Mylar® is a polyester film that is widely used due to its exceptional mechanical and chemical properties. It is so popular that it has become nearly synonymous with any plastic film. Mylar is used in numerous applications, from helium-filled balloons and food packaging to electrical and thermal insulators. It was first developed in the mid-1950s by the companies Imperial Chemical Industries (ICI), Hoechstand, and DuPont. It is a registered trademark of DuPont Teijin Films. This article will define Mylar film, describe how it’s made, discuss its properties, and give examples of Mylar applications.
What Is Mylar?
Mylar is a plastic film that is coveted for its useful properties, including: chemical and dimensional stability, electrical insulation, impermeability, high tensile strength, reflectivity, and transparency. While the term Mylar is often used to describe any plastic film, it’s not the only PET film produced by DuPont Teijin Films. Trade names for other popular PET films include Melinex® and Hostaphan®.
What Is Mylar Made Of?
Mylar is made from polyethylene terephthalate (PET). The material is also known by its scientific name BoPET (biaxially-oriented polyethylene terephthalate). Here's how Mylar is fabricated:
- PET polymer is melted and extruded onto a chilled drum roller to form a film.
- The film is stretched biaxially, in the machine (or feed) direction, and in the transverse (width) direction. This is achieved by feeding the film over a series of rollers and then into a stenter frame where it is stretched in the transverse direction. This stretching process serves to orient the PET molecules in such a way as to enhance the film’s mechanical properties.
- The film is heated to 200°C (392°F) to stabilize its structure and to ensure that it does not shrink at temperatures below the original heat set temperature.
At the end of the fabrication process, the Mylar film is so smooth that it tends to stick to itself. Mylar material is often coated with silicon dioxide (SiO2) to reduce stickiness. Additionally, Mylar can be coated with evaporated gold, aluminum, or other metal using a physical vapor deposition process to reduce transparency, increase reflectivity, and make it less permeable to gases.
What Are the Properties of Mylar?
The versatility of Mylar, and its ability to retain its properties across a wide temperature range (-94°F to 302°F or -70°C to 150°C), make it ideal for a variety of applications across different industries. Mylar can be used in extremely low and high temperatures (-418-392°F, or -250-200°C) as long as mechanical requirements are not too demanding. Extreme temperatures can cause degradation of Mylar’s tensile strength and ductility. The properties of Mylar are listed below:
- Tensile strength of 29 ksi
- Dimensionally stable over a wide temperature range
- Chemically inert, resistant to oils, solvents, moisture, and grease
- Low permeability—can be used as a barrier against most liquids and gasses
- Excellent thermal stability and a low thermal expansion coefficient of 1.7 × 10 –5 in/in/°C (9.5 × 10 –6 in/in/°F). This makes the material an excellent thermal insulator
- High electrical resistivity of 1018 ohm⋅cm, making it an excellent electrical insulator
- Reflective. If coated with metallic particles, its reflectivity contributes to thermal stability and aesthetic appeal
- If not coated, Mylar is transparent and can transmit 80-90% of radiation in visible and infrared spectrums. This can be desired for certain applications such as tags, and equipment labels
What Are the Uses of Mylar?
Mylar overall is a great material. Its strength and dimensional stability over a wide temperature range make it a versatile material. Its low permeability makes it great for food packaging, while its electrical properties make it a great electrical insulator.
Some common uses of Mylar are in:
- Flexible food packaging, such as: yogurt lids, potato chip bags, foil coffee pouches, and candy wrappers
- Product packaging for clothing, books, and other consumer products
- Product labels, stickers, and tags
- Thermal insulation for air ducts, tents, survival blankets, and other temperature-sensitive items
- Electrical insulation for wiring applications
- Decorative balloons, party decor, kites, and other items
Can Mylar Be Used in Laser Cutting?
Yes, Mylar can be cut using a laser. All available Mylar thicknesses are well within the capabilities of standard laser cutters. Its low thickness, coupled with its relatively low vaporization temperatures (662°F or 350°C) when compared to other plastics like Delrin®, make laser cutting Mylar easy and efficient.
What Are the Uses of Mylar in Laser Cutting?
Mylar is often processed by laser cutting because it is easy to cut and can be cut by even entry-level laser cutters.Mylar's durability and flexibility make it the perfect option for many plastic film applications. Its low vaporization temperature makes laser cutting the perfect option for processing Mylar products into the desired shape.The primary application of laser-cut Mylar is the fabrication of stencils for craft applications. However, laser-cut Mylar can also be used to create beautifully intricate patterns, shapes, and designs, or to create products such as food packaging.
For more information, see our guide on Laser Cutting.
How Is Mylar Used in Stencils?
Mylar is often used to produce stencils for craft and hobby applications. Laser cutting is a popular method to fabricate stencils because the laser produces accurate, clean cuts. While other materials, like cardboard and cardstock, can also be laser cut to produce stencils, they are not ideal to provide clean artwork. Additionally, these materials lack longevity and can easily be deformed.
How To Use Mylar for Making Stencils
To laser cut Mylar stencils, use low power and high cutting speed. This helps prevent the cut edges of the sheet from melting and vaporizing. The steps below describe in detail how to use Mylar for making stencils by laser cutting:
- Place a backer board, such as cardboard or cardstock, underneath the Mylar sheet. This will protect the laser work table or the surface directly underneath the laser from being damaged by the laser.
- Secure the sheet to the backer board using a glue stick, spray adhesive, or tape. Then, secure the backer board to the work table using tape or a clamp. This will prevent the sheet from shifting during laser cutting. It will also allow the finished stencil to be easily removed since the unwanted portions will stick to the backer board.
- Configure the laser system for cutting Mylar material. Cutting speeds should be sufficiently fast to avoid the material from melting excessively. However, the thickness of the sheet determines the power that must be used.
Table 1 below shows the recommended power settings and speeds for cutting various thicknesses of Mylar:
Sheet Thickness | Laser Power | Cutting Speed |
---|---|---|
Sheet Thickness 0.1 | Laser Power 7 W | Cutting Speed 150 mm/s |
Sheet Thickness 0.20 mm | Laser Power 8 W | Cutting Speed 150 mm/s |
Sheet Thickness 0.25 mm | Laser Power 9 W | Cutting Speed 150 mm/s |
Sheet Thickness 0.25 mm | Laser Power 9 W | Cutting Speed 150 mm/s |
Frequently Asked Questions About Mylar
What Is the Ideal Mylar Thickness for Laser Cutting Stencils?
The ideal Mylar thickness for laser cutting stencils is 0.1 to 0.2 mm. While all Mylarcan be laser cut easily with any laser system, thicker sheets are not ideal for stencils. This is because using stencils for drawing and art can be difficult if the stencil is too thick.
Is Mylar Expensive?
No, Mylar is not expensive. Mylar can be purchased in packs of individual sheets, in entire rolls, or as bags. Rolls as large as 4 ft x 100 ft can be purchased for as little as $50. A roll this large will furnish enough material to complete numerous projects.
Is Mylar a Reflective Material?
Yes, Mylar is a reflective material but can also be made with a matte finish, or can be made transparent. Mylar is often used for thermal insulation because of its reflective properties. It is used for items like food packaging and survival blankets, where heat retention is critical.
Is Mylar Chemically Reactive?
No, Mylar is chemically inert. It does not react with materials like oils and solvents. The material’s chemical inertness also makes it very easy to clean. Mylar is not only chemically unreactive, but it is also impermeable. This makes it a great barrier against gasses and odors.
Summary
This article presented Mylar, explained it, and discussed its various uses across different processes. To learn more about Mylar, contact a Xometry representative.
Xometry provides a wide range of manufacturing capabilities and other value-added services for all of your prototyping and production needs. Visit our website to learn more or to request a free, no-obligation quote.
Copyright and Trademark Notices
- Mylar® and Melinex® are trademarks of DuPont Teijin Films.
- Hostaphan® is a trademark of Mitsubishi Chemical Group.
Disclaimer
The content appearing on this webpage is for informational purposes only. Xometry makes no representation or warranty of any kind, be it expressed or implied, as to the accuracy, completeness, or validity of the information. Any performance parameters, geometric tolerances, specific design features, quality and types of materials, or processes should not be inferred to represent what will be delivered by third-party suppliers or manufacturers through Xometry’s network. Buyers seeking quotes for parts are responsible for defining the specific requirements for those parts. Please refer to our terms and conditions for more information.
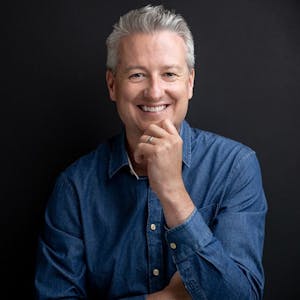