Laser beam quality significantly influences machine efficiency, particularly in applications like cutting and engraving, where precision and energy concentration are crucial. In principle, the ideal energy profile of laser output is defined by a “normal” or Gaussian distribution—smoothly bell-shaped and symmetrical, reaching a peak at the central optical axis. This peak is defined as the fundamental mode (TEM00). While this is the ideal, it is only approximated in reality. This energy profile results in the lowest divergence, reducing the widening of the beam with distance from the source. Higher beam quality minimizes the impact of diffraction, allowing for a tighter focal spot and reduced beam divergence. It enables a smaller focused dot size, maximizing energy concentration within the diffraction limit of the optical system. Optics, laser source, and path imperfections all affect the distribution adversely, and managing these issues is the result of good design. This article will discuss laser beam quality, M2 beam quality, the importance of laser beam quality, its characterization, and how it is measured.
What Is Laser Beam Quality?
Laser beam quality describes how well a laser beam maintains its shape, intensity, and coherence during propagation. Laser beam quality is evaluated based on its intensity distribution, divergence, and other parameters such as M², Strehl ratio, and beam parameter product (BPP). Space-bandwidth product (SBP) quantifies the trade-off between beam waist size and divergence, often used in optical communication and imaging systems rather than direct laser quality assessment. Observation of beam pattern symmetry allows the spatial mode properties to be assessed, which shows any obstruction or distortion in the beam path. Measuring the focused dot size helps determine how closely the beam approaches the diffraction limit, typically quantified using the M² parameter. It also helps to understand the source and optic distortion of the beam's energy distribution.
What Is M2 Beam Quality?
M2 is the parameter that defines laser quality in the real world, where an M² value of 1 represents a perfect Gaussian energy distribution. It quantifies how much the actual beam deviates from an ideal Gaussian beam. M2 is measured either manually or with an automated instrument, and it’s calculated from the relationship between the beam waist diameter at the focal point (D0), the half‐angle divergence (θ0), and the wavelength (λ), as given by the formula:
ϴ0=2M2D0
What Is the Importance of Laser Beam Quality?
Laser beam quality defines several properties critical to material processing, including:
- Higher beam quality results in a small focal point, increasing energy density.
- Higher energy density enables more rapid material vaporization, reducing the heat-affected zone (HAZ) and improving cut precision.
- A smaller beam diameter improves precision in cutting and engraving applications.
What Are the Common Ways to Characterize Laser Beam Quality?
Certain beam properties are more important in some applications than others. The most common ways to characterize laser beam quality are listed below:
1. Strehl Ratio
The Strehl ratio is the ratio of the peak intensity of the laser spot compared with the theoretical, diffraction-limited ratio of an optically perfect system. Values range from 0 (no spot of energy) to 1 (optically perfect, the intensity at the theoretical maximum). The Strehl ratio was originally developed to assess the quality of astronomical instruments. It is finding commercial use in laser cutting equipment as a way to quantify the optical path quality of a device.
2. Laser Beam Parameter Product
This quantification is mathematically simple. It is more closely related to the functional rather than the theoretical, potentially making it a more understandable reference. The laser beam parameter product is the product of the beam waist radius (i.e. the radius of the focused dot) and the divergence half-angle (in radians or more usefully milli-radians)—i.e., an easily measurable physical property.
3. Laser Beam Propagation Ratio (M2)
M2 is a calculated value that defines the divergence of the actual distribution from the Gaussian ideal. It results in a value between 1 and sometimes 10 or higher, where 1 is a perfect, theoretical beam and higher is degrading quality, as defined in ISO Standard 11146. In reality, laser cutters with M2 as high as 10 can be effective in heavy work, but lower is desirable.
4. Power in Bucket Parameter
Power in Bucket (PiB) is not yet measured by a universally accepted measurement. PiB typically quantifies the fraction of total beam power contained within a defined aperture, although no universally accepted measurement method exists.
Vertical axis beam quality is calculated from the:
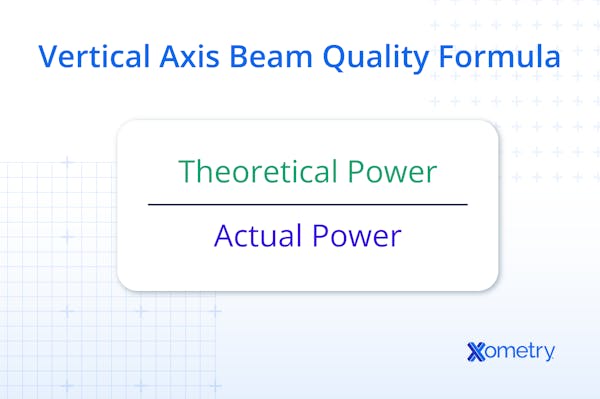
Horizontal power distribution for a given power is calculated as the ratio:
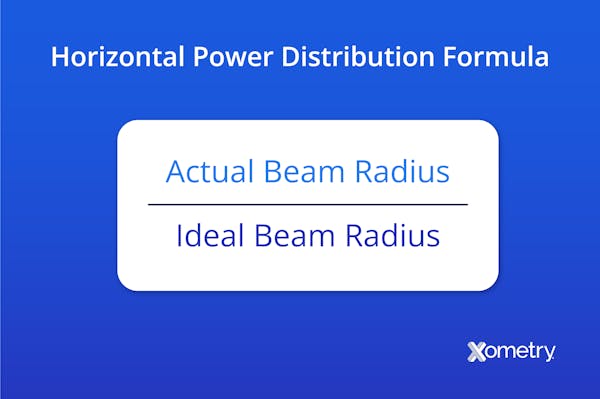
What Does a High Beam Quality Imply?
A higher-quality beam allows greater separation between the optics and the cut surface. This reduces deposition on the lens and obstruction of the beam. It also allows a smaller beam diameter at the focal point, potentially reducing the need for large-aperture optics. A higher-quality beam can be better focused to a point. It increases the energy density per unit area at the cut. This results in a smaller heat-affected zone (HAZ) and lower kerf in the cut. A higher-quality beam can be achieved with diode-pumped lasers, which often feature stable beam parameters and can be positioned farther from the workpiece.
What Does a Low Beam Quality Imply?
Low beam quality has serious impacts on laser cutter performance. Greater beam divergence results in more HAZ and greater kerfing. Low beam quality lessens the ability to tightly focus the beam to a point. This results in lower specific energy, requiring higher overall power to compensate for the loss of efficacy in the beam. The poorer focus must be compensated for by lower separation between optics and cut surface. This increases the risk of debris and deposition obstruction.
What Is the Ideal Laser Beam Quality Ratio?
A Strehl ratio of around 0.8 is often considered good in practical terms, although the theoretical maximum is 1 for a perfect optical system. For CO2 lasers, the M2 value typically lies between 1.1 and 1.3. Diode lasers typically range from 1.1 to 1.7. High-energy devices can be around 3 or 4, and values as high as 10 are not uncommon. PiB values commonly lie between 0.2 (quite poor) and 0.6 (good).
How Is Laser Beam Quality Measured?
Measuring the Strehl ratio often requires specialized beam profiling or interferometric equipment, as it involves comparing the measured beam to a theoretical diffraction-limited profile. It measures at the optic exit point and at the focal point, which will map the energy levels. This is used in conjunction with the diffraction-limited theoretical value for the laser.
The most easily assessed measurement is the BPP (beam parameter product). This can easily be measured with simple instruments. By increasing the laser optics to target distance to a large, known value and measuring the large disc of the incident light, the divergence half-angle can be calculated. By bringing the laser optics to the focal length and measuring the diameter of the dot of light that results, the second measurement gives the focal radius. Multiplication of these two values gives the BPP.
An essentially identical method can be used for calculating M2, and with a known laser wavelength, the value is simple to calculate. The PiB (power in a bucket) parameter is also difficult to measure. It requires an energy measurement at multiple points across the axis of the beam, both at the exit of the optics and at the focal point. These measurements are not easy to achieve, requiring a fairly scientific approach.
For more information, see our guide on How to Measure Laser Beam Quality.
How To Improve the Quality of a Laser Beam?
Manipulating a particular laser's quality to improve (lower) the M2 value is advanced optical physics. It is tackled using phase reshaping, continuous phase elements, and a variety of other approaches. In a commercial application, the best approach is to upgrade either the laser module, the optics, the beam path guides, or all three. Imperfect optics, beam occlusion, and poor-quality lasers are relatively easily changed to improve beam quality.
What Factors Influence the Quality of the Laser Beam in Various Laser Types?
Laser beam quality is affected by:
- The deviation between the ideal Gaussian distribution that a laser could produce and the actual output is directly attributable to the quality of the laser’s injection and the uniformity of the lasing elements.
- The optical quality and alignment of the collimation lenses.
- The optical quality of the focal lens arrangement.
- The alignment of the beam to the optical path.
- Occlusions and contamination in the optical path, both before and after the focal arrangement.
What Role Do Nonlinear Optics Play in the Quality of the Laser Beam?
Nonlinear optics (NLO) is the science that describes how high-intensity energy beams interact with matter, undergoing quantum effects that change the nature and wavelength of some or all of the light. In smaller, low-power devices, these effects are negligible, but in extremely powerful industrial devices, the effect can be marked.
These effects can be harnessed using phase manipulation to improve beam quality through the intelligent and adaptive design of the optical pathway components. Second harmonic generation is an example of an NLO effect, where a laser beam interacts with a nonlinear crystal—such as KTP or BBO—to produce light at half the original wavelength, thereby modifying its spectral and phase properties.
How Can the Quality of a Laser Beam Be Described Using Knowledge of Laser Parameters?
Beam quality is either a direct or indirect measure of the distribution of energy across the beam and the divergence of the beam. Both of these are very influential in the eventual application of energy to vaporize a target to cut material. These factors determine how tightly the beam can be focused. As beam quality degrades, the beam cannot be focused as sharply, which lowers the energy density at the cut point and increases the effective divergence beyond the focal point, often resulting in a wider kerf.
Is Having a Low Beam Quality Good?
No, having a low-quality beam is not good. As beam quality degrades, the specific power (energy per mm2) drops, making the effective laser power lower and slowing or preventing effective cutting.
Is a Low Value of M2 the Ideal Laser Beam Quality?
Yes, a low M² value is ideal because it indicates performance near the diffraction limit. However, M² is one of several important metrics, and factors such as PiB and BPP also contribute valuable insights into overall beam effectiveness. Other approaches to analysis also provide good approximations for laser cutter effectiveness. However, no laser cutter with a high PiB or BPP is likely to have a disadvantageous M2 value, so each of the beam quality measures has a similar utility.
Is a High Beam Quality Safe?
No, high beam quality is not inherently safe, although it is desirable for performance. A high-quality beam results in higher specific energy (W/mm²) at the focal point, which can increase hazards such as intense scattered light, especially when cutting reflective materials. Appropriate safety measures—such as filter barriers, interlocks, and protective eyewear—are essential.
Summary
This article presented laser beam quality, explained what it is, and discussed it in detail. To learn more about laser beam quality, contact a Xometry representative.
Xometry provides a wide range of manufacturing capabilities, including sheet cutting and other value-added services for all of your prototyping and production needs. Visit our website to learn more or to request a free, no-obligation quote.
Disclaimer
The content appearing on this webpage is for informational purposes only. Xometry makes no representation or warranty of any kind, be it expressed or implied, as to the accuracy, completeness, or validity of the information. Any performance parameters, geometric tolerances, specific design features, quality and types of materials, or processes should not be inferred to represent what will be delivered by third-party suppliers or manufacturers through Xometry’s network. Buyers seeking quotes for parts are responsible for defining the specific requirements for those parts. Please refer to our terms and conditions for more information.
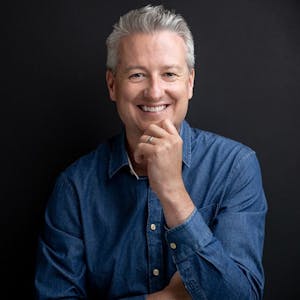