Thermoplastic rubber is a material that has the elastomeric properties of rubber while being easy to process using existing thermoplastic processing equipment like injection molding. It must be noted that TPR has different chemistry when compared to rubber and contains no latex. TPR was created to replace typical vulcanized rubber products which are more time-consuming, costly, and difficult to process.
The key properties of thermoplastic rubber include excellent fatigue resistance, chemical resistance, impact resistance, and high recyclability.
This article will describe the typical properties of thermoplastic rubbers, how they are manufactured, their chemical resistance, and their origin.
What Is Thermoplastic Rubber (TPR)?
Thermoplastic rubber (TPR) is a semi-crystalline material with both rubber-like and thermoplastic properties. This means it is flexible and can be manufactured using melt processing techniques like injection molding. TPR material is synthesized using block copolymers like SBS (Styrene-Butadiene-Styrene). Thermoplastic rubber can also be described as a thermoplastic elastomer. However, when comparing TPR vs. typical TPE, TPEs are mostly manufactured from SEBS (Styrene-Ethylene-Butadiene-Styrene) based polymers whereas TPRs are manufactured from SBS polymers.
Chemical Properties | Definition |
---|---|
Chemical Properties Chemical Resistance | Definition TPRs show excellent resistance to a wide range of chemicals including: dilute acids, dilute alkalis, oils, grease, and hydrocarbons. |
Chemical Properties Easily Colored | Definition TPR can be manufactured in a wide array of colors and can also be painted. |
Chemical Properties Recyclable | Definition Due to its thermoplastic nature, TPR can be recycled as easily as other thermoplastics. |
Table 1. TPR Chemical Properties
Physical Properties | Definition |
---|---|
Physical Properties Impact-resistant | Definition Most elastomer materials, including TPR, have excellent compression strength and can therefore withstand impact loads. |
Physical Properties Temperature Range | Definition TPR can maintain its properties across a wide range of temperatures from -40 °C up to 120 °C. |
Physical Properties Highly Elastic | Definition TPR has excellent elasticity that can be compared to vulcanized rubbers and thermosetting elastomers like polyurethane. |
Physical Properties Wide Range of Hardness | Definition TPRs can be made very hard with a hardness range starting at 20 Shore 00 through to a very high hardness value of 85 on the Shore D scale. |
Physical Properties Flexural Fatigue Resistance | Definition TPRs can undergo multiple load/unload cycles without failing due to fatigue. This is why they are often used for shoe soles. |
Physical Properties Tear & Abrasion Resistance | Definition TPR will resist tearing if nicked while also exhibiting excellent abrasion resistance. |
Physical Properties Electrical Insulator | Definition TPR can behave like an electric insulator. |
Table 2. TPR Physical Properties
How Thermoplastic Rubber is Manufactured
TPR is a block copolymer made up of SBS (Styrene-Butadiene-Styrene), which is essentially a synthetic rubber. SBS, and by extension TPR, are manufactured using living anionic polymerization. This is a chain polymerization process that takes two monomers, namely: butadiene and styrene; and polymerizes them into SBS. This creates a polymer structure that contains hard crystalline regions that consist of styrene and soft amorphous regions that contain butadiene. Styrene provides thermoplastic properties whereas butadiene supplies elastomeric properties.
The figure below indicates the differences between amorphous, semi-crystalline, and crystalline molecular structures:
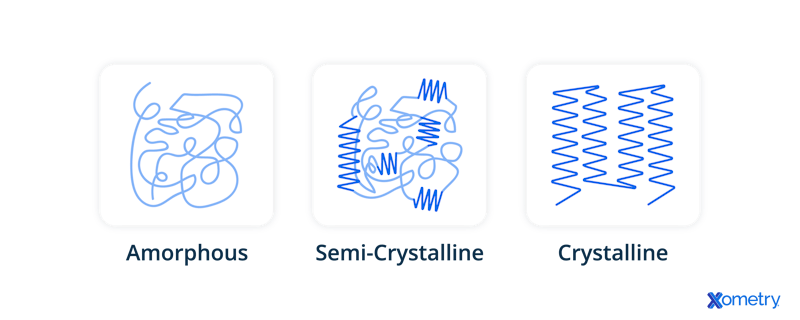
TPR is typically produced as plastic pellets that are then used for melt-processing manufacturing techniques, such as the following:
- Rubber Injection Molding: Molten plastic is injected into a mold to create complex-featured parts. Alternatively, the TPR is molded over a more rigid structure to create soft grips; this process is called overmolding.
- Blow Molding: Air forces the molten plastic onto the inner surface of a mold to create thin-walled components
- Extrusion: Molten plastic is forced through a die that enables the manufacture of components with a continuous cross-section
- Calendering: This process is used to create flat flexible sheets, sometimes with fabric cores. Typical applications are conveyor belts.
Corrosive Chemical | TPR Material Chemical Resistance |
---|---|
Corrosive Chemical Aliphatic Hydrocarbons | TPR Material Chemical Resistance Excellent |
Corrosive Chemical Aromatic Hydrocarbons | TPR Material Chemical Resistance Good |
Corrosive Chemical Halogenated Hydrocarbons | TPR Material Chemical Resistance Moderate |
Corrosive Chemical Dilute Acids | TPR Material Chemical Resistance Excellent |
Corrosive Chemical Dilute Alkalis | TPR Material Chemical Resistance Excellent |
Corrosive Chemical Alcohols | TPR Material Chemical Resistance Good |
Corrosive Chemical Oil & Grease | TPR Material Chemical Resistance Excellent |
Table 3. TPR Chemical Resistance Properties
Thermoplastic Rubber as an Injection Molding Material
TPR is an excellent choice for injection molding due to the melt-processing properties of thermoplastic rubber. It is the best material choice if rubber-like properties are desired while also having good mechanical properties and chemical resistance.
For more information, see our Full Guide to Plastic Injection Molding.
Xometry provides a wide range of manufacturing capabilities and value-added services for all of your prototyping and production needs. Get an instant quote today.
Disclaimer
The content appearing on this webpage is for informational purposes only. Xometry makes no representation or warranty of any kind, be it expressed or implied, as to the accuracy, completeness, or validity of the information. Any performance parameters, geometric tolerances, specific design features, quality and types of materials, or processes should not be inferred to represent what will be delivered by third-party suppliers or manufacturers through Xometry’s network. Buyers seeking quotes for parts are responsible for defining the specific requirements for those parts. Please refer to our terms and conditions for more information.
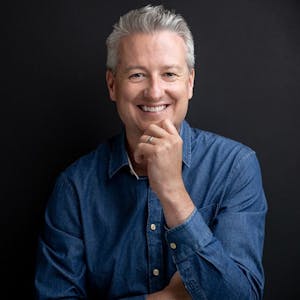