TPR (Thermoplastic Rubber) is a synthetic, rubber-like elastomer that behaves as thermoplastic, meaning that it can be melted during processing and will solidify after cooling. TPR is primarily used for applications in which flexibility, toughness, and grip are important. One of the main uses for TPR is shoe soles. PVC (polyvinyl chloride) is an engineering thermoplastic with excellent corrosion resistance; PVC can be flexible (plasticized PVC) or rigid (unplasticized PVC). Rigid PVC can be processed using extrusion, injection molding, or blow molding. Rigid PVC is widely used in the construction industry for piping, whereas flexible PVC is used for PPE (personal protective equipment) and flexible hoses.
This article will discuss the differences and comparison of TPR vs. PVC in terms of applications, uses, properties, and costs.
What to Know About TPR
Thermoplastic rubber refers to a range of synthetic rubbers that can be melt processed via injection molding, compression molding, and blow molding, for example. There are also non-natural (synthetic) rubbers that are not thermoplastics, like butyl. Normal, natural, and synthetic rubbers do not melt when heated and will break down chemically if overheated. Thermoplastic rubber is used in applications for which a flexible, durable, and high-grip material is required but is sufficiently complex in terms of geometry to necessitate the use of thermoplastic processing equipment like blow molding or injection molding. TPR is tough, has good chemical resistance, and has good fatigue resistance. For more information, see our guide on Thermoplastic Rubber.
Figure 1 is an example of a shoe sole made from TPR:
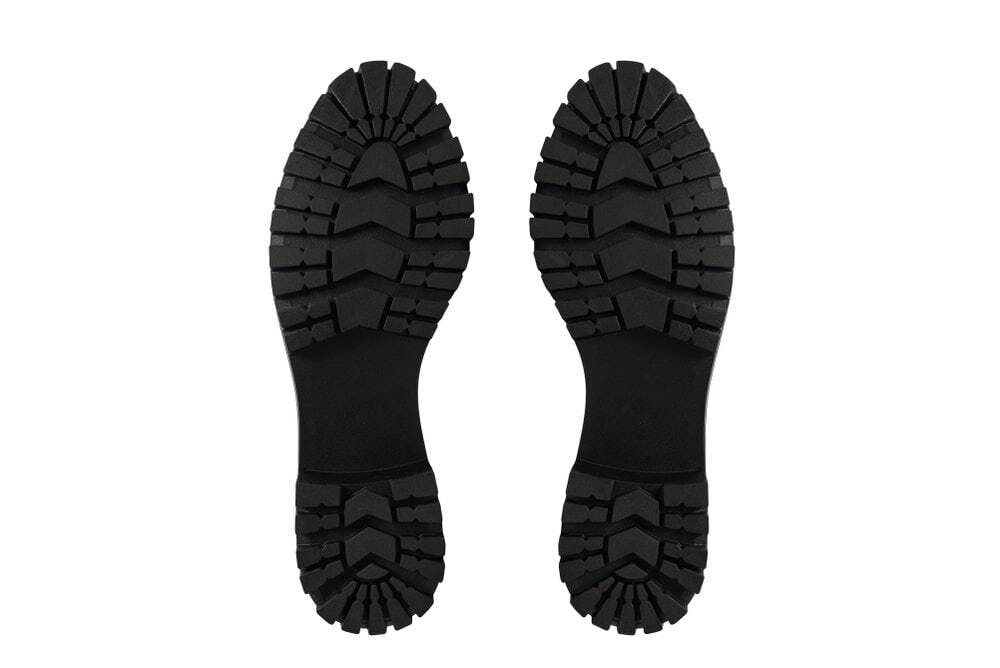
Black rubber shoe soles.
Image Credit: Shutterstock.com/mdbildes
TPR is made up of SBS (Styrene Butadiene-Styrene) which is a type of block copolymer. TPR is synthesized by making use of a process called living anionic polymerization. This is a chain polymerization process that polymerizes two monomers, namely butadiene, and styrene, into SBS. This creates a polymer structure with hard, crystalline regions and soft, amorphous regions. The hard regions contain styrene, and the soft regions contain butadiene. The hard regions provide the thermoplastic properties, whereas the amorphous regions supply the elastomeric properties.
