The materials known as thermoplastic elastomers (TPE) exhibit the properties of thermoplastics as well as those of elastomers. This combination allows designers to get elastomeric capabilities out of melt-processed materials. Thermoplastic elastomers are used in almost every industry and there are many types of thermoplastic elastomers on the market. This article will explore them and discuss some general TPE material properties.
Table 1 below summarizes the types of thermoplastic elastomers:
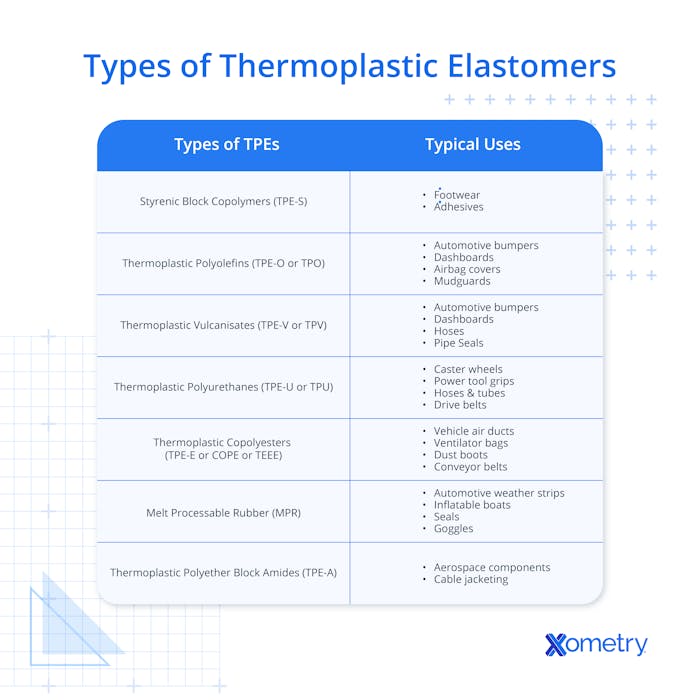
1. Styrenic Block Copolymers (TPE-S)
Styrenic block copolymer thermoplastic elastomers, commonly known as TPE-S materials, are either made from SBS or SEBS. Styrene Butadiene Styrene (SBS) is a type of TPE whose molecular structure consists of repeated styrene and butadiene units with styrene end caps. This structure creates hard blocks of styrene and soft blocks of butadiene. SBS is the most common TPE. Styrene Ethylene Butylene Styrene (SEBS) is made by hydrogenating SBS, a process that breaks down the butane mid-block into ethylene butadiene. This process improves the TPE’s heat and chemical resistance, gives it good weathering resistance, and better protection against UV and ozone. SEBS can bond to other thermoplastics. It is ideal for outdoor applications.
TPE-S can be processed using standard melt-processing techniques like injection molding.
Applications for TPE-S
- Adhesives
- Asphalt modifying agents
- Footwear
- Low-grade seals
Properties of TPE-S
- Electrically insulative
- Large hardness range
- Good abrasion resistance
- Colorless & transparent
- UV & ozone resistant
2. Thermoplastic Polyolefins (TPE-O or TPO)
TPO materials, often referred to as thermoplastic olefins, are thermoplastic elastomers that blend polypropylene or polyethylene with an elastomer such as: EPDM, EPR, EO, or EB. These elastomers are typically not cross-linked. The various constituents are mechanically blended together. TPO has good thermal and chemical resistance. It does not exhibit many elastomeric properties and has a relatively high hardness of 80 on the Shore A scale. TPO is used in applications where standard polypropylene is not tough enough. TPO can be processed using injection molding, extrusion, or blow molding.
Applications of TPO
- Automotive bumpers
- Dashboards
- Airbag covers
- Mudguards
Properties of TPO
- Flame retardant
- Excellent weather resistance
- Good chemical resistance
- Tougher than polypropylene copolymers
3. Thermoplastic Vulcanisates (TPE-V or TPV)
TPVs (Thermoplastic Vulcanisates), like TPOs, are made from a mixture of polypropylene and EPDM. However, in this case, the EPDM is vulcanized during compounding. TPVs have a wider hardness range. They also exhibit better elastomeric properties than TPOs. TPVs can resist temperatures up to 120°C and are widely used in vehicle engine compartments. TPV materials can be formed using standard melt-processing techniques like injection molding.
Applications of TPV
- Automotive seals
- Bellows
- Hoses
- Pipe seals
Properties of TPV
- High-temperature resistance of up to 120°C
- Low compression set
- Chemical and weather resistant
- Hardness range from 45A to 45D
4. Thermoplastic Polyurethanes (TPE-U or TPU)
TPU (Thermoplastic Urethane) is formed by reacting diisocyanates with either a type of polyester or polyether polyol. The diisocyanates form the hard segments whereas the polyethers or polyesters form the soft segments. TPUs can be easily modified by changing the polyol and diisocyanate blend. TPU is typically processed with injection molding, extrusion, and blow molding.
Applications of TPU
- Caster wheels
- Power tool grips
- Hoses and tubes
- Drive belts
Properties of TPU
- Excellent abrasion resistance
- High tensile strength
- Significant elastic elongation range
- Excellent tear strength
- Resistant to petroleum-based oils and fuels
5. Thermoplastic Copolyesters (TPE-E or COPE or TEEE)
TPE-Es (Thermoplastic Copolyesters) are high-performance thermoplastic elastomers that share many properties with thermosetting elastomer polymers while having the advantage of being melt-processible. TPE-Es are block copolymers that typically consist of hard segments made from polybutylene terephthalate alongside soft segments made from various polyesters. TPE-E is widely used in the medical industry.
