Most cutting lasers fall into either the CO2 or fiber laser categories. Each technique has strengths and weaknesses that must be evaluated when selecting equipment for any particular task. Fiber lasers can cut almost all materials and do so 3 to 5 times quicker than other styles. However, they work best on sheet materials 5 mm or thinner. In the transition range from 5 to 20 mm thickness, the advantages of fiber lasers are less marked and the capabilities of CO2 lasers can be beneficial. Above 20 mm, fiber lasers rapidly lose their value. Materials like steel with thicknesses of up to 100 mm typically need oxygen-assisted CO2 lasers. This article seeks to explain the differences between CO2 lasers vs. fiber lasers that are important to know when specifying services or purchasing equipment.
What is a CO2 Laser?
A CO2 laser exploits the electrically induced vibration of carbon dioxide molecules to trigger the rapid emission of photons. It works by applying an electric field either along or across a gas-filled tube containing 10-20% each of N2 and CO2 along with trace hydrogen and xenon. The remainder of the tube is filled with helium. The electric field causes the N2 molecules to vibrate. Nitrogen, being homonuclear, cannot lose energy by photon emission, so the vibration of N2 molecules increases rapidly. N2 and CO2 have very similar natural vibration frequencies, so the energy is transferred to the CO2 by sympathetic oscillation. They then impact helium atoms, altering their vibrational mode and heating the helium. Vibrational mode transition releases a photon, so it generates light. CO2 has three vibrational modes, giving it two potential transitions. CO2 lasers can thus emit two primary frequencies of laser light (if they are built to allow for both). The ends of the tube are capped with Brewster mirrors: one half-silvered and the other fully silvered. The light passage out from the half-silver mirror is collimated and can be reflected and refracted to direct and shape the beam.
CO2 lasers put out infrared energy. It’s a relatively low-frequency electromagnetic wave but has better effective power than many other wavelengths. Thus, these lasers have some significant advantages:
- Despite complex physics, their construction is simple.
- Can be tuned for milliwatt to high kilowatt power outputs.
- Cheap to manufacture.
- The constant beam has a continuous peak output power.
- Power can be increased simply by using a longer tube.
- Can be Q tuned by rotating mirror elements, increasing pulse power.
Some variants, like RF gas flow CO2 slab lasers, are improvements on the basic type. These enhancements improve output, product life, and efficiency.
For more information, see our guide on CO2 Laser.
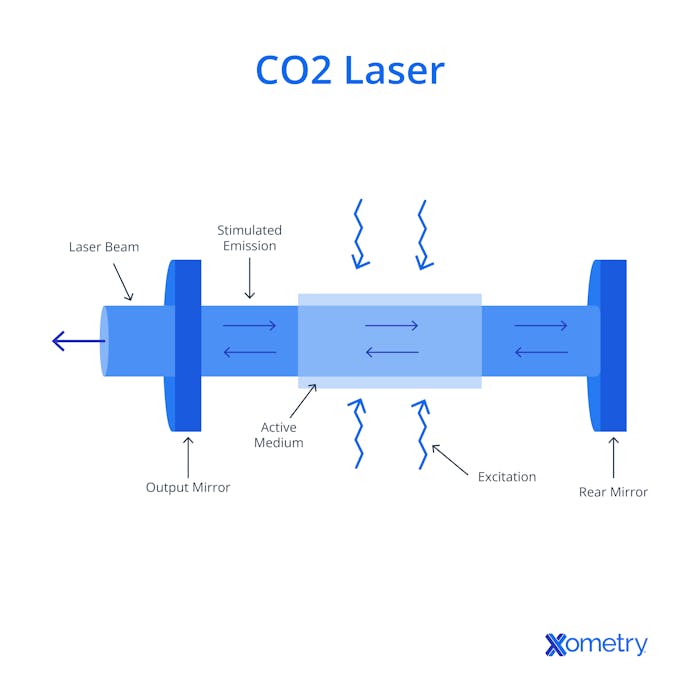
What is a Fiber Laser?
Fiber lasers are monolithic in construction and built around a specialized optical fiber. Light is introduced into the optical fiber generator, usually from a small solid-state laser, and the optical fiber doping acts as an amplifier. A fiber laser consists of a series of devices that function in sequence to create laser light. It works with a pump source (laser diode) that emits light captured by a ‘reflective’ clad fiber optic guide that retains virtually all of the pump source light. Light leaves the guide and enters the laser cavity. The pump source light hits rare-earth dopants inside that cavity. This process generates more light through a cyclic process of electron excitation and relaxation. The dopant element has a specific frequency of emission, which defines the frequency of the resulting laser light.
Ytterbium dopant emits at 1064 nm and is the type generally used in laser cutting. The internally emitted light hits a series of fiber-Bragg gratings which act as internal reflectors, keeping the light within the laser cavity. The second type of fiber Bragg grating acts as a ‘gate.’ It allows a portion of the light to pass while reflecting most back into the cavity. Laser light leaves the cavity through another fiber guide, by now highly collimated (i.e. very parallel). The beam then passes through a short-focal-length lens and is concentrated to the shape and diameter required for a cutting application.
As a specialist group of solid-state lasers, fiber devices offer significant benefits over other technologies, including:
- Maintenance-free operation for prolonged periods.
- Easy to integrate into equipment.
- Very reliable and stable when in use.
- Can produce very high beam quality with low noise and minimal low-frequency flicker.
- Compact and portable.
- Lower cost of ownership than other systems of equivalent power.
- Can handle challenging environmental conditions like temperature variations.
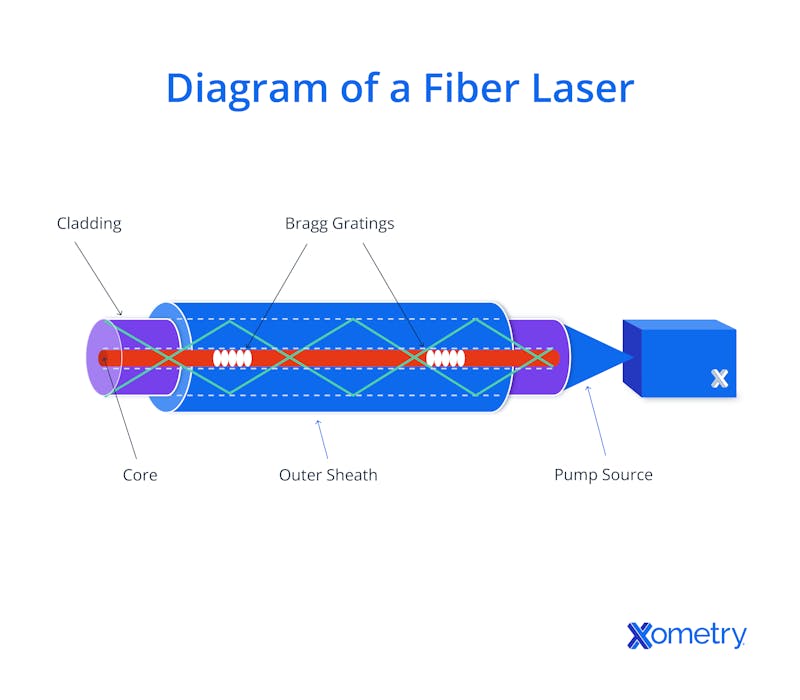
Differences Between a CO2 and a Fiber Laser
CO2 lasers consume considerably more power than fiber lasers for the same energy output, so their operational power costs are much higher. The up-front cost of CO2 lasers is also considerably lower than that of equivalent fiber lasers. The most expensive fiber laser-equipped cutting machines will commonly be 5 to 10 times the price of their CO2 equivalent. Fiber lasers provide higher cut precision than CO2. They have 10 times the working life of CO2 devices, often reported as 25,000 working hours. Refurbishing services for fiber devices are also easy to access.
Differences in Materials Each Can Cut
CO2 lasers are well suited to cutting many nonmetallic materials and nonferrous metals. Examples are acrylic, melamine, mother of pearl, paper, mylar, plastic, rubber, non-resin wood, Delrin® (POM), cloth, Corian®, cork, fabric, fiberglass, leather, dense card, and plywood.
Fiber lasers, on the other hand, are less specific in material applications and will work with most materials, although they’re best suited to cuts of 20 mm or less. Examples of materials are metals (including highly reflective types such as stainless steel), glass, acrylic (PMMA), POM, paper, dense card, and most foams.
Power and Wavelength Differences
CO2 lasers can be made in powers ranging from a few dozen watts up to around 100 kW. High-powered devices produce poor-quality beams unless they are very long. Because of their very low efficiency (5-10%), larger devices need considerable cooling capacity, increasing size even further.
Low-power ytterbium-doped fiber lasers fall in the same ranges as CO2 ones, but the type’s upper power limit approaches 1 MW (for very large, very expensive devices). High operational efficiency (often above 90%) results in a limited need for cooling, especially in smaller devices.
The difference in wavelength between a CO2 laser and a fiber laser is around a factor of 10. CO2 lasers produce light at 10.6 µm (or 9.6 µm for some types), whereas ytterbium-doped fiber lasers emit at 1064 nm (or 1.064 µm).
Cost Differences
In terms of up-front cost, fiber lasers are more expensive per watt of power than CO2 devices. However, they typically have up to 10 times the functional life expectancy of CO2 devices, so they’re usually the better long-term option.
In terms of operational power use, CO2 lasers are around 5 to 10% efficient — meaning they draw 10 to 20 times as much electricity as they emit in the form of laser light. This compares very poorly with fiber lasers, which generally offer over 90% efficiency (i.e. only 10% of their power fails to get converted into laser light.
Industry Usage Differences
CO2 lasers can cut most materials and find applications in all industries, including medical, military, communications, and other manufacturing industries. In particular, they are the best option for the processing of thicker (10-20 mm or more) metal plates. Operators often add oxygen assist to speed up the cutting of a 100 mm steel plate.
Fiber lasers are more prevalent in high-precision and high-value market sectors such as telecommunications, medical, material processing, automotive, and electronics. Fiber laser cutting machines can cut most materials but function best with difficult-to-cut and reflective metals like titanium, brass, and aluminum.
Xometry provides a wide range of manufacturing capabilities including CNC machining, 3D printing, injection molding, laser cutting, and sheet metal fabrication. Get your instant quote today.
Disclaimer
The content appearing on this webpage is for informational purposes only. Xometry makes no representation or warranty of any kind, be it expressed or implied, as to the accuracy, completeness, or validity of the information. Any performance parameters, geometric tolerances, specific design features, quality and types of materials, or processes should not be inferred to represent what will be delivered by third-party suppliers or manufacturers through Xometry’s network. Buyers seeking quotes for parts are responsible for defining the specific requirements for those parts. Please refer to our terms and conditions for more information.
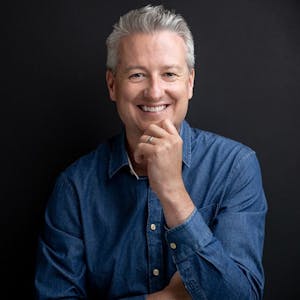