What to Know About PVC
PVC or poly vinyl chloride is an engineering thermoplastic with excellent resistance to moisture ingress and UV (ultraviolet light). Its good abrasion resistance makes it a popular choice for piping and construction materials. PVC is generally available in two forms, namely plasticized (PVC-P) and unplasticized (PVC-U). Unplasticized PVC is used in parts that require rigidity, like pipes and fittings. Plasticized PVC is used in applications that require flexibility, like cables, tubes, and PPE (personal protective equipment). Modified grades of PVC are available which have various additives to improve PVC properties—like overall strength. These grades are referred to as PVC-M (Modified). PVC can be melt-processed using injection molding, extrusion, and blow molding. In addition to this, PVC pipes and fittings can be bonded with glue. Figure two shows a PVC pipe:
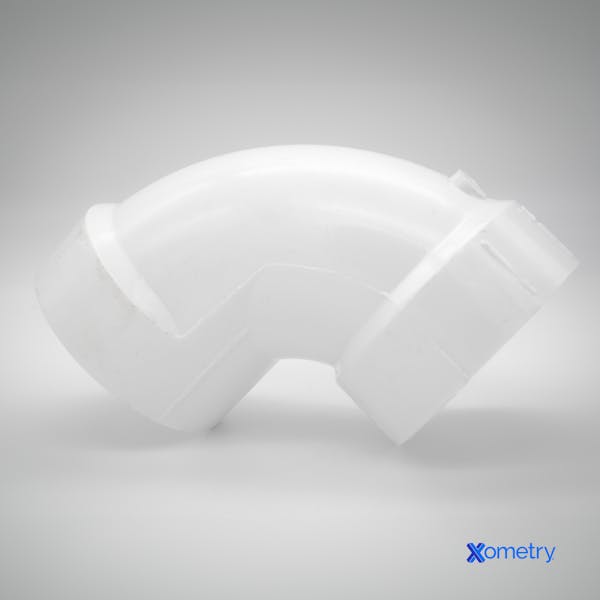
PVC is synthesized via the polymerization of the vinyl chloride monomer, through a process called addition polymerization, which opens the double bands on the vinyl chloride molecule and joins it up with another vinyl chloride molecule to create a long polymer chain.
TPR vs. PVC: Applications and Uses
TPR has been widely used for shoe soles due to its slip resistance, low cost, and flexibility. Some typical applications are listed below:
- Shoe soles
- Dog toys
- Tire treads
- Gaskets
PVC is available in a rigid form as well as a flexible form. The applications listed below relate to the flexible form of PVC for comparative purposes. PVC has excellent chemical resistance.
