Overview
Though often unassuming, laser tube cutting projects can be quite complex with many cuts, such as miters and copes. Cuts are often modeled normal to the edge using standard extrude and cut features in CAD. However, the actual cut path for laser tube cutting is 90 degrees, or normal to the surface of the tube. This article helps you understand what a normal-to-surface cut is and what to expect when ordering laser tube cutting services.
Normal-to-Surface Cuts
A normal-to-surface cut is perpendicular to the outside surface of the tube. Normal-to-surface cuts have many aliases, including normalized cut, 90-degree cut, or true cope. Whatever their name, normal-to-surface cuts are the industry standard for laser tube cutting.
Quoted laser tube cutting projects will always assume the cuts in your model are normal to the surface. Normal-to-surface cuts can decrease lead times and price. This is because normalized cuts allow the laser head to remain at a 90-degree angle to the tube surface at all times during manufacturing, giving a consistent cut thickness on the tube regardless of the feature.
Normal-to-Edge and Other Cuts
While possible, performing normal-to-edge cuts would require a manual review for quoting and increase lead time and price. This is because the laser must have an additional axis to tilt and cut the tube at an angle, increasing the time to cut features on the tube. Other types of cuts, like post-machined cuts, would also require a manual review. Maintaining a 90-degree angle standard reduces cutting difficulty and excessive heat build-up caused by making sharp cuts in thick-walled tubing.
Differences Between CAD and a Normal Cut Surface
It's important to make sure your CAD models resemble your end part. CAD software, such as SolidWorks, likely won’t assume normal to surface cuts. Many SolidWorks weldment tools and other tube modeling workflows do not normalize surfaces automatically. It takes a few extra commands to normalize your tube cuts, but this practice can reduce manufacturing issues and confusion.
Designing Normalized Cuts
There are many ways to normalize your cuts in CAD. It’s a good idea to get familiar with different techniques, as the same technique won’t always work for different cuts. You can learn how to normalize different cuts in the following guides:
- Designing Normalized Coped Cuts on Round Tube
- Designing Normalized Mitered Cuts on Round Tube
- Designing Normalized Mitered Cuts on Rectangle Tube
Pro Tip: Wonder if a cut is normal to surface? Rotate your model and imagine if a laser could make every cut perpendicular to the surface of the tube. If not, that surface may look different when fabricated.
Image Gallery
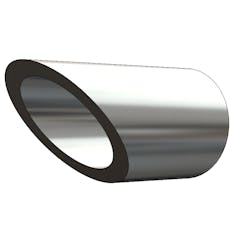
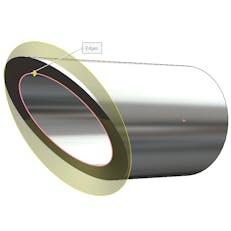
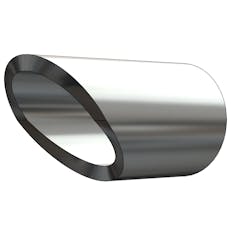
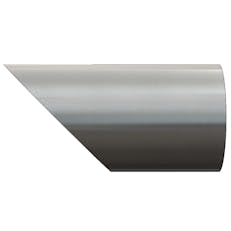
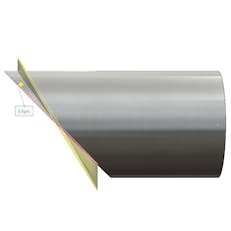
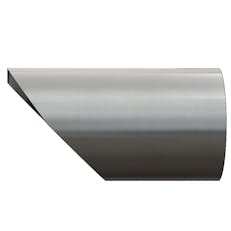
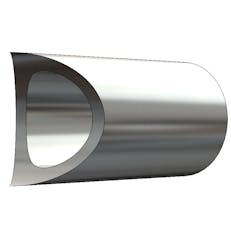
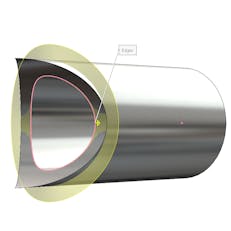
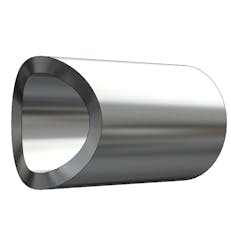
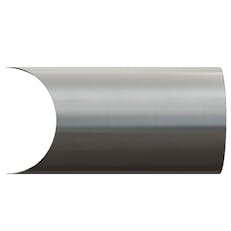
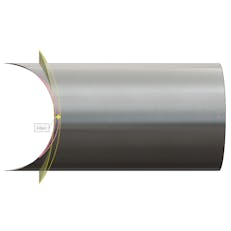
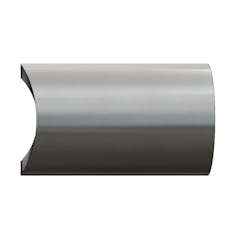
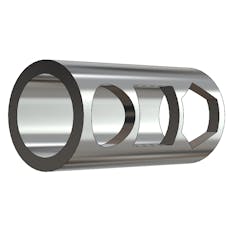
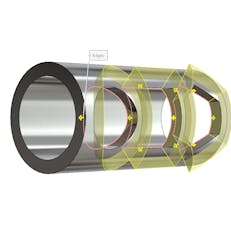
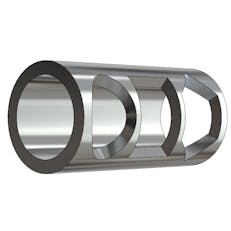
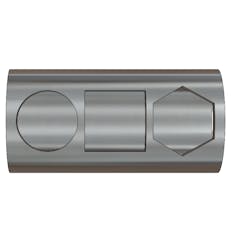
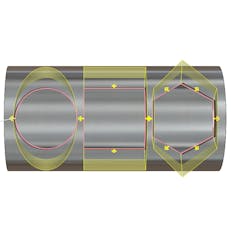

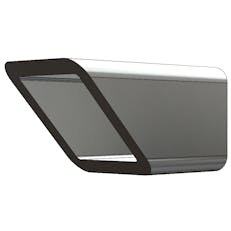
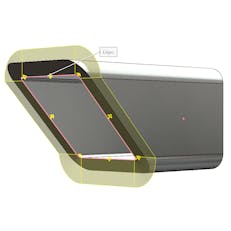
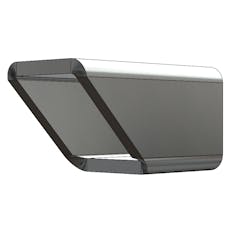
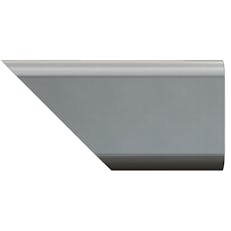
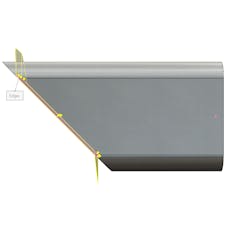
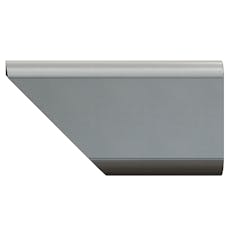
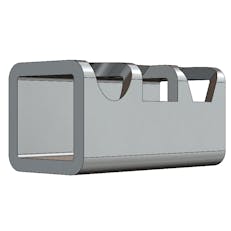
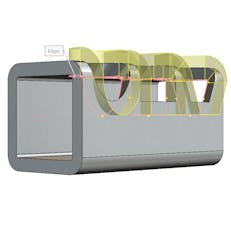
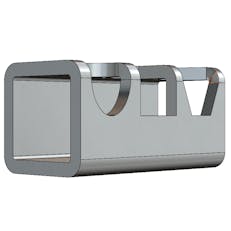
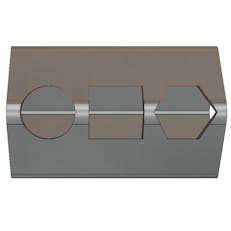
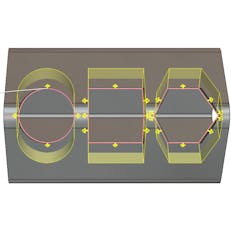
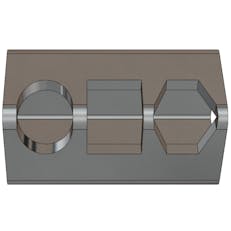
FAQ
What is a normal to surface cut?
A normal to surface cut is a cut that is perpendicular to the surface of the tube. These cuts are industry standard and can reduce lead time and price of laser tube cutting projects.
Do I need to model my cuts normal to surface?
No. But modeling can help you understand how your design will look after fabrication. To learn how to model a normal to surface cut in SolidWorks review the following guides:
How do I normalize my cuts in CAD?
There are many techniques for normalizing tube cuts in CAD. To learn our favorite methods for modeling a normal to surface cut in SolidWorks review the following guides:
What if I need my part cut edges exactly as designed?
If you need to retain features that would not resolve in 90-degree cutting you can request a manual review and our team will update the quote.
How do I know if my cuts are normalized?
Rotate your model and imagine if a laser could make every cut perpendicular to the outside surface of the tube. Check out the gallery above for more visuals.
Will a normalized cut affect square or rectangular tube?
Sometimes. On flat faces the features will work as-designed assuming they aren't interfering with the perpendicular wall.
Xometry's Tube and Fabrication Services
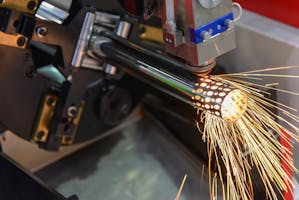
Laser Tube Cutting Services
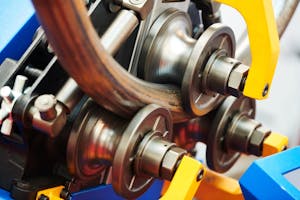
Tube Bending Services
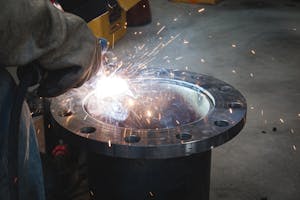
Custom Online Weldment Services by Xometry
