Every product has a story, from simple everyday consumables to complex machines held together by dozens of custom interlocking parts. Every product is intentionally built from a series of hundreds of decisions; a carefully selected combination of materials, discerning design choices, and shrewd business decisions. If you want to develop a product, you will need many things, including at least a well-executed plan, intensive conversations between internal stakeholders, and the tenacity to overcome the problem-solving process.
In this article, we will guide you through the seven stages of the product development process. You will also find out how Xometry, the world’s largest digital manufacturing marketplace, is equipped to provide you with comprehensive manufacturing services and development guidance, no matter what stage you find yourself in. Finally, we will demonstrate how Xometry can help you in each stage of product development by highlighting relevant case studies from entrepreneurs, engineers, and designers like you.
P.S: Want a quick tip? Click on the image above to find a story with relevant product development examples from a customer like you.
The Seven Stages of the Product Development Process
The product development process refers to the series of steps a development team undertakes to turn a fledgling concept into a final competitive product that resonates within a target market. A product manager has many things to consider before they begin the product development process, including:
- What is the product concept or the general idea behind their proposal?
- How are they going to develop a product that stands out in the market? Does it have a unique value proposition?
- Who is their target market, and what marketing strategy (or strategies) will be employed to reach them?
- How many resources (financial, social, time, etc.) can be invested in this new product development process?
Once a product manager has laid out the basics of their product development strategy, they are ready to begin enacting the 7 product development stages:
- Idea generation
- Prototyping
- Business Analysis
- Pilot Line Manufacturing
- Testing
- Scaling
- Mass Production
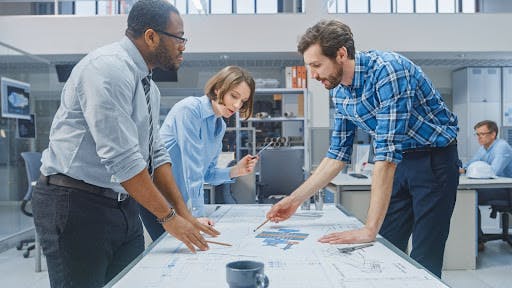
Before any product can be physically manufactured, it first must be built in the mind. While this stage of the product development process may require significantly less financial investment than any other step, it still requires a lot of mental resources. This first stage is not just about coming up with a unique product but taking the initial idea through a concept development process.
This part of idea generation helps you weed out novel and valuable product ideas from those without a compelling value proposition. This process includes:
- Brainstorming to create a pool of potential product or service concepts. E.g., what problem is your product solving?
- Performing customer research to target your ideal customer.
- Estimating the market potential for your product or service concept.
- Creating a prototype for your product.
- Devising a marketing strategy.
- Performing test marketing.
- Evaluating your results. (Source)
After following these steps and laying out a clearly defined product roadmap, the development team should focus on developing a minimum viable product, or MVP, to test their product concept. Unfortunately, this can introduce a slew of difficulties:
- How will they manufacture the initial prototype?
- What manufacturing process will be the best fit for their product?
- How much time and money will it take to test these product ideas?
How Xometry Can Help
With Xometry, you have access to a range of manufacturing solutions to help you develop initial prototypes, work through the stages of concept development, and scale up to high volume production. You can create custom parts using over 70 materials and 15 manufacturing processes, each with its own advantages.
With the Xometry Instant Quoting Engine, you can get quotes within seconds for processes like CNC machining, 3D printing, sheet metal fabrication, urethane casting, and more. Simply upload a 3D CAD file and instantly receive pricing, lead times, and design-for-manufacturing feedback.
Xometry’s expert engineering team can even provide direct consultation. They are ready to advise you in this early stage of the product development process by helping you choose the right manufacturing process and material to test the core functionalities of your minimum viable product. This may even span iterative prototyping or multiple processes to simulate results.
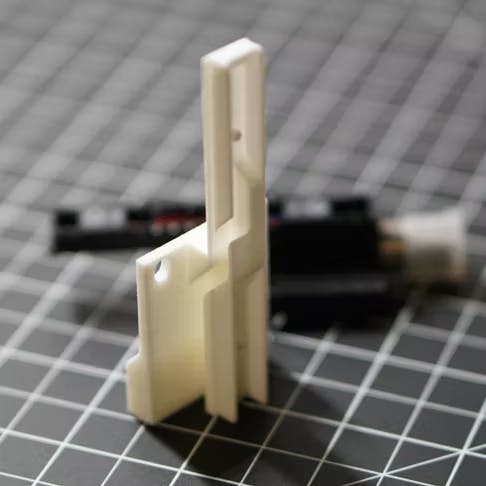
Case Study: An Industrial Automation Company Rethinks Fixturing with 3D Printing
Melton Machine & Control Company, an industrial automation solution provider, plays a pivotal role in the automotive value chain by crafting tools, fixtures, and machines to hold parts steadily in place while they are welded. Weston Miller, a mechanical design engineer at the company, needed to design a more durable solution for a new switch assembly.
Miller, who is well-trained in 3D printing, decided to try SLS nylon 12 as a 3D printed material for his switch housing, knowing it would provide thermal-resistant solid properties alongside the ability to resolve small features. After getting an instant quote from Xometry and consulting with the platform’s project engineers, he said he became “a Xometry convert” and was able to produce a successful final product.
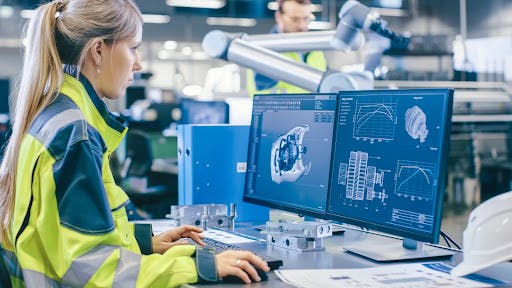
In this stage of the product development process, a product development team moves beyond concept development and begins developing a physical minimum viable product. In this stage, concept testing occurs with a final product prototype. These prototypes provide critical information to engineers on the development team, helping them make crucial design choices before moving to higher fidelity models that will be used for functional testing and production.

Traditional manufacturing methods can require a considerable time investment before a product manager can get a physical prototype in hand. Thankfully, Xometry’s 3D printing service is particularly well suited to this task. One of the many advantages of 3D printing is its ability to rapidly manufacture prototypes. Xometry empowers product managers to design prototypes with speed, accuracy, and affordability. Our global supplier network can manufacture multiple designs of a prototype all at once, allowing for quick revisions. Rapid prototyping can test a variety of designs and materials, mitigating the risk that could occur if a project moved forward without this crucial early feedback.
A quick proof of concept test allows our engineers to quickly and affordably create a proof of concept for your idea. Some of the most commonly used manufacturing methods to provide an initial prototype include:
Manufacturing Process | Cost | Lead Time | Use Cases |
---|---|---|---|
Manufacturing Process | Cost $ | Lead Time 1 day | Use Cases Basic form and fit verification |
Manufacturing Process | Cost $ | Lead Time 1 day | Use Cases Higher resolution form and fit |
Manufacturing Process | Cost $ | Lead Time 1 day | Use Cases Higher resolution form and fit |
Manufacturing Process | Cost $ | Lead Time 4 days | Use Cases flat cut parts in a wide variety of plastics, metals, gaskets, and composite options. |
Manufacturing Process | Cost $$ | Lead Time 4 days | Use Cases A prototype in the end material for preliminary durability tests |
Manufacturing Process | Cost $$$ | Lead Time 4 days | Use Cases A prototype in the end material for preliminary durability tests |
Manufacturing Process | Cost $$$ | Lead Time 15 days | Use Cases High-fidelity prototyping |
Many of these 3D printing processes can produce prototypes at low costs. When 3D printing isn't a feasible option, and proof of concept prototypes need to be created in materials that can validate physical properties like weight and surface finish, Xometry can use other manufacturing processes like CNC machining, sheet metal fabrication, and injection molding. Keep in mind that these manufacturing processes have higher costs due to their machine and tool set-up, and even the simplest will cost more than typical 3D printing projects.
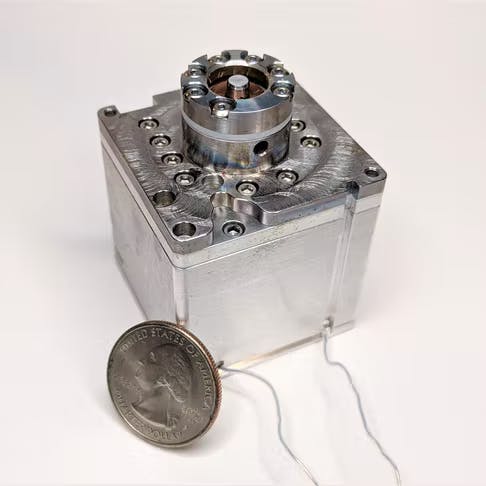
Applied Ion Systems (AIS) is changing the aerospace industry by creating tiny electric propulsion systems that lower the barrier of entry for small teams looking to break into the market. AIS needed to find a way to source increasingly complex prototype parts while keeping costs low.
By ordering CNC machined and 3D printed parts from Xometry, AIS dramatically lowered its prices and lead times. Xometry’s network capabilities empower companies like AIS, helping them with rapid prototyping projects and empowering them to move through the product development process more quickly.
Stage 3: Business Analysis
At this stage of the product development, you have moved past concept development, you have a prototype in hand, and you are ready to start investing more resources to determine if you want to stick with the existing product design or if it is time to create a new product development process.
In this stage, you will want to ask yourself:
- Who is your target audience based on market research performed by you or your marketing team?
- Have you conducted any market research with your target market, and what consumer feedback did you receive?
- How much do you need to invest in R&D? For most businesses, business analysis and R&D are necessary to stay ahead in international markets.
This is one of the most critical stages of the product development cycle. Given the investment required in order to move to the next stage of the product roadmap, do you want to continue investing time and resources into product development or should you consider alternative paths forward?
How Xometry Can Help
With the Xometry Instant Quoting Engine, you can get instant pricing and lead times for your designs, helping you to make the right business decision for your company. Unlike traditional manufacturing, where you have to go back and forth to haggle every time you start a new product development process, you can get instant feedback from our AI-powered digital marketplace.
Our artificial intelligence uses a machine learning approach to accurately and quickly estimate prices for part designs, generate lead times, and match you with the right seller. Using data gathered from other transactions across our marketplace, we continually improve prices across a huge range of product designs, material selections, and project sizes.
The technology from the Xometry Instant Quoting Engine has been added to a variety of third-party CAD software platforms, which allows engineers to flesh out their product idea from an easy-to-use computer program. If you are interested in downloading an app that can provide initial feedback, pricing, and lead times for free, check out Xometry’s add-ins for SOLIDWORKS, Autodesk Fusion, and Onshape.
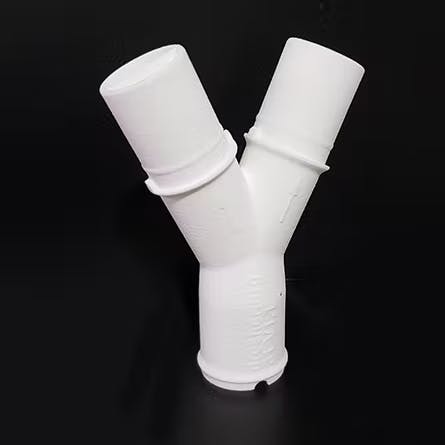
In product development, some designs grow into successful products while other ideas never translate to a finished product. Product development processes can end for several reasons: impractical manufacturing requirements, high costs, or existing competitive products that already appeal to your target customers. Rapid prototyping using 3D printing allows engineers to evaluate product designs for functional tests or market research quickly. This helps to save thousands of dollars by identifying needs and getting measurable feedback early before wasting time and money.
Read on to discover how a group of engineers and medical experts joined forces to fight the first wave of COVID-19 by rapidly prototyping a medical device. Xometry manufactured 9 different prototype designs in under 3 weeks, offering expert advice and rapid production capacity that provided critical information for project engineers to decide whether or not to move forward with the designs.
Stage 4: Pilot Line Manufacturing
Before you begin a full-scale product launch, you’ll want to create the first pilot line of your product. A pilot line is an initial batch of your product that helps you see how it performs in a real-world setting among your target audience. Pilot production of parts can provide crucial feedback regarding your product development and allow you to improve your product or pivot before incurring significant capital expenses.
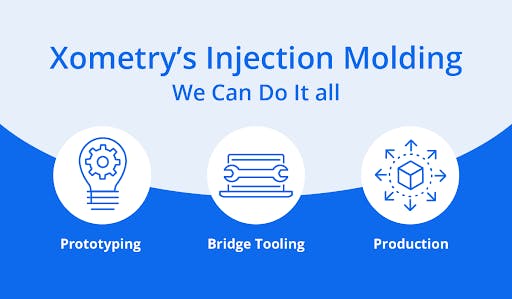
For those working toward full-scale production, Xometry’s injection molding service is a fantastic option, as it is the cheapest way to produce plastic parts at scale regardless of production stage. Xometry’s team of experienced engineers will manage the process for you, handling all the complexities related to prototype molding, bridge tooling, high-volume production, and everything in between! Leave the sourcing, tool design, fabrication, problem-solving, and logistics to the Xometry experts.
Xometry’s manufacturing network offers some of the fastest lead times in the industry, helping you hit milestones in weeks, not months. Xometry and its manufacturing partners incorporate scientific molding techniques and advanced processes using high-volume tooling.
Once your project is kicked off, Xometry will build a high-quality injection mold. Once the mold has been created, the team will send out part samples, called T1s, for approval. After the samples are approved, Xometry moves forward with production and delivers final parts straight to your door. Best of all, you own your tool, which allows you to easily reorder parts past your pilot line as demand grows.
The chart below offers a quick comparison to other Xometry tooling services and highlights some of the advantages typically associated with a tool designed for high-volume production.
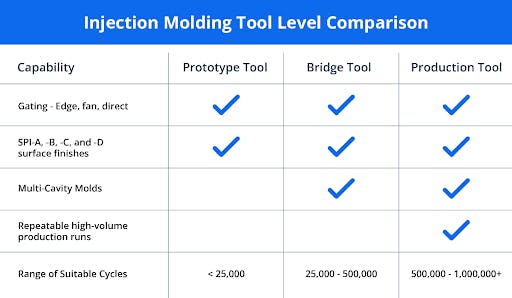
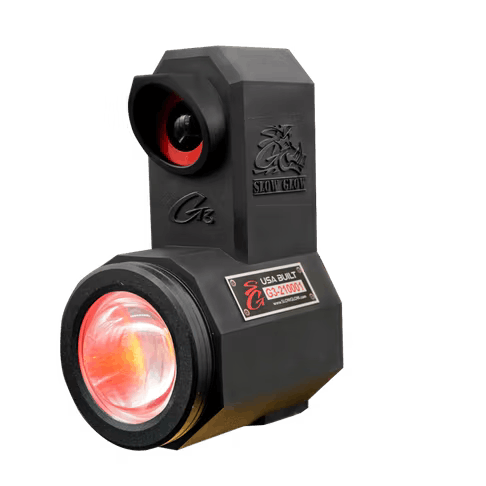
In an effort to combat the rise of an invasive wild boar species spreading across America’s vast agricultural landscape, hunting enthusiasts needed to develop a light that gradually turns on to help avoid scaring their target and losing sight of them. The Slow Glow team needed to find a way to quickly and affordably manufacture parts to reduce their production time and meet ever-increasing demand.
Slow Glow’s Murray Choate felt confident using Xometry’s injection molding services after consulting with the team of expert representatives, learning that the turnaround timeline for his project would take less than 30 days. With every step, the team at Xometry clearly communicated with Choate, monitoring the development of their new product development process and assuring a high standard of quality for their parts. “This was the largest investment our company had ever made,” Choate explained, “and Xometry fully delivered.”
Stage 5: The Testing Stage
As you enter the latter half of the product development life cycle, it is vital that product managers properly emphasize the importance of product testing. In this development phase, the product is tested to ensure it aligns with customer feedback and the technical requirements of the product. It is important for product development teams to understand what validation tests are required to optimize and ensure the quality of the finished product properly, how many tests are necessary, and how frequently they should be administered. Developers should carefully invest their budget appropriately in this stage, neither underinvesting and missing critical corrections born from testing nor overspending on unnecessary tests.
How Xometry Can Help
Once you reach this stage of product development, you'll likely have iterated on your CAD design and come to a finalized geometry that meets customer needs and the specifications set forth in your product requirement document. You will want to choose the appropriate materials and manufacturing processes that can be verified against all the desired functions and metrics. Your custom manufactured components will be tested alongside PCB circuitry for thermal, power, and EMI stresses.
Below, we outline some of the most common engineering validation tests you can run, and their uses cases by process:
Manufacturing Process | Cost | Lead Time | Use Cases |
---|---|---|---|
Manufacturing Process | Cost $$ | Lead Time 2 days | Use Cases Fit-check parts that need beautiful surface finish, high resolution, and multi-material composition |
Manufacturing Process | Cost $ | Lead Time 3 days | Use Cases Fit-check parts that need beautiful surface finish, high resolution, and clear finishes |
Manufacturing Process | Cost $$ | Lead Time 3 days | Use Cases End-use parts that need durable enclosures, brackets, and panels with a variety of corrosion resistance, flex, and durability properties |
Manufacturing Process | Cost $$$ | Lead Time 4 days | Use Cases End-use parts that need the high impact and fatigue resistance of metals, coupled with a variety of unique properties depending on the alloy |
Manufacturing Process | Cost $$$ | Lead Time 6 days | Use Cases End-use parts that need complex metal geometries that would be cost-prohibitive with CNC machining |
Manufacturing Process | Cost $$$ | Lead Time 6 days | Use Cases End-use parts that need specialized properties like high heat deflection, high flexibility, or biocompatibility |
Manufacturing Process | Cost $$$ | Lead Time 15 days | Use Cases A prototype with similar properties as the end material for preliminary durability tests |
Manufacturing Process | Cost $$$$ | Lead Time 15 days | Use Cases A high fidelity prototype in the end material for preliminary durability tests |
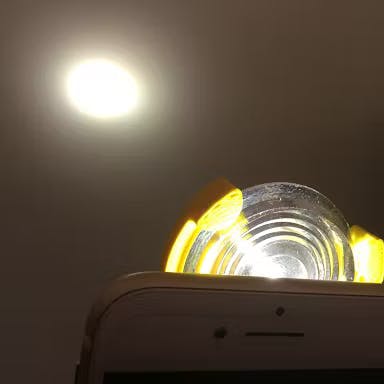
While Point Sur Lighthouse’s historic Fresnel lens has since been replaced by an LED beacon, guides like Richard Ruh keep the history of the Fresnel lens alive through tours. To showcase what Ruh refers to as “the magic of Fresnel lens,” Ruh created multiple handheld setups for park visitors to try themselves.
Before landing on a cell phone demonstration setup, Ruh wanted to test collimating another light source. Xometry’s CNC machining suppliers manufactured various iterations of CNC plates without a problem, even including threads to match the flashlight’s 35mm diameter thread and thru-holes ranging from 46-87 mm diameter.
Stage 6: Scale Up
In the penultimate stage of product development, a product idea has been fully developed, tested, and approved; it is now ready to reach a larger audience. Alongside an appropriate marketing strategy and product distribution strategy, a company will also need to ramp up its production capacity to take full advantage of the new market launch.
How Xometry Can Help
If you need to scale up production, it’s definitely worth learning more about Xometry’s injection molding service. Injection molding is the most cost-effective way to produce plastic parts at scale. With Xometry, you can choose from thousands of possible combinations of materials, finishes, tolerances, markings, and certifications for your order. Our team will help you get molded parts delivered to your door, taking the hassle out of sourcing, project management, logistics, or shipping. We are also ISO 9001:2015, AS9100D, and ISO 13485 certified; only the top molders that apply to our global supplier network make it through our qualification process.
Plus, If you're a first-time injection molding customer at Xometry, we'll take $500 off your first injection molding order to sweeten the deal.
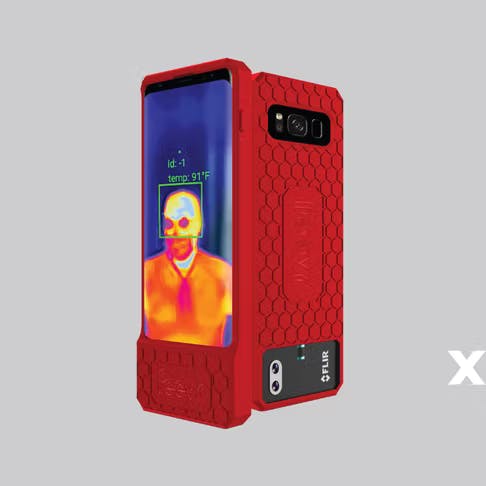
X.Labs, a startup R&D firm specializing in advanced sensing technology, needed to fabricate housings and mounts for their contactless heat detection product called Feevr. They were looking for a manufacturing partner that could deliver a bespoke, sterilizable, and durable manufacturing solution.
Xometry rapidly manufactured parts for X.Labs — moving through the full hardware development cycle from prototyping to production —- within just one month. Xometry met X.Labs’ strict manufacturing criteria for durable and medical-grade parts that deliver unique solutions for government entities across the globe.
Stage 7: Mass Production
Production is the final stage of the hardware development process, during which a company or individual reaches a finalized design that is ready to use and sell in their end environment. Production batches can be low-, medium-, or high-volume and may comprise a single design or multiple-part designs. In this final stage of the product life cycle, a company needs to find manufacturing partners with the capacity to meet the market share they hope to have.
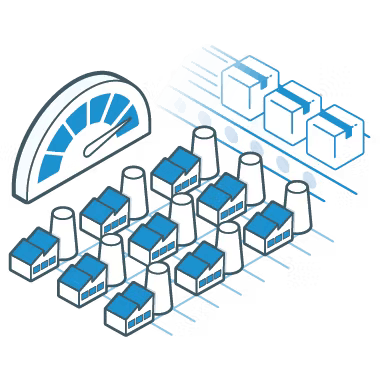
At Xometry, you don’t have to be limited to local suppliers. The platform integrates seamlessly with over 10,000 Xometry-vetted manufacturing facilities across 46 U.S. states and 22 countries. A comprehensive quality system backs our network and helps to ensure your parts' fit, form, and function. After you place an order, suppliers provide updates for you while your parts are in process and will send you an inspection report upon completion of your order.
Xometry also offers various manufacturing technological processes to create high-volume end-use parts quickly and affordably. There are dozens of production options; Xometry engineers are ready to advise developers, letting them know which process and material will perform best in the final environment. Injection molding is a go-to choice for scaling up lightweight, durable plastic parts, while CNC machining and sheet metal fabrication technology are better suited to produce precision metal parts with strict material requirements. 3D printing technology is a solid choice for engineers looking for a way to quickly make parts with solid mechanical qualities and appealing affordability.
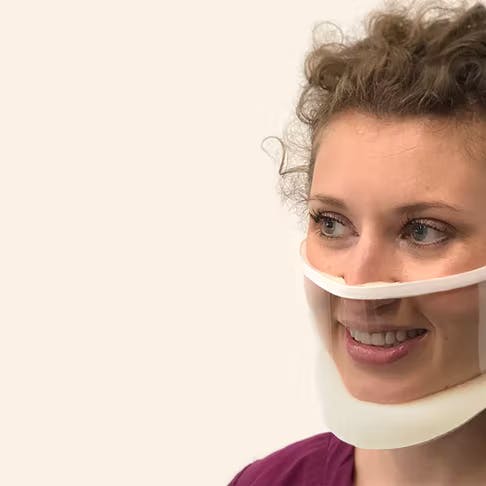
Alyssa Dittmar and her business partner Aaron Hsu, alongside a team of their fellow Johns Hopkins University alumni, created a fully transparent surgical mask to help those who rely on the ability to lip-read. The ClearMask™,a fully transparent, FDA-cleared surgical mask created by Maryland-based medical company ClearMask LLC, provides strong protection against airborne transmission while maintaining effective communication and human connection. ClearMask partnered with Xometry to scale up the production of their product, producing millions of masks and increasing the safety and quality of care for many during the COVID-19 pandemic.
When its time to launch your new product, remember that Xometry is prepared to guide you through every stage of the product life cycle, from idea screening and concept testing to full-scale production. The global network’s diversity and wide-ranging capabilities can help you access all the manufacturing services you need in one place. It’s all waiting for you in the Xometry Instant Quoting Engine.
If you are interested in learning more about how Xometry can help you as you develop new products, or if you would like to iterate on existing products, download Xometry’s Complete Production Guide or listen to Xometry’s Path to Production with Injection Molding Strategies Webinar. And, if you would like to speak to someone on the Xometry engineering team, feel free to contact them here.