- Cables
- Tank liners for chrome plating
- PVC films
- Flooring, roofing
- Flexible pipe and hose
- Waterproofing membranes
- Packaging
TPR vs. PVC: Physical Properties
Table 1 below lists the mechanical, thermal, and electrical properties of TPR as well as those of rigid and flexible PVC:
Properties | Thermoplastic Rubber (TPR) | Plasticized PVC (PVC-P) (Flexible Grade) | Unplasticized PVC (PVC-U) (Rigid Grade) |
---|---|---|---|
Properties Tensile Strength (MPa) | Thermoplastic Rubber
(TPR) 2.5 | Plasticized PVC (PVC-P)
(Flexible Grade) 9.65 | Unplasticized PVC (PVC-U)
(Rigid Grade) 16.6 |
Properties Melting Temperature Range (C) | Thermoplastic Rubber
(TPR) 140–185 | Plasticized PVC (PVC-P)
(Flexible Grade) 190 | Unplasticized PVC (PVC-U)
(Rigid Grade) 177 |
Properties Impact Strength (Izod Notched) J/cm | Thermoplastic Rubber
(TPR) - | Plasticized PVC (PVC-P)
(Flexible Grade) 4.45 | Unplasticized PVC (PVC-U)
(Rigid Grade) 6.62 |
Properties Hardness (Shore A & D) | Thermoplastic Rubber
(TPR) 40 A | Plasticized PVC (PVC-P)
(Flexible Grade) 75 A | Unplasticized PVC (PVC-U)
(Rigid Grade) 68.3 D |
Properties Modulus of Elasticity (GPa) | Thermoplastic Rubber
(TPR) - | Plasticized PVC (PVC-P)
(Flexible Grade) 2.4 | Unplasticized PVC (PVC-U)
(Rigid Grade) 2.16 |
Properties Elongation at break (%) | Thermoplastic Rubber
(TPR) 550 | Plasticized PVC (PVC-P)
(Flexible Grade) 328 | Unplasticized PVC (PVC-U)
(Rigid Grade) 312 |
Properties Tear Resistance (N/mm) | Thermoplastic Rubber
(TPR) 15 | Plasticized PVC (PVC-P)
(Flexible Grade) 53.7 | Unplasticized PVC (PVC-U)
(Rigid Grade) 33.6 |
Properties Dielectric Strength (kV/mm) | Thermoplastic Rubber
(TPR) - | Plasticized PVC (PVC-P)
(Flexible Grade) 58.9 | Unplasticized PVC (PVC-U)
(Rigid Grade) 14–20 |
TPR represents a wide range of different formulations. As such, the values represented in Table 1 only serve as a snapshot of the potential range of properties. Always consult a raw material supplier for more applicable datasheets when choosing a material.
TPR vs. PVC: Recyclability and Sustainability
PVC and TPR are both produced from crude oil—which is non-renewable and a pollutant and therefore cannot be regarded as sustainable. PVC can be recycled up to eight times. Despite this recyclability, the vast majority of plastics are not recycled; they simply end up on landfill sites or in the ocean.
TPR is a thermoplastic and as such can be theoretically recycled. However, plastic recycling is already quite rare with far more popular commodity plastics like polyethylene. In light of this, recycling lower-volume materials, like TPR, is not typically economical or common practice.
TPR vs. PVC: Cost
Thermoplastic rubbers like TPR are generally more expensive than the more popular PVC. PVC has an annual production volume of 44.3 million metric tons and is relatively low-cost when compared to other rigid engineering thermoplastics. PVC can cost up to US $1,389 per ton and TPR can cost between $1,470 and $2,250 per metric ton.
Alternative Materials to TPR and PVC
A suitable alternative to TPR or flexible PVC would be either TPE-S (also known as the thermoplastic elastomer SEBS) or TPU (thermoplastic polyurethane). These materials have similar elastomeric properties as well as comparable mechanical properties like tensile strength and elongation. Potential replacements for rigid PVC include polypropylene or HDPE (High-Density Polyethylene). Both of these materials have excellent corrosion resistance and toughness.
How Xometry Can Help
Xometry provides a wide range of manufacturing capabilities and other value-added services for all of your prototyping and production needs. Visit our website to learn more or to request a free Xometry production quote.
Disclaimer
The content appearing on this webpage is for informational purposes only. Xometry makes no representation or warranty of any kind, be it expressed or implied, as to the accuracy, completeness, or validity of the information. Any performance parameters, geometric tolerances, specific design features, quality and types of materials, or processes should not be inferred to represent what will be delivered by third-party suppliers or manufacturers through Xometry’s network. Buyers seeking quotes for parts are responsible for defining the specific requirements for those parts. Please refer to our terms and conditions for more information.
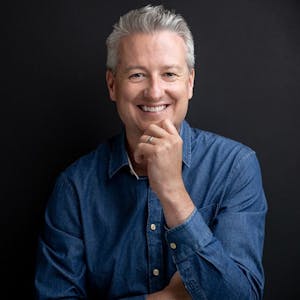