Magnesium alloys are known for their amazing strength-to-weight ratios, regardless of whether they are cast or wrought, and so this makes them extremely useful and appealing for many engineering applications. Compared to other materials Xometry offers, such as stainless steel and aluminum, magnesium can be up to 70% and 33% lighter respectively. In the world of structural metals, magnesium alloys do not only have the highest damping capacity, but they’re also cost-effective and very easy to work with.
This is why they’re commonly used in industries such as aerospace, automotive, electronic, defense, biomedical, green energy technologies, and manufacturing. Let’s take a look at everything to do with magnesium, including its composition, applications, chemical and physical properties, and advantages and limitations, to name a few. So, let’s get right to it.
What is Magnesium?
Magnesium (Mg), atomic number 12 on the periodic table, is a silvery-white alkaline earth metal that looks a little like aluminum and is solid and quite dense at room temperature. It got its name from Magnesia, a region in Greece’s Eastern Thessaly. At first, magnesium was mainly recognized through compounds like Epsom salts (magnesium sulfate), magnesia or magnesia alba (magnesium oxide), and magnesite (magnesium carbonate).
It’s the eighth most abundant metal on Earth, making up around 2.4% of the Earth’s crust. With a density of only 1.74 g/cm3, magnesium is considered the lightest structural metal. It only consists of magnesium atoms, and each atom has 12 protons in its nucleus, with each of them having a corresponding number of electrons orbiting around the nucleus.
Looking closer at its formation, magnesium has a hexagonal close-packed (hcp) crystalline arrangement. Like other metals with the same structure, magnesium is less malleable in lower temperatures when it’s being processed. Interestingly, when it’s in its pure form, it doesn’t possess enough strength for most structural applications. That’s why it’s often alloyed with other elements to improve its mechanical properties and make it fantastic for situations that require a light, yet durable material. The automobile, electronics, and aerospace sectors are all examples of industries that love to use magnesium alloys.
Regarding magnesium’s silvery-white color, this is only the case when it’s freshly exposed. Over time, when it’s exposed to air, it can develop a more gray color because of the thin layer of magnesium oxide that tends to form on the surface. Sometimes, the color can vary even more depending on the composition and surface treatment.
A Brief History of Magnesium
Magnesium made its first appearance way back in 1808, when Sir Humphrey Davy, a British chemist, passed electricity through a mixture of magnesium sulfate and mercury and then heated the mixture in order to remove the mercury and only leave the magnesium behind. Then, 20 years later, French scientist Antoine Bussy was able to produce the first metallic magnesium by reducing melted magnesium chloride with potassium vapor.
In 1833, there was further development when Michael Faraday, a scientist from England, made magnesium from the electrolysis of molten magnesium chloride. He did so well with this experiment that it was later replicated by German chemist, R. Bunsen. By 1886, magnesium was getting ready for industrial-scale production, thanks to the company Aluminium und Magnesiumfabrik Hemelingen based in Germany.
Fast-forward to the 1920s and 1930s, this company had become well-established in the magnesium production sector, especially when it came to the IG Farben process, which allowed them to produce large amounts of almost water-free magnesium chloride, and electrolyze it in order to extract chlorine and magnesium metal.
Making Magnesium
You won’t be able to find pure magnesium in nature, so obviously, it has to be produced by specialized chemical processes. The main places where magnesium can derive from are seawater and natural brines, which have approximately 1.3 kg/m3 of dissolved magnesium, and minerals like magnesite and dolomite.
A lot of energy is required in order to extract magnesium from raw source materials. The first step is to concentrate the source material into a form that can be used in one of the two following methods: the thermal reduction method, also called the Pidgeon process, or the electrolytic process. Let’s take a closer look at each of these.
Pidgeon Process
The Pidgeon process requires dolomite ore to be crushed and heated in a kiln, which produces a mix of magnesium and calcium oxides. After being combined with crushed ferrosilicon, this blend is made into briquettes, which are then heated in a vacuum until the silicon in the ferrosilicon has reduced the magnesium oxide to magnesium.
The process needs to be done at a temperature above magnesium’s vaporization temperature for a good result. When it’s finished, the pure element is collected as a gas, and then it’s condensed, cooled, and cast into ingots. The pigeon process can produce magnesium at a purity of up to 99.99%, which is slightly higher than the electrolytic processes, which we’ll dive into right now.
Electrolytic Process
The electrolytic process is broken down into two parts:
- Obtaining pure magnesium chloride from seawater or brine. This first step requires the treatment of seawater or brine with calcined dolomite, which produces magnesium hydroxide. This newly produced Mg(OH)2 is then converted into oxide. The oxide is then heated with carbon with some chlorine present, and this is carried out in an electric furnace at a high temperature.
- Electrolysis of fused magnesium chloride is the second step. When step one has been completed and fused anhydrous magnesium chloride has been produced, it’s then fed into electrolytic cells and melted in order to conduct electricity.
After the process has been completed, the molten magnesium is cast into ingots, and the chlorine gas is recycled into the chlorination furnace. After the electrolytic process has been done and magnesium has been extracted, it’s usually processed even more and used as an alloying element.
Magnesium’s Characteristics
Before using magnesium in any particular project, it’s good to know its key characteristics. We’ve compiled a list of them below, which primarily apply to pure magnesium, unless stated otherwise.
- Low density
- Highly flammable
- Susceptible to oxidation and corrosion
- Decent electrical conductivity
- Can be used in conjunction with other elements to form various alloys
- Excellent strength-to-weight ratio (especially in magnesium alloys)
- Great thermal conductivity (even when alloyed)
- Easy to cast (especially when alloyed)
- Biodegradable and biocompatible
- Fairly soft and pliable (can vary depending on each specific alloy structure)
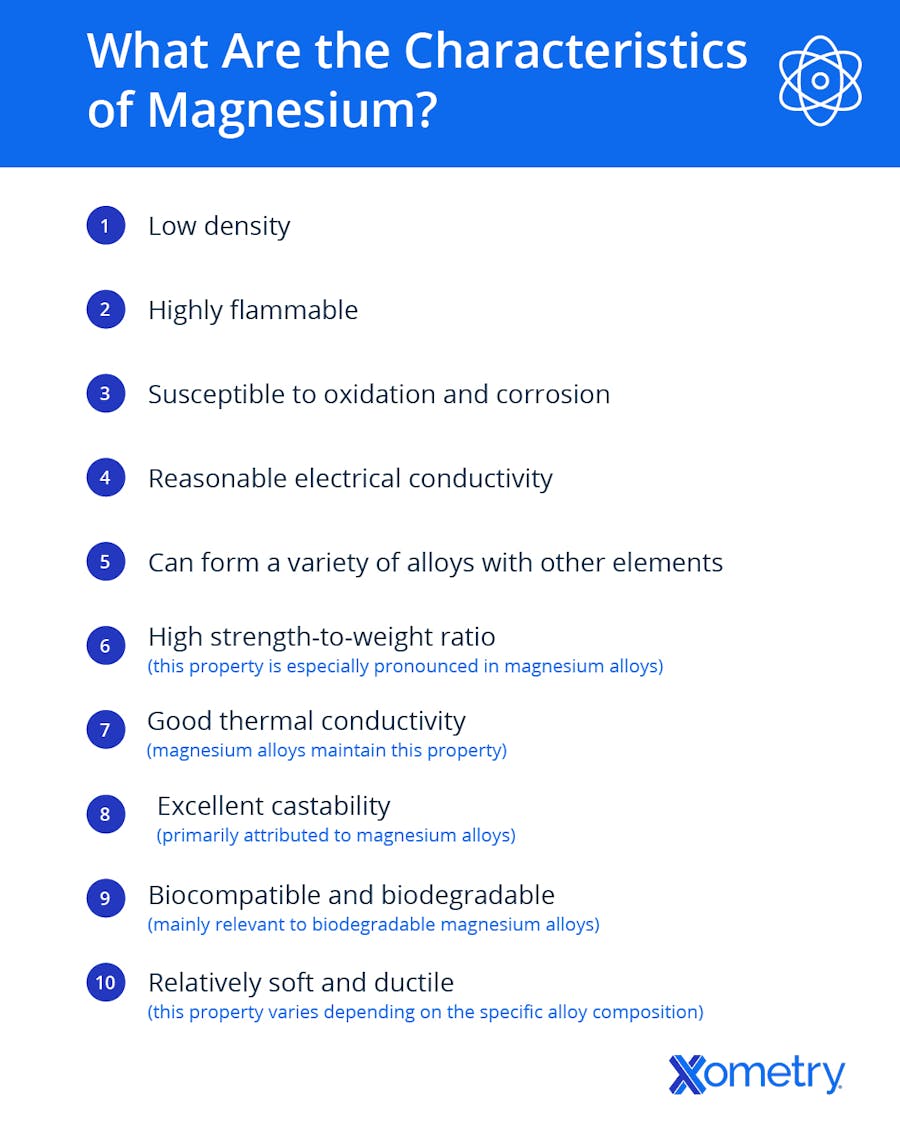
Property | Value/Description |
---|---|
Property Color | Value/Description Silvery-white |
Property Density | Value/Description 1.74 g/cm^3 at 20 °C |
Property Brinell hardness | Value/Description 30 |
Property Tensile strength | Value/Description up to 280 MPa (cast alloys), up to 360 MPa (wrought alloys), up to 20 MPa (pure cast) |
Property Yield strength | Value/Description up to 160 MPa (cast alloys), up to 300 MPa (wrought alloys), up to 20 MPa (pure cast) |
Property Young’s Modulus | Value/Description 44-45.5 GPa |
Property Ductility | Value/Description 0.12-0.2 |
Property Poisson’s Ratio | Value/Description 0.28-0.295 |
Property Melting point | Value/Description 650 °C (alloys will have different values) |
Property Boiling point | Value/Description 1107 °C (alloys will have different values) |
Property Flammable | Value/Description Yes |
Property Electrical conductivity | Value/Description 2.3×107 S/m |
Property Corrosion resistance | Value/Description Poor |
Property Thermal conductivity | Value/Description 156 W/mK |
Physical Properties of Magnesium
Property | Value/Description |
---|---|
Property Atomic number | Value/Description 12 |
Property Atomic mass | Value/Description 24.30 g/mol |
Property Atomic radius | Value/Description 0.160 nm |
Property Structure | Value/Description hexagonal close-packed (HCP) crystal structure in pure form |
Property Isotopes | Value/Description 3 natural isotopes with mass numbers 24,25 and 26 |
Property Valence electrons | Value/Description 2 |
Property Recyclable | Value/Description Yes |
Chemical Properties of Magnesium
Benefits | Limitations |
---|---|
Benefits Lightest structural metal, with a weight advantage of around 30% over aluminum, and 50% over titanium | Limitations Highly flammable—especially in its pure form—but this is not as bad when it’s in bulk form as opposed to powder or shaved strips |
Benefits Cost-effective option because it’s easy to find | Limitations Without the use of corrosion-resistant alloys, it can be more prone to corrosion than other metals like aluminum and stainless steel |
Benefits Incredible strength-to-weight and stiffness-to-weight ratios | Limitations Processing magnesium can be quite complex when compared to processing other metals |
Benefits Great thermal conductivity | Limitations Some magnesium alloys can be brittle, especially at low temperatures |
Benefits Excellent for electromagnetic shielding in aerospace and electronics applications | Limitations Though it’s easy to find, extracting and refining magnesium can consume a lot of energy |
Benefits Offers great corrosion resistance when engineered | Limitations Susceptible to galvanic corrosion, especially in the presence of an electrolyte |
Benefits Doesn’t require a lot of energy to recycle | Limitations The processing and production process can get more expensive than it would for other metals like aluminum and steel |
Benefits Has the highest known damping capacity among structural metals | Limitations Because of its low melting point, it’s not great for applications that need true high-temperature performance |
Benefits Easy to alloy with other metals and elements | Limitations - |
Benefits Some magnesium alloys are biocompatible and can be used for implants and medical devices | Limitations - |
Benefits Certain magnesium compounds are flame-retardant and useful in applications requiring fire safety | Limitations - |
Benefits When used in contact with other metals (especially in the presence of an electrolyte) it can protect the other metals from galvanic corrosion | Limitations - |
Magnesium—Benefits vs. Limitations
Magnesium—Common Applications
Magnesium has so many different uses and is commonly found in many applications, a few of which we’ve listed below.
Pyrotechnics
When burned, magnesium produces an intense bright, white light, so it’s often used in fireworks and flares. It’s an incredible way to enhance the visual effects of pyrotechnic displays.
Luggage
Magnesium’s great strength-to-weight ratio has made it a popular go-to for the manufacturing of luggage, with many high-end brands using magnesium alloys for their lightweight yet durable suitcase frames.
Sports and Recreation Equipment
You’ll often see sports equipment like tennis rackets, golf clubs, and bicycle frames made from magnesium alloys. That’s because its ability to provide durability and stiffness despite its lightweight makes it very appealing to athletes and sports companies alike.
Cameras
Cameras, especially high-end modular cameras, can get very heavy and require careful handling because of their sensitive nature. That’s why magnesium is often used in the production of camera bodies, to keep them as light as possible, while making them more durable.
Power Tools
Power tools are often made from magnesium in order to keep them light and resistant to heavy impact. Another impressive feature of magnesium is that it can actually dampen vibrations, making it ideal for use in power tools.
Car Seats
Especially important in sports cars, car seats need to be durable but not weigh the car down with unnecessary weight. That’s where magnesium comes in handy—often used by car manufacturers for the construction of seat frames.
Laptops
Depending on how you’re reading this article, you may be holding some magnesium right now. Laptop casings are often made using magnesium, especially high-end models, because of important benefits like its strength, weight, and heat dissipation properties.
How Xometry Can Help
At Xometry we are used to creating parts in a variety of materials, and magnesium is no exception. While we currently don't support auto-quoting of the material and it's alloys, we are happy to manually review any projects you have which may require it. We can produce magnesium parts through our CNC machining and die casting services. To get started, simply upload your designs to the Xometry Instant Quoting Engine®. From the list of materials, you can select "Other" and write in the specific alloy you are interested in getting a quote for.
Disclaimer
The content appearing on this webpage is for informational purposes only. Xometry makes no representation or warranty of any kind, be it expressed or implied, as to the accuracy, completeness, or validity of the information. Any performance parameters, geometric tolerances, specific design features, quality and types of materials, or processes should not be inferred to represent what will be delivered by third-party suppliers or manufacturers through Xometry’s network. Buyers seeking quotes for parts are responsible for defining the specific requirements for those parts. Please refer to our terms and conditions for more information.
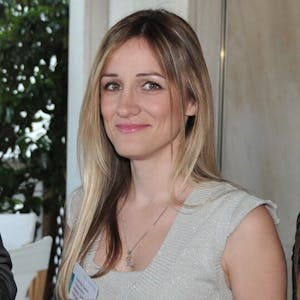