Laser cutting reflective materials can be challenging because the surface can cause the laser to reflect coherent, high-energy beams in unexpected directions. This can damage the laser optic head, but more importantly, it creates a user hazard. It is important to take appropriate safety measures when laser cutting reflective materials, such as wearing appropriate protective gear and ensuring that the laser cutting area is properly ventilated. With high-value workpieces (silver, gold, platinum, etc.), using a precious metals specialist cutting service can reduce costly mistakes. Some general suggestions for laser cutting reflective materials are: use a high-power fiber laser, use laser pulses to reduce bulk heating, adjust feed rates according to material properties to balance heat input and cutting efficiency, and use argon or nitrogen assist to clear the cut. Listed below are the seven types of reflective materials for laser cutting:
1. Gold
Gold is particularly reflective in the frequencies of common laser types used for cutting. A few techniques can help produce high-quality cuts, including:
- Where possible, use a fiber laser.
- Use pulsed laser bursts to allow some cooling time. Additionally, use argon or nitrogen assist to accelerate cooling and quickly remove molten material.
- Use a specialist precious metals optics head to improve cut quality.
2. Silver
Silver requires similar precautions to gold. Pure silver is hard to cut in its cold state, requiring significantly more laser energy to initiate the cut. The reflection is reduced quickly by the onset of melting, but the cut is very difficult to start. Molten material absorbs IR better, so the cut can proceed once it is started. Start with a very slow feed rate, around 90% or lower of the maximum speed, to ensure the cut initiates properly before gradually increasing speed. Reduce the amount of “cold” material that the laser has to handle by setting the focus at the top of the target material. This increases energy levels and the wider kerf below cuts more easily as the material impacted by the laser is liquid. High-pressure oxygen can significantly improve cutting efficiency. However, oxygen can cause surface oxidation and discoloration, which may be undesirable for applications requiring a clean surface finish.
3. Copper
Pure copper is particularly hard to cut. In its cold state, pure copper is highly reflective of IR, especially for CO2 lasers, but fiber lasers (1.06 µm) achieve better absorption. Nd:YAG lasers absorb better than CO₂ lasers but remain less effective than fiber lasers for copper cutting. The reflected percentage drops off quickly once the metal melts, so the difficulty is in initiating the cut. Once melt has occurred, the laser is better absorbed (in the molten metal), carrying heat outwards and allowing the cut to advance. It is important to reduce feed speeds to give the beam time to initiate the cut. Dropping the feed to 10–15% below the maximum is likely a good starting point. Focus the beam on the upper surface of the material. Increased energy concentration will give the fastest cut initiation, and a partially melted cut area will absorb IR much more strongly. The use of high-pressure oxygen can greatly assist the cutting process. While copper oxide absorbs IR better than clean copper, excessive oxidation can degrade surface quality and affect downstream processing. For more information, see our guide on Copper.
4. Brass
Brass shares most of the cut difficulties of copper. But, it absorbs slightly more strongly in the fiber laser output frequency range, making cut initiation and rate slightly better. Brass laser cutting benefits from oxygen or nitrogen assist; oxygen enhances cutting speed through an exothermic reaction, while nitrogen prevents oxidation for a cleaner cut.
5. Bronze
Bronze is also a difficult material to cut because of the IR reflectivity of the solid material. The same strategies used for copper are required for bronze, although the IR reflectance of the copper is lowered a little by the tin alloying element.
6. Titanium
Titanium is very similar in laser cut behavior to stainless steel. It is recommended to use a high power setting, a slightly reduced feed speed (compared with similar thickness stainless steel) and argon assist to improve cut speed/quality. Argon is beneficial as it will reduce the yellow or bronze staining of oxidation at the cut, compared with air or even nitrogen assist.
7. Aluminum Material
Aluminum is widely acknowledged as more difficult to cut than stainless steel due to its high reflectivity. A fiber laser's main wavelength (1.06 µm) is relatively well absorbed. A surface coating can be effective with aluminum, so long as it doesn’t burn away before melting has started. The highest available power, combined with a high feed rate, generally yields the best results in cutting aluminum. Higher alloy content generally makes aluminum easier to cut. Meanwhile, pure, soft, ductile aluminum is the hardest to get good results from. For more information, see our guide on Anodized Aluminum.
How Difficult Is It To Cut Reflective Materials With a Laser?
Cutting reflective materials requires careful optimization but can be mastered with experience. If the machine is appropriate—i.e., equipped with a fiber laser (or an Nd:YAG in some cases), gas assist, and well-optimized settings—then even highly reflective materials can be cut effectively. But, it is not easy, and common home laser cutters, with limited gas assist and CO2 lasers, will not give good results.
Can You Cut Reflective Materials With a Laser?
Yes, reflective materials can be laser cut with the correct parameters, sufficient power, and experienced handling. With enough power and with a fiber laser, preferably with a cutting head developed specifically for precious metals (to withstand the high reflected energy), most materials that are highly IR reflective can be cut.
What Laser Cutting Technique Is Used To Cut Reflective Materials?
The best laser cutting technique to use on reflective materials is to use a fiber laser. These lasers deliver sufficient power to rapidly melt the material’s surface. Once liquefied, the material absorbs laser energy more efficiently, improving cutting performance. It is recommended to use a gas assist, such as nitrogen or argon, to prevent oxidation and help clear molten metal from the cut zone. A cutting head that is designed to handle reflective materials also works better for reflective materials. A surface coating can improve laser absorption at the start of the cut, particularly for CO₂ lasers, but it must remain effective until melting initiates. Reflectivity decreases significantly once melting begins, improving laser absorption. Trial adjustments to the feed rate and laser power are also advised to optimize for the cutting you are making.
It is possible to get satisfactory results with high-power CO2 laser equipment, but initiation of the cut requires a surface coating that improves the instant absorption spectrum to initiate melting. Once melt has occurred, the cut can proceed, but each start point will require the same issue to be addressed. For more information, see our guide on the Types of Laser Cutting.
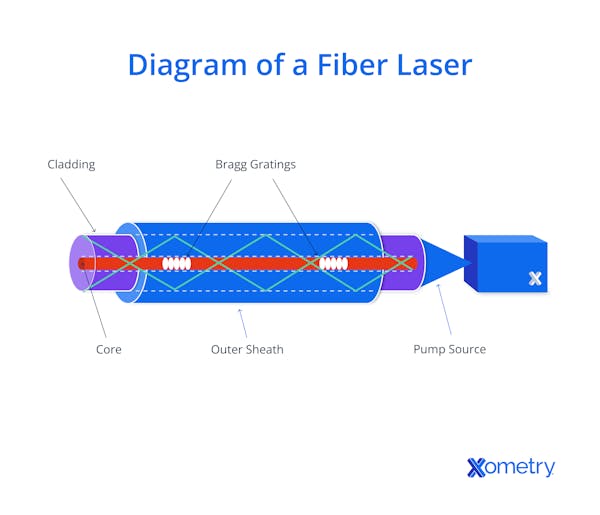
How Does Laser Cutting Reflective Materials Work?
Laser cutting reflective materials begins by applying sufficient power to melt a small area, allowing the cut to progress downward. Positioning the focal point at the upper surface maximizes energy concentration for efficient cut initiation. The absorption of IR increases greatly, and the laser can drill down once the surface has melted. Feed speeds are varied. For example, precious metals need pulsed laser energy and low feed rates, whereas aluminum benefits from higher feed rates. Use gas assist when laser cutting. Air assist helps remove molten metal but may introduce oxidation in some materials, affecting surface quality. Nitrogen or argon is preferred for reducing oxidation and maintaining a clean cut surface, especially in precious metals. Nitrogen assist clears cut debris and suppresses oxidation, preventing surface staining. Argon assist serves the same purpose as nitrogen but gives more protection against oxidation. Oxygen assist is beneficial for some metals, as oxidation enhances IR absorption and cutting efficiency.
What Are the Reflective Material Laser Cutting Settings?
The reflective material laser cutting settings are:
- High laser power (fiber lasers give the best results. CO₂ machines require a surface coating for absorption, which is not always feasible).
- Use pulsed power to reduce the heat-affected zone.
- The focal point should be carefully adjusted, often slightly below the surface, to improve cut penetration and stability.
- Very low feed rates (below 85%) may be needed at the start to overcome initial reflectivity before increasing speed.
- Once cutting begins, feed rates can be gradually increased. Each restart should begin at a lower speed.
- Air/inert gas/oxygen assist should be selected according to recommendations from the machine supplier.
Is Laser Cutting with Low Power Possible in Reflective Materials?
No, low-power cutting of reflective materials is generally not possible. If the material is very thin (foil rather than sheet) and a wide heat-affected zone can be accepted, lower-power machines are possible. In general, small, low-power machines—particularly those with CO2 lasers, are poorly suited to cutting reflective materials.
Can I Engrave in Reflective Materials?
Yes, a machine setup that can cut reflective materials can also engrave them. Engraving is generally easier than cutting since it requires lower power and less energy. Laser settings for cutting do not always translate directly to engraving. For best results, engraving requires lower power, controlled pulse settings, and proper focus adjustment.
Summary
This article presented reflective materials for laser cutting, explained what they are, and discussed their various applications. To learn more about laser cutting materials, contact a Xometry representative.
Xometry provides a wide range of manufacturing capabilities, including sheet cutting and other value-added services for all of your prototyping and production needs. Visit our website to learn more or to request a free, no-obligation quote.
Disclaimer
The content appearing on this webpage is for informational purposes only. Xometry makes no representation or warranty of any kind, be it expressed or implied, as to the accuracy, completeness, or validity of the information. Any performance parameters, geometric tolerances, specific design features, quality and types of materials, or processes should not be inferred to represent what will be delivered by third-party suppliers or manufacturers through Xometry’s network. Buyers seeking quotes for parts are responsible for defining the specific requirements for those parts. Please refer to our terms and conditions for more information.
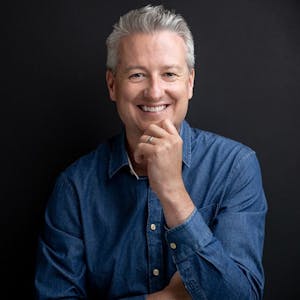