Nickel alloys, also known as high-performance alloys, are metals that contain some nickel in their elemental makeup to improve some of their properties and make them better suited for applications outside their typical wheelhouse. Let’s look at everything to do with nickel alloys, including where they’re used, the different types, and their characteristics and physical properties.
What is Nickel Alloy?
If a metal contains nickel as one of its primary elements, it’s classified as a nickel alloy. Some types of nickel alloys are even classed as “superalloys” because, if you compare them to other metals, their oxidation and creep resistance is off the charts and allows them to be used at temperatures of over half their melting points. Although not all superalloys are nickel alloys, the vast majority of them are nickel-based. Here’s an image of a nickel alloy in use:
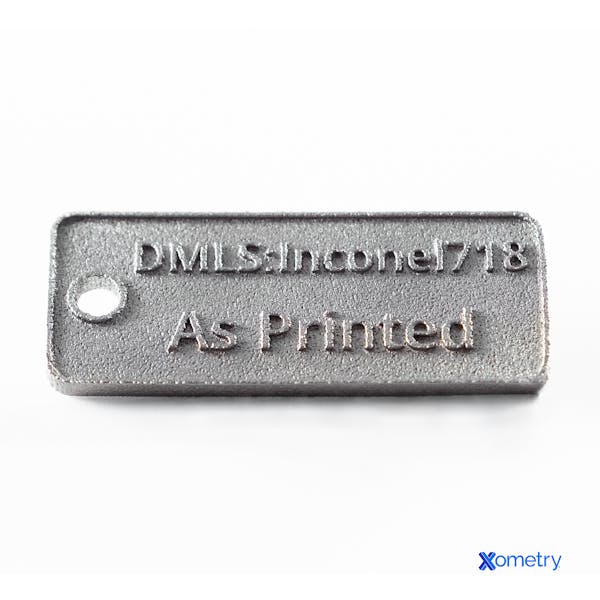
Not all metals can be mixed with nickel, but some of the most common elements are iron, chromium, aluminum, molybdenum, copper, cobalt, and titanium. To make nickel alloys, you’d have to follow the same process used for pretty much every other metal alloy. The alloying elements need to be decided on, and their ratios need to be carefully chosen. Once that’s done, the elements are all melted together in something like an arc furnace, which also purifies them, and then the alloy is cast into ingots, and off to be formed using either cold or hot processing.
A Brief History
It’s believed that the first nickel alloy was used in 200 BCE in China. That’s the earliest record available, and the material was referred to as “white copper,” which experts believe was an alloy of nickel and silver. Fast forward to 1751, A. F. Cronstedt, a German scientist, managed to isolate nickel from the niccolite mineral. Copper and zinc were often found in these first nickel alloys, which came to be known as “German silver” and weren’t really used for anything other than ornaments.
After James Riley made an iron-chromium alloy in 1913, W. H. Hatfield figured out that adding nickel to these alloys would make them incredibly corrosion-resistant. This led to the creation of what we now know as austenitic stainless steel.
Nickel Alloy Characteristics
Here are the main characteristics of nickel alloys:
- Corrosion/oxidation resistant
- High strength
- Heat resistance up to 980°C
- Highly ductile, won’t break easily if bent
- Magnetic, can easily be magnetized and demagnetized
- Weldability with various welding methods (although could develop hot or warm cracking and porosity)
- Low thermal conductivity, higher with nickel-copper alloys
- Low electrical conductivity, less than pure copper or silver
- Low thermal expansion coefficient, great for precision
- Varying colors depending on alloying element
It’s generally quite hard to differentiate nickel alloys from other types of metals. Nickel alloys can seem slightly dull when their surface is rough, but when it’s smooth, they can be shiny and reflective. Here’s an example of what copper-nickel alloy rods look like:
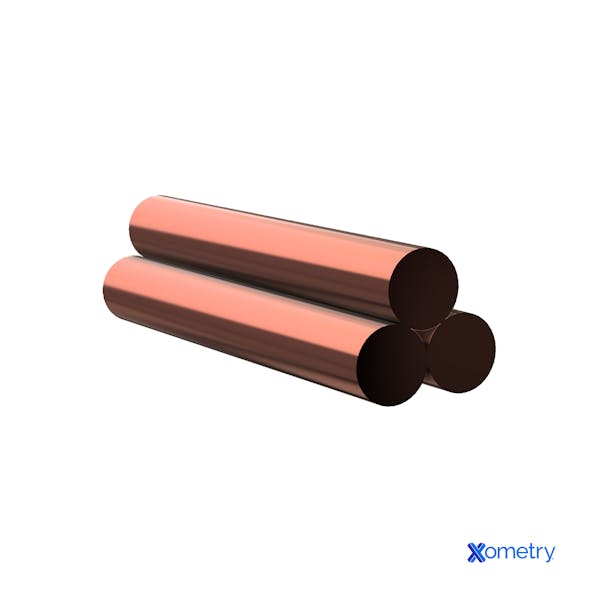
Nickel alloy type | Composition | Characteristics | Common subtypes |
---|---|---|---|
Nickel alloy type Nickel-Chromium | Composition Chromium, molybdenum, iron | Characteristics Oxidation resistance, high mechanical strength, excellent in high-temperature environments, can be hard to cold form due to its quick work-hardening | Common subtypes Inconel, 625, 718, and 600 |
Nickel alloy type Nickel-Copper | Composition Copper (55–91.5%), iron, tin, manganese | Characteristics Saltwater corrosion and fouling resistance, high strength, performs well in low-temperature environments (its ductility won’t reduce and its strength and hardness can increase), can work harden during cold forming | Common subtypes Monel 400, R-405, and K-500 |
Nickel alloy type Nickel-Molybdenum | Composition Either chromium or molybdenum | Characteristics Great thermal stability, corrosion- and oxidation-resistance at high temperatures | Common subtypes Hastelloy, C-22, and C-276 |
Nickel alloy type Nickel-Iron | Composition Iron, nickel (up to 50%), cobalt, small amounts of silicon | Characteristics High ductility, low thermal expansion, corrosion resistance, soft magnetic properties | Common subtypes Invar |
Nickel alloy type Nickel-Chromium | Composition High nickel content of around 70% | Characteristics Maintain strength in high temperatures, very good corrosion and oxidation resistance, as well as high electrical resistivity, high melting point of over 1300°C | Common subtypes Nichrome |
Nickel alloy type Nickel-Titanium | Composition Nickel, titanium | Characteristics Great corrosion resistance and mechanical strength. This is a shape memory alloy (SMA) that can be formed into a shape above a certain high temperature (the transition temperature). When it cools, the part can be deformed to a certain extent, but when heated back up to the transition temperature, it will resume its original shape. The transition temperature can be adjusted by changing the alloy’s composition | Common subtypes Nitinol |
Types of Nickel Alloys
Property | Type | Benefits | Applications |
---|---|---|---|
Property Ultimate Tensile Strength [MPa] | Type Inconel 625 | Benefits Excellent corrosion and oxidation resistance, high creep strength | Applications Turbine blades and other aerospace components |
Property Curie Temperature [°C] | Type Invar 36 | Benefits Low thermal conductivity | Applications Tooling, dies, cryogenic components |
Property Coefficient of Linear Thermal Expansion @ @ 93 °C (Annealed) (µm/µm·°C) | Type Invar 36 | Benefits High melting temperature | Applications Tooling, dies, cryogenic components |
Property Thermal Conductivity @ 93 °C (Annealed) (W/m·K) | Type Monel 400 | Benefits Excellent saltwater resistance and low-temperature strength | Applications Process vessels, process piping, pumps |
Nickel Alloy Properties
Type | Corrosion Resistance | Oxidation Resistance | Main Alloying Elements | Magnetic | Heat Resistance [Solidus] °C |
---|---|---|---|---|---|
Type Inconel 625 | Corrosion Resistance Very resistant to pitting, chloride ion stress corrosion cracking, and crevice corrosion | Oxidation Resistance Highly resistant to oxidation at elevated temperatures | Main Alloying Elements Ni - 58% / Cr - 20 to 23% / Fe - 5% / Nb,Ta - 3.15 to 4.15% | Magnetic No | Heat Resistance [Solidus] °C 1290 |
Type Hastelloy 276 | Corrosion Resistance Very resistant to pitting, chloride ion stress corrosion cracking, and crevice corrosion | Oxidation Resistance Highly resistant to oxidation at elevated temperatures | Main Alloying Elements Ni - 57% / Mo - 15 to 17% / Cr - 14.5 to 16.5% / Fe - 4 to 7% / Co - 2.5% / Mn - 1% | Magnetic No | Heat Resistance [Solidus] °C 1323 |
Type Invar 36 | Corrosion Resistance Not resistant to corrosion due to high iron content, must be nickel-plated to improve corrosion resistance | Oxidation Resistance Not really resistant to oxidation due to its iron content when compared to other nickel alloys | Main Alloying Elements Fe - 63% / Ni - 36% | Magnetic Yes | Heat Resistance [Solidus] °C 1427 |
Type Monel 400 | Corrosion Resistance Highly resistant to saltwater environments | Oxidation Resistance Some Monel grades can have good high-temperature oxidation resistance | Main Alloying Elements Ni - 63% / Cu - 28 to 34% / Fe - 2.5% / Mn - 2% | Magnetic No | Heat Resistance [Solidus] °C 1300 |
Type Nichrome 35-20 | Corrosion Resistance Not very corrosion-resistant | Oxidation Resistance Not very resistant to oxidation | Main Alloying Elements Fe - 42% / Ni - 35% / Cr - 20% / Si - 2% / Mn - 1% | Magnetic No | Heat Resistance [Solidus] °C 1390 |
Nickel Alloy Chemical Properties Table Credit: https://matweb.com/
Property | Inconel 625 | Hastelloy 276 | Invar 36 | Monel 400 | Nichrome 35-20 |
---|---|---|---|---|---|
Property Density [g/cm3] | Inconel 625 8.44 | Hastelloy 276 8.89 | Invar 36 8.05 | Monel 400 8.8 | Nichrome 35-20 7.9 |
Property Ultimate Tensile Strength [MPa] | Inconel 625 689–1103 | Hastelloy 276 601.2–826.7 | Invar 36 621 | Monel 400 450–550 | Nichrome 35-20 750 |
Property Curie Temperature [°C] | Inconel 625 -196 | Hastelloy 276 -269>26.85 | Invar 36 279 | Monel 400 20–50 | Nichrome 35-20 N/A |
Property Melting Temperature [°C] | Inconel 625 1290–1350 | Hastelloy 276 1323–1271 | Invar 36 1427 | Monel 400 1300–1350 | Nichrome 35-20 1390 |
Property Electrical Resistivity @ 93 °C (Annealed) [µΩ·cm] | Inconel 625 132 | Hastelloy 276 130 | Invar 36 82 | Monel 400 54.7 | Nichrome 35-20 104 |
Property Coefficient of Linear Thermal Expansion @ 93 °C (Annealed) (µm/µm·°C) | Inconel 625 13 | Hastelloy 276 11.2 | Invar 36 1.3 | Monel 400 13.9 | Nichrome 35-20 19 |
Property Thermal Conductivity @ 93 °C (Annealed) (W/m·K) | Inconel 625 10.8 | Hastelloy 276 11.1 | Invar 36 10.15 | Monel 400 21.8 | Nichrome 35-20 13 |
Property Specific Heat @ 93°C (Annealed) (J/kg·°C) | Inconel 625 427 | Hastelloy 276 427 | Invar 36 515 | Monel 400 427 | Nichrome 35-20 500 |
Nickel Alloys Physical Property Comparison Table Credit: https://matweb.com/
Application | Description |
---|---|
Application Aerospace | Description This is one of the most common applications for nickel alloys because of the high operating temperatures that are so common on aerospace equipment. Rocket engine parts and turbine blades are often made from Inconel. |
Application Chemical processing | Description It’s very common for this sector to require materials that are highly resistant to corrosion environments and substances. Nickel alloys are often used here for things like tanks, piping, and mixing devices. |
Application Oil & gas | Description Understandably, any materials exposed to oil and gas will need the ability to withstand high temperatures, high pressures, and corrosive environments. That’s why nickel alloys fit the bill. They’re often used to make pumps, pipes, pressure vessels, and heat exchangers. |
Application Medical | Description Alloys are suitable for medical equipment that goes through regular sterilization at high temperatures or some sort of solvent. They’re also used for orthopedic implants and stents, thanks to the SMA properties |
Application Electrical/ electronics | Description Some nickel alloys are electrically conductive and resistant to corrosion, making them great for electrical contacts in corrosive environments. Others feature low coercivity, making them perfect for soft magnetic applications like memory storage units or transformers. |
Application Marine | Description Marine environments can be extremely corrosive and not many alloys can withstand that, especially with prolonged exposure to saltwater and salt spray. Nickel alloys, especially if they’ve got lots of copper in them, are made for the job. They’re often used to make propellers, bilge pumps, and valves. |
Application Precision Instruments | Description These often need a low coefficient of thermal expansion to reduce temperature effects. An alloy with a low thermal expansion can be used alongside a metal with high thermal expansion, then joined into a bimetal strip that can be used as a temperature switch. Examples include hermetic seals found in X-ray tubes. |
Nickel Alloy Applications
Limitations
Nickel alloys are typically reserved for high-performance applications because they tend to be more expensive than other types of metal. As we’ve seen, nickel alloys are usually strong and tough, and that can make them a pain to machine. If you’re interested in machining this type of alloy, you’ll probably need extra tools.
Their high melting points can make them difficult to weld, but it’s not impossible. If you want to create a sufficient pool of weld metal, you’ll need more heat, but if you use more heat, there’s more chance of residual stress which can deform the component. Basically, it needs a lot of care. When in long-term contact with the skin, some nickel alloys can cause an allergic reaction. That’s why they’re probably not the best choice for wearables and medical devices. Also, when exposed to the elements, some nickel alloys (especially copper-based) will tarnish over time.
How Xometry Can Help
Xometry provides many manufacturers with all sorts of alloys and other metals, and relevant services. We have a wide range of manufacturing capabilities, including 3D printing, laser cutting, CNC machining, and many more. If you’d like to learn more about nickel alloys or request a free no-obligation quote, reach out to a Xometry representative today.
Copyright and Trademark Notices
- Inconel® and Monel are trademarks of INCO ALLOYS INTERNATIONAL.
- Hastelloy® is a trademark of HAYNES STELLITE COMPANY.
- Invar® is a trademark of STE. AME. DE COMMENTRY FOURCHAMBAULT ET DECAZEVILLE.
- Nitinol® is a trademark of Nitinol Devices and Components, Inc.
Disclaimer
The content appearing on this webpage is for informational purposes only. Xometry makes no representation or warranty of any kind, be it expressed or implied, as to the accuracy, completeness, or validity of the information. Any performance parameters, geometric tolerances, specific design features, quality and types of materials, or processes should not be inferred to represent what will be delivered by third-party suppliers or manufacturers through Xometry’s network. Buyers seeking quotes for parts are responsible for defining the specific requirements for those parts. Please refer to our terms and conditions for more information.
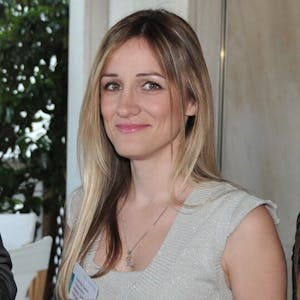