Brass is a gold-colored, shiny metal used for a wide range of applications from decoration and nameplates to plumbing fixtures. Brass is an alloy of copper and zinc, in which the proportions of the two metals (and other minor alloying elements) can vary to produce different mechanical and chemical properties. Copper is usually the main element in the alloy.
Brass can be laser cut for decorative purposes, and brass nameplates are frequently engraved on trophies and awards. Its popularity in these applications is due to its shiny gold finish. Due to its high percentage of copper, brass is a reflective metal which can make it difficult to laser cut. This article will discuss the definition of brass laser cutting and engraving, the type of laser cutting used, and the key elements of successful brass laser cutting.
What Is the Definition of Brass Laser Cutting?
Brass laser cutting utilizes a laser with enough energy to melt brass. An assist gas is used to blow out and remove the molten metal as well as maintain the clean cut.
CO2 lasers cannot typically be used to cut metals like brass, as they have high reflectivity and therefore absorb very little of the energy within the 10.6 μm wavelength beam. Fiber lasers work very well as an alternative to CO2 lasers. At the shorter wavelength, the metal reflectivity is a little lower, and fiber lasers typically have a higher power output. This allows a significant transfer of energy to the brass, and the resultant heat causes localized melting.
What Is Brass Laser Engraving?
Brass laser engraving is the process of removing the upper surface of a brass sheet to create a clearly defined pattern using a fiber laser. Fiber lasers can engrave metals due to their shorter wavelength being better absorbed by the material and also due to their higher power output.
While CO2 lasers are unable to engrave brass due to their high reflectivity at 10.6 μm wavelength, they can be used to mark brass. Marking of metals is different from engraving as it does not remove any material from the surface of the metal, but only creates a mark on top of the surface of the metal in combination with a marking compound. This marking solution is applied to the surface of the metal. The heat of the CO2 laser causes the solution to react and bond with the brass surface. This leaves a permanent dark mark.
What Issues Most Frequently Arise When Brass Is Laser Cut?
Laser cutting brass can be difficult to do, as there are a number of issues that arise when laser cutting brass, such as the following:
- Brass Is Highly Reflective: The primary issue when laser cutting brass is that it is highly reflective of infrared laser light (together with other metals such as gold, silver, and copper). This high reflectivity is worse at the longer wavelength of a CO2 laser compared to the wavelength of a fiber laser. The reflection of the laser beam can cause hazards for both the laser optics and the people and equipment around the laser cutter. If the laser light reflects back to the laser source, causing it to heat up past its design temperature, the laser source may be permanently damaged, necessitating an expensive replacement.
- Brass Absorbs Very Little Laser Energy: The high reflectivity of brass means that very little of the laser energy that falls on the brass surface is absorbed, as most are reflected. Since most energy is not absorbed by the metal, it is very difficult to cut it.
- Brass Must Be Molten To Lower the Reflectivity: Brass has a very high reflectivity when it is in a solid state. Once the material is molten, its reflectivity drops substantially, allowing a higher absorption of laser energy. The key to successfully laser cutting brass is therefore to pierce the material quickly—once that has been accomplished, the laser will then fall on molten metal and be more readily absorbed. For example, at the wavelength of a fiber laser (approximately of the order 1.06 μm), copper has a reflectivity of 95% in its solid state, but this drops to 84% when molten.
- Brass Is Hard To Cut in its Solid State: There is some risk to the machine of laser energy reflecting back to the source when starting the cut on solid brass. It is important to try to limit the length of time that the laser is exposed to the solid metal before it begins to melt.
Which Type of Laser Cutting Is Employed When Cutting Brass?
A fiber laser is a better method to cut brass because of its higher power output and shorter wavelength compared to CO2 lasers. Brass (and other reflective “yellow” metals) are difficult to laser cut because they reflect most of the laser energy and absorb very little. A fiber laser’s shorter wavelength at 1.06 μm is better absorbed for most materials. Additionally, fiber lasers can melt brass much more quickly than other lasers because of their greater energy output. Brass reflectivity drops significantly in the molten state, so the quicker that enough energy is absorbed to start melting the material, the sooner the laser is effective at cutting.
Check out our Brass Laser Cutting Service for parts.
What Are the Key Elements in Laser Cutting Brass Successfully?
There are four key elements to laser cutting brass successfully:
- The Right Power Setting: Use a high power setting, preferably the maximum that your machine can provide. For example, 1000 W should be used for a 0.04-inch sheet of copper. For a thicker sheet of 0.25 inches, a power of at least 4000 W is required. High power reduces the time for the material to become molten, therefore minimizing the time that it is at its highest reflectivity.
- Cutting Speed: Cut at a slightly lower speed. Set the cutting speed at approximately 10–15% less than the maximum rate that can be managed on the sheet. It is important to not let the cut extinguish, as that will require the material to be pierced again.
- Point of Focus: Keep the point of focus as close to the top surface of the material as possible, while still achieving an acceptable quality of cut. The reason is that the laser energy is focused over a small surface area, causing a higher power density and reducing the time needed for the material to melt.
- High-pressure Cutting Gas: Nitrogen can be used to cut brass, whereas oxygen may be needed for other reflective metals such as copper. When using nitrogen for brass, the gas acts purely to remove the molten metal mechanically. For materials like copper, the oxygen reacts with the surface at the cut in order to form a copper oxide, which reduces the reflectivity of the metal.
Common FAQs on Brass Laser Cutting
Does Higher Laser Power Result in Faster Cutting of Brass?
Yes, using a higher laser power does result in faster cutting of brass. Brass as a solid has a high reflectivity, but the reflectivity decreases significantly when it is molten. Therefore, to cut brass well, the key is to melt it as quickly as possible to reduce the length of time in the high-reflectivity state. A higher laser power reduces this time by transferring more energy to the brass within a shorter amount of time.
Does Slower Speed Make Brass Cutting Easier?
Yes, using a slower laser speed makes brass cutting easier. Although brass is a reflective material, its reflectivity drops substantially when molten. So long as a cut can be sustained after piercing, brass can be laser cut easily. Therefore it is important to minimize the chance that the laser will move over insufficiently heated (unmelted) brass, as doing so may extinguish the cut. To ensure that the cut is sustained, it is easier to reduce the laser speed to about 10–15% less than the maximum that can maintain the cut.
Does Employing Nitrogen To Cut Brass Work Well?
Yes, employing nitrogen gas to cut brass works well. Nitrogen does not react chemically with the molten material, but only mechanically removes the molten metal to prevent it from fusing again behind the path of the laser. Nitrogen works well, rather than needing to use oxygen to react with brass since the reflectivity of the molten brass material is low enough that the laser can continue to cut. No chemical influence by the cutting gas is required.
Summary
This article presented brass laser cutting, explained what it is, and discussed the manufacturing process in detail. To learn more about brass laser cutting, contact a Xometry representative.
Xometry provides a wide range of manufacturing capabilities, including sheet cutting and other value-added services for all of your prototyping and production needs. Visit our website to learn more or to request a free, no-obligation quote.
Disclaimer
The content appearing on this webpage is for informational purposes only. Xometry makes no representation or warranty of any kind, be it expressed or implied, as to the accuracy, completeness, or validity of the information. Any performance parameters, geometric tolerances, specific design features, quality and types of materials, or processes should not be inferred to represent what will be delivered by third-party suppliers or manufacturers through Xometry’s network. Buyers seeking quotes for parts are responsible for defining the specific requirements for those parts. Please refer to our terms and conditions for more information.
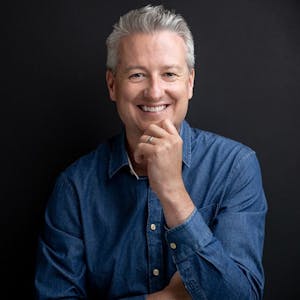