TPR (thermoplastic rubber) is a copolymer that merges the properties of butadiene (synthetic) rubber and polystyrene (PS). This material has similar properties to synthetic rubber but can be processed and reprocessed using a more precise and controllable injection molding process. TPR is known for its outstanding fatigue resilience, impact strength, and chemical stability, as well as for being reasonably recyclable with the right processing.
Latex, meanwhile, has both a colloquial definition and a very different scientific definition. In science, latex means any suspension (colloid) of polymer particles in a liquid (usually aqueous) medium. In common usage, latex refers to the sap of the Brazilian rubber tree, or, less commonly of the Congo rubber vine (among other plants). It also gets applied to a group of rubber materials that find various uses in industry and the home. In that context, latex is taken to mean the variety of natural rubbers that contain dried natural rubber.
This article will further compare TPR vs latex and list some of the applications, physical properties, costs, and alternatives to both.
What is TPR?
TPR is a blend containing 23% of polystyrene and 77% of butadiene. It is prepared by emulsion polymerization of the constituent polymers which makes an inseparable material that contains an elastomeric, thermoset phase, and a distributed, rigid matrix of thermoplastic material. TPR derives properties from both components but can be processed with extreme precision in injection molding equipment.
Typical rubbers are first synthesized or refined in a partially polymerized form and the cross-linking is completed by applying heat. In the case of TPR, the butadiene component is manufactured fully crosslinked and produced as a fine powder. The PS component then substitutes for the crosslinking by bonding the rubber into a strong polymer matrix. Flexibility results from the elasticity of the butadiene component, while the intra-particle rubber bonding is essentially inelastic.
TPR does not match the performance of vulcanized rubbers and has too low a tear modulus to be used in tires. However, the significantly better ozone, weathering, and UV properties of TPR mean that it finds wide use across many product sectors. For more information, see our guide on What is TPR Material.
What is Latex?
Latex refers to rubber materials made by the dry natural rubber process. In its newly harvested form, the rubber tree sap is a viscous, milky liquid that quickly coagulates when exposed to the atmosphere and allowed to dry. The coagulate eventually dries into a black, sticky, and foul-smelling mass that functions as feedstock for the manufacture of many rubber products.
Processing begins by boiling the partially coagulated latex, causing pieces of crude rubber to float to the surface. This material is rolled into sheets. The remaining fluid is removed and forms partially crosslinked natural rubber which can be incorporated into other manufacturing processes. This sheet rubber is then masticated (shredded and pressed) and a variety of compounding additives are introduced, depending on the intended application. The resultant material from this stage is either calendared (hot rolled into sheets) or extruded.
Some products are put through an additional vulcanization stage. The material is pressure-heated to 140°C at 1 atmosphere and finely divided sulfur is added. The sulfur penetrates the material and adds strong crosslinks. In its unvulcanized form, the rubber is highly elastic, soft, and relatively weak. Once vulcanized, the rubber takes on the form we find most familiar. It’s often black due to a carbon additive it receives at the compounding stage. Both vulcanized and unvulcanized latex has many applications.
TPR vs. Latex: Applications and Uses
Listed below are some market sectors that use TPR with their corresponding applications:
- Auto manufacture: Door and window seals, transmission/suspension parts, fender inserts, exterior and interior trim, instrument panels, AC and engine air ducts, grommets, drive belts, fluid pipes, floor mats, O-rings.
- Construction: Doors and window seals, hydraulic seals, plumbing seals.
- Consumer: Refrigerator seals, hand grip overmolds, mobile phone covers, switch panels, vibration dampers.
- Electronics: Encapsulation, power leads, high-quality cables, mobile phone shock protection, and seals.
- Footwear & Sports Equipment: Diving flippers, snorkels, masks, ski pole grips, ski boot components, and shoe soles.
- Industrial: Vibration dampers, pipes, manifolds, seals, suspension bushes, shock absorbers, roof membranes.
- Medical: Air tubes, syringe seals, breathing masks and plenums, seals, valves, and catheters.
Listed below are some latex applications:
- Auto manufacture: Tires, inner tubes, suspension components, window seals, floor mats, etc.
- Construction: Sound dampening, carpet underlay.
- Industrial: Vibration dampers, pipes, manifolds, seals, suspension bushes, shock absorbers, roof membranes, adhesives, spray nozzles, and duckbill valves.
- Consumer: Disposable gloves, condoms, diaphragms, elastic bands, and erasers.
- Medical: Vasculogenesis and osteogenesis aids, matrix for controlled drug release, blood pressure cuff coils, hypodermic injection ports, and vial ports.
- Footwear & Sports Equipment: Diving flippers, snorkels, masks, ski pole grips, ski boot components, and shoe soles.
TPR and latex (natural rubber) are parallel but dissimilar materials that have limited common properties. While they often find use in the same market sectors and product areas, the use of unalloyed natural rubber is less common than it used to be, since the synthetic alternatives cost less and generally perform better. There are applications that are optimal for latex-derived rubbers (generally those that best exploit its extreme elasticity). TPRs are ill-suited to most such uses, being less elastic, harder, and more expensive. Natural rubbers are more fragile in environmental exposure, so they’re mainly good for single-use items. The exceptions are when they’re heavily loaded with carbon black (tires, for example).
