With its ability to make parts with elaborate designs, laser cutting has quickly become one of the most common manufacturing methods used today by both hobbyists and industrial professionals. It’s versatile and can cut, engrave, and etch lots of different materials, including organic leather, wood, paper, non-organic metals, plastics, and… copper!
The way a material reflects light and its melting and boiling points play a huge role in how well it can be laser cut. If a material reflects a lot of the laser’s energy, it can be a pain to cut. Also, the amount of time it takes for a material to melt or turn to vapor ultimately dictates how hot the laser needs to get. A highly reflective material can also damage the laser optics equipment.
Copper and its alloys are notorious for being really difficult to cut because of how much light they reflect, especially infrared radiation (over 95%!) when in a solid state. It makes the process unstable and hard to control—but it’s not impossible! You just need the know-how. We got our in-house experts on the case and picked their brains for the best tips and tricks for successfully laser-cutting copper.
Copper Laser Cutting Overview
When cutting a copper sheet or workpiece using a laser cutter, you’ll ideally want to use one with a fiber laser because copper can easily absorb the blue, violet, and ultraviolet wavelengths from these. Below, you can see an example of copper that’s been laser-cut.
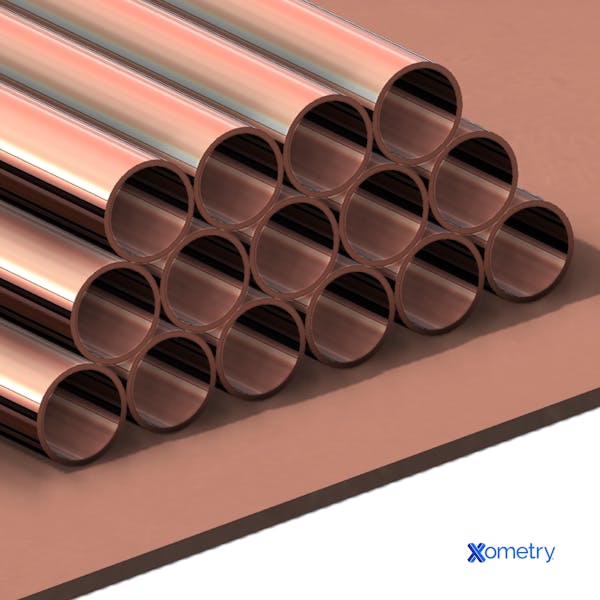
There are three main types of laser cutting—fusion, flame, and sublimation (vaporization)—but only flame cutting can be used on copper. Flame cutting uses oxygen, which creates a chemical exothermic reaction that releases energy to its surroundings. It heats up the workpiece and forms a copper oxide. The magic is all in this oxide; it makes the material’s surface much less reflective and helps it better absorb energy. Since flame cutting is likely to leave some burrs behind, you’ll need to do some post-processing work if your piece needs to be pretty.
Best Practices
The challenges associated with laser cutting copper all pretty much boil down to its inability to absorb enough laser energy. That said, if you carefully optimize your laser power settings, you can work around it.
Laser power: For smooth and efficient cutting on copper, set the machine to maximum power throughout the whole process. This will reduce the amount of time the copper is most reflective. The table below provides a rough guide to the most suitable laser power for a range of copper thicknesses:
Material Thickness | Power |
---|---|
Material Thickness 0.04-0.06” (1–1.5 mm) | Power 1000W |
Material Thickness 0.08” (2 mm) | Power 1500W |
Material Thickness 0.12” (3 mm) | Power 2000W |
Material Thickness 0.16” (4 mm) | Power 3000W |
Material Thickness 0.25” (6 mm) | Power 4000W |
Copper Thicknesses for Laser Cutting
Cut speed: Keep this at 85–90% of the maximum speed allowed. That will keep the copper heated and not highly reflective, which should allow you to keep cutting without any interruptions. If you do make some cuts that are unsuccessful at first, you can reduce the cutting speed a little.
Point of focus: This can be adjusted using different optical lenses and changing the distance between the lens and the worktable. Keep the focal point on the surface of the workpiece, or as close as possible, to maximize the energy density of the laser at the surface of the workpiece. This will ultimately melt it faster.
High-pressure oxygen gas: Although we’ve saved this for last, it’s actually a high-priority point because this is what will make that reflectivity-reducing copper oxide we mentioned. Aim for 100–300 psi, depending on the thickness of your material.
FAQs on Copper Laser Cutting
Can you laser-cut copper with a low-powered laser?
You can, but a high-powered laser can better provide the energy needed to cut through copper, leading to better results. For a low-powered laser, you’ll need to keep the cutting speed low and carefully adjust settings like focus and pulse frequency.
Can you laser-cut copper with a CO2 laser?
Yes, but it’s harder to do than with a fiber laser because the copper will reflect the laser’s red and infrared wavelengths. But there is a workaround; you can coat the copper with a metal marking spray or paste, which will allow it to absorb the CO2 energy. It won't provide the same high-quality cut, or work as well as a fiber laser, but should be fine for small-scale or hobby projects.
Copper laser cutting vs. laser engraving–what's the difference?
Laser cutting is able to cut right through a material, whereas laser engraving just makes marks on the surface. The first can basically chop a workpiece into two or more pieces, while engraving is used to change the external appearance of the copper with logos, identification marks, designs, patterns, or other decorative details.
How is flame cutting different from fusion and sublimation cutting?
Fusion cutting uses an inert gas like nitrogen to force molten material from the slit or kerf, and sublimation cutting works by heating up the material so quickly that it doesn’t have much time to melt, so it’s directly vaporized. With this type of cutting, a shield gas is used to help prevent the edges of the workpiece from oxidizing. Flame cutting, as we’ve covered, uses oxygen.
How Xometry Can Help
Producing copper parts is more than possible at Xometry, and we have a long list of manufacturing services you can get quotes for depending on your needs, including copper CNC machining, copper sheet metal fabrication, and other related customized services. You can get an instant quote on these processes, as well as many others, easily on our website.
Disclaimer
The content appearing on this webpage is for informational purposes only. Xometry makes no representation or warranty of any kind, be it expressed or implied, as to the accuracy, completeness, or validity of the information. Any performance parameters, geometric tolerances, specific design features, quality and types of materials, or processes should not be inferred to represent what will be delivered by third-party suppliers or manufacturers through Xometry’s network. Buyers seeking quotes for parts are responsible for defining the specific requirements for those parts. Please refer to our terms and conditions for more information.
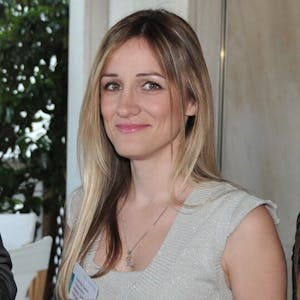