Laser-cutting machines are versatile machines that can make complex cuts and patterns using a powerful laser. They cut or engrave materials by vaporizing select portions of the workpiece. They are rapidly becoming more popular due to their non-contact nature and ability to consistently produce smooth and pristine cuts. Laser-cutting systems are useful in both industrial settings and craft and hobbyist environments.
Certain properties, or laser parameters, such as power, wavelength, and polarization, characterize the behavior of the laser. You won’t achieve the highest-quality cutting results unless you first understand the parameters and the ways they impact the final product. This article will discuss the ideal laser parameters, their definitions, and their benefits.
The Parameters of a Laser
Users must familiarize themselves with seven laser parameters to properly optimize for their particular laser-cutting projects. These laser parameters are described below:
1. Power
Power refers to the total energy that is emitted from a laser per second. Different laser-cutting systems have different maximum power ratings. Power is an important laser parameter because it defines how much energy goes into the operation, and potentially, how deep the cut will be.
2. Wavelength
The wavelength, typically recorded in nanometers (nm), refers to the color of the light emitted from the laser. More specifically, it relates to the frequency and energy of the electromagnetic radiation emitted from the laser. Shorter wavelengths (such as ultraviolet) have higher frequencies than longer ones (like infrared) and consequently, also have higher energy. The wavelengths used in laser systems range from infrared to ultraviolet, with visible light falling in between.
3. Polarization
The polarization of a laser beam refers to the direction in which the beam’s emitted electric field resonates. It is controlled by the specific optical equipment in the laser system. Polarization is an important laser parameter because it characterizes how materials both reflect and absorb light.
There are many different ways in which a laser beam can be polarized. However, circular and elliptical polarization are the two most commonly found in laser-cutting devices. Circular polarization means the orientation of the emitted electric field changes by 360° within a single wavelength. Elliptical polarization is similar in that its orientation changes by 360°. However, this change can occur over the span of multiple wavelengths.
Polarization affects laser-cutting operations differently depending on the beam’s angle of incidence. This is the angle at which the laser contacts the workpiece material. Metal workpieces can demand incidence angles as high as 70 to 80°. A high incidence angle coupled with circular or elliptical polarization can improve laser absorption rates by as much as 80% compared to linearly polarized light. That means the workpiece absorbs more energy and takes less time to cut. Users sometimes need to modify their lasers so they put out circularly polarized light.
4. Cooling
Cooling is an important laser parameter simply because the laser head generates heat while operating. Proper cooling keeps the laser optics at a more optimal temperature throughout its operation. This not only improves workpiece quality but also prolongs the laser system’s functional lifetime.
5. Pulse Width
Pulse width refers to the length of time between the start and end of a single laser pulse (the short firing of a laser). It is an important laser parameter because it characterizes how much energy is allowed to accumulate in the laser over a given period. This can affect laser cut quality and cutting speed.
6. Coherence Length
Coherence length refers to the distance the laser can travel before its light falls out of phase and becomes scattered.
7. Spot Size
Spot size is the total diameter of the laser beam as determined by the focal length of its focusing lens. Smaller spot sizes concentrate more energy in a smaller area, while larger spot sizes deliver less energy per unit area.
Laser parameters refer to the different properties that characterize the behavior of a particular laser. It’s important to understand these parameters and how they impact the laser’s performance and cut quality. Once you master these ideas, you’ll be able to choose the best settings for any project, workpiece, or material you choose.
The Benefits of Understanding Laser Parameters
Your thorough understanding of laser parameters will aid you throughout the laser-cutting process. The knowledge is critical to properly configuring your laser system to cut or engrave specific materials. Plus, you can develop more efficient processes overall.
The Impact of Laser Power on Laser Cutting
The impact of laser power on laser cutting cannot be understated. The higher the laser power, the more intense the laser beam. However, other factors can affect the beam’s intensity even at high power levels. Laser power must be balanced with spot size, another laser parameter, to achieve the right intensity to cut through a given material. This is similar to how a magnifying glass focuses the light from the sun on a hot summer day. A high-powered laser that’s matched with the right spot size will generate a very intense beam.
Note that your laser-cutting device must be rated highly enough for the power rating your workpiece needs. Some are not capable of cutting or engraving tough materials like metal or ceramics. Different workpiece materials require different power levels. Engraving demands less power, in general than cutting.
Laser Wavelength in Laser Cutting
Wavelength plays an enormous role in laser cutting. Every material exhibits its own absorptivity and reflectivity characteristics; a wavelength that is absorbed well by one material may not work well on the next. You must avoid wavelengths that are easily reflected because the reflected energy can cause safety risks.
For instance, most non-coated metals readily absorb green wavelengths but reflect infrared wavelengths, making them easier and less energy-intensive to cut using green lasers. On the other hand, passivated materials more readily absorb ultraviolet wavelengths, so UV lasers are best for them. Users need to understand how this laser parameter affects the success of a laser cut by evaluating the absorptivity of their particular workpiece material.
How Cooling Helps with Laser Cutting
Cooling plays an indirect role in laser cutting. When laser systems hit high temperatures, their accuracy and stability degrade. Thermal stress from these high temperatures damages the laser tubes, leading to costly repairs or complete replacement of the system. The workpiece material itself is not being cooled; rather, it is the tube within the laser system that is cooled. By keeping the laser tube between about 59°F and 77°F, the laser can deliver accurate and precise cuts and be used for prolonged time periods before requiring repair or replacement.
How Choosing the Proper Pulse Width Helps with Laser Cutting
Proper pulse widths make possible better laser-cutting quality and increased cutting speeds. Every workpiece material has its own optimal pulse width, though.
Pulsed lasers can deliver higher amounts of energy to a workpiece than a continuously fired laser. For example, in one second a 100 W laser can deliver 100 W of energy if continuously fired. Alternatively, if the pulse width of the laser is one millisecond, the same 100 W laser can deliver 6,000,000 W of energy in one second. Consequently, the pulse width can have a profound effect on the quality of a laser cut or engraving.
How Spot Size Helps in Laser Cutting
Spot size helps a laser cut because it defines how much of the laser’s energy is concentrated onto the surface per square micron. Small spot sizes consolidate energy into a smaller area and are controlled by the focal length of the focusing lens. Smaller spot size is correlated with a shorter depth of focus. A laser with sufficient power and a small enough spot size will be able to cut through the workpiece material.
Understanding Laser Parameters
With a thorough understanding of laser parameters and the ways each configuration affects the process, you’ll be better equipped to choose the right settings for your projects. Laser-cutting settings that can be directly set by the user are listed below:
- Power (as a percentage of max power)
- Speed (as a percentage of max speed)
- PPI (pulses per inch)
- Number of passes
- Cut depth
Each of these settings is related to one or more of the laser parameters described above. The right combination of settings for power, PPI, and speed will result in a successful cut. Knowledge of how the laser parameters affect laser-cutting settings will allow you to successfully and safely cut any material for which the laser cutter is rated.
How Xometry Can Help
Xometry provides a wide range of manufacturing capabilities, including sheet cutting and other value-added services for all of your prototyping and production needs. Visit our website to learn more or to request a free, no-obligation quote.
Disclaimer
The content appearing on this webpage is for informational purposes only. Xometry makes no representation or warranty of any kind, be it expressed or implied, as to the accuracy, completeness, or validity of the information. Any performance parameters, geometric tolerances, specific design features, quality and types of materials, or processes should not be inferred to represent what will be delivered by third-party suppliers or manufacturers through Xometry’s network. Buyers seeking quotes for parts are responsible for defining the specific requirements for those parts. Please refer to our terms and conditions for more information.
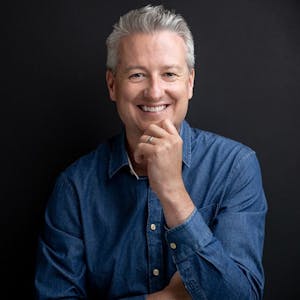