Whether it’s for functional purposes or aesthetic reasons, you might discover a need to engrave or laser cut polycarbonate products. It’s a precise way to make repeatable cuts with clean edges, and there’s no tool wear to worry about, either. The only downsides are that it often creates burred finishes, or discoloration and charring on the cut edges, and requires experience, the right supplies, and a careful hand to keep the process safe. We’ll break down the steps you’ll have to take to use a laser engraving tool and some advice for a successful project.
How to Laser Cut Polycarbonate
Here is a general look at the steps involved in laser cutting polycarbonate sheets:
- Gather up your supplies and high-powered CO2 laser.
- Choose the polycarbonate sheets you’ll be engraving—preferably with a width of no more than 3mm.
- Open your project file within the design application you created it in and connect it to the laser/engraver interface.
- Adjust the machine’s settings as necessary.
- Put the sheet on the machine’s cutting bed.
- Before starting on your main piece, do a test to check all the settings are as they should be, then you’re good to go.
Below is an example of a laser-cut polycarbonate item we made at Xometry.
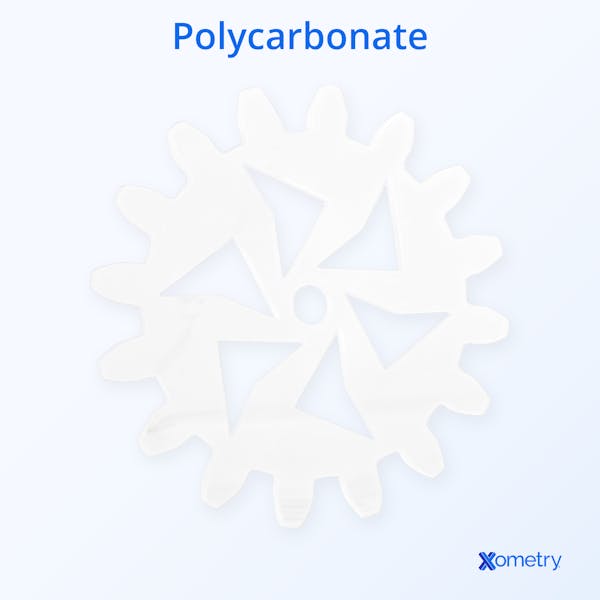
General Part vs. Presentation Part Cutting
It’s good to consider what the polycarbonate is going to be used for once it’s engraved, as this will help you decide the best method for cutting. In many instances, you’ll notice that polycarbonate sheets can get a bit stained around the edges, which is fine for components that will be used but won’t be on display, so don’t have to be particularly attractive. For presentation parts, laser cuts create a distracting and, quite frankly, ugly finish, especially anything under 3mm or over 8mm in thickness.
So while laser engraving is a perfectly acceptable technique for general parts and in cases where you’re not concerned about any tarnished parts, presentation parts will need to be cut with lasers at a higher speed of around 70mm per second. This is because cutting at a slower speed exposes the material to heat for longer, giving it more time to char. A quicker laser speed can keep the change of color to a minimum. When working with a CO2 laser (the type we recommend to our customers), try to keep it between 50–100 watts.
Recommended Settings
There are settings and specific measurements to have in mind in order to get the best laser cut or etching possible on polycarbonate. You’ll also want to know how these factors all impact one another.
The thickness of the polycarbonate sheet you’re cutting will make a difference in the end result (the thicker it is, the harder it is to get a clean cut and the more power, energy, and time it will need to properly cut and melt through it). The best thickness is 1mm or under, but you can work with up to 3mm. The power levels will vary based on this (i.e., a very thin piece may only need 50 watts, whereas a thicker piece will need 150 watts).
For resolution, go with 400 PPI (160 PPcm) and a 2-inch lens. The laser’s frequency should be about 50 kHz, and the gas pressure around 400 kPa (this will help push out the melted material faster and avoid that dreaded discoloration). You can approach the whole method in two ways, depending on whether you’re working with a high-power or low-power machine:
- High power: Set these machines to lower outputs, like 75–100 watts on a 150-watt cutter. Then you can fine-tune the speed as you see fit, normally this will be around 50–75 mm/s.
- Low power: This is often better for thicker sheets of polycarbonate, which can’t be lasered with other machines. Use the full power of the machine and give it two to four passes at the highest speed it can go.
The best way to avoid any problems is by using a high-powered laser (like CO2) on the fastest speed possible. Another final tip is to keep the protective film on the polycarbonate in place until you’re completely done cutting or etching.
How Xometry Can Help
At Xometry, we’re experts in polycarbonate and have several services that handle this material, which you can get free quotes for on our website. Learn more about what we can do for you when it comes to polycarbonate 3D printing or polycarbonate CNC machining.
Copyright and Trademark Notices
- LexanTM is a trademark of SABIC Global Technologies B.V.
- MakrolonTM is a trademark of Covestro Intellectual Property GmbH.
Disclaimer
The content appearing on this webpage is for informational purposes only. Xometry makes no representation or warranty of any kind, be it expressed or implied, as to the accuracy, completeness, or validity of the information. Any performance parameters, geometric tolerances, specific design features, quality and types of materials, or processes should not be inferred to represent what will be delivered by third-party suppliers or manufacturers through Xometry’s network. Buyers seeking quotes for parts are responsible for defining the specific requirements for those parts. Please refer to our terms and conditions for more information.
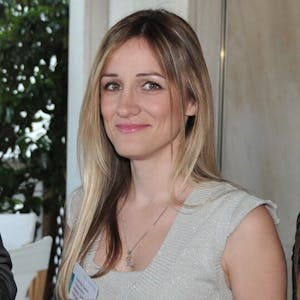