No matter what manufacturing project you're tackling, taking the time to sit down and go over all the expected costs should be at the top of your to-do list so that you don’t end up overspending. This is especially true with precision techniques like plasma cutting, where various factors can quickly push you over budget without you even realizing it. A good cost calculator can help you stick to your planned budget and prevent unexpected expenses. Proper planning could save you thousands. Let’s have a look at exactly what these calculators are and how they work.
What is a Plasma Cutting Calculator?
A plasma cutting cost calculator is a specialized tool that uses advanced technology and algorithms to provide accurate cost estimates for your project. You’ll be prompted to enter key project details—such as material type, thickness, and cutting speed—and the calculator will generate a detailed estimation so that you can plan accordingly.
Plasma Cutting Cost Calculator
Why Use One
There are several benefits of using a cost calculator for plasma cutting rather than relying on guesswork. For starters, they’re accurate, reliable, and easy to use. Knowing exactly what you’ll spend and how different factors influence the final amount can help you identify cost-saving opportunities. The clear breakdown of costs will allow you to make more informed decisions and stay on top of expenses. A cost calculator also helps you work out if a project is feasible or not—you might realize it’s not worth the cost after all and avoid investing both time and money. Alternatively, you can adjust certain aspects to make the project both viable and cost-effective. Your accountant will be happy, too!
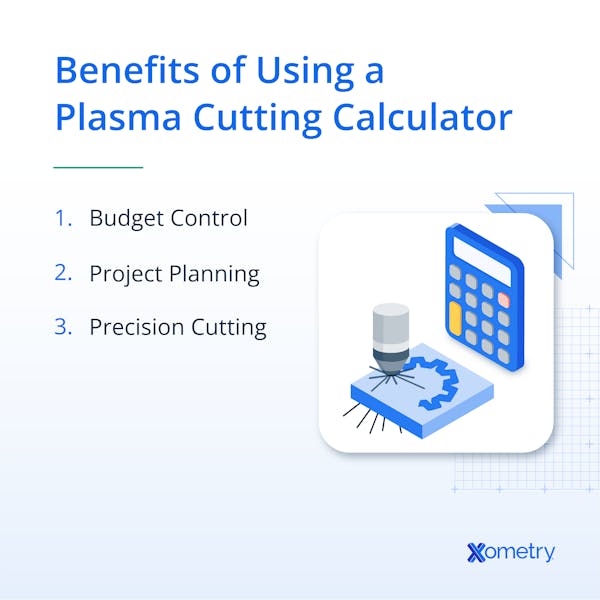
Plasma Cutting Costs
Here are the main factors that influence the final cost of plasma cutting:
Material type: The type of metal you choose has a big impact on costs, as different metals and alloys vary in price and cutting characteristics. For instance, some metals might need specialized settings or consumables that could up the price.
Material thickness: How thick a metal is will also affect the price. Thicker metals understandably require longer piercing times, and this can impact the quality of the cut, increase consumable wear, and ultimately add a few extra bucks to the process.
Cutting speed: Faster cutting speeds increase efficiency—especially for mass production—but can also impact cut quality and shorten consumable lifespan, driving up costs.
Power: The power levels used during plasma cutting also influence costs because different power levels affect arc stability, cut quality, and how long the consumable lasts.
Consumables: Electrodes, nozzles, shields, and other consumables are unavoidable costs in plasma cutting—and unfortunately, they will need replacing. How often depends on the complexity of the project and the level of wear they go through.
FAQs on Plasma Cutting Costs
How can I keep plasma cutting costs down?
To cut costs, consider materials that don’t require specialized consumables or settings. Choosing thinner materials where possible can also help. Experimenting with the calculator by inputting different variations can help you find the optimal cutting speed that balances efficiency and affordability. Optimizing power settings allows manufacturers to achieve the desired results while keeping expenses in check. Also, efficient consumable usage and replacement strategies can help control costs. Shopping around for deals on consumables or buying in bulk can also be beneficial for long-term projects.
What materials can be used with plasma cutting?
Plasma cutting is mainly used on electrically conductive metals. On the more affordable end of the cost spectrum, we have mild steel (carbon steel), galvanized steel, and aluminum in thin sheets. More expensive options—which typically have more to offer than their budget counterparts, like durability—include stainless steel, thicker aluminum, copper, brass, and titanium.
How Xometry Can Help
As we’ve seen, to get started on your plasma cutting project, you’ll need to know all the associated costs. You can get started today by uploading your designs to the Xometry Instant Quoting Engine®!
Disclaimer
The content appearing on this webpage is for informational purposes only. Xometry makes no representation or warranty of any kind, be it expressed or implied, as to the accuracy, completeness, or validity of the information. Any performance parameters, geometric tolerances, specific design features, quality and types of materials, or processes should not be inferred to represent what will be delivered by third-party suppliers or manufacturers through Xometry’s network. Buyers seeking quotes for parts are responsible for defining the specific requirements for those parts. Please refer to our terms and conditions for more information.
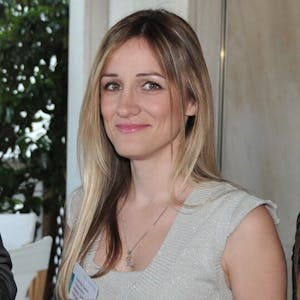