TPR vs. Latex: Physical Properties
Table 1 below compares TPR vs latex in terms of physical properties:
Property | TPR value (metric) | Latex value (metric) |
---|---|---|
Property Hardness, Shore D | TPR value (metric) 10 - 69 | Latex value (metric) 30 - 100 |
Property Tensile strength, ultimate | TPR value (metric) 0.345 - 80.0 MPa | Latex value (metric) 28 MPa |
Property Tensile strength, yield | TPR value (metric) 0.586 - 4.83 MPa | Latex value (metric) - |
Property Elongation at break | TPR value (metric) 30-500% | Latex value (metric) 100-800% |
Property Modulus of elasticity | TPR value (metric) 0.0180 - 0.683 GPa | Latex value (metric) Very low! |
Property 100% modulus | TPR value (metric) - | Latex value (metric) 1.5 MPa at 100% strain |
Property Flexural yield strength | TPR value (metric) 2.66 - 24.1 MPa | Latex value (metric) - |
Property Flexural modulus | TPR value (metric) 0.0917 - 0.814 GPa | Latex value (metric) - |
Property Taber abrasion, mg/1000 cycles | TPR value (metric) 30-800 | Latex value (metric) High but unreported |
Property Melting point | TPR value (metric) 104 - 191°C | Latex value (metric) Softens or decomposes above 180°C |
Property Coefficient of thermal expansion, linear | TPR value (metric) 110 - 170 µm/m°C | Latex value (metric) 225 µm/m°C |
TPR vs. Latex: Recyclability and Sustainability
The two materials come from quite different source chemistries and have very different environmental profiles. TPR is generally derived from petrochemical sources, the styrene monomer being manufactured from oil and the butadiene portion being manufactured from pre-refined butane. It is highly recyclable, but like most polymers, the recycled material is second-grade. TPRs are stable materials that degrade extremely slowly in the natural environment. Additionally, algal-derived monomer source materials for TPRs have begun reaching the market.
Latex is a naturally derived material made from the sap of the Brazilian rubber tree, Hevea brasiliensis, or less commonly from the Congo rubber vine, Landolphia owariensis. Significant amounts of forest land around the tropics have been cleared to make way for rubber plantations. Plantations are monocultures that can only sustain very limited biodiversity. Raw unvulcanized latex, meanwhile, is far more environmentally friendly than its petroleum-based counterparts. It has a short functional lifespan and breaks down into harmless residues. It is also attacked by various microorganisms. Once vulcanized (cross-linked by the addition of sulfur and heat), the rubber becomes very environmentally stable and represents a significant environmental burden.
TPR vs. Latex: Cost
TPRs are generally very low-cost materials, in the range of$1.60 to $2.00 per kg. Latex-based natural rubbers, in the pre-vulcanized, partially crosslinked state can be bought at $1.20 per kg. Vulcanized rubber can be bought starting at $1.48 per kg.
Alternative Materials to TPR and Latex
Latex and TPR are not interchangeable, but there is significant commonality in their applications. TPRs, as the name suggests, are thermoplastics, so they can be processed in injection molding equipment (and also in transfer molding). Latex is a thermosetting material that is generally transfer-molded or extruded in its partially polymerized state and then heat-cured to complete the cross-linking process. It cannot be injection molded.
For injection molding use, a wide variety of thermoplastic elastomeric materials are available, with an equally wide spectrum of properties and costs. While no one version can serve all purposes, their properties overlap enough to create a broad spectrum of materials. The following cover most applications:
- Fluoropolymer Elastomers (FPE)
- Melt Processable Rubber (MPR)
- Thermoplastic Polyether Block Amides (TPE-A)
- Thermoplastic Copolyesters (TPE-E or COPE or TEEE)
- Thermoplastic Vulcanisates (TPE-V or TPV)
- Thermoplastic Polyolefins (TPE-O or TPO)
- Styrenic Block Copolymers (TPE-S)
In parallel, thermosetting polymers whose properties are generally closer to those of latex offer additional material choices:
- Butadiene Rubber (BR)
- Nitrile Butadiene Rubber (NBR)
- Polyisoprene (IR)
- Polychloroprene (CR)
- Vulcanized Natural Rubber (NR) (also called buna rubber)
Thermoset rubbers bring new properties and new restrictions to the table but can achieve remarkable results when the goal is a specific property and when thermoset processing is not a disqualifier.
Summary
This article presented TPR and latex, explained what they are, and discussed when to best use each material. To learn more about TPR and latex, contact a Xometry representative.
Xometry provides a wide range of manufacturing capabilities and other value-added services for all of your prototyping and production needs. Visit our website to learn more or to request a free, no-obligation quote.
Disclaimer
The content appearing on this webpage is for informational purposes only. Xometry makes no representation or warranty of any kind, be it expressed or implied, as to the accuracy, completeness, or validity of the information. Any performance parameters, geometric tolerances, specific design features, quality and types of materials, or processes should not be inferred to represent what will be delivered by third-party suppliers or manufacturers through Xometry’s network. Buyers seeking quotes for parts are responsible for defining the specific requirements for those parts. Please refer to our terms and conditions for more information.
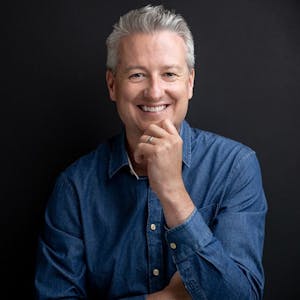