Bring Your Metal to the Next Level with Surface Finishes
Surface finishing is critical when your parts are visible or cosmetic rather than deep inside an assembly. Parts fresh off the waterjet or laser often have a burr on their bottom face, marks from handling, frosting near the cut line from overspray, and vestigial tabs from being held in place during cutting. Applying a finishing process to parts post-cutting will help you get parts that need minimal cleanup before installation. Now, with our expanded list of finishes, Xometry offers more options for your finished parts. Read on to see what finishes are available for sheet cut and sheet metal parts.
Standard, As-Cut Surface Finishes
This process is the most common option for parts that will not be seen or handled, or if you will be applying your finish once you receive the parts from Xometry. Standard finishes of flat sheet cut parts may not have a consistent cosmetic appearance. For example, overspray from the waterjet near the cut line, especially at pierce points and on the bottom face, may show a visible halo. There may be minor marks from handling on the top and bottom faces and from exposure to water. Similarly, lasers can discolor metal around the cut edges. Some metals also have mill marks from the manufacturer, which look like printed text.
On smaller parts where one or both dimensions are less than four inches, we have to tab the part to the sheet during cutting to keep them from ending up at the bottom of the waterjet tank. In these instances, we allow the techs to pop them off the sheets or ship you the sheet with the parts still attached. Tabbed parts are shipped still attached if the individual parts are so small they could easily get lost in packaging. If you want your parts to ship separated from the sheet, with the tabs ground down, you will want to select one of the finishing options below or select "Remove Tabs" and not raw parts when ordering.
Gallery: Standard, As-Cut Surface Finishes
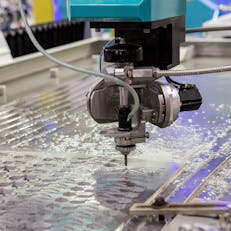
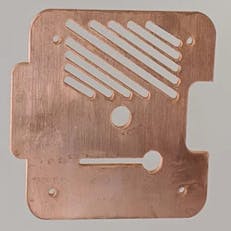
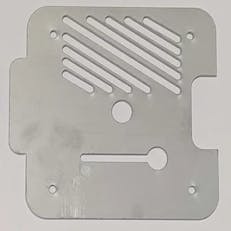
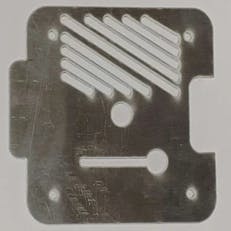
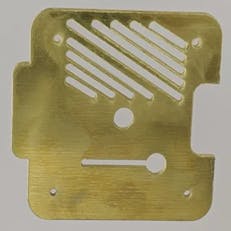
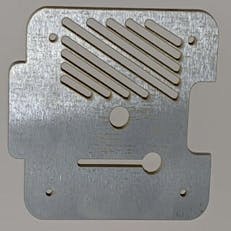
Bead Blast Finish
Bead blast finish removes burrs and surface imperfections while providing a fine grain finish across the entire part. We apply this finish by blasting the parts with a high-pressure stream of tiny glass beads. This option is a perfect match for waterjet cutting, as the surface resembles the cut edge produced by the garnet from the waterjet, meaning that the finish on the faces and cut edge are closely matched. Bead blast finish is an excellent option if you plan to paint your parts post cutting as the even "tooth" of the surface allows paint the nooks and crannies it needs to get a good hold of the surface. It is also a great option when looking for a matte finish. Before anodizing, bead blast and other matte finishes are ideal surface preparations, creating a nonreflective matte appearance.
The parts must fit in a blast cabinet to apply the bead blast finish. Parts must be less than 24 inches in both height and width. We recommend bead blast for parts over one square inch; any smaller, and the parts will be hard to hold and it will be difficult to apply the finish evenly. Parts given a bead blast finish will be removed from their source sheet and have their tabs ground off to make the edges as clean as possible.
Gallery: Bead Blast Finish
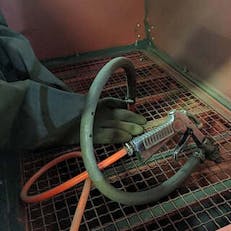
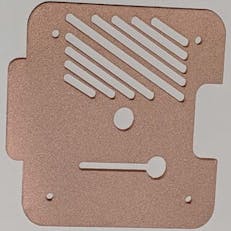
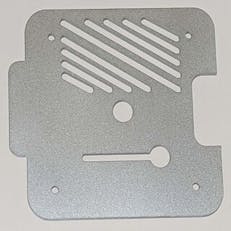
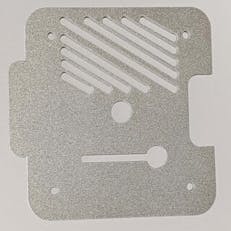
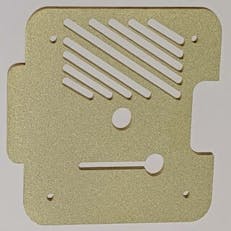
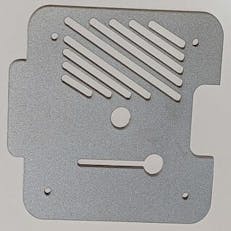
Sanding Random (Swirl) Finish
Sanding Random (Swirl) parts are finished on both the top and bottom faces with a powered non-woven abrasive pad in a random orbital pattern. Many of our signage clients use this finish for signs as the all-over brushed finish looks good in a wide variety of locations, and the texture left behind by the abrasive pad also provides a good "tooth" for paints to hold. This finish removes all light surface scratches, mill marks, and burrs. Orbital sanding finishes are best for parts above six inches. Tumbling (see below) is recommended for smaller parts. Like bead blast, sanding random swirl finishes are excellent for preparing surfaced before anodizing to create a matte non-reflective appearance.
Gallery: Sanding Random (Swirl) Finish
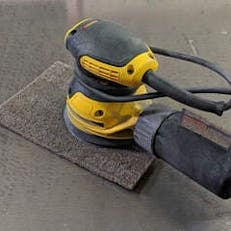
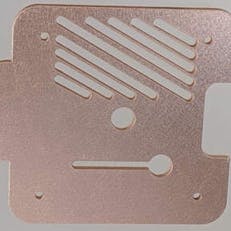
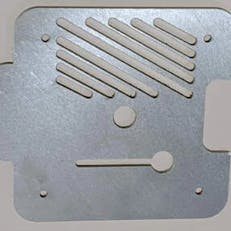
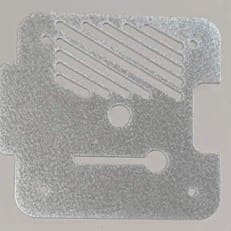
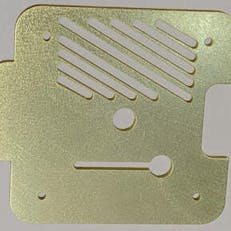
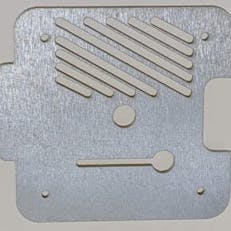
Sanding with Grain (Linear)
With the Sanding with Grain (Linear) Finish, both sides are finished with a non-woven abrasive on a belt sander, giving a brushed finish with parallel lines. While parts produced with this finish will look great on your wall and will make most clients satisfied, this is not a perfectly even #4 standard finish, as it is a manual operation. Due to the limitations of our machinery, parts given this finish must be less than six inches in either height or width. Sanding with the material's grain is our default, with grain direction specified through a technical drawing.
Gallery: Sanding with Grain (Linear) Finish
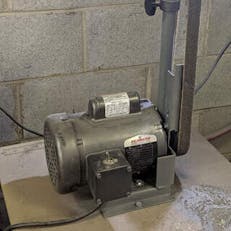
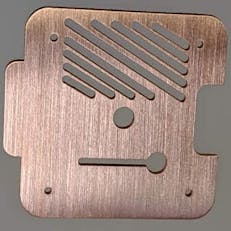
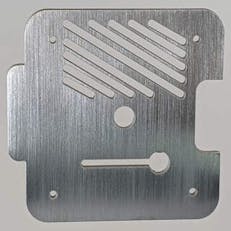
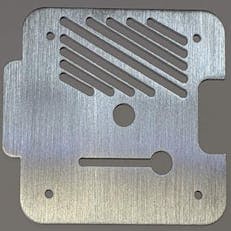
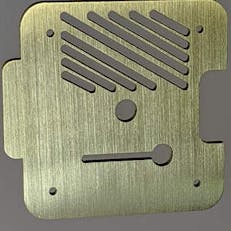
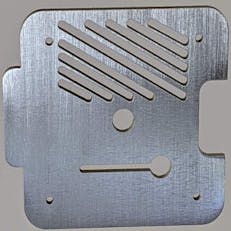
Tumbled Finish
Tumbled finishing is an inexpensive way to remove burrs, reduce surface marks, and produce an even texture on smaller parts. We place parts for tumbling in a vibratory tumbler with ceramic abrasive media. This combination of movement, water, and media puts a smooth and even surface all over the part's surface. Tumbling is excellent if you want to prep small jewelry parts or electrical connectors before further polishing or soldering. It is also a great way to process small parts for production work.
Parts with tumbling applied are typically smaller than four inches in both height and width. Also, the stock material must be strong enough to handle the tumbling process, so stainless steel parts must be 0.030" thick or thicker. Aluminum and other non-ferrous metals must be thicker than 0.045". With a Tumbled Finish, our techs will also remove any tabs by grinding so that they do not appear on the finished part.
Gallery: Tumbled Finish
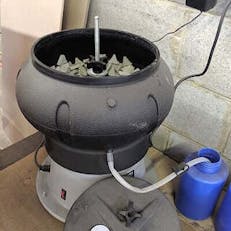
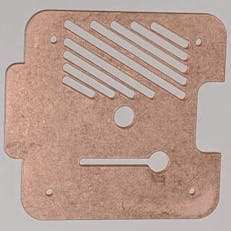
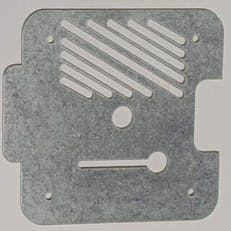
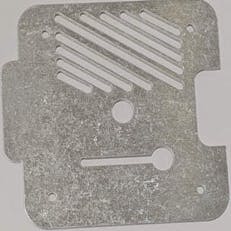
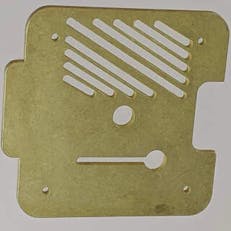
Additional Finishes
Like our other services, Xometry can offer turnkey finishing services like anodizing, chem-film, metal plating, powder coating, heat-treating, passivation, and even multiple custom finishes. These can be specified directly through our Xometry Instant Quoting Engine. Our techs will remove any tabs and burrs with any secondary surface finish by grinding them to not appear on the finished part.
Metal Reactivity
One aspect of metal finishing you should also be aware of is how reactive the materials you are ordering are and how mill materials are shipped. We attempt to keep our stock materials clean, dry, and minimize scratching when handling; however, the sheets we order from our suppliers do not have pristine surfaces. Waterjet cutting also uses abrasive materials and a cutting method that is not conducive to pristine mirror-polished sheets or sheets with coatings. Most suppliers process mill sheets with a thin layer of oil to minimize oxidization. Abrasive finishes remove protective coatings, which lead to oxidation, tarnish, or dulling. While not as challenging to remove as tarnish, the stainless steel parts will also show fingerprints from handling.
Most non-abrasive jewelry cleaners will remove the tarnish on copper and brass materials. At the same time, many of our partners use denatured alcohol or other solvents to bust fingerprints off of stainless steel. 000 steel or bronze wool helps scrub off oxidation on metals. Just be sure to work in the direction of the finish applied. A dab of clear microcrystalline wax worked into the surface of your part can keep it resistant to oxidization. Some metalworkers also suggest clear polyurethane and paste waxes as options for keeping oxidization away.
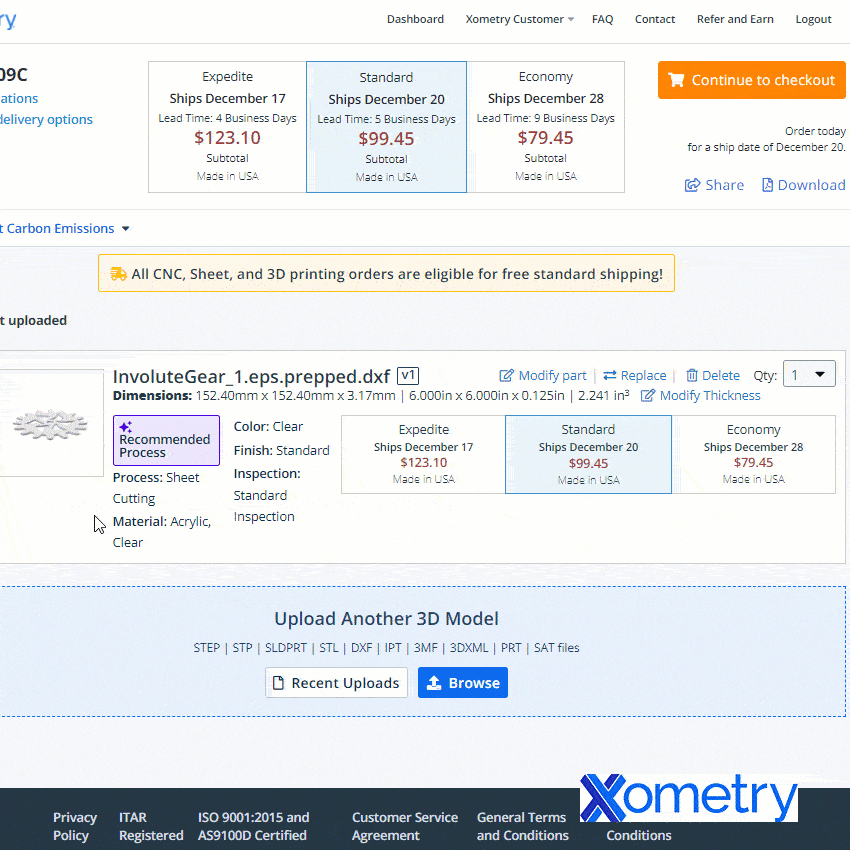
