A stencil is a device that can help make designs or patterns on a surface. Lasers are often employed to create a variety of stencils for different applications. By following a few basic rules, you can design and make effective and long-lasting stencils by laser cutting. A variety of material options can be considered, based on the expected use and desired longevity of the stencil. This article will discuss the process of creating stencil designs using laser cutting, who can use them, and the suitable material for stencil laser cutting.
How To Make Stencil Designs Using Laser Cutting
The process of making stencil designs using laser cutting depends on the machine you are using. It is recommended to check the manufacturer’s guidelines to ensure the process is correct. In general, the steps to create stencil designs using a laser cutter starts with converting the design image into a vector format. Next, check the thickness of the stencil sheets based on the design requirements and the laser cutter you are going to use. Secure the sheet to the cutting bed, set the machine, and start the laser cutting process. Figure 1 below is an example of a laser cut stencil:

Laser cut floral design stencil.
Image Credit: Shutterstock.com/ZinYu
What Are the Uses of Laser Cut Stencil Designs?
Laser cut stencil designs have many applications including:
- Adding artwork in a precise way to manufactured objects.
- Adding repeat versions of artwork.
- Adding texture and highlighting flourishes to products.
- Executing artwork without requiring artistic or traditional craft skills.
- Applying adhesives to surfaces, to allow appliqué of materials with precision.
- Applying adhesives for fabric assembly.
- Applying solder precisely and selectively to PCBs.
- Ownership marking materials, and applying branding to products.
Who Can Use Stencil Designs?
Anyone with even moderate vector drawing package skills and access to a laser cutting machine can create stencils easily, quickly, and at a low cost. Stencils are widely used in the manufacture of printed circuit boards (PCBs) in the precise application of solder paste, prior to wave or flow soldering. In art, stencil artwork is still commonly used for applications such as: printing onto low-cost consumer products, particularly onto plastic components for branding, certification information, and warnings.
What Materials Are Suitable for Laser Cutting Stencil Designs?
The materials suitable for laser cutting stencil designs are listed below:
- Mylar® (Polyester): Mylar cuts well, supports excellent detail, and is low cost. Mylar stencils, with careful use, can be used many times and can generally be cleaned before material buildup poses a problem. Adhesion by paints is very poor and a slight flexing of the stencil will crack and peel many materials.
- Paper: Paper stencils are not strong enough for swept-contact stencil use but can perform well with spray paint, sponge dabbing of ink/paint, or airbrush application.
- Sticker Paper: This type of material can perform better than plain paper. The adhesive layer adds toughness and resistance to the stenciling medium. Adhered stencils can give better results than “floating” ones, as the adhesive reduces bleeding (of applied inks, paint, etc.) under the stencil.
- Polypropylene (PP): PP sheets can make robust stencils, but only when the thickness is sufficient. The generally available thicknesses of PP are too large for highly detailed and fine-featured stencil work but can be used to good effect on simpler images. An advantage of PP is its high chemical resistance. Repeated exposure to paints and dyes will generally not alter/degrade the stencil.
- Acrylic: Acrylic is generally available in thicker sheets and is therefore only suited to simple cut work. Acrylic stencils can be tough, although thin sections will be at risk of cracking under any rough handling.
- Cardboard: This group of materials offers a low-cost route to stencil making. The result will be tougher than paper and can serve more application steps.
- Rubber and Silicone: These materials offer some significant advantages but relatively high costs. They will allow the use of stenciling on 2D and 3D-shaped surfaces, conforming to a degree.
- Magnet Sheets: This material is very useful for coarse stenciling and particularly on vehicle or machinery steel panels. The stencil will potentially hold itself in place under even fairly aggressive use.
Is Mylar the Most Effective Material for Laser Cutting Stencil Designs?
Yes, Mylar is the most effective material for laser cutting stencil designs. It offers a good combination of stiffness, toughness, clean cutting, and availability. Thickness is an issue that must be carefully considered, as thinner stencils provide better results. Thicker Mylar, however, makes a much more durable stencil.
What Is Mylar?
Mylar is referred to as biaxially oriented polyethylene terephthalate (BoPET). Polyethylene terephthalate (PET) that has been pulled to increase its length and reduce its thickness on two axes undergoes a polymer chain alignment that improves many of its mechanical properties. Mylar films are available from very fine films (as thin as 12 µm) up to stiff sheets of 500 µm and more in thickness. It cuts cleanly with low-cost equipment.
What Are the Stencil Designs I Can Make Using Mylar?
Some examples of stencil designs that can be made using Mylar are:
- Spray Painting a Graphic or Advertising Slogan Onto a Surface: Mylar is tough and unaffected by general paint solvents, so the stencil will survive repeated use. The flexibility of the film allows the stencil to conform to a degree to uneven or curved surfaces.
- Daub Application of Paint as Decorative Features: Mylar stencils can perform admirably in delivering fine detail and a robust stencil that can endure repeated use.
- Controlled Application of Wood Glue in Building a Product: Mylar stencils can offer advantages in precision and speed of application, by roller or squeegee for example. Multiple applications can be made with careful design and planned use that avoids folding/lifting/wrinkling the stencil. It can also be washed between uses to reduce contamination.
How To Measure the Right Thickness of Mylar for a Stencil Design
Selecting the right thickness of Mylar for a stencil design depends on the application. There is much discussion about thickness and its relationship to feature size, but there is little benefit in going thinner than 4 thousandths of an inch (4 thou, or 0.1 mm) as the films get quite foldable and easily damaged. Once the thickness rises to 7.5 thou (0.19 mm) the film gets quite strong and durable and will still deliver good results with a fairly fine and complex design. For some uses, such as stencil application of high-build and high-viscosity media, a thicker stencil can be desirable to allow a taller layer of material to be laid down. This makes the laser cutting harder and limits the detail that can be fully reproduced.
What Software Is Used for Designing a Laser Cut Stencil Design?
There is a wide spectrum of 2D/3D CAD design and drawing tools that can be used for designing stencils. Listed below are the top three:
- SolidWorks®: SolidWorks® allows 3D visualization of the details you’re designing. It provides great flexibility in design/modeling and enables precision in features that can be hard to achieve with simpler tools.
- Adobe® Illustrator®: Adobe® Illustrator® allows you to draw precise features and quality curves as vector graphics. This provides an excellent 2D design platform that equips you with these simpler design tasks.
- SketchUpTM: SketchUp™ equips basic users to achieve good results quickly. If your design ambitions are limited to laser-cutting 2D shapes, SketchUp™ is a great tool set. It offers a wide spectrum of plug-ins that extend its capabilities into other areas.
What Are the Factors To Consider When Planning To Make a Stencil Design?
The factors to consider when planning a stencil design are:
- Price: Determine what cost is acceptable for the finished stencil. For example, Mylar sheet costs more than paper. Stainless steel sheet, however, costs more than Mylar and is considerably more difficult to cut.
- Flexibility: Is it to be applied to a 2D curved surface? Or a 3D curved surface? More flexible materials may be of advantage in fitting, but may also be much more difficult to stencil with.
- Durability: Is it for single use? Is the paint/dye to be sprayed or wiped? How many times do you hope to use this stencil? A harder-wearing stencil will be either thicker Mylar or potentially stainless steel foil. This may make the stencil harder to handle or harder to get good results from.
- Level of Detail: More detail suggests a thinner sheet is a good choice. But that may conflict with the requirement for durability, so a compromise may be required.
- Density of the Artwork and Complexity: Dense features may mean small and potentially long arms of a stencil to form the gaps between features. This can make good results difficult to achieve if bleeding through nullifies the desired blank areas in the paint/dye after application. You could consider widening the remaining sections or using an adhesive stencil that will reduce the bleed-through. This may require removal after the paint/dye is cured, however, to avoid smearing.
- Strength: The required strength is derived from both the type and thickness of the material. A stiffer or harder material will allow smaller features and allow the stencil to retain its integrity. The compromise this requires is usually a cost issue.
- Graphic Structure and Design: Do all the features work, both in the cutting and in the use of the stencil? You may need to adjust features to improve the integrity of the remaining material or to improve the functionality while using the stencil.
- Type of Surface: This can affect the choice of stencil material and the possible design features. There is no point in designing fine details in a stencil that you expect to use on a coarse or rough surface. Equally, rougher surfaces can be stenciled more effectively with sprayed media rather than wiped paint/dyes.
What Is the Advantage of Using Stencil Designs?
Some advantages of using stencil designs are:
- Allows the rapid and repeatable reproduction of designs in a range of colors, onto many parts and materials.
- Allows the use of a variety of media such as paints, dyes, spray paint, adhesives, and even solder to be applied with high precision and repeatability.
- Offers a way to imprint artwork onto surfaces without the need for craft talents.
- Stenciled images can elevate a simple product, provide useful information to aid in the use of a product, impose branding, and more.
Are Laser Cut Stencil Designs Reusable?
Yes, laser cut stencils can be made to be reusable. This simply requires that they have enough strength and stiffness to cope with the process of stenciling—and exhibit limited or no tendency for the stenciled medium (paint, dye, solder, adhesive, etc.) to negatively influence the stencil material itself.
Summary
This article presented laser cutting stencil designs, explained what they are, and discussed how it's done and its uses. To learn more about laser cutting stencil designs, contact a Xometry representative.
Xometry provides a wide range of manufacturing capabilities, including sheet cutting and other value-added services for all of your prototyping and production needs. Visit our website to learn more or to request a free, no-obligation quote.
Copyright and Trademark Notice
- Mylar® is a trademark of DuPont Teijin Films™
- SolidWorks® is a registered trademark of Dassault Systèmes SolidWorks Corp.
- Adobe® Illustrator® is either a registered trademark or trademarks of Adobe in the United States and/or other countries.
- SketchUp™ is a United Kingdom trademark and brand of Trimble Inc., Sunnyvale 94085, United States.
Disclaimer
The content appearing on this webpage is for informational purposes only. Xometry makes no representation or warranty of any kind, be it expressed or implied, as to the accuracy, completeness, or validity of the information. Any performance parameters, geometric tolerances, specific design features, quality and types of materials, or processes should not be inferred to represent what will be delivered by third-party suppliers or manufacturers through Xometry’s network. Buyers seeking quotes for parts are responsible for defining the specific requirements for those parts. Please refer to our terms and conditions for more information.
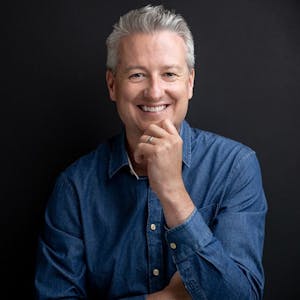