate of heat that’s flowing through it. Insulation materials used in construction should have high thermal resistance values because they reduce the speed of the heat transferred through the building envelope, helping to maintain interior temperature and improve energy efficiency. In contrast, heat exchangers and sinks need to be made from a material that has low thermal resistance because the aim is for heat to travel as easily and effectively as possible.
When it comes to manufacturing processes like plastic injection molding, 3D printing, and laser cutting, thermal resistance will dictate the material’s performance. The wrong thermal properties can lead to warping, cracking, or deformation. Low thermal resistance materials require slower laser cutting to prevent damage, while high resistance materials can withstand higher speeds with minimal or no distortion. In thermal management, it helps prevent overheating, improves energy efficiency, and enhances print quality. High thermal resistance materials also reduce energy costs, help keep temperatures stable indoors, and are even used in fireproofing applications.
A material’s thermal resistance is a bit tricky to accurately calculate because there’s no one-size-fits-all formula; it depends on the material’s thickness, surface area, and thermal conductivity. But don’t worry, we’ve got an easy-to-follow guide below with everything you need to do to work it out.
Christian Tsu-Raun, a Team Lead, Manual Quoting here at Xometry says "Thermal resistance is important because we live in a thermal environment. One of the key properties of plastics is that they are plastic — that is to say workable at low temperatures, not very far above environmental temperatures. This allows them to be extruded/injected/cast with minimum additional heating, reducing cost. However, this also means that possible ambient temperatures can cause parts to warp, shift, or deform more easily. Because of this, it is important to consider the thermal conditions the parts will be subject to, and choose a material that is able to withstand them."
Affecting Factors
First, let’s have a look at a few things that could affect the thermal resistance of a material, and why.
Surface area: This influences the rate of heat transfer between the material and its surroundings, so it affects the thermal resistance. An increased surface area and lower thermal resistance can make the part more effective at transferring heat.
Porosity: Porous materials have a lower thermal conductivity than non-porous ones, even if it’s the same material, because trapped air reduces heat transfer. This is quite a major factor in insulation materials where high thermal resistance is needed.
Composition: Materials with poor thermal conductivity typically have a high thermal resistance.
Thickness: Thicker materials generally resist heat transfer better than thin ones. The precise relationship between thickness and thermal resistance ultimately depends on the material’s characteristics and the mode of heat transfer.
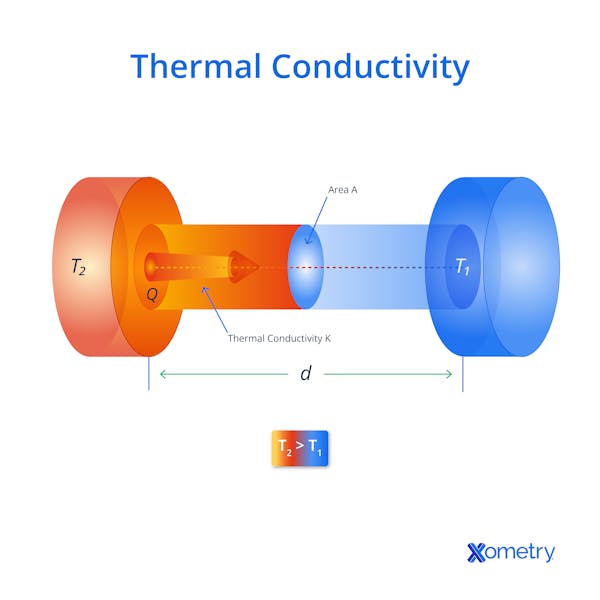
Calculating Thermal Resistance
Here’s the technical bit. To calculate the thermal resistance in a material, you’ll first need to know the keys:
R = Thermal resistance (degrees Kelvin per watt (K/W) or Celsius per watt (°C/W))
L = Thickness of the material (m) perpendicular to the heat flow
k = Thermal conductivity (W/mK) (how well the material conducts heat)
A = Cross-sectional area perpendicular to heat flow (m²)
The thermal resistance of a flat object and some popular 3D printing materials can be determined by the following equation for steady-state heat transfer, which basically translates to “thermal resistance = thickness / (area x thermal conductivity):
R = L / kA
So, as you can see, to figure out the thermal resistance of a material, you’ll need to know its thickness, cross-sectional area, and thermal conductivity. Measuring the thickness and cross-sectional area is pretty straightforward and can be done with a ruler or caliper. You’ll need to refer to the Material Safety Data Sheet to find its thermal conductivity. Once you’ve got all that info, you can go ahead and do the equation.
The thermal resistance formula for conductive heat transfer is a rearranged version of Fourier’s Law of Heat Conduction:
Q = kAΔT / L
Q = Heat transfer rate (W)
ΔT = Temperature difference across the material (K or °C)
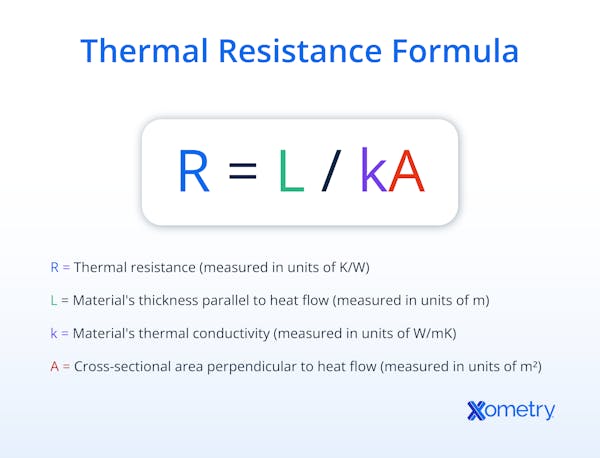
Examples
Here are some real-world example calculations to give you a better idea of how this works.
Item | Thickness | Thermal conductivity | Area | Equation | Result |
---|---|---|---|---|---|
Item Steel plate | Thickness 0.02 m | Thermal conductivity 50 W/mK | Area 0.5 m² | Equation R = 0.02 / 50 × 0.5 | Result 0.0008 K/W |
Item Steel plate | Thickness 0.02 m | Thermal conductivity 50 W/mK | Area 0.1 m² | Equation R = 0.02 / 50 × 0.1 | Result 0.004 K/W |
Item Copper plate | Thickness 0.02 m | Thermal conductivity 401 W/mK | Area 0.1 m² | Equation R = 0.02 / 401 × 0.1 | Result 0.0005 K/W |
Item Glass window | Thickness 0.003 m | Thermal conductivity 0.8 W/mK | Area 2 m² | Equation R = 0.003 / 0.8 × 2 | Result 0.001875 K/W |
Thermal resistance calculation examples
Make sure the thickness, area, and thermal conductivity are all expressed in the same unit of measurement (e.g., all in meters or all in inches) and that the units cancel out properly in the formula.
FAQs on Thermal Resistance
High vs. low thermal resistance—what’s the difference?
Both situations have their uses. Insulating materials need to exhibit high thermal resistance to slow heat infiltration or exfiltration from insulated regions. On the flip side, devices like radiators need to be made of materials with low thermal resistance because their purpose is to transfer heat away from themselves and their associated devices.
Thermal resistance vs. thermal conductivity—what’s the difference?
Thermal resistance describes how well (or not) a particular material can resist heat flow, and thermal conductivity measures a material's inherent capacity to conduct heat.
Are there any limitations to highly thermal-resistant materials?
Although they can reduce the speed of heat transfer, high thermal resistance materials can’t completely stop it. No matter how resistant a material is, heat will always travel from warmer to cooler regions. In some circumstances, even excellent insulation might not be enough to stop heat gain/loss in a building or enclosed space. Temperature variations may also be caused by other factors, such as air leakage and poor ventilation design. Also, some insulating materials (i.e., fiberglass) can also absorb moisture, which reduces thermal resistance and could cause problems like mold growth.
How Xometry Can Help
Any questions on thermal resistance? Get in touch with one of our representatives, who can answer all your queries and guide you in the right direction. You can also quickly and easily get an estimate for any of our many prototyping and production services—get started today by uploading your designs to the Xometry Instant Quoting Engine®!
Disclaimer
The content appearing on this webpage is for informational purposes only. Xometry makes no representation or warranty of any kind, be it expressed or implied, as to the accuracy, completeness, or validity of the information. Any performance parameters, geometric tolerances, specific design features, quality and types of materials, or processes should not be inferred to represent what will be delivered by third-party suppliers or manufacturers through Xometry’s network. Buyers seeking quotes for parts are responsible for defining the specific requirements for those parts. Please refer to our terms and conditions for more information.
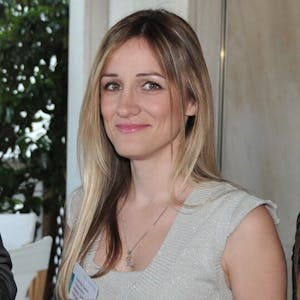