Applications of TPE-E
- Vehicle air ducts
- Ventilator bags
- Dust boots
- Conveyor belts
Properties of TPE-E
- Resistant to creep and compression set
- Excellent long-term resistance to temperatures up to 165C
- Resistant to oils and greases
- Electrically insulative
- Dimensionally stable
6. Melt Processable Rubber (MPR)
MPR is an alternative to vulcanized rubber and consists of a cross-linked halogenated polyolefin mixed with plasticizers and stabilizers. The primary purpose of MPR is to create rubber-like parts using thermoplastic processing equipment. MPR outperforms many other rubbers below an operating temperature of 120C.
Applications of MPR
- Automotive weather strips
- Inflatable boats
- Seals
- Goggles
- Hand grips
Properties of MPR
- UV resistant
- High friction coefficient
- Resistant to gasoline and oil
7. Thermoplastic Polyether Block Amides (TPE-A)
TPE-As consist of soft segments made from either polyethers or polyesters as well as hard segments made from polyamide. Different polyamides can be used such as polyesteramide (PEA), polyether ester amide (PEEA), or polycarbonate-esteramide (PCEA). The properties of an individual TPE-A depend heavily on the type of polyamide involved. TPE-A can be bonded to thermoplastic polyamides.
Applications of TPE-A
- Aerospace components
- Cable jacketing
Properties of TPE-A
- Excellent temperature resistance of up to 170C
- Good solvent resistance
- Good impact resistance
- Flexible at low temperatures
- Good wear resistance
Where are Thermoplastic Elastomers (TPEs) Used?
Thermoplastic elastomer materials are used across all major industries, including: automotive, agricultural, consumer, industrial, and electrical industries. Typically, TPE plastics are used wherever flexibility is required. Manufacturers select specific types of thermoplastic elastomers based on their expected operating environment; some are tailored for chemically corrosive conditions or high-temperature environments, for example.
Which Thermoplastic Elastomers (TPEs) Have the Most Applications?
The thermoplastic elastomer class with the widest range of uses is TPE-S. It is the most common TPE material on the market and finds use in many different applications. This is due to its relatively low cost compared to the more advanced thermoplastic elastomers. Additionally, it has generally good thermal, chemical, and mechanical properties.
What are the Benefits of Thermoplastic Elastomers (TPEs)?
Thermoplastic elastomers are mainly used for applications that demand elastomeric behavior and other TPE material properties. Some additional benefits of TPEs are listed below:
- Less energy required for production than thermosets compared to thermosets
- Recyclable due to thermoplastic behavior
- Good mechanical properties such as fatigue strength and creep resistance
- Melt processible using standard thermoplastic techniques such as: injection molding, 3D printing, and blow molding
- Easily colored using a wide variety of pigments
What Kind of Stretch Qualities Should My TPE Have?
TPEs exhibit a wide range of elastic behaviors. Their individual stretch qualities depend on the application and the types of thermoplastic elastomers involved. It must be noted that despite TPEs' ability to stretch far past their original length, they incur some degree of permanent deformation with each extension. As such, parts are best designed to stretch to only a fraction of their full capacity to keep this permanent deformation to a minimum.
Common FAQs About Thermoplastic Elastomers
How do Thermoplastic Elastomers (TPEs) React to Shrinkage?
Like most thermoplastics, TPEs shrink slightly after molding. This shrinkage can be accounted for by oversizing the mold dimensions. However, the exact shrinkage can only be accurately determined after molding a test part. Remember that it is easier to remove material from an undersized mold than it is to add material to one that’s too large.
Is it Safe to Use Thermoplastic Elastomers (TPEs)?
In general, TPE has a good record of material safety. TPEs are used in many different applications with some being medically safe and biocompatible and others declared food safe. In order to determine the safety of a specific TPE, refer to the MSDS (Material Safety Data Sheet) for that material.
Is There a Temperature at Which TPEs Should Be Used?
TPEs can be used across a wide range of temperatures. However, the range maxes out at 170°C for even the most temperature-resistant TPEs. TPEs are less resistant to heat than some high-temperature thermoplastics.
Summary
This article reviewed the properties and applications of 7 different types of thermoplastic elastomers (TPEs).
Disclaimer
The content appearing on this webpage is for informational purposes only. Xometry makes no representation or warranty of any kind, be it expressed or implied, as to the accuracy, completeness, or validity of the information. Any performance parameters, geometric tolerances, specific design features, quality and types of materials, or processes should not be inferred to represent what will be delivered by third-party suppliers or manufacturers through Xometry’s network. Buyers seeking quotes for parts are responsible for defining the specific requirements for those parts. Please refer to our terms and conditions for more information.
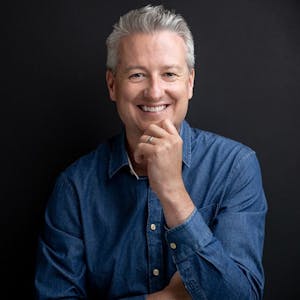