Aluminum and its alloys are one of the most commonly requested materials we offer at Xometry, especially for CNC machined components. It has been around for centuries, and even to this day, it’s an important metal found everywhere — from enormous manufacturing facilities to domestic kitchens. It plays a big part in a long list of applications, like sheet metal fabrication, aircraft construction, and the creation of cooking pans, soda cans, and foil for food storage. While you might be familiar with the element or material, we’re going to explore the background of aluminum, what purposes it serves in different industries, its chemical properties, and the services we have at Xometry that involve this metal.
What is Aluminum?
Aluminum is the most abundant metal on earth, and you’ll recognize it by its silvery-white appearance. Its attributes that garner the most attention are its ductility, corrosion resistance, and that it’s nonmagnetic. Because it’s largely abundant — it makes up 8% of the earth’s crust, after all — and has useful properties across the board, it’s the most produced refined non-ferrous metal, too, and makes up a $229.85 billion industry.
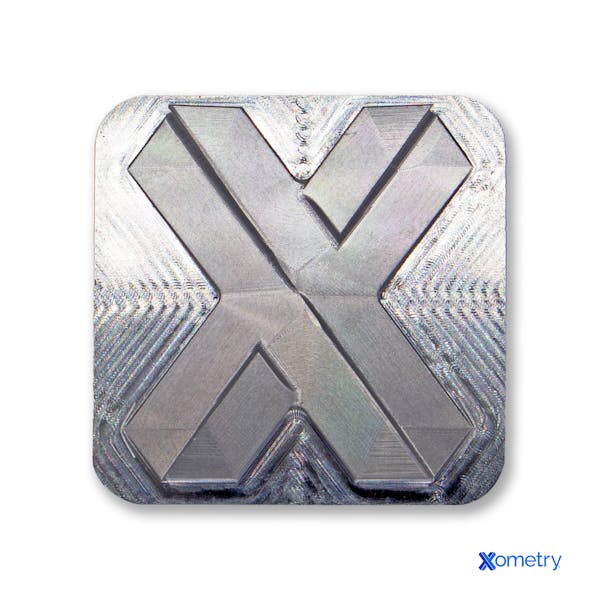
Discovery and History
We have been using aluminum long before it ever had a name or was scientifically recognized. Aluminum goes all the way back to the time of ancient Egypt, but it wasn’t until 1807 when British chemist Humphry Davy noticed its existence and named it. Later, in 1825, a Danish chemist by the name of Hans Christian Ørsted isolated aluminum.
As time went on, Henri Sainte-Claire Deville helped develop a method for producing aluminum in higher quantities and Charles Martin Hall and Paul Louis Toussaint Héroult created the smelting method for this metal, which is still very important for aluminum processing today — even to high manufacturing standards — and aptly titled the Hall-Héroult process.
Atomic Weight, Symbols, and Names
You can spot aluminum on the periodic table by the symbol Al and the atomic number 13, and it’s found in the third period and 13th group. Weighing in at 26.98 atomic mass units, it isn’t as heavy and dense as other metals out there.
While aluminum doesn’t have another name, it does have another spelling. Outside of the U.S., there is an extra “i” and it’s written and pronounced as aluminium.
Characteristics
Although aluminum is lightweight, it’s a strong and durable metal that’s great for electric and heat conductivity. You’ll find it sitting within the Boron group on the periodic table, and notice it’s capable of bonding with oxygen and various other elements that are in a -3 state. Get to know more of its physical and chemical properties up ahead.
Physical Properties of Aluminum
Below is a chart outlining the physical properties of aluminum:
Property | Definition | Example | Units | Importance |
---|---|---|---|---|
Property Density | Definition The mass of material per unit volume | Example 2.71 g/cm3 | Units g/cm3 | Importance Lightweight material with a high strength-to-weight ratio. |
Property Strength | Definition The ability of a material to withstand a load. | Example 80 MPa (AA1050A 0) to 570 MPa (AA7075 T6) | Units MPa or psi | Importance Has high strength given its low weight, which allows it to be used in several load-bearing applications. |
Property Color | Definition The wavelength of light reflected by a material | Example Lustrous, silver-white color | Units N/A | Importance Appealing appearance for various consumer products and structures. |
Property Ductility | Definition The ability of a material to bend or stretch before fracturing. | Example Highly ductile | Units Unitless. Total percent elongation after a tensile test | Importance Absorbs energy as plastic deformation before fracture, easily formed. |
Property | Definition | Example | Importance |
---|---|---|---|
Property Oxidation potential | Definition A reaction, typically with air. | Example Aluminum oxides in bauxite. | Importance Readily reacts with air and are typically found in nature as oxides. |
Property Ability to form alloys | Definition Ease of forming alloys with aluminum. | Example Several hundreds of different aluminum alloys exist. | Importance Allow desired physical and mechanical properties to be obtained that are not present in pure aluminum. |
Property Reactivity | Definition Ability to form aqueous and mutual solutions with other materials. | Example Aluminum reacts with mineral acids and alkalis to make aqueous solutions. | Importance Aluminum acids like aluminum hydroxide are commonly used as a fire retardant and in pharmaceuticals. Aluminum bases are commonly used in water treatment and accelerating concrete curing. |
Property Corrosion resistance | Definition A material’s ability to resist degradation due to corrosion | Example Commonly found as aluminum oxide in nature which makes it naturally corrosion resistant. | Importance Its natural corrosion resistance allows aluminum and its alloys to be used in a wide range of environments. |
Types of Aluminum
There are several types of aluminum, and some serve more specific uses than others. Learn more about the different types, below:
1. Pure Aluminum
With the lowest concentration of contaminants and no alloying elements, this type of aluminum is the purest form available. It’s rarely ever found in nature, so you often must refine bauxite and other ores to get this soft, ductile, conductive, and corrosion-resistant metal in its purest state. This type is best used for wires, cables, foil, and other applications where it won’t be expected to bear any loads.
2. Aluminum Alloys
Aluminum alloys are a melted mix of pure aluminum and other elements — like copper, zinc, silicon, and magnesium. The additional elements help create an aluminum that’s stronger and harder than pure aluminum. It still has its other characteristics, like good ductility and corrosion resistance, but it’s strong enough to be used in engines, airplane wings, and other products. Our most popular aluminum alloys at Xometry are aluminum 6061-T6 for machined parts and aluminum 5052 for sheet cut and sheet metal parts.
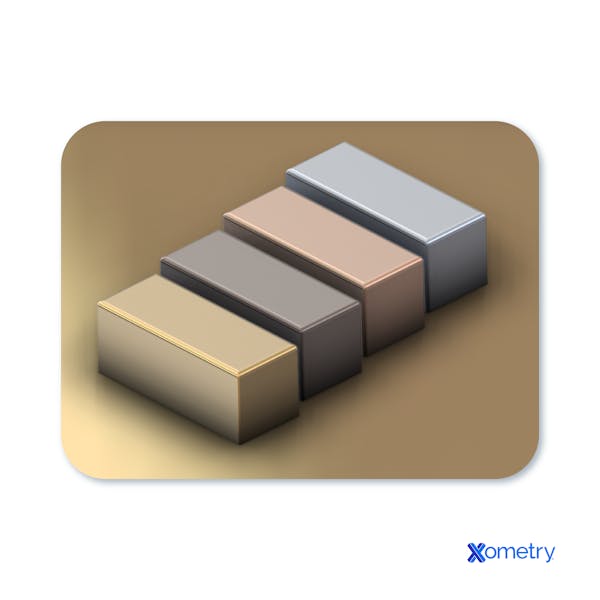
3. Cast Aluminum
To get cast aluminum, alloys are melted down and poured into molds, which then harden into the intended shape. As far as costs are concerned, it’s a more affordable way to create large numbers of parts, but with a lower price comes slightly lower ductility and tensile strength. At Xometry, we help with die casting products, which work particularly well with softer metals like aluminum.
4. Wrought Aluminum
This aluminum type is produced through rolling, forging, or metal extrusion, another service we offer. The results are strong aluminum rods, billets, or ingots, which you can then machine into parts for cars, aerospace vehicles, medical instruments, and consumer goods.
5. Anodized Aluminum
If manufacturers need to colorize or up the hardness of aluminum even further, they can anodize it. This occurs through an electrochemical reaction and results in a surface that’s harder and more durable. During this process, you can also change the color of aluminum and affect whether or not the finish is lustrous or matte. This process is usually selected when aluminum will be used in construction, home, or architectural products, like window frames, interiors of airplanes and trains, and kitchen appliances.
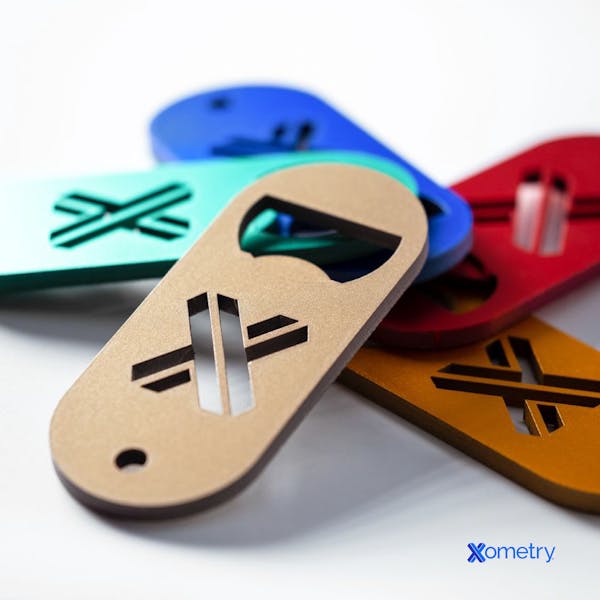
6. Clad Aluminum
This aluminum alloy is made to have even better levels of corrosion resistance. This is another form of anodized aluminum that’s created by adding extra layers of pure aluminum or an aluminum alloy on top of an aluminum substrate. Also called Alclad, it’s another go-to material solution when it comes to automotive, railway, and aerospace applications.
Applications
There is a lengthy list of uses for aluminum, so here are just a few:
- Aircraft components like wings and fuselage
- Hulls, masts, and other marine vessel components
- Automotive engines, vehicle bodies, and wheels
- Consumer packaging
- Beverage cans
- Home, high-rise, and building structures
- Electric appliances, like TV antennas, power lines, and satellite dishes
- Consumer goods like cookware, smartphone cases, laptops, and TVs
- Medical equipment such as wheelchairs, surgical instruments, walkers, and crutches.
Advantages and Disadvantages of Using Aluminum
Working with aluminum brings its fair share of benefits and disadvantages. Some of the advantages include:
- It’s a very lightweight material, which can be helpful for applications where weight is important — like with automotive and aircraft. It has about one-third the density of steel, ringing in at 2.71 g/cm³.
- Aluminum naturally forms a protective oxide layer on its surface, making it a great corrosion-resistant material to use in numerous environmental conditions. Corrosion resistance can be enhanced further by finishes like chem-film which we offer as a standard finish for aluminum parts.
There are also a few limitations of aluminum you should be cognizant of:
- Despite its strength, aluminum isn’t as strong as some other metals, like steel.
- It typically has a higher price than plastics, and some of the fancier aerospace-grade aluminum alloys can be pricey.
- Welding aluminum can be tricky as welds solidify much more quickly because of its high thermal conductivity.
How Xometry Can Help
Xometry offers a plethora of manufacturing services, many of which can involve aluminum, including sheet metal fabrication, metal extrusion, and custom die casting. If you need custom aluminum parts, you can upload your files and get an instant quote today.
Disclaimer
The content appearing on this webpage is for informational purposes only. Xometry makes no representation or warranty of any kind, be it expressed or implied, as to the accuracy, completeness, or validity of the information. Any performance parameters, geometric tolerances, specific design features, quality and types of materials, or processes should not be inferred to represent what will be delivered by third-party suppliers or manufacturers through Xometry’s network. Buyers seeking quotes for parts are responsible for defining the specific requirements for those parts. Please refer to our terms and conditions for more information.
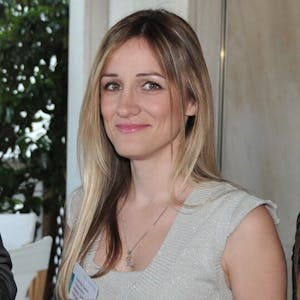