Laser welding is an important technique in high-tech manufacturing and engineering, and its popularity is only growing by the day. It offers lots of advantages over traditional welding techniques, such as the ability to weld all sorts of materials, and can create clean, strong welds quickly and precisely. The process has been adopted in aerospace, automotive, and medical, and it’s widely used to make electronics, too. This article will discuss all the ways in which laser welding can be used, its pros and cons, and the different types.
What is Laser Welding?
Laser welding is an efficient and quite gentle method that joins metal parts with a high-intensity light beam that causes the materials to melt and fuse together when cool and dry. The equipment used is either a large stationary machine or a hand-held torch, similar to stick welding. The process is easy to automate and delivers high-volume production and consistent quality that you could only really achieve with spot welding via other methods. Sometimes a metal filler is used for extra bonding power, but this isn’t always necessary. The laser welding beam is typically generated by a solid-state, fiber, or CO2 laser, each of which has its own advantages over the other (we’ll talk more about this a little further down).
At the beam’s focus point, the metal reaches its melting point and forms a localized pool, into which the filler rod can be melted as required. The laser beam is then moved along the surface of the joint. This melts a leading edge and leaves the molten, fused trailing edge of the pool to cool and solidify. In a successful weld, the cooled metal attaches to both parts to a roughly equal degree and remains free of oxidation. The process’s standout feature is by far its accuracy. If you have a tiny spot to weld, you can get to it easily without affecting the surrounding material, or causing any damage to the workpiece.
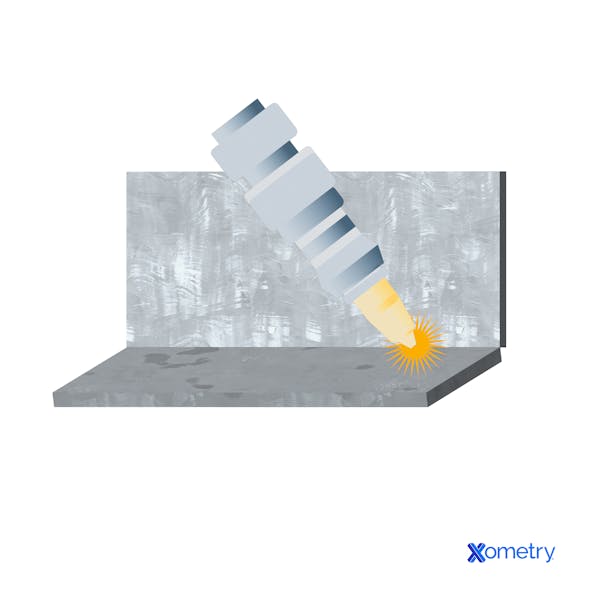
The laser welding process came out in the 1960s, around the same time lasers did. Bell Telephone Laboratories researchers were the first to try them out. They used a ruby laser with short and intense bursts of energy that were focused right where the metals connected. The desired outcome was achieved: the metals would melt and then merge. Even in these early experiments, this resulted in very narrow and detailed welds, with minimal heat-affected zones, and distortion. It even demonstrated some ability to join dissimilar materials.
Laser welding works on a wide range of materials, including metals (i.e., aluminum, copper, brass, steel, titanium, and nickel), plastics (like polycarbonate, nylon, and ABS), and even some ceramics (particularly alumina and zirconia). Carbon fiber-reinforced plastics are amenable to this technique, and there’s some advanced research and early success in laser welding metal parts to carbon fiber composites. It can even weld materials with differing thicknesses and properties together—something that can’t be said of most other welding techniques.
Whether or not you can weld something with this method will depend on the material’s physical properties; for instance, its melting temperature, albedo, thermal conductivity, and the point at which it melts just before it starts to char. The operator will need quite a bit of experience to use it properly, efficiently, and safely, especially for highly reflective materials, but practice makes perfect! (Some training wouldn’t go amiss, either).
The equipment for this welding method, however, is rather expensive and costs more than electrical or traditional thermal welding machinery. Some laser welding machines are also high maintenance, further increasing the cost. Though laser welding is effective on a vast range of materials, many plastics and ceramics cannot be welded for thermal and chemical reasons. Also, if you’re not very careful and don’t wear all the correct safety gear, laser welding can be dangerous (we’re talking burns and eye injuries … not nice).
The laser welding process is best suited to thin and light applications with very close-fitting parts that the optical parts can easily access. It is not currently well adapted to heavy-duty roles such as shipbuilding. It’s also less forgiving of contaminants, surface oxidation, and gaps between parts than traditional processes. In addition, the material edges must be close-fitting and smooth for good results.
Laser Welding Types
There are several different laser welding options to choose from. You’ll find them listed below.
- Conduction: This method fuses the materials together with only capillary action (no filler) and has a low power rating. It’s great for thin metals and fitted edges.
- Deep penetration: This is suitable for welding thick parts and uses high laser power to heat a deep and wide portion of the material. In general, the laser is first used to cut a keyhole that penetrates through the material (ensuring full-thickness welding). The resulting hole is then closed with a molten filler rod at its trailing edge, as the laser progresses along the weld.
- Laser spot: Best for small and more complex parts, this type makes smaller, localized welds that can make point joints between edges or melt through one part so that it can merge with the one under it.
- Laser seam: This approach makes long, continuous seams. It often uses a filler rod to create a filet at the joint using similar pool control motions to those seen in electrical and traditional thermal methods.
- Hybrid laser: This mixes laser and other welding processes such as MIG and TIG. Combining processes in this way can give you the advantages of both systems.
Laser Types
The types of lasers used in laser welding are listed below:
- CO2 (carbon dioxide): These powerful lasers can focus on an extremely small point and work by exciting carbon dioxide gas molecules, which then makes them emit radiation. It’s good for most materials, but some, like stainless steel and titanium, could initially reflect the laser and slow you down a bit
- Nd:YAG (neodymium-doped yttrium aluminum garnet): These lasers produce a powerful infrared light at a 1.064 micrometer wavelength, which is effortlessly absorbed by materials like stainless steel, aluminum, and titanium. They’re easy to focus and don’t need a lot of maintenance either.
- Fiber: These are also highly powerful and are energy efficient too. The beam in this laser is transmitted via a fiber optic cable straight to the weld spot. They’re often used in robotic welding and other automated systems, and have impressive longevity..
- Disk: These are some of the newer lasers around, and they use a thin disk made from a semiconductive material that has been liquid-cooled for laser generation. The beam can be emitted in two ways: in a reflector path, or via a light pipe straight to the torch. These are powerful, cool quickly, have excellent beam quality, and are easy to maintain.
Laser Welding: Basic Steps
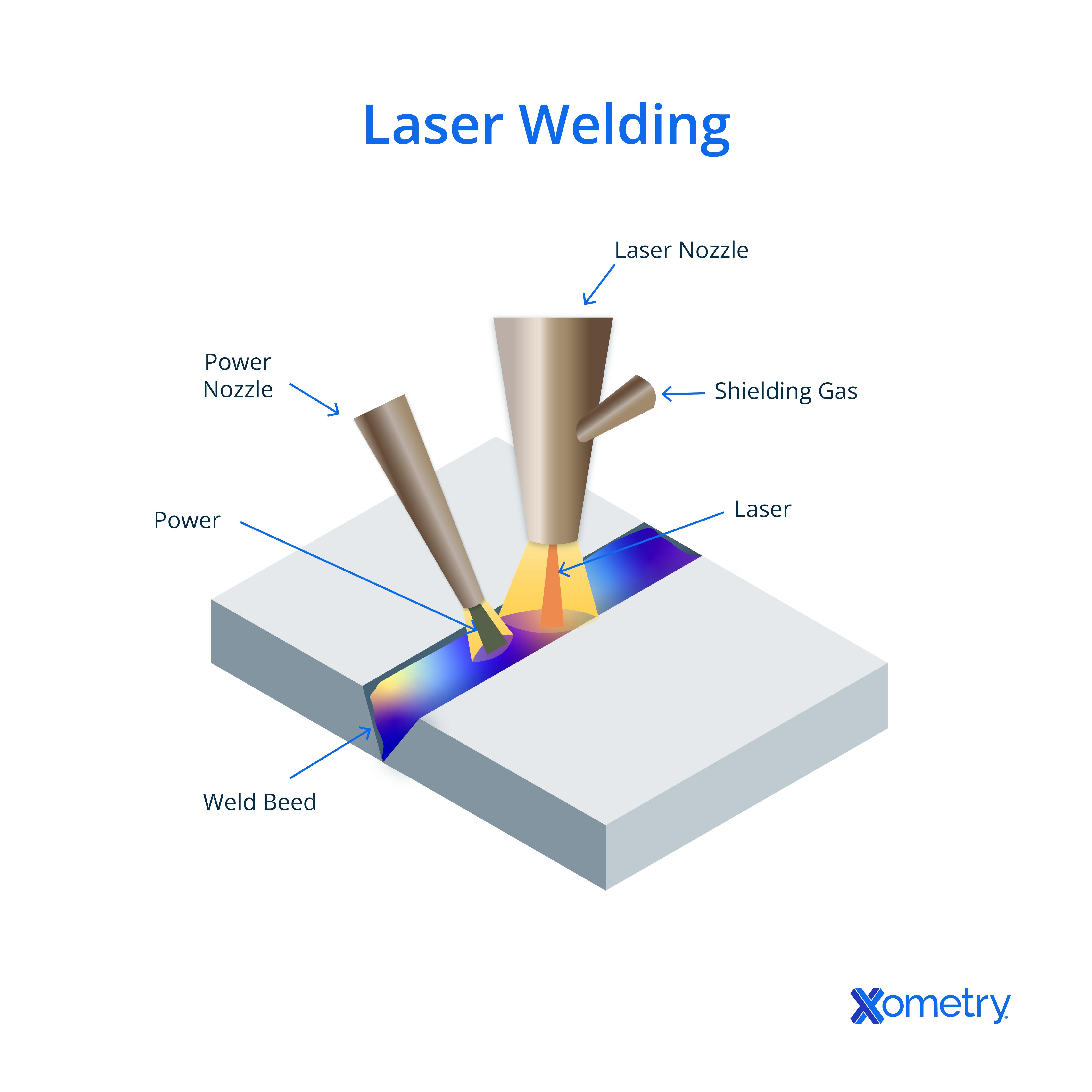
These are the generic steps in the laser welding process:
- Clean the parts you need to weld and position them as accurately as possible. The line where they meet should be totally closed without any gaps.
- Use manual clamps or automated fixtures to hold parts in place and keep them stable during the welding process.
- Adjust the beam’s focal point onto the welding area. The optical gear in the welding torch usually provides for easy adjustment of focus.
- Adjust the power of the beam and test it on some scrap material. Before moving to the workpiece, make sure it is putting out sufficient energy to melt the material but not enough to excessively heat parts.
- Aim the beam at the start of your weld area and once you’ve got a good melt going, traverse it along the connection steadily. Traditional welding techniques such as hot point rotation will encourage good fusion and improve weld quality.
- Cool the part naturally once the welding is complete. You can also quench it in water or use other cooling methods.
How Xometry Can Help
Xometry provides a wide range of manufacturing capabilities including CNC machining, 3D printing, injection molding, laser cutting, and sheet metal fabrication. We provide welding services on your parts, too, if needed. You can get started today by uploading your designs to the Xometry Instant Quoting Engine®!
Disclaimer
The content appearing on this webpage is for informational purposes only. Xometry makes no representation or warranty of any kind, be it expressed or implied, as to the accuracy, completeness, or validity of the information. Any performance parameters, geometric tolerances, specific design features, quality and types of materials, or processes should not be inferred to represent what will be delivered by third-party suppliers or manufacturers through Xometry’s network. Buyers seeking quotes for parts are responsible for defining the specific requirements for those parts. Please refer to our terms and conditions for more information.
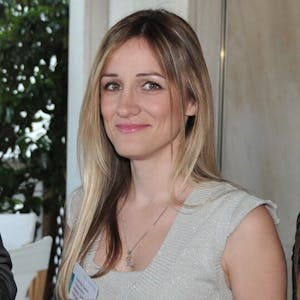