Laser cutting has reached a point at which many of those materials previously labeled as “difficult” can now be cut. Today, modestly powered laser cutters of up to a few hundred watts of cutting/engraving capacity are considered normal in home workshops. The largest laser cutting machines can cut steel, 100 mm thickness, at up to 100 mm/s feed. With the selection of the right methods, even the most difficult materials, such as stainless steel, can be cleanly cut. The lowest-cost machines (under $100), on the other hand, can cut many thin sheets and engrave on a wide spectrum of materials.
Despite the improved capability of laser cutters, there are still good and bad materials for laser cutting, for example: acrylic, plywood, and MDF. Listed below are the most common laser cutting materials:
1. Acrylic
Acrylic (PMMA) is a transparent plastic material known for its outstanding strength, optical clarity, and stiffness. There are two forms of acrylic: cast and extruded. Extruded sheet is harder to cut because residual stresses result in stress cracking. Slower cutting of extruded acrylic can leave better-looking cut edges. Ventilation is required when laser cutting acrylic because the vapor is an ignition risk and is toxic.
CO2 or diode-pumped is the recommended laser type when cutting acrylic. It is suggested to use the lowest power in cutting acrylic. High power will result in scorching. An 80 W laser should cut 8 mm acrylic at about 5 mm/s and produce high-quality edges, with a minimal heat-affected zone (HAZ). If the blower is set high, rough edges will result—the right pressure is the strongest you can blow on your finger, for setup.
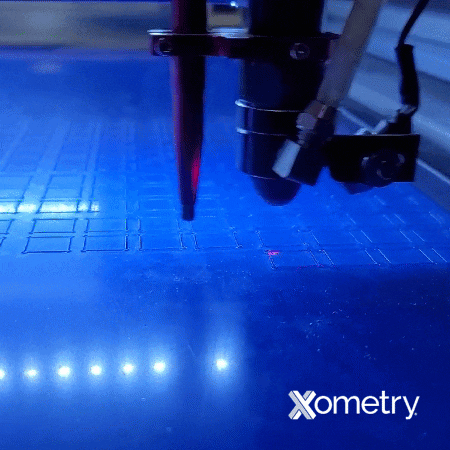
2. Plywood
Plywood is made from bonded wood veneers. While many forms of plywood are marketed, all plywood can be laser cut. Plywood is bonded with resins and produces toxic gasses when heated. It is therefore recommended to use ventilation when cutting.
Plywoods require high power and fast speeds when performing multiple cuts—which may result in an increase in kerf size. Higher blower pressure will result in cleaner cutting and allow higher feed rates. The recommended laser types are CO2 and fiber lasers.
3. MDF
MDF (Medium Density Fiberboard) sheet is an engineered material made with hardwood or softwood residuals. It is not an easy material to laser cut because its density and high adhesive content make it slow to cut and easy to produce staining and soot marking. MDF’s high density requires slow cut speeds and results in high HAZ and wide kerfing. It is recommended to use CO2 or a diode-pumped laser when cutting MDF.
When cutting MDF, it is necessary to use the highest power available. An 80 W laser cuts 10 mm MDF at about 3.5 mm/s with scorched and stained edges. The blower pressure also needs to be high. There will be burned residue to blow away, to allow the laser to pass and avoid depositing soot/residues on the optics.
4. Cardboard
Cardboard is a generic term for heavy paper-based products. It is a low-cost material used extensively for product packaging, modeling, and advertising. All laser types work well with cardboard.
When laser cutting cardboard, it is recommended to maintain ventilation. However, the volume of combustion products will be low, and cardboard has no significant toxicity. Additionally, use moderate power levels and fast feed speeds. Kerfing will also be limited and the HAZ will be small. Blower pressure should be set low, as the material can be lifted by air pressure, but some flow will make for better cut quality.
5. POM
POM (PolyOxyMethylene, Delrin®, or acetal copolymer) is an engineering material used in applications requiring strength, chemical resistance, and dimensional stability such as machine parts. CO2 lasers give the best results, but a fiber laser can be used for marking/engraving. The POM cuts very cleanly, with little HAZ using a CO2 laser.
When laser cutting POM, it is important to use ventilation because the scorched plastic presents high toxicity. Similar laser settings to those used for acrylic are often recommended although 25% slower feed rates are acceptable. Set to the lowest power that will allow the cut to proceed. An 80 W laser should cut 8 mm Acetal/POM at about 4 mm/s. The blower should also be set to moderate pressure.
6. Foam
A foam is a broad term that refers to materials formed by trapping pockets of gas in a liquid or solid. It encompasses a range of materials, some of which can be laser cut, several of which cannot. Some cuttable examples are: expanded polystyrene or polypropylene foams, Depron modeling foam, foam-cored boards like Gatorfoam, and EVA foam. There is no simple recommendation of a laser type, as foams belong to a range of material types—but any laser type is likely to cut well.
Laser cutting of foams requires very low power and high feed rates, good ventilation, and a breathing mask, as most foams release toxic gasses when heated. Blowers should also be set to a low level for thin materials.
7. Metal
Metal is a family of materials requiring high power to cut anything thicker than foil. Some metals work best with fiber lasers or solid-state, but others work with CO2 lasers. Cut quality is a result of laser power, pulsation, beam diameter, focal depth, and light frequency. Metals produce little by way of gas or residues and generally exhibit low toxicity, although normal precautions should still be applied.
Two methods are employed in the laser cutting of metals: reactive laser cutting and fusion cutting. Reactive laser cutting uses an oxygen jet in the cut to accelerate the cutting by oxidation. For thicker steel sections and titanium, the metal is rapidly oxidized and/or melted and then blown out of the cut area. Fusion cutting, on the other hand, is used to cut aluminum, stainless steel, copper, nickel, and tungsten. This technique uses a blend of nitrogen and argon to blow molten metal away from the cut.
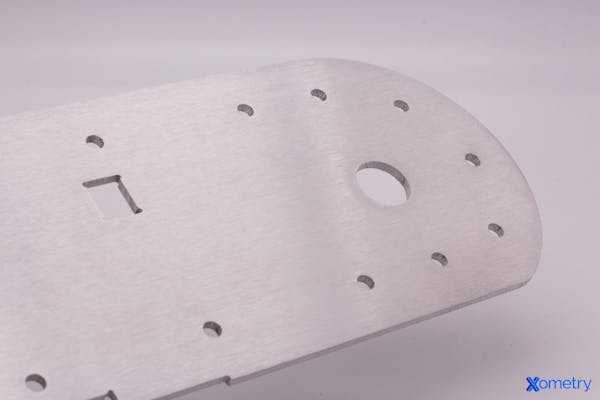
8. Leather
A leather is a strong and flexible material that is traditionally made of animal skins, although faux leather (artificial) is now available. CO2 lasers are generally the most effective at cutting leather. Modestly powered lasers will make good cuts in leather, although multiple passes may be required. Laser cutting in leather is clean and leaves no torn or damaged fibers. Laser cutting leather avoids the stress distortion that occurs with even the sharpest hand tools.
9. Plastic
Plastic is another broad classification that contains materials that cut well. Some of the plastic materials suitable for laser cutting are polyimide (Kapton®) and polyester (Mylar®) which cut well using diode laser and CO2 lasers respectively. Polycarbonate sheet, on the other hand, can be cut at 1 mm max, but the HAZ yellows and can distort. Polystyrene also cuts cleanly but tends to produce a lot of smoke and releases toxic styrene gas. Cut quality is a result of influences in laser power, pulsation, beam diameter, focal depth, (for thicker cuts), and light frequency (laser type). No two plastics have the same requirements. All plastics produce toxic gas or residues, and these pose serious health risks, so precautions are recommended.
10. Cork
Cork is the bark of the cork oak and is usually used in manufactured sheets. For cork, up to 3 mm thick, the speed of cut should be fairly fast, tens of millimeters per second. Thicker cork mats will require multiple passes for good cutting. Start with quite low power and increase until a smoke-free cut is achieved. The blower should be set to a high level, but not high enough to lift the sheet or cut areas.
11. Textiles
Natural textiles such as cotton, silk, and wool are great candidates for laser cutting. Low to moderate power and high feed rates will generally give excellent cut quality. Blower use is beneficial but must be at low pressure to prevent the fabric from being displaced and lifted. Synthetic fabrics can pose some issues as the line between melting the cut line and creating a fire can be quite narrow. There are no general settings that ensure good results. However, synthetic fabrics work well for laser cutting, once stable settings can be achieved.
12. Paper
Paper is very well suited to laser cutting. Any small laser-cutting machine will do a great job with paper, but it’s not well suited to larger industrial machines. Paper requires low power settings and high feed speeds, as it cuts very fast. Heavier papers may need slightly lower feed rates. Very clean cuts with no visible HAZ can be made.
Laser Cutting Settings for Each Material
The laser cutting settings for each material vary. Table 1 below lists some example:
Material | Machine power (W) | % power setting | PPI suggest | Speed (mm/s) | Max depth (mm) | Passes |
---|---|---|---|---|---|---|
Material Wood | Machine power (W) 80 60 40 | % power setting 50 65 80 | PPI suggest 500 engrave 500 cut | Speed (mm/s) 15 | Max depth (mm) 6 | Passes 1 |
Material Balsa Wood | Machine power (W) 80 60 40 | % power setting 50 65 80 | PPI suggest 500 engrave 500 cut | Speed (mm/s) 45 | Max depth (mm) 8 | Passes 1 |
Material Plywood | Machine power (W) 80 60 40 | % power setting 70 85 85 | PPI suggest 500 engrave 500 cut | Speed (mm/s) 10 7 5 | Max depth (mm) 5 | Passes 1+ |
Material Acrylic | Machine power (W) 80 60 40 | % power setting 55 70 85 | PPI suggest 500 engrave 1000 cut | Speed (mm/s) 12 | Max depth (mm) 6 | Passes 1+ |
Material MDF | Machine power (W) 80 | % power setting 100 | PPI suggest 500 engrave 500 cut | Speed (mm/s) 3.5 | Max depth (mm) 10 | Passes - |
Material Acetal/POM | Machine power (W) 80 60 | % power setting 100 100 | PPI suggest 500 engrave 500 cut | Speed (mm/s) 4 4 | Max depth (mm) 8 4 | Passes 1 |
Material Expanded polystyrene | Machine power (W) 80 60 40 | % power setting 12 15 15 | PPI suggest 1000 engrave 1000 cut | Speed (mm/s) 45 45 45 | Max depth (mm) 10 | Passes 1 |
Material Urethane foam | Machine power (W) 80 60 40 | % power setting 12 15 18 | PPI suggest 1000 engrave 1000 cut | Speed (mm/s) 25 25 25 | Max depth (mm) 20 | Passes 1 |
Material Leather | Machine power (W) 80 60 40 | % power setting 70 85 85 | PPI suggest 500 engrave 200 cut | Speed (mm/s) 12 10 7 | Max depth (mm) 8 | Passes 1+ |
Do Laser Cutters Have Software Programs?
Yes, laser cutters have software programs. Laser cutters are a branch of CNC machine tools. They have an onboard operating system, and their settings and cutter path instructions are generally provided as G-code.
Is It Safe To Laser Cut Flammable Materials?
No, it is not safe to laser cut flammable materials. However, some precautions can be taken to reduce the flammability of some materials. This consists of cutting in an atmosphere-controlled machine that fills the cutting space with nitrogen or nitrogen/argon mix, to prevent ignition. This method is only applicable to industrial-scale equipment and some laboratory laser cutters. No small-scale or home equipment is well suited to cutting flammable materials.
Summary
This article presented twelve laser cutting materials, explained what they are, and discussed the specifications of each material. To learn more about laser cutting materials, contact a Xometry representative.
Xometry provides a wide range of manufacturing capabilities, including sheet cutting and other value-added services for all of your prototyping and production needs. Visit our website to learn more or to request a free, no-obligation quote.
Copyright and Trademark Notices
- Kapton® and Mylar® are registered trademarks of the DuPont - Teijin Corporation.
- Delrin® is a trademark of DUPONT POLYMERS, INC.
Disclaimer
The content appearing on this webpage is for informational purposes only. Xometry makes no representation or warranty of any kind, be it expressed or implied, as to the accuracy, completeness, or validity of the information. Any performance parameters, geometric tolerances, specific design features, quality and types of materials, or processes should not be inferred to represent what will be delivered by third-party suppliers or manufacturers through Xometry’s network. Buyers seeking quotes for parts are responsible for defining the specific requirements for those parts. Please refer to our terms and conditions for more information.
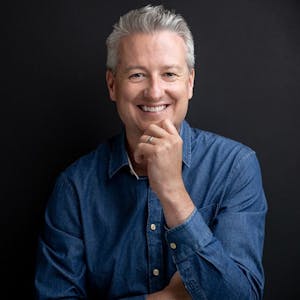