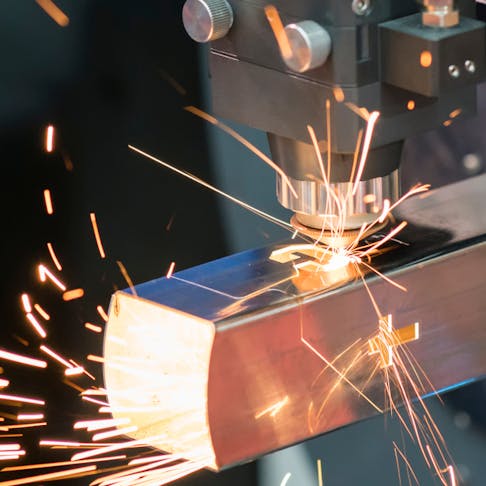
5-Step Laser Welding Process: How Does It Work?
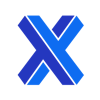
The laser welding process involves a series of steps that enable the joining of metal components using a concentrated laser beam. This cutting-edge method produces results that are precise and effective for a variety of applications. The process takes place in five general steps. It is computerized and continuously monitored to ensure accuracy and control. Depending on the particular requirements of the application, laser welding can be carried out using a variety of techniques, including conduction welding and deep penetration welding. Although laser welding has many benefits, it also has some drawbacks, which we will go over in more detail later. Listed below are the 5 steps in the laser welding process:
1. Preparation
The first step in laser welding is preparation. This includes: cleaning the workpieces to get rid of contaminants, getting the fit-up and alignment right, planning the joint configuration, and using fixtures commonly made from a solid milling block. This step is essential to guarantee high-quality welds. Cleaning removes substances that could interfere with welding, and fit-up and alignment ensure precise and durable welds. Joint construction allows for effective heat transfer and desired strength. It might be necessary to use fixtures to hold the parts in place while welding.
2. Beam Focusing
Beam focusing, an important phase in laser welding, entails expanding and reshaping the laser beam so that its energy is concentrated onto the weld joint. It includes collimation and focusing to converge the beam into a smaller spot size. The laser beam's effectiveness for welding is only realized when it undergoes the process of focusing through a specialized lens. Proper beam focusing is essential as it determines the intensity and size of the energy spot, impacting the weld quality, depth, and width. It enables precise heating and melting of the workpieces, enhancing weld quality and control. Key considerations for optimal energy delivery include: lens selection, optimizing focal distance, and aligning the beam with the weld join. For more information, see our guide on Laser Beam Quality.
3. Welding Parameters
Welding parameters in laser welding are the specific settings that control the laser power, welding speed, beam diameter, pulse duration, and repetition rate. Laser power determines the energy delivered to the weld joint, while welding speed affects heat input and the size of the heat-affected zone. Beam diameter determines energy concentration while pulsing duration and repetition rate control melting and solidification. Proper selection and optimization of welding parameters are crucial for achieving desired weld characteristics such as strength and quality. Factors like material type, thickness, joint design, and application requirements should be considered when determining the welding parameters. It is recommended to follow the recommended welding parameters of the machine’s manufacturer as well as the suggested settings for the material.
4. Welding Process
The actual welding process involves directing the laser beam along the joint to melt and fuse the materials. A coherent energy source emits a high-energy beam. The beam passes through a delivery path of mirrors to a series of lenses and focuses on a specified spot on the workpiece. As the beam hits the workpiece, localized heating and rapid melting of the joint area occur. Proper execution of this step is essential for achieving strong and reliable welds with minimal distortion. The welding process ensures high-quality bonds between materials.
5. Cooling and Solidification
After the application of heat, the molten metal begins to cool down. The cooling rate affects the weld's microstructure and mechanical properties. As the metal cools, it solidifies, forming a strong bond between the workpieces. Proper cooling and solidification are essential for achieving desired weld characteristics and minimizing residual stresses. Techniques like post-weld heat treatment or cooling devices can be employed to control the cooling rate and optimize the weld's properties. Ensuring controlled cooling and solidification enhances the overall integrity and strength of the weld.
What Is Laser Welding?
Laser welding is a precise and efficient welding technique that uses a high-energy laser beam to join materials including metals and thermoplastics, creating a strong and durable bond. Laser welding offers several advantages, including: high precision, minimal heat-affected zone, and the ability to weld complex geometries. It finds applications in various industries such as: automotive, aerospace, electronics, and medical devices. For more information, see our guide on What is Laser Welding.
How Does Laser Welding Work?
The process of laser welding involves heating and melting the materials to be joined with a high-energy laser beam. The material is heated to the point of melting when the laser beam is concentrated onto the weld joint. The molten material solidifies along the path of the laser beam, creating a sturdy weld. An automated system overseeing the procedure ensures precise control over the welding parameters. Fast and precise welding is possible with little distortion and a small heat-affected zone due to the laser beam's concentrated heat source.
What Are the Types of Laser Beam Welding?
There are two main categories of laser beam welding: heat conduction welding and deep penetration (or keyhole) welding.
To learn more, see our guide on the Types of Laser Welding.
1. Heat Conduction Welding
In this method, the laser beam generates heat at the surface of the material, causing it to melt. The heat then conducts through the material, resulting in the fusion of the workpieces. Heat conduction welding is suitable for thinner materials and applications in which a shallow weld depth is desired.
2. Deep Penetration/Keyhole Welding
This method involves greatly increasing the laser beam's intensity to penetrate the material deeply or to form a keyhole. The material is vaporized by the intense beam, creating a cavity filled with vapor. Then, the keyhole's walls collapse, completely fusing the two workpieces. Deep penetration welding is commonly used for thicker materials and applications that call for stronger welds.
What Is the Importance of Laser Welding?
Laser welding is important because it can produce welds with a high aspect ratio, or a large depth to a narrow width. This capability makes laser welding suitable for joint configurations that might not be possible with other conduction-limited welding techniques. For instance, stake welding through lap joints is a challenge with conventional methods but is possible with laser welding. With flexibility and versatility across numerous industries, this capability increases the number of applications in which precise and powerful welds are necessary.
What Are the Advantages of Laser Welding Compared to Conventional Welding?
Advantages of laser welding compared to conventional welding techniques include:
- Offers exceptional accuracy and control, resulting in precise and clean welds.
- The concentrated laser beam minimizes the heat-affected zone, reducing distortion and preserving material properties.
- Can join a wide range of materials, including dissimilar metals.
- Enables fast welding speeds, leading to increased productivity and cost-effectiveness.
- Can reach difficult-to-access areas, allowing for welding in tight spaces.
- Minimal spatter and clean welds often eliminate the need for extensive post-welding cleanup or machining.
What Are the Disadvantages of Laser Welding Compared to Conventional Welding?
Disadvantages of laser welding compared to conventional welding techniques include:
- Laser welding equipment can be more expensive to purchase and maintain compared to conventional welding equipment.
- The penetration depth of laser welding may be shallower compared to certain conventional welding processes.
- Often requires specialized training and expertise to operate and optimize the process effectively.
- May be more sensitive to material properties, such as reflectivity and thickness variation, compared to conventional welding methods.
For more information, see our guide on Disadvantages of Laser Welding.
How Much Does a Laser Welding Machine Cost?
A laser welder's price can vary significantly depending on the model, brand, and features required. The average cost of a laser welder is between $5,000 and $10,000. It's vital to remember that premium models with cutting-edge features and additional capabilities can cost upwards of $20,000. The cost may also be impacted by the application's specific requirements, such as power output, welding area, and the degree of automation that is desired. It is advisable to speak with manufacturers or suppliers to obtain precise pricing data based on particular requirements.
Can Laser Welding Be Used in Any Type of Welding Application?
No, laser welding may not be suitable for all types of welding applications. While laser welding offers numerous advantages, it has limitations such as limited joint thickness and sensitivity to material properties. Additionally, the cost and equipment requirements of laser welding may not be practical for certain applications. Each welding method has its strengths and limitations, and the choice depends on the specific requirements of the application. For more information, see our guide on Laser Welding Applications.
Is Laser Welding Expensive?
Yes, compared to other welding techniques, laser welding can be quite expensive. Additionally, effective use of laser welding systems often requires specialized training and knowledge. Laser welding's improved accuracy and efficiency, however, can result in cost savings in some situations by reducing material waste and speeding up production.
Is Laser Welding Efficient?
Yes, laser welding is an effective method. The laser beam's concentrated heat source enables precise and localized melting, resulting in reduced heat-affected zones and less distortion. High welding speeds are another benefit of laser welding, which makes it appropriate for automated and large-scale manufacturing processes.
Summary
This article presented the five steps of the laser welding process, explained what it them, and discussed them in detail. To learn more about laser welding, contact a Xometry representative.
Xometry provides a wide range of manufacturing capabilities, including sheet cutting and other value-added services for all of your prototyping and production needs. Visit our website to learn more or to request a free, no-obligation quote.
Disclaimer
The content appearing on this webpage is for informational purposes only. Xometry makes no representation or warranty of any kind, be it expressed or implied, as to the accuracy, completeness, or validity of the information. Any performance parameters, geometric tolerances, specific design features, quality and types of materials, or processes should not be inferred to represent what will be delivered by third-party suppliers or manufacturers through Xometry’s network. Buyers seeking quotes for parts are responsible for defining the specific requirements for those parts. Please refer to our terms and conditions for more information.
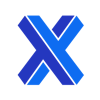