For welding on a job site or some other more remote area away from your workshop, arc welding is the way to go. Welders like it for its portability, and whether they’re in the construction or automotive sectors, it’s a go-to for maintenance and repairs. When up against other types of welding, it’s seen as affordable and easy enough for both pros and hobbyists. Let’s get into everything else worth knowing about arc welding.
What is Arc Welding?
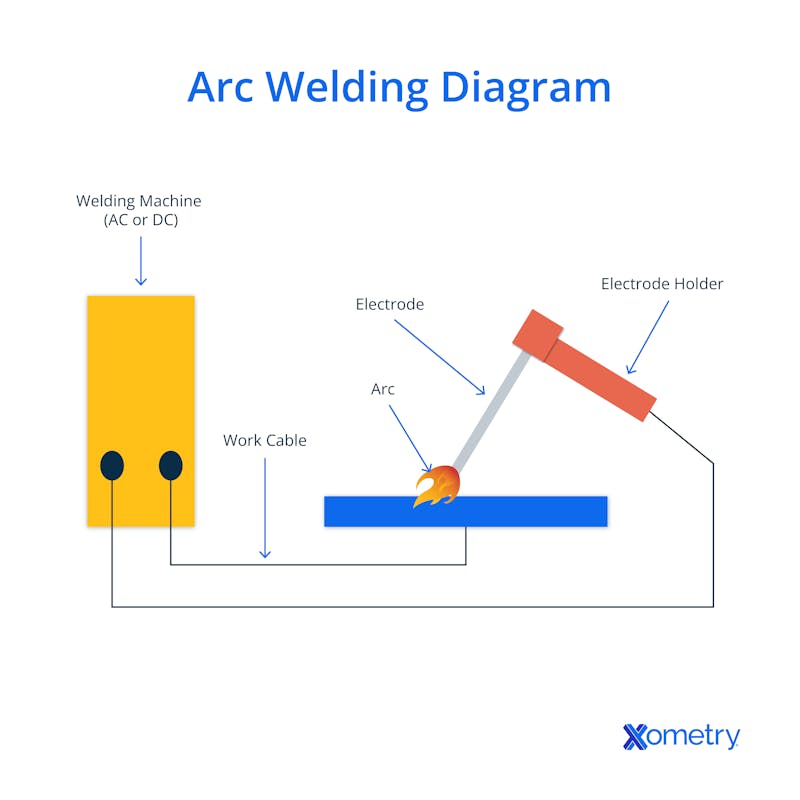
In 1987, Nikolai Bernardos and Stanislaw Olszewski filed for a patent for a carbon electrode for arc welding. From there the process evolved, with an American patent for a metal electrode in 1890, and coated electrodes in 1900. Arc welding uses a special rod that is electrically charged (an “electrode”) to join two pieces of metal together by forming an arc (or spark) in the air between them. The arc can reach temperatures over 5,432°F which gets the metal to its melting point pretty quickly, and it focuses all that heat on a very small, precise area of the metal surface. The two pieces of metal being joined melt together, often with a filler material from a consumable electrode to make a single molten mixture. After cooling and hardening, you now have a strong weld. Either you can move the electrode or it can be done automatically with a machine.
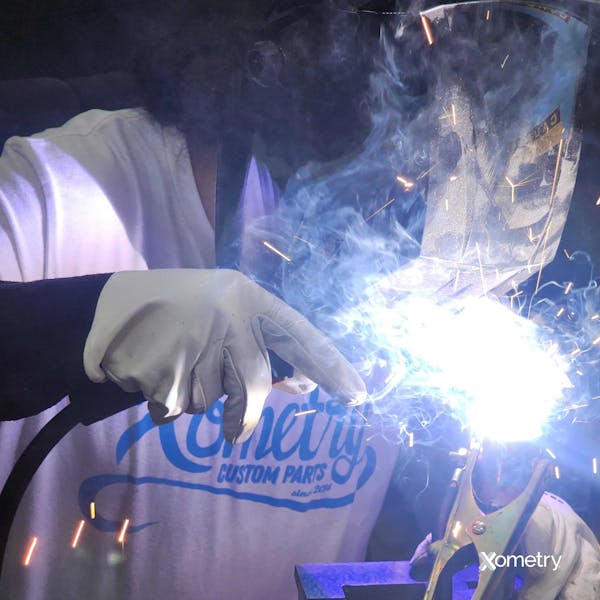
Electrode Types
The right electrode—either consumable or non-consumable—used in the arc welding process depends on the method of welding you choose. The latter helps to start up and control the welding arc, but doesn’t release any filler to the weld and doesn’t get used up in the process. Consumables melt along with the metal when the arc is active. For example, tungsten inert gas (TIG) welding is a tungsten-based electrode that moves along the joint to complete the arc, but if the weld needs filler it has to be fed in using a separate wire and a specific chemical composition. Some electrodes are coated with a thin layer of a deoxidizing agent, like copper, that helps to stabilize the arc. A heavier coating can also add a protective sleeve of inert gas around the arc, helping keep oxides or nitrides from forming in the weld.
The most important consideration when choosing the right electrode for the job is the material that you’re welding (there are different ones for different metals). Some can make any shape, while others can only do horizontal welds—you can find this info in each electrode’s code so you can choose the right one depending on your welding needs. The codes, set up by the American Welders Society, start with “E” and have four or five numbers after that which indicate the tensile strength, flux composition, and power supply needed.
Types
There are a few different types of arc welding to choose from. Details of these can be found in the table below.
Arc Welding Type | Electrode Type | Description |
---|---|---|
Arc Welding Type Shielded metal (or stick) | Electrode Type Consumable | Description This common and accessible type uses a hand-held electrode (AKA the stick) that melts as you weld away. It’s coated in flux, which also melts and forms a shielding gas that prevents oxidation or rust from forming. |
Arc Welding Type Flux core | Electrode Type Consumable | Description This is similar to stick welding, except the process is faster as it’s semi-automatic (the machine feeds the rod so you don’t have to hold it). This rod, too, is flux-coated. |
Arc Welding Type Metal inert gas (MIG) | Electrode Type Consumable | Description This uses a machine-fed electrode, and also creates a shielding gas that protects the melt from the atmosphere. |
Arc Welding Type Submerged | Electrode Type Consumable | Description This is for automated welding tasks, where the joint being welded is completely submerged in a protective flux, and is finished under it. |
Arc Welding Type TIG | Electrode Type Non-consumable | Description This uses a tungsten electrode that’s not consumable, so it needs a filler wire to complete the weld, as well as a shielding gas. It’s often considered the strongest arc weld type because of its high temperatures and slow cooling time. |
Arc Welding Types
There are many external factors that make any one arc welding type better or stronger than another, i.e., skill, how the metal was prepared, filler and electrode choice, and weld length and depth.
Materials
Five main metals are used in arc welding:
Steel
This is the most common arc welding metal in general and was actually one of the first metals used when the process was first invented. Stick welding with steel gives good quality welds, but you can use steel with pretty much any type of arc welding depending on the need.
Stainless Steel
With stainless steel, you can opt for TIG, MIG, or stick—but they all offer different results. MIG and stick are easier, but not the prettiest, whereas TIG takes longer, but you need more experience to successfully weld stainless steel in this way.
Aluminum
This is the most common metal for MIG and TIG welding and has high thermal conductivity, and a surface oxide layer with a higher melting point than pure aluminum. Aluminum isn’t the easiest to work with, but it’s nothing that arc welding can’t handle.
Magnesium
Often used to repair castings, magnesium needs special equipment for arc welding; the electrode needs to be sodium chloride-free to prevent corrosion. It’s also important to protect from the bright light magnesium creates when welded.
Titanium
This easy-to-weld metal is common in TIG but can also be used in MIG welding. The material has to be very clean before you start, though, so that the shielding gas can properly protect it.
How Xometry Can Help
We have a number of welding services, along with other manufacturing and fabricating solutions. If you’d like to know more, please reach out to one of our reps who will be glad to assist you or get a quick and free instant quote today.
Disclaimer
The content appearing on this webpage is for informational purposes only. Xometry makes no representation or warranty of any kind, be it expressed or implied, as to the accuracy, completeness, or validity of the information. Any performance parameters, geometric tolerances, specific design features, quality and types of materials, or processes should not be inferred to represent what will be delivered by third-party suppliers or manufacturers through Xometry’s network. Buyers seeking quotes for parts are responsible for defining the specific requirements for those parts. Please refer to our terms and conditions for more information.
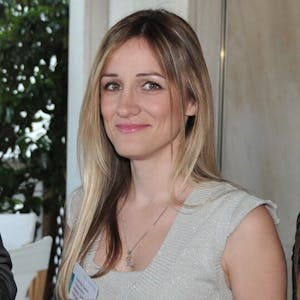