TIG (tungsten inert gas) welding is a common method used in manufacturing to join pieces of metal together. It’s a form of GTAW (gas tungsten arc welding) and is used for many things, including assembling exhausts, fuel lines, tanks, and structural and engine parts in aerospace and car manufacturing. It’s a go-to for many because it can make strong and reliable high-quality welds that are aesthetically pleasing. The process produces very minimal splatter, so there’s a lot less post-weld cleanup needed.
We’ll explain exactly how this welding method works, how it’s different from other popular welding types, like MIG (metal inert gas) and laser welding, and also, how you can do it!
What is TIG Welding?
TIG welding makes joints in metals via a tungsten electrode in the torch. This electrode produces a very high-temperature arc (up to 11,000°F) that melts the metal and creates a weld pool. A filler metal can also be used if you want to make an extra strong joint. The reason the method has the “IG” in its name is because it uses a non-reactive shielding gas (usually argon) to protect both this electrode and the area you’re welding from any contamination in the air. If it weren’t for this gas, the metal could form rust or oxidize.
The gas is stored in a cylinder, and the flow of the gas as well as the arc formation is controlled by the TIG torch. In addition to the torch, the electrode, and the shielding gas, a TIG welding system also has a power source for the electricity it needs to operate and a foot pedal or some type of hand control to control the current. You can see all the different parts of a TIG welding system in the diagram below.
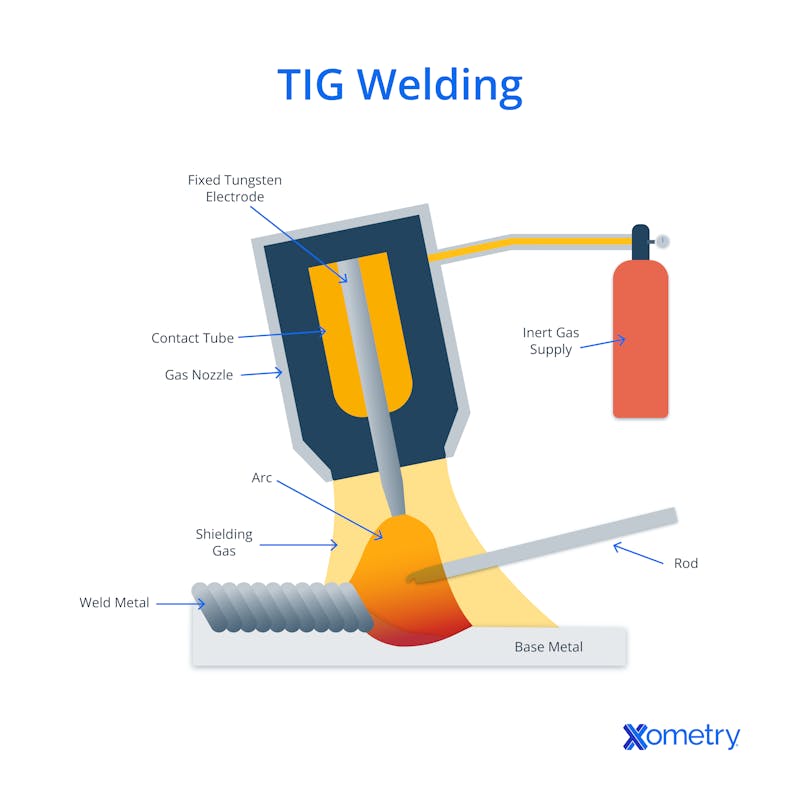
One of the main reasons this welding method is at the top of many manufacturers’ fabricating methods list is that it’s compatible with many different nonferrous metals, including copper, aluminum, and steel (like carbon and low-alloy). If you’re TIG welding stainless steel, you’ll want to use a DC machine to give the electrode negative polarity so that the metal can stay corrosion-resistant. The best way to do this is by connecting the torch to the welder’s negative terminal and the ground clamp to the positive terminal.
TIG is the most common welding method used on nickel alloys because the material needs the gas protection for best results. With this material, argon or helium (or even a mix of the two) is used, but an argon-hydrogen gas mix will be best for pure nickel. Another alloy that is typically TIG welded is chromium-molybdenum (chromoly), which is used to make bicycles and motorbikes because other welding methods might cause cracks in the metal. It can even work on thin metals, thanks to the precise heat control offered, but it won’t be the best option if you have thick materials to weld because of its slow deposition rate.
TIG Welding vs. Other Methods
The main difference between TIG and MIG welding is that the latter has a consumable electrode that doubles as the weld filler. A TIG electrode just generates the arc and if you needed a filler metal, you’d have to add a rod or some type of hand-held filler. With laser welding, a high-powered laser beam is used to make the melt.
In comparison to MIG welding, TIG tends to take a little longer and more skill is needed. The get-up is also a bit more expensive than MIG or oxyfuel welding equipment. Like MIG, laser welding is also faster than TIG and it can make more compact welds because it has a smaller heat-affected zone. Laser can also work with other materials like plastics, not just metals.
How To TIG Weld
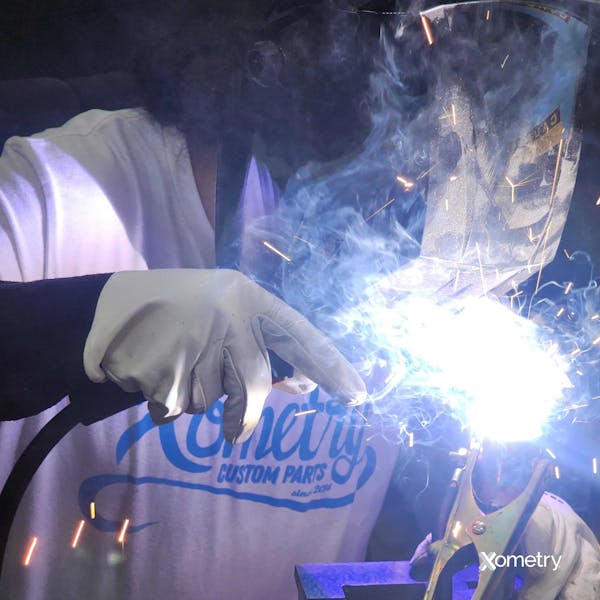
To make the best welds with this process, here’s an easy step-by-step guide to TIG welding:
- Get all your necessary gear together (the welding machine, electrode, filler rod (if necessary), gas cylinder, and all your PPE, like gloves and welding helmet)
- Clean the workpiece thoroughly with a wire brush or solvent
- Set up the welding machine and adjust its settings according to your metal’s type and thickness
- Grip the torch at an angle of around 70–80°, then lift it just a touch, keeping the tip 1/16 to 1/8 inches from the workpiece (don’t let the tungsten come into contact with it; this could cause contamination and you’ll have to regrind the tungsten)
- A steady hand is needed so that you can move the torch and direct the arc along the weld path in a controlled way
- Adjust the amperage (and filler rod if you have it) to control the heat
- Keep the torch as close to the workpiece as you can for better control and visibility
- Once you’ve finished, slowly reduce the amperage and let the weld cool down
- When it’s cooled, check for any defects, and if you need to make any adjustments or repairs, this is when you’d do them.
How Xometry Can Help
When it comes to welding, our weldment services are a hit with our customers. Whether you need TIG, MIG, shielding, spot, or laser welding, let us help you out. If you upload your design on our site, you can get a free instant quote with absolutely no obligation. You can also reach out to one of our reps anytime you like.
Disclaimer
The content appearing on this webpage is for informational purposes only. Xometry makes no representation or warranty of any kind, be it expressed or implied, as to the accuracy, completeness, or validity of the information. Any performance parameters, geometric tolerances, specific design features, quality and types of materials, or processes should not be inferred to represent what will be delivered by third-party suppliers or manufacturers through Xometry’s network. Buyers seeking quotes for parts are responsible for defining the specific requirements for those parts. Please refer to our terms and conditions for more information.
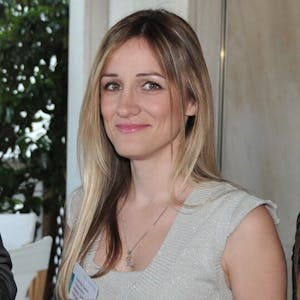