Many grades of stainless steel can be laser-cut quickly and precisely as long as you have the right tools. Laser cutting offers various advantages over more traditional approaches — it prevents work hardening, applies minimal heat to the metal, and often necessitates no finishing processes. However, cutting stainless steel does require knowledge, care, and good equipment. This article is intended as a primer on how to do it right and avoid common pitfalls.
Stainless steel is a broad term for austenitic, ferritic, precipitation, martensitic, and duplex (those with both austenitic and martensitic components) alloys. These alloys contain iron, carbon, chromium, and a range of other metallic alloying agents such as nickel, molybdenum, copper, niobium, titanium, and aluminum. Intentional additions can also be non-metallic, such as silicon, carbon, and sulfur.
The result is a spectrum of properties. Some alloys are strongly magnetic while others are only weakly so or entirely non-magnetic. Some such steels are easy to work-harden while others barely change. And though “stainless steel” is rhetorically synonymous with corrosion resistance, some versions actually do not fare well on that front.
The Types of Laser Cuttable Stainless Steel
All stainless steel alloys can be laser-cut given the proper machine settings, sufficient power, and the right controlled atmosphere. In general, the types of cuttable stainless steel are:
- Austenitic Stainless Steel: These steels have a face-centered cubic structure. They cannot be heat treated and they’re non-magnetic. The austenitic structure of the 300 series comes from the high nickel content whereas, in the 200 series, it is an effect of manganese and nitrogen in the structure. They are highly corrosion-resistant and work-harden to various degrees.
- Martensitic Stainless Steel: Martensitic stainless steel can come in high or low-carbon varieties. They can all be hardened and tempered by heat/quench processes. Classed as 400 series, they are generally less tough than austenitic steels and offer lower corrosion resistance. However, they are considerably more machinable because of their lower nickel content and a lower tendency to work harden.
- Ferritic Stainless Steel: This is a subgroup of the 400 series. These materials are heat-treatable and harden without putting in too much work. Examples are 430 stainless steel, often referred to as blade steel. They don’t tolerate cryogenic conditions but retain their properties at high temperatures. Additionally, they're not weldable.
These three families of materials are distinct in properties such as: work hardening, magnetic permittivity, corrosion resistance, hardness, and crystalline structure.
Understanding What Lasers Can Do to Stainless Steel
Laser cutting offers significant advantages over other 2D processing methods when working with stainless steel. The technology involves no force or distortion, so it does not induce any work hardening. Laser cutting, when performed under optimal conditions, produces fused, fairly smooth edges that rarely need post-processing. Cuts as deep as 100 mm are possible in a single pass which allows fast processing of large items.
Laser marking of stainless steel comes in two forms: straightforward ablation and laser annealing. Laser ablation is the process by which material is vaporized and removed. Laser annealing, on the other hand, is where the chromium oxide surface is largely undisturbed; instead, the metal beneath is annealed or melted and a limited amount of oxidation takes place below the outer oxide film. The latter method makes cleaner markings but it requires considerable skill to do it without ablating some material away. The low (highly localized) heating of the target area results in little or no distortion and staining in the wider heat-affected zone (HAZ). By contrast, rapid rotating cutter machining can alter hardness considerably around the cut zone and can result in heat distortion and discoloration over wider areas.
Laser engraving of stainless steel is possible as well, but it often results in discoloration. The engraving process destroys some of the surface oxide layers. Laser engraving is functionally identical to laser cutting. The difference is that the cut depth must be very tightly controlled to achieve good surface quality.
Laser etching is a more controlled process for stainless steel. The subsurface of unoxidized metal is annealed or melted without removing the protective oxide surface layer, which is essentially transparent to most cutting lasers. This method allows limited diffusion of oxygen through the oxide layer, staining the metal below in shades of yellow or brown depending on the intensity. This process is sometimes referred to as laser annealing.
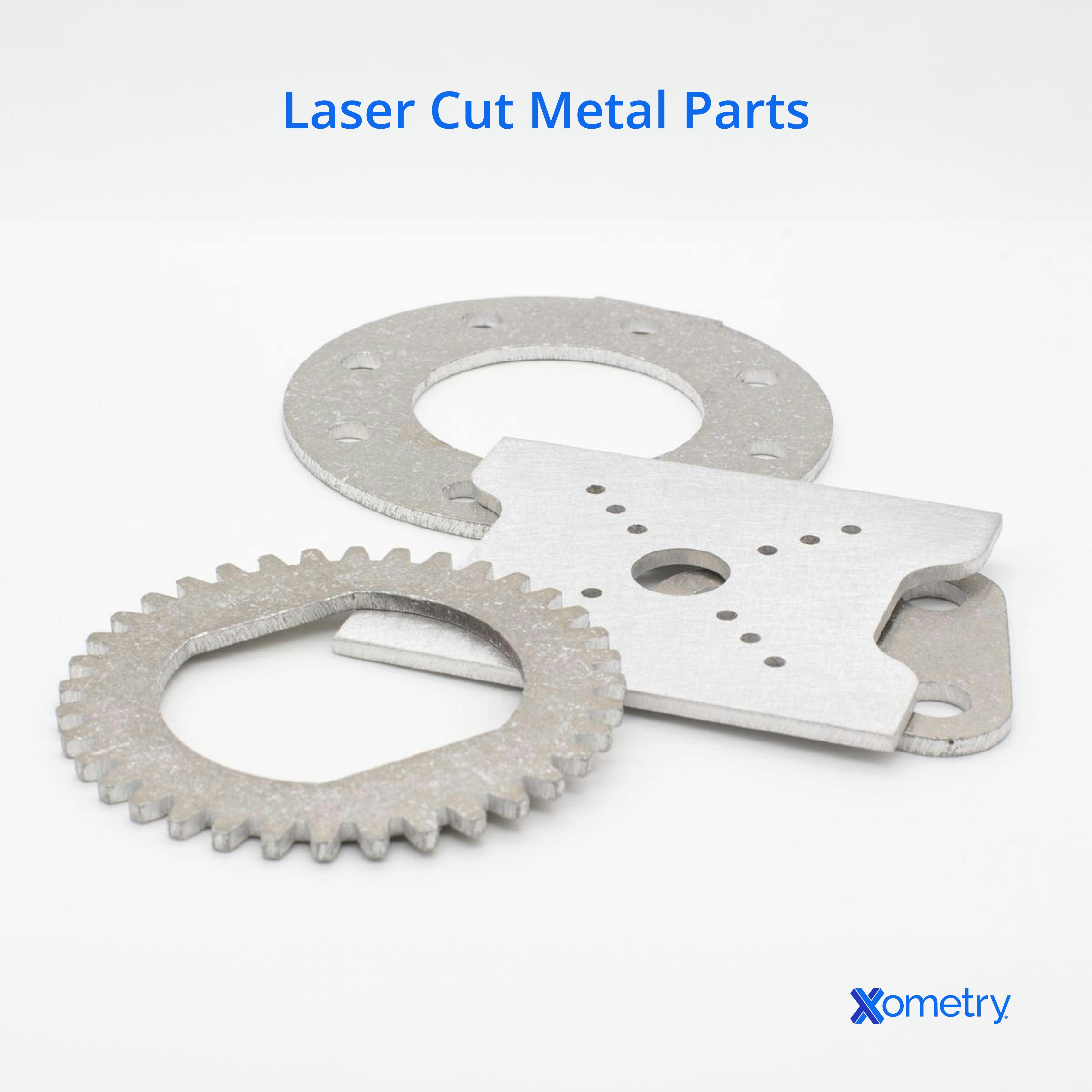
The Kind of Lasers That Can Effectively Cut Stainless Steel
The lasers that can effectively cut stainless steel are fiber and CO2 lasers. Fiber lasers can produce much narrower beams — typically half the diameter of the cutter ‘dot’ of a CO2 laser. This results in about quadruple the effective power for the same laser output energy. Fiber lasers can process faster and with greater precision because of this. Operating costs for fiber lasers are lower because of their electrical efficiency (4 to 6 times better than for CO2 devices) and solid-state construction. They do require more nitrogen shielding gas in the cutting process, though.
CO2 laser cutting typically delivers a 600-µm cutter beam width. These lasers are capable of much higher device power than fiber lasers, though modern fiber lasers are gaining ground in that regard. CO2 lasers are better suited to lower-precision cuts on thicker parts. The CAPEX cost of equipment is considerably lower than for fiber laser machines, but OPEX costs are higher per length of cut. For more information, see our guide on Types of Laser Cutters.
The Expected Outcomes of Using a Laser for Cutting Stainless Steel
Laser cutting of stainless steel can be precise and leave clean edges with little or no heat damage when all settings are optimized. To make this possible, though, a gas-assist setup must keep the laser’s path free of debris. The process is not foolproof; certain faults are common and can be corrected once they’re recognized. These are listed below:
- Large, Irregular Dripping at the Lower Face on Both Sides of the Cut: The cutter is running too hot. Increase the feed rate (for reduced local heat), air assist (for cooling), or raise the focal point slightly higher above the cut.
- Large, Irregular Dripping at the Lower Face, One side of the cut: Similar faults to dripping on both sides, but usually caused by an air assist nozzle that is poorly centered.
- Small Drips at the Lower Edge of the Cut: The focal point is too low and/or the feed rate is too high.
- Upwards Splashing of Melt is Visible: The feed rate is too high and, in some cases, the air assist is too aggressive.
- Yellow or Brown Staining at the Cut: Nitrogen feed is too low or the nitrogen has been contaminated with oxygen.
Tips to Consider When Laser Cutting Stainless Steel
There are many variables in setting up and operating a laser cutter, and stainless steel is not an easy material to process. Listed below are some tips to consider:
- Make sure the blower is set appropriately. Watch for splashback from the cut (material blown upwards by too much air), occluded optics (too little air), and asymmetric clearance (blower not centered well enough).
- Make sure the focal depth is set right. Carefully measure the size and shape of the kerf.
- Make sure the optics are clear.
- If you’re using nitrogen for the blower, look for oxidation (yellow or brown staining at the cut). If seen, this suggests the nitrogen flow rate is too low to exclude oxygen.
- Look for a wide heat-affected zone (melted or discolored/blue kerf) around the cut and melt evidence on the underside. It can indicate too slow a feed rate or too high a laser power.
As a policy, it’s best to start with the machine manufacturer's recommended settings for the material you’re cutting. Adjust parameters incrementally to understand the effect of changes.
Laser Cutting Stainless Steels
The process of laser cutting stainless steel is listed below:
- Confirm that your machine has a suitable laser type for stainless steel cutting — either CO2 or fiber laser types are optimal.
- Set the machine’s power output to meet at least the minimum required for the cut you're planning to perform
- Ensure the machine setup is correct according to the manufacturer's instructions. This includes focal length, power settings, clean optics, air assist, or gas assist.
- Place a scrap material sample on the table and set up a sequence of test cuts. Settings should start at the manufacturer's recommendation for the planned cut. Make small adjustments to one parameter at a time to explore the variables and their effects on cut quality.
- Execute the required cut on fresh material.
Understanding The Pricing of a Stainless Steel Laser Cutting Machine
There really is no average price for laser-cutting machines capable of processing stainless steel. This is because these machines vary so significantly depending on capability and features. For example, very light-duty machines such as the SculptfunS9 start around $300 while heavier-duty machines start around $3,000. High-end industrial machines will generally cost over $30,000.
Fiber lasers generally cost 5-10 times the price of CO2 lasers to buy, though their productivity is higher and their maintenance and power costs considerably lower. For light use, though, the advantages of fiber laser cutters are not overwhelming, and cannot yet achieve the huge peak power available from CO2 lasers.
The Difference Between CO2 and Fiber Laser for Laser Cutting Stainless Steel
CO2 lasers offer coarser beams than fiber lasers. However, CO2 lasers are capable of delivering considerably higher power in the 100+ kW power range. These lasers are cheaper but have higher maintenance costs than fiber lasers. Fiber lasers have limited power (15-20 kW), but can cut considerably faster than CO2 laser machines (3 to 5 times the feed speed), because their narrower beam means higher effective energy at the cut point. For more information, see our guide on CO2 Laser Vs Fiber Laser.
Xometry provides a wide range of manufacturing capabilities including CNC machining, 3D printing, injection molding, laser cutting, and sheet metal fabrication. Get your instant quote today.
Disclaimer
The content appearing on this webpage is for informational purposes only. Xometry makes no representation or warranty of any kind, be it expressed or implied, as to the accuracy, completeness, or validity of the information. Any performance parameters, geometric tolerances, specific design features, quality and types of materials, or processes should not be inferred to represent what will be delivered by third-party suppliers or manufacturers through Xometry’s network. Buyers seeking quotes for parts are responsible for defining the specific requirements for those parts. Please refer to our terms and conditions for more information.
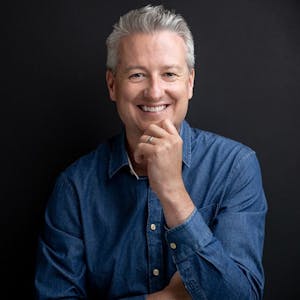