Laser welding is used in many industries because it’s accurate and quick and can be used for many projects. At Xometry, our manufacturing partners may use this technique when welding sheet metal components and assemblies. The laser welding manufacturing process works with a highly concentrated light beam that melts and fuses materials together to create a strong bond.
This method does carry some disadvantages, which we will discuss in this article.
Laser Welding Disadvantages
Specifically, we will go over six disadvantages of laser welding and identify any potential difficulties when dealing with this type of welding.
High Cost
First off is the price. Laser welding equipment is notoriously expensive and costs more than other types of welding equipment. This is because it has advanced components like modern optics, control systems, and necessary safety features. Plus, you’ll have to factor in repair and maintenance costs.
Limited Penetration Depth
While laser welding is great for joining thinner materials, it struggles with thicker ones—the deeper the laser penetrates a material, the weaker it gets, so you may find your laser welding machine grappling when faced with a thick material. If you are set on laser welding thick materials, electron beam welding, which uses electron beams that are powerful enough to penetrate thicker materials, should be able to complete the weld in a single pass.
Sensitivity to Materials
Laser welding can’t be used with as wide a range of materials as other types of welders. A laser welder could struggle with materials that are reflective and have high thermal conductivity (i.e., aluminum or copper alloys). Laser welders don’t really like reflective surfaces because, during welding, a lot of the energy is reflected off the surface before it’s absorbed, and whatever is absorbed disperses quickly. This makes it hard for the laser beam to properly heat the surface and create a strong enough weld.
When laser welding materials like high-carbon steel and aluminum alloys, the process’s rapid temperature change could cause them to crack, distort, and even change their material properties.
Safety
Laser welding can be a dangerous endeavor without sticking to all the safety precautions and careful and proper operation. If your skin comes in contact with the beam, it could cause serious injury and burns. If you forget to wear protective eye goggles, eye trauma is a real possibility, and if you don’t work in a well-ventilated area, the gasses, vaporized particles, and fumes emitted from laser welding equipment could cause respiratory problems, among others.
To avoid injuries and health problems, make sure you have stocked up on (and wear) the appropriate safety gear, like goggles, face shields, and gloves. You’ll also need to follow the correct safety procedures down to a T and weld in a ventilated area.
Limited Joint Access
A laser beam can typically only reach a small portion of the joint, meaning you’ll more than likely have to go over it in several passes or reposition your workpiece, something that could prove time-consuming. This is especially true of more complex and intricate parts.
Reduced Weld Strength
The downsides to laser welding include high cooling rates, partially completed fusion and penetration, material sensitivity, and joint design limitations, all of which could lead to weaker and less durable welds. Weak welds are the last thing you’ll want as they can be a potential safety hazard leading to failures.
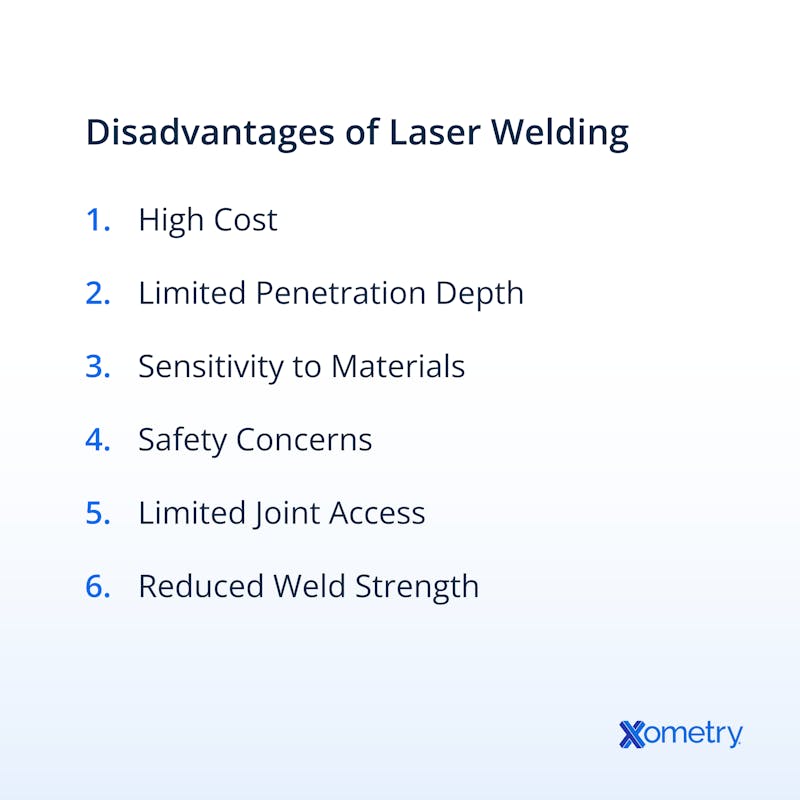
How Can Xometry Help
At Xometry, we offer a wide array of welding techniques through our global manufacturing network. If you don’t have the capability in-house or are simply looking to outsource work, we can help.
Learn more about our fabrication services on our sheet metal services page.
Disclaimer
The content appearing on this webpage is for informational purposes only. Xometry makes no representation or warranty of any kind, be it expressed or implied, as to the accuracy, completeness, or validity of the information. Any performance parameters, geometric tolerances, specific design features, quality and types of materials, or processes should not be inferred to represent what will be delivered by third-party suppliers or manufacturers through Xometry’s network. Buyers seeking quotes for parts are responsible for defining the specific requirements for those parts. Please refer to our terms and conditions for more information.
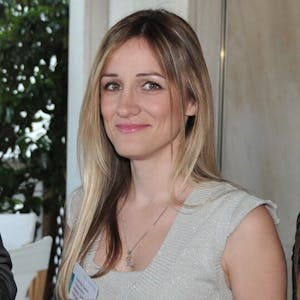