Gas welding uses pressurized gas in cylinders to assist the welding process, usually by providing heat through combustion. It heats and melts metal to fuse two pieces of metal together. Listed below are types of welding that utilize gas, and the applications of these different welding approaches:
1. MIG Welding
MIG welding (metal/inert gas welding), which is actually a type of arc welding, but one that uses gas. The gas is a shield gas, to protect the molten weld pool of metal from the atmosphere and control the chemical constituents of the resulting solidified weld. The shielding gas prevents oxides and nitrides from forming in the weld.
MIG welding creates the electric arc between the metal workpiece and a consumable electrode. This consumable electrode is fed continuously into the weld pool as it is consumed. This provides the filler material for the weld.
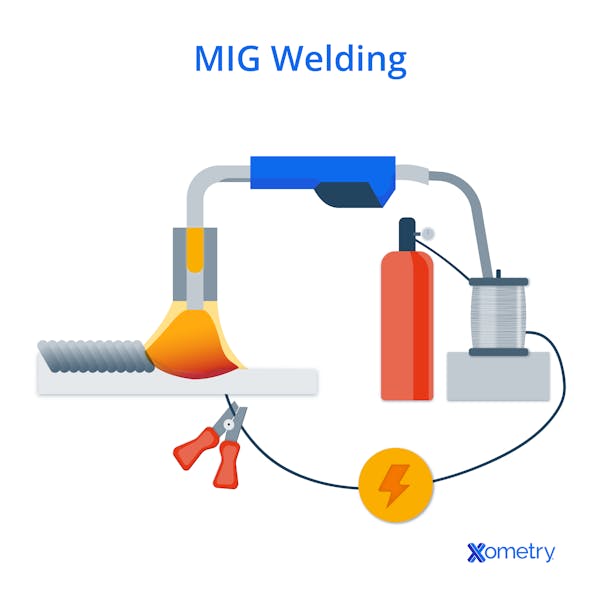
2. MAG Welding
MAG welding (metal/active gas welding), is also a type of arc welding that is very similar to MIG welding, but the shielding gas used is different. The gas typically used is carbon dioxide (CO2) or can be a mixture of CO2 or oxygen with argon (an inert gas). The active gas makes the gas around the arc more conductive, which increases the electrical voltage in the arc and therefore increases the heat at the weld pool. This helps to create deeper penetration into the metal and therefore is used to weld thicker components.
3. Oxy-Acetylene Welding
Oxy-acetylene welding is the most common type of gas welding. A mixture of oxygen and acetylene is burned to create a high-temperature flame, which then heats and melts the metals to be welded. Two pressurized gas cylinders must be provided, one of oxygen, and the other of acetylene. The ratio of the two gases in the mixture changes the characteristic of the flame created by the gas torch. As a result, the flame can be lean in acetylene fuel, rich, or balanced. This method can be applied to a range of ferrous and non-ferrous metals and is commonly used for copper, brass, and bronze.
4. Oxy-Fuel Welding
Oxy-fuel welding refers to a category of gas welding in which fuel gas is burnt together with oxygen. Therefore this term covers oxy-acetylene welding (the most common oxy-fuel combination), oxy-hydrogen welding, as well as propane brazing. Specifically, oxy-fuel welding requires two pressurized gas cylinders—one with oxygen, the other with fuel. The choice of fuel affects the flame temperature and other characteristics, and therefore the applications of each.
5. Pressure Gas Welding
Pressure gas welding is a technique that presses two pieces of metal together while heating their touching surfaces with a gas flame. The pressure of the two pieces being pressed together, combined with the heating from the flame, fuses the two pieces together. No filler material is required. This type of welding is commonly used for rods (like reinforcing bars for concrete construction) or railroad rails.
6. Hydrogen Welding
A variation of gas welding is the combustion of hydrogen as a flammable gas rather than acetylene. This oxy-hydrogen welding was historically used for specialist applications such as underwater welding, or for specific materials. It has been supplanted by other welding techniques (such as arc welding) in some of these areas, but it still finds niche application. For example, it is used in forming laboratory glass, in which carbon-free combustion gases are necessary.
7. Gas Tungsten Arc Welding (GTAW)
Gas tungsten arc welding, also referred to as tungsten/inert gas welding (TIG) is a type of arc welding. However, TIG welding does use an inert gas (argon) to shield the weld that is performed by the arc. The purpose of the inert shielding gas is to prevent the formation of oxides and other chemical compounds in the weld that could reduce the strength and corrosion resistance of the weld. TIG welding uses a non-consumable tungsten electrode to create the arc to the workpiece, and the welder then feeds a wire for the filler material. TIG welding is slow and requires a highly skilled welder, but it gives the best aesthetic finish.
8. Air-Acetylene Welding
As the name suggests, air-acetylene welding is carried out by the combustion of acetylene gas mixed with air. This provides a lower heat output than oxy-acetylene welding. Therefore the technique is favored for soldering piping in HVAC systems, in which the lower heat input helps to avoid overheating the solder and flux. Only one pressurized gas cylinder is needed—for the acetylene, compared to oxy-acetylene welding which requires a second cylinder for the oxygen.
9. Propane Butane Gas Welding
Propane (together with butane in mixtures) is commonly known as Liquified Petroleum Gas (LPG). LPG can be combined with oxygen to create a flame in a gas torch. A propane flame, however, cannot actually be used for welding as it does not create a reducing environment but rather an oxidizing one—it causes the metal to be welded to “rust”. However, propane can be applied for brazing as well as cutting. It has some advantages over oxy-acetylene as propane is a cheaper gas, and the heat output from a propane flame is higher (although at a lower temperature) than an acetylene flame.
What Is Gas Welding and How Does it Work?
Gas welding uses the heat source from the combustion of flammable gas to melt and weld metal. Typically two pressurized gas cylinders are required: one for the flammable gas (fuel) and the second for oxygen. A gas torch is used to control the mixture of the fuel with oxygen and to control the resulting flame. The flame of the gas torch is applied manually to a metal surface to heat it and melt it for welding. Gas welding includes some variations, particularly in the fuel gas that is used. Acetylene is the most common, but hydrogen and LPG can also be used depending on the application.
In general, gas welding works by creating a hot flame through the combustion of a flammable gas mixture. Two pressurized gases—fuel and oxygen—are fed to a handheld gas torch. The flow of each gas is adjusted at the torch handle. A nozzle is fitted at the outlet of the torch, where the gas mixture is ignited. The torch is also equipped with flashback arrestors.
Depending on the fuel being burned, and the oxygen:fuel ratio, the flame at the torch nozzle has slightly different characteristics. For the most common example of oxy-acetylene welding, a neutral flame is achieved when the ratio allows complete combustion. The flame has a hot (white) inner zone and a cooler (blue) outer zone. A reducing flame is achieved when the oxygen is cut back, and an oxidizing flame is achieved when the oxygen is increased past the neutral point.
The flame is directed at the metal to be welded to heat it. The combustion gases from the flame (such as carbon dioxide) provide a shield around the weld pool. Fusion between the metal components can take place without a filler material, but generally, a filler material is used. This may be in the form of a consumable wire that is fed continuously and melted into the weld pool to provide material to build up the weld. The flame is then moved on, and the metal can cool and solidify.
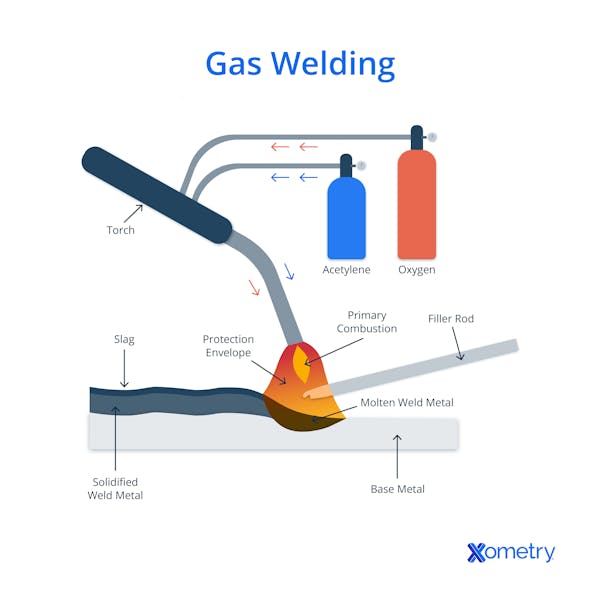
What Are Some Applications of Gas Welding?
There are many different applications of gas welding, as it is one of the oldest commercial welding techniques. Some areas in which gas welding can be applied have seen other types of welding (particularly arc welding) rise in popularity, but gas welding is still the first choice in multiple sectors. Listed below are some examples:
- Repair Works: Gas welding is frequently used to repair existing metallic components. The small size of the torch (compared to other types of welding equipment) and its ease of manipulation make gas welding a good choice when carrying out repairs in awkward positions. It is also popular in rural and agricultural areas, as an electrical connection is not necessary.
- Welding Thin Sheets of Metal: Gas welding is well suited to welding thin sheets of metal, as the heat input can be easily controlled by the handling of the torch.
- Plumbing and HVAC: The joining of copper pipes for plumbing and HVAC systems is widely done by gas welding or brazing. This is true for both domestic and industrial pipe fitting.
- Automotive Repair: Gas welding is used for repairing automotive systems such as exhausts, frames, and bodywork. It allows control over the heat input and is therefore chosen for delicate repairs.
Summary
Xometry provides a wide range of manufacturing capabilities including CNC machining, 3D printing, injection molding, laser cutting, and sheet metal fabrication. Get your instant quote today.
Disclaimer
The content appearing on this webpage is for informational purposes only. Xometry makes no representation or warranty of any kind, be it expressed or implied, as to the accuracy, completeness, or validity of the information. Any performance parameters, geometric tolerances, specific design features, quality and types of materials, or processes should not be inferred to represent what will be delivered by third-party suppliers or manufacturers through Xometry’s network. Buyers seeking quotes for parts are responsible for defining the specific requirements for those parts. Please refer to our terms and conditions for more information.
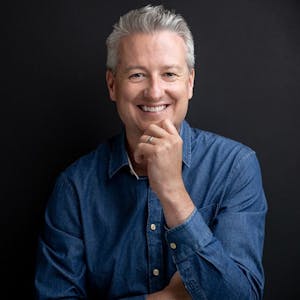