PPE-PS is a ductile material with excellent hydrolytic stability, flame resistance, and UV resistance. These properties make it ideal for applications in the process engineering, electrical, and medical industries. PPE-PS can be processed using injection molding, extrusion, blow molding, and 3D printing. It has a very high melting temperature of over 200°C and must be heated to over 300°C if processed using 3D printing.
This article will describe in detail what PPE-PS is, its key characteristics, as well as its potential adverse health effects.
What is PPE-PS?
PPE-PS is a blend of polyphenylene ether and polystyrene. PPE material is an amorphous thermoplastic with a high glass transition temperature of 215°C. Polystyrene is often used in an expanded foam state for product packaging. It is also available in clear and hard forms.
PPE on its own is not often used due to difficulties in processing as it has poor molten flowability. As such, it is often blended with polystyrene to improve processability. PPE can be blended with any proportion of PS. The glass transition temperature tends to decrease with higher proportions of polystyrene. Other additives like glass fiber can also be added to further improve mechanical properties.
Processing techniques for PPE-PS include: injection molding, blow molding, extrusion, and 3D printing. The image below shows a smoke detector casing made from PPE-PS:
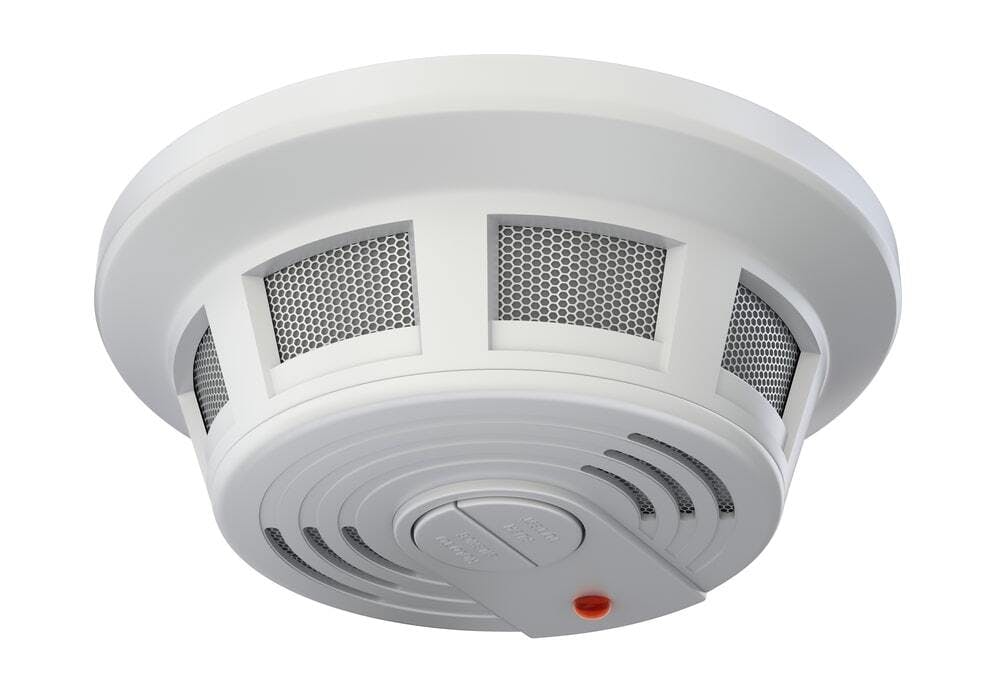
Smoke detector on a white background.
Image Credit: mipan/Shutterstock.com
What is the Filament Specification of PPE-PS?
Thermax PPE-PS from 3DXtech is a plastic filament typically used in FDM (Fused Deposition Modeling) 3D printers. Parts printed with Thermax tend to have better properties when compared to ABS and PC. Thermax PPE-PS prints at very high temperatures, and care must be taken when printing with it. Extruder temperatures of between 290 and 320°C are required and bed temperatures must be between 90 and 110°C. To prevent excessive warping, heated chambers at 50 to 80°C are also recommended. The filament is available in both 1.75 and 2.85 mm. Despite having low moisture absorption properties, PPE-PS filaments can still absorb moisture. It must be dried at 80°C for 4 hours before printing for best results.
Property | Value |
---|---|
Property Density [g/cm3] | Value 1.07 |
Property Glass Transition Temperature [C] | Value 215 |
Property Melting Point [C] | Value 200 |
Property Tensile Strength [MPa] | Value 72 |
Property Modulus of Elasticity [GPa] | Value 2.2 |
Property Flexural Strength [MPa] | Value 109 |
Property Flexural Modulus [GPa] | Value 2.54 |
Property Impact Strength [kJ/m2] | Value 6 |
Table 1: Key Physical Properties of PPE-PS
What Are the Uses of PPE-PS?
PPE-PS is typically used in applications that leverage its high-temperature resistance, hydrolytic stability, and flame resistance. Listed below are some common uses of PPE-PS:
- Consumer electronics: Components like printers, copiers, modems, smoke detectors, and speaker housings make effective use of PPE-PS due to its high impact strength and temperature resistance.
- Process engineering equipment: Components in pumps, valves, water meters, hot water tanks, and water softeners leverage the hydrolytic stability at elevated temperatures of PPE-PS.
- Electrical equipment: Instrument panels, bulb sockets, capacitor casings, smoke detectors, and cable connectors make use of the high-temperature resistance of PPE-PS.
- Medical equipment: PPE-PS is easily sterilized due to its high-temperature resistance and as such can be used for reusable medical devices.
What Are the Advantages of PPE-PS?
PPE-PS is a tough and ductile amorphous material with exceptional impact resistance, low shrinkage, and low creep at elevated temperatures. PPE-PS has good hydrolytic stability, especially at elevated temperatures. It has good chemical resistance to a wide array of acids, bases, and other aqueous chemical solutions. PPE-PS is not degraded by UV radiation (rated F1 as per UL 746C). It has a flame retardant rating of UL94 V-0. PPE-PS can also produce parts with excellent surface finishes and can be readily painted.
What Are the Disadvantages of PPE-PS?
PPE-PS can experience environmental stress cracking when exposed to some mineral oils and ketones. It also tends to swell or dissolve when exposed to some organic solvents like aromatic or aliphatic hydrocarbons. PPE-PS requires higher than typical processing temperatures. It can provide some challenges to processing, especially with 3D printing which requires heated enclosures, high extruder temperatures, and high bed temperatures.
How Does PPE-PS Affect Human Health?
PPE-PS has no major negative effects on human health. Some additives and pigments, however, like carbon black may be carcinogenic. These pigments and additives are bonded to the plastic matrix and do not readily present an exposure risk to persons exposed to these elements under normal melt-processing conditions. PPE-PS particles can cause mechanical irritation if they come into contact with the eyes or other sensitive areas.
Is PPE-PS Toxic?
PPE-PS is not shown to be toxic if ingested and repeated skin contact has no adverse effects. Processing fumes can irritate the respiratory tract, and severe exposure to processing fumes can cause nausea and headaches. Over time, a grease-like film can collect on molding equipment and ventilation ducting which can irritate the skin.
When combusted, PPE-PS produces thick toxic fumes that contain carbon dioxide, carbon monoxide, and hydrocarbon fragments. However, combustion is not encountered during normal processing conditions and requires continuous exposure to a direct flame to ignite.
Is PPE-PS (Polyphenylene Ether + Polystyrene) a Good Plastic Injection Molding Material?
PPE-PS is widely used for injection molding and produces parts with excellent surface finishes. It also has very low mold shrinkage rates, meaning parts will have excellent dimensional consistency. PPE alone has very poor mold flowability and as such, it is not ideal for injection molding. With the addition of PS, the PPE+PS blend becomes much easier to process for injection molded components.
For more information on Plastic Injection Molding, see our full Plastic Injection Molding Guide and The Most Common Plastic Injection Molding Materials Guide.
To learn more about how PPE-PS can be utilized in your specific application, contact a Xometry representative or make use of Xometry's powerful quoting tool.
Summary
This article provided a summary of the properties, uses, advantages, limitations, and toxicity of PPE-PS. For assistance with material selection, contact Xometry to connect with our materials experts or request a quote.
Disclaimer
The content appearing on this webpage is for informational purposes only. Xometry makes no representation or warranty of any kind, be it expressed or implied, as to the accuracy, completeness, or validity of the information. Any performance parameters, geometric tolerances, specific design features, quality and types of materials, or processes should not be inferred to represent what will be delivered by third-party suppliers or manufacturers through Xometry’s network. Buyers seeking quotes for parts are responsible for defining the specific requirements for those parts. Please refer to our terms and conditions for more information.
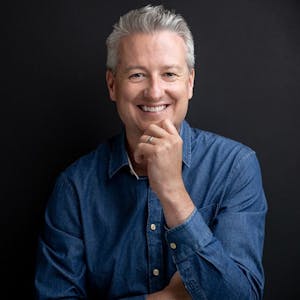