Although lasers were invented in 1964, it took a whole 12 years for laser etching to be discovered. No one really knows who exactly came up with the idea, but since 1978, this technique has been used in industrial settings and by large manufacturers, but also by small businesses and hobbyists. In this article, we’ll talk about how this process works, why it’s so loved, and we’ll also get into practical aspects like which machines are worth buying and their costs.
What is Laser Etching?
Laser etching is used to create markings, patterns, and designs on materials for aesthetic or informational purposes using a focused laser beam. It can be performed on organic, synthetic organic, and inorganic materials, and there are different types of lasers that work best with each material, including CO2, fiber, crystal, and diode. The only exceptions are materials that release harmful toxins when heated.
Perhaps its most important use is adding serial numbers to products so that companies can easily track them, isolate problems, and deal with recalls, defects, and necessary design changes. Ultimately, it’s important to the quality assurance, safety, and durability of products. What’s more, it can be a highly profitable business. Sure, you’ll have to initially invest in the machinery but there is a big demand for these services, and the method is pretty beginner-friendly and easy to learn. There are also many online tutorials and resources available.
Below are all the important details on laser etching, like compatible (and non) materials, as well as applications and pros and cons.
Compatible materials
- Easy to do on low melting point metals (magnesium, aluminum, anodized aluminum, zinc, lead)
- Can be done on steel with a more powerful laser
- Can be done on stainless steel but removes its protective coating (better to do laser annealing here)
- Laserable brass
- Wood
- MDF (medium-density fiberboard)
- Leather
- Paper/cardstock
- Ceramics
- Glass
Non-compatible materials
- PVC (polyvinyl chloride)
- PVB (polyvinyl-butyral)
- PTFE or Teflon
- Beryllium oxide
- Any material with halogen elements
Benefits
- Durable, precise, clean marks (better quality than by acid or abrasive methods)
- Quick, reduces production time
- Highly customizable
- Can be used on many different materials
- No-contact, so no mechanical stress to the material and no chemical reactions
Disadvantages
- Can wear out or distort in abrasive conditions
- Machinery can be expensive
Applications
- Personalized gifts, trinkets, and jewelry made of paper, wood, glass, and precious metals
- DIY and home decor, decorative items
- Brand symbols (logos, slogans, motifs)
- Traceability and identification features (QR and barcodes, serial numbers)
- Parts for the aerospace, automotive, and medical sectors
How it Works
Let’s get a little more technical. The etch mark is made with a laser that is blasted at the material. This modifies its surface, which expands and cools, and results in a slightly discolored and depressed mark that has raised edges all around it (shown below):
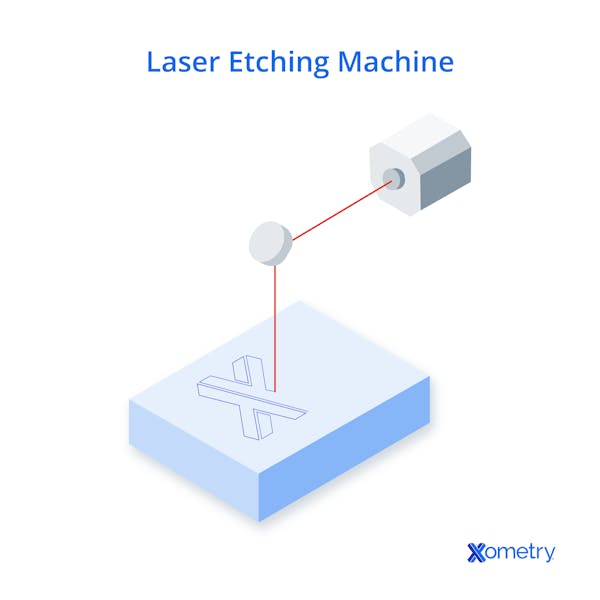
Pulsed lasers are typically used in the process as they’re better at etching than continuous wave lasers. These deliver powerful bursts of energy at set intervals, something that increases the energy absorbed by the material in a short period of time. Taking a 100W pulsed laser as an example, this can emit up to 100,000 pulses in just one second, whereas a continuous wave laser delivers the equivalent of 10,000 joules in the same timeframe. These short, high-intensity bursts, which are more powerful than a gentler, continuous stream, rapidly heat the material, causing it to melt, expand or, in the case of wood, decompose.
The laser power needed depends on the material used and its properties, like melting point or decomposition temperature. Wood, for instance, doesn’t melt but turns directly into charcoal and gases such as carbon dioxide. Plastics and metals melt into liquids before hardening again, but steel and other similar metals with high melting points will need much more laser power due to their thermal resistance. Also, some metals might need some pre-treating with a metal marking spray or paste before you can etch them so that their reflectivity is reduced and they can absorb more radiation.
Laser Etching: Step by Step
As already discussed, the process isn’t a difficult one, but you do want to follow these steps for a high-quality and precise result.
- Safety first: Before you do anything else, make sure you look after yourself. This means putting on protective eyewear rated for the specific laser you’re using and working in a well-ventilated area so that fumes can escape.
- Prep: Convert your pattern into a format that’s compatible with your machine. This could be .dxf or a similar vector-based format.
- Settings: Adjust the machine’s settings—power, speed, frequency, and focus—according to the material you’re working on and the design. You’ll find how to do this in the manual.
- Secure the material: The workpiece has to be firmly held in place if you are to have any chance of success, and you can do this with clamps, tape, or adhesives.
- Begin: Once you double-check everything is in order, you’re ready to go—but don’t forget to continuously monitor the progress! Focusing the laser lens can be done manually as needed, but you can also use the auto-focus function that many machines come with.
Laser Etching Machines
These machines cost anywhere from around $300 for basic starter machines to over half a million dollars for industrial-grade options. More expensive machines will understandably have a lot more capabilities, features, power, and precision. If you don’t have mass production needs and would rather not invest that much, there are some affordable options that work well. Just make sure that the piece of equipment you’re looking at can actually do what you need it to.
Whether you buy it from the manufacturer’s website or a large online retailer like Walmart or Amazon, check that a warranty and direct customer support are offered. Customer reviews are also helpful when you’re deciding which one to pick.
Here are three options that are fairly reasonably priced that we can recommend:
Attribute | OMTech 50W | Atomstack X7 Pro | Ortur Laser Engraver, Laser Master 2 S2 SF |
---|---|---|---|
Attribute Type | OMTech 50W Fiber laser | Atomstack X7 Pro 10W diode laser | Ortur Laser Engraver, Laser Master 2 S2 SF 1.6W diode laser |
Attribute Features | OMTech 50W Works with many materials, exceptional precision, tolerances of ±0.0001 mm, operation speeds of up to 275 inches per second | Atomstack X7 Pro Work area: 16.14 x 15.75 inches, spot size 0.002 x 0.002 inches, etching accuracy of ±0.08 mm | Ortur Laser Engraver, Laser Master 2 S2 SF Compatible with many materials, etching accuracy of ±0.0125 mm |
Attribute Price | OMTech 50W $5,300 | Atomstack X7 Pro $570 | Ortur Laser Engraver, Laser Master 2 S2 SF $233 |
Attribute Best for | OMTech 50W Professionals who need to work on various materials with high precision and speed | Atomstack X7 Pro Both beginners and professionals and those looking for a balance of affordability and efficiency | Ortur Laser Engraver, Laser Master 2 S2 SF Beginners who need a low-cost entry-level machine for simpler projects |
Laser Etching Machines
FAQs on Laser Etching
How long do laser etching machines last?
With proper care, use, cleaning, and maintenance (as per the manufacturer’s guidelines), these laser etching machines could last a good 10 years—sometimes even more. Other factors that contribute to their lifespan are construction quality, the type of laser it uses, how often it’s used, and the types of materials it works on.
Does laser etching wear off?
Yes; over time, the etching can wear off, especially if the item is in an abrasive or harsh environment. With etching, you’re essentially removing some of the surface of the material, and this can actually make it a little more vulnerable to wear and tear.
How does laser etching work on glass?
Laser etching glass involves the melting and deforming of the material’s surface, causing interactions between the metallic oxides used in glass coloring or strengthening, and silica with the air. This reaction forms tiny but visible fractures that result in the desired etched look.
Laser etching vs engraving: What’s the difference?
The terms laser etching and laser engraving are often used interchangeably, but they shouldn’t be as they’re quite different. Laser engraving needs more laser power and works by vaporizing material away to create shallow cuts into a part, while etching requires less power and melts the material at its surface, making an altered or slightly raised mark. Basically, laser engraving makes cuts deeper into the part. We’ve got a couple of dedicated articles on these processes if you’re interested in learning more:
How Xometry Can Help
For any more information on laser etching, or if you want to know how you could get started with either performing the process yourself or finding services for your projects, feel free to contact an Xometry representative. You could also upload your designs to the Xometry Instant Quoting Engine® for a free, no-obligation quote.
Disclaimer
The content appearing on this webpage is for informational purposes only. Xometry makes no representation or warranty of any kind, be it expressed or implied, as to the accuracy, completeness, or validity of the information. Any performance parameters, geometric tolerances, specific design features, quality and types of materials, or processes should not be inferred to represent what will be delivered by third-party suppliers or manufacturers through Xometry’s network. Buyers seeking quotes for parts are responsible for defining the specific requirements for those parts. Please refer to our terms and conditions for more information.
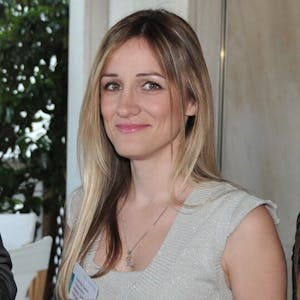