Introduction to Injection Molding Tolerances and How to Optimize Them
Correctly specifying injection molding tolerances is critical to ensuring that the final parts will fit together during assembly. This article will describe how to control injection molding tolerances and ensure high quality through design for manufacturing principles, material selection, tool design, and process control.
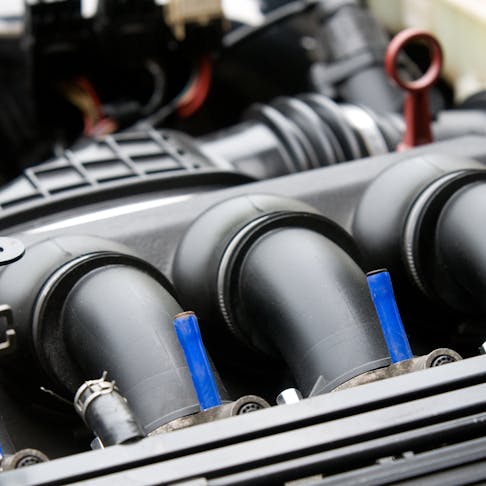
The vast majority of plastic products are manufactured using injection molding. This is primarily due to the process’s high production rates and very low unit cost. As with any manufactured assembly, the tolerances are of critical importance. If they are incorrectly specified or controlled, the final parts will not fit together during assembly. These types of errors are especially problematic since the upfront cost of the mold is so significant. This article will describe how to control injection molding tolerances and ensure high quality through DFM (design for manufacturing) principles, material selection, tool design, and process control.
Why is Tolerancing so Critical?
Even though it may be minimal, there is always variation when manufacturing parts. As such, it is important to define an acceptable range of deviations from the nominal size that still allows the part to function as expected. This becomes all the more important when multiple parts are being assembled.
If, for example, two flat parts need to be bolted together, the locational tolerance of the holes on each part must allow for the full range of possibilities. Even if one part is at its minimum tolerance and the other is at its maximum, they must still fit during assembly. This seems relatively simple in this case, but when multiple parts need to be assembled one part can cause the entire assembly to be non-functional. Tolerance analyses like the worst-case method, tolerance stack, and statistical analysis can be used to optimize injection molding tolerances of multi-part assemblies.
Factors Affecting Injection Molding Tolerances
1. Part Design
One of the most important methods of limiting warping, excessive shrinking, and part misalignment is to use DFM principles when designing a part. That’s best achieved by engaging with an injection molding service early on in the design process to prevent costly redesigns later in the design phase.
- Wall Thickness - Uneven shrink rates can occur in parts with variable wall thicknesses. When thick areas are unavoidable, coring must be utilized to maintain an even wall thickness. Uneven wall thickness can cause part deformation that will interfere with tolerances and fit-up. Thicker walls are not always the best option for increasing strength; where possible it’s better to use ribs and gussets to improve part strength.
- Draft Angles - Draft angles are critical to ensure easy ejection from the tool. If done sub-optimally the part can get stuck during ejection, scraping and warping the finished product. Draft angles can vary from 0.5° to 3° depending on the part design and surface finish.
- Boss Features - Bosses are generally used to accommodate fasteners when multiple plastic parts are assembled. If bosses are made too thick they can create sink marks on the part. If they are not connected to side walls via ribs they can distort significantly. This will make assembly of these parts near impossible.
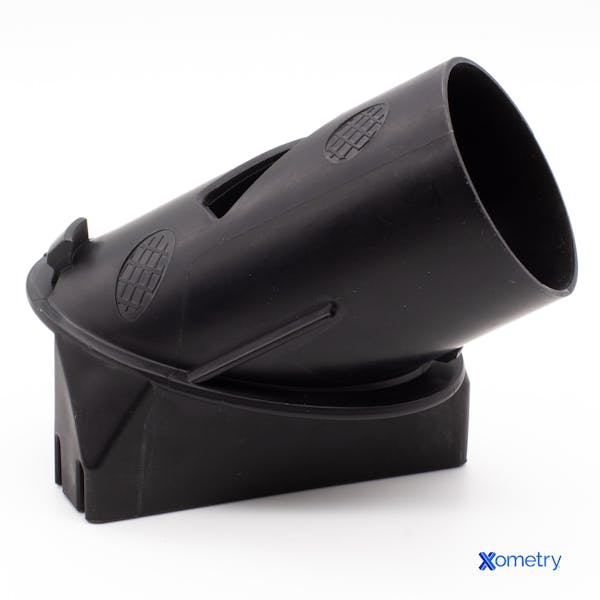
2. Material Selection
Injection-molded plastics can be manufactured from a wide range of resins. The selection of these materials is driven primarily by the application of the final product. Each resin has a different shrink rate.
This shrinkage needs to be taken into account when designing the molding tool and is normally done by oversizing the tool dimensions by the percentage shrinkage of the material. If multi-material assemblies are required, the different shrinkage rates need to be designed for. Not designing in appropriate tolerances can result in parts that do not fit together, which is a costly mistake when it comes to injection molding.
Injection molding tolerances are driven primarily by the shrinkage of the material and the part geometry. Before the tool can be designed and manufactured, the material selection needs to be finalized. Tool design is highly dependent on the chosen material(s).
3. Tool Design
Once the material is selected, the tool is often oversized to account for the relevant material shrinkage. However, shrinkage is not consistent in all dimensions. Thicker parts have a different cooling rate than thinner parts, for example. As such, a complex part that has a mixture of thin and thick walls will have variable cooling rates. The resultant warping or sink can severely affect injection molding tolerances and assembly fit-ups. To limit these effects, toolmakers take into consideration the following factors when designing mold features.
- Tool Cooling - Controlling cooling is critical to maintaining even shrinkage rates. Poor tool cooling will result in uncontrolled shrinkage, creating parts that deviate drastically from their tolerance requirements. Intelligent placement of cooling channels can significantly improve part consistency.
- Tool Tolerances - Out of tolerance tooling will result in all subsequent injection molded parts having this inaccuracy added to any inaccuracies caused by shrinkage. However, tool tolerances are often tightly controlled and monitored during CNC machining and therefore out of tolerance tools are rarely the cause of out-of-tolerance parts. In addition, these tools are often made “steel-safe.” This refers to manufacturing the tool in a way where critical dimensions or features can be adjusted through extra milling. The additional material allows for fine-tuning of the tool by machining it out if some of the parts’ finished dimensions are not within tolerance. For example, a tightly toleranced hole feature on a part may have a tool designed with the core pin at the wider side of the tolerance. If the hole needs to be adjusted, it would be machined thinner, making the hole thinner.
- Ejector Pin Location - Ejector pins push the molded part out of the tool as it opens; this needs to happen as quickly as possible to minimize cycle time. If ejector pins are placed in suboptimal positions, they can damage the part. Some materials are not completely rigid as they leave the tool and uneven ejection can cause significant warping and dimensional inconsistency.
- Gate Location - The gate is the part of the tool into which the resin flows. If placed in non-ideal positions, this will create poor cosmetic finishes. In addition to this, uneven fill rates can also result in warping and erratic shrinkage. Complex parts often require multiple gates to achieve even fill and mitigate these challenges.
4. Process Control
Despite all the upfront design work and material considerations to optimize your part’s injection molding tolerances, there is still the possibility that the part will be out of tolerance when the first samples, often called T1 shots, are delivered. Once all of the above methods are incorporated, the next step to improving tolerance compliance is to tweak the process. Controlling the temperature, pressure, and holding time are some of the most common ways of increasing part quality. Once the ideal set of conditions are determined, the mold can create consistent parts with very little dimensional variability between parts.
In complex, multi-feature parts, it may be beneficial to embed pressure and temperature sensors into the tool in order to measure these parameters during manufacturing to allow for real-time feedback and process control. Consistently maintaining pressure and temperature in the tool can go a long way toward ensuring consistent tolerances.
FREE Injection Molding Design Guide
Getting Started With Injection Molding
Injection molding is an incredibly versatile manufacturing process for making consistent and durable plastic parts. But with this versatility comes considerable complexity. To ensure that your investment into the tooling is as risk-free as possible, contact a Xometry representative to discuss how best to design your parts to ensure successful products. The Xometry team is happy to provide design for manufacturability feedback and suggestions before the project gets underway. Proper planning for injection molding tolerances can prevent cost overruns and vastly improve product